项目要点及显著成果
某一体化压铸车间共投入4套压铸设备,可生产3种车型的后地板总成及前机舱总成共6个零件号产品,每个压铸机生产节拍为105秒/件,满足焊装双班70JPH生产节拍需求。
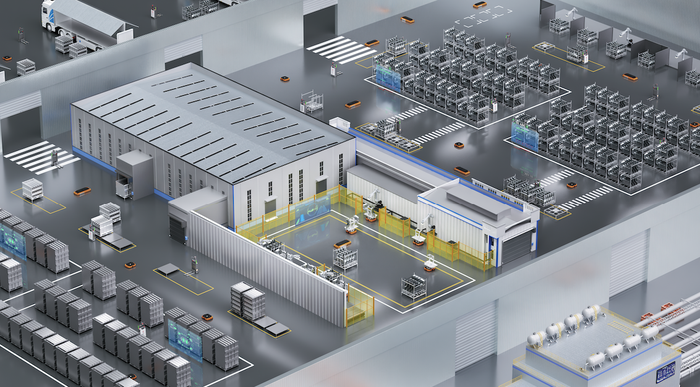
该项目通过导入移动机器人与机器视觉,实现了压铸车间铝锭原材料收货入库及上线、半成品上下线转运与质量检测、成品出入库全流程自动化作业。解决了客户人工作业劳动强度大、有安全隐患、人工质检有漏检风险等业务痛点。具体解决方案为:
第一,铝锭收货、存储及上线流程,通过iWMS管理入库交接点位实现空载具的自动补充,通过货物检测装置自动触发AMR搬运铝锭经视觉读码门读码后入库,同时铝锭送线通过上层系统与iWMS集成实现自动叫料、配送。实现铝锭从供应商、订单、入库时间、质量、送线等全过程精准追溯
第二,压铸半成品的上下线转运及机器视觉应用,机械臂在3D视觉的引导下完成装箱/取件之后,自动给AMR下发搬运任务,AMR实现空满料架搬离至缓存区以及空料架补充。RCS调度完成各个工位的转运,可通过任务模板配置灵活、精确的管理各个工位、缓存区、排队区状态,实现AMR最大化利用。在质检方面,配置工业相机,通过VM算法平台训练实现缺陷的高效检出且缺陷检出可以通过软件平台进行查看、分析和追溯。
第三,压铸成品仓储管理,通过iWMS系统实现了生产上下线、存储、配送各个环节的一体化管理和追溯,另一方面从管理的颗粒度和精细度上对于压铸件零件号、名称、数量、质量状态等库存管理。
通过部署一体化压铸解决方案,给用户带来的收益主要体现以下三个方面:
第一,管理精细化—传统管理如对于铝锭、压铸件库存管理、人效管理难以获取精细数据,通过方案部署,能精准知晓业务运行种的详细数据
第二,拉进管理距离—通过解决方案部署,实现对于大量数据的感知、采集,通过数据分析精准刻画压铸工序各个环节、流程,给作业者、监管者、管理者实时了解现场运行,如工序利用效率、周转效率、库容等等
第三,快速辅助决策成为可能:海量数据的采集、汇聚和分析,作为数字孪生的基础,为管理者发现运营的堵点痛点,进而优化运行流程、布局提供依据。