高级工匠的技巧加上丰富的实践经验,才能将镁合金与铝合金巧妙地铸造成一个整体,从而研制出一种新型的大功率发动机。德国宝马公司在Landshuter生产厂的铸造专家们就具备了这样的技巧和经验。他们成功地将铝合金铸芯‘镶嵌’在镁合金发动机缸体中,从而使这种缸体的重量比相同结构、其他材料的缸体还要轻10kg。
宝马公司是第一家利用自己的设备生产镁合金水冷发动机的生产厂,他们充分挖掘了镁合金材料的优点,最大限度地避免了镁合金材料的缺陷。
由纯镁或者传统镁合金铸造的发动机缸体无法进行大批量生产,因为其具有较低的承载能力、极易脆断、脆裂和难以提高的表面粗糙度等特点,这些都阻碍了金属镁作为轻金属材料在汽车制造领域中的应用。
对于宝马公司的发动机设计师来讲,他们知道:只有经过对不同材料的组合,经过精心而又巧妙的结构设计,才能使新设计的发动机满足所有的技术要求。该新型组合材料发动机的基础是宝马公司的新型四缸发动机。在此基础上,他们将新型发动机缸体在曲轴轴承平面的高度位置处将发动机缸体分为两部分,以提高结构刚性,降低发动机工作噪声和提高发动机的使用寿命。
在这一部位,镁合金缸体与铝合金缸体的不同之处在于:镁合金组合缸体的上部包含有被镁合金环绕的铝合金缸套和水套。
由于铝合金部件有着较高的热承载能力和机械承载能力,因此在这些铝合金铸芯中加工连接曲轴轴承和缸盖的连接螺栓孔。围绕在铝合金铸芯周围的镁合金缸体,则主要用于容纳机油通道和连接发动机的其他辅助设备。
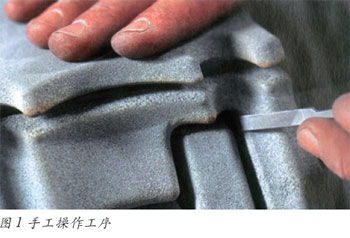
新型的密封系统能防止不同金属间的接触腐蚀
由于发动机辅助设备的功能集成度比原来有了较大提高,因此辅助部件的数量也相应减少。这样,镁合金缸体的上半部分主要用于安装起动机和低压泵等,缸体的下半部分同样也是镁合金压铸件,它的内部含有安置轴承的烧结钢块。采用手工操作工序时,砂型制造的烧结钢块必须手工准确地放置到位,然后才能生产出高性能、长寿命的发动机(见图1)。
根据新的发动机结构设计方案而研制开发的新型密封系统,可以很好地密封分隔各个结合面。为了防止钢和镁之间的接触腐蚀,工程师们还设计采用了高强度铝合金连接螺栓。
为了保证镁合金组合缸体生产的可靠性,选择合适的镁合金成分也是关系到镁-铝组合缸体铸造成败的前提条件。
在深入进行材料基本理论的研究之后,宝马公司Landshuter生产厂的材料学专家、发动机设计专家和铸造技术专家们研制出了一种最佳的镁合金材料配方:一种专门适合于铸造镁合金缸体的材料配方。从而重新定义了镁合金材料的使用范围,开辟了镁合金材料应用的新领域。
宝马公司的组合缸体也将大批量投入生产
Landshuter生产厂的专家们克服了一系列难题,如在镁合金材料的研制过程中,有蠕变强度、腐蚀性能、热承载能力和机械承载能力等难题,此外,还有铸造技术中的难题、镁与其他金属之间的接触腐蚀的难题以及发动机密封的难题等。
与此同时,他们还在Landshuter压铸中心制造了镁合金组合缸体生产所必需的设备,并完成了对全套的压铸生产工艺技术进行的可靠性验证。这种新型材料和新型加工工艺技术研制开发以及生产过程都是由宝马公司的工程技术人员独立自主完成的。
在这种新研制的镁合金压铸工艺技术中,镁合金在冷却收缩时紧紧地包住了铝合金铸芯,同时,铝合金铸芯上突出的镶片也依靠其形状而牢固地嵌入到镁合金外套中。
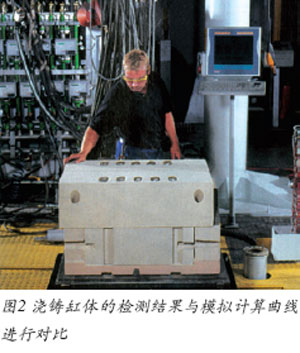
由于金属镁与金属铝在温度在500℃~600℃之间有着十分接近的冷却过程,因此在浇铸时对温度的控制要求非常严格。浇铸后的缸体必须经红外线探伤检测,检测结果还需与模拟计算的曲线进行对比(见图2)。镁合金溶液必须准确地加热到合适的温度,压铸模具也必须冷却到合适的温度,必要时在合适的位置放置冷铁。
新设计的镁合金组合缸体在宝马公司Landshuter生产厂压铸中心的压铸机中压铸成形。在全自动化的压铸生产过程中,在重达60t的压铸模分型面上涂抹分型剂,然后放入铝合金铸芯,最后合模。
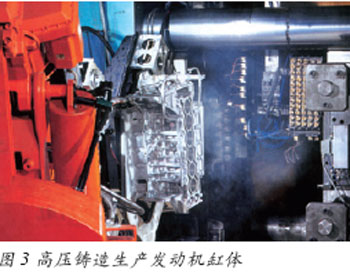
压铸时,温度高达700℃的镁合金熔液在1000bar的压力作用下在短短的0.01s内压入模具中(见图3),此时,模具的合模力达4000t左右。10s内,镁合金材料开始冷凝,20s后可由机器人将压铸好的镁合金组合缸体从模具中取出,镁合金组合缸体在压铸成形后被运送到下一工位进行热处理,以消除内应力。
不仅在铸造时,而且在机械加工时,镁合金组合缸体均表现出完全不同于铝合金缸体的特性。采用新的加工工艺技术,镁合金有着比铝合金材料更好的机械加工性能。
目前,Landshuter生产厂压铸中心正在对镁合金组合缸体的全自动生产工艺过程进行大批量生产的二次开发与优化。在今后的两年内,宝马公司可望在Landshuter新建的生产厂中完成该缸体的大批量生产。
评论
加载更多