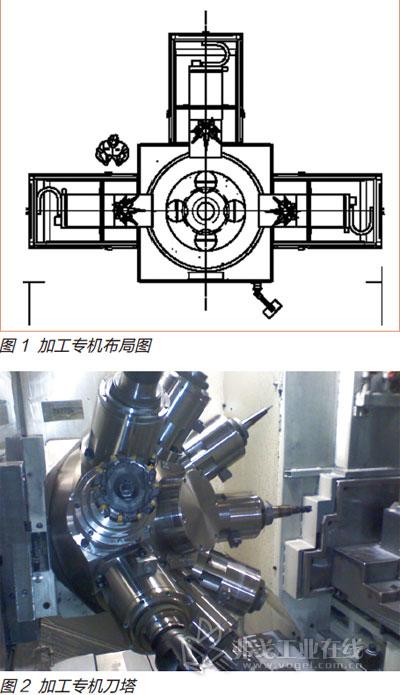
发动机的配气机构件——凸轮轴因其结构特殊性及高精度的要求,加工设备具有多样化、精度高、高效及高柔性的特点。本文通过实例,介绍了凸轮轴加工设备的选型方法。
凸轮轴属于刚性较差的轴类零件,要实现在较高生产率条件下达到较满意的尺寸精度、几何精度以及粗糙度等,加工设备的选型需要特别关注。按工艺流程和加工难易程度,凸轮轴的主要加工设备包括中心孔加工设备、轴颈粗/精加工设备及凸轮加工设备。
随着装备制造业的发展,满足相同加工要求的有多种类型设备供企业选择,故企业要了解设备选型的三点基本原则:适用性、先进性及经济性。
本文将以凸轮轴机工设备选型做一些探讨。
中心孔加工设备
中心孔作为轴类零件的工艺基准,用于装夹定位、检验和装配的整个工艺过程中,生产线的第一道工序基本上多为加工中心孔。
凸轮轴中心孔因不涉及质量中心或几何中心的选择,中心孔的加工较为简单,保证轴的两端所钻出的中心孔具有正确位置、在钻中心孔前增加铣两端面即可,故现在大部分生产线第一工序为铣端面和加工中心孔。
中心孔加工设备可选用端面铣打专机或卧式加工中心(专机),如江苏新瑞长城(原江苏多棱)端面铣专机、沈阳机床厂的卧式加工中心,以及德国HELLER、伯林格及LARU等的加工专机,这些设备在奇瑞公司均有应用。
图1为加工专机的设备布局,多主轴多工位,高速转台;图2为加工专机主轴,高速主轴可根据产量/产品特点,布置2~3个主轴,装载铣刀/钻头等多类型刀具,可加工凸轮轴的轴向/径向所有加工内容。
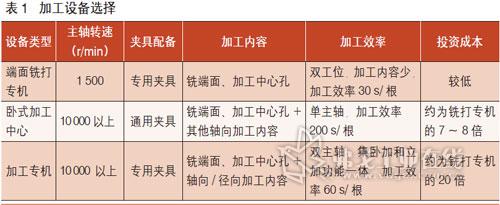
由表1可以看出,选用哪种类型的中心孔加工设备取决于生产线的精度、效率要求以及生产线的定位。其中:端面铣专机适用于简单的加工内容和工艺路线要求,具有投资成本较低、设备易维护的特点;卧式加工中心适用于加工内容尽量集中的要求,具有较好的柔性,设备通用性强的特点;加工专机适用于加工内容高度集中化的要求,具有高效率、高精度和全自动化的特点。
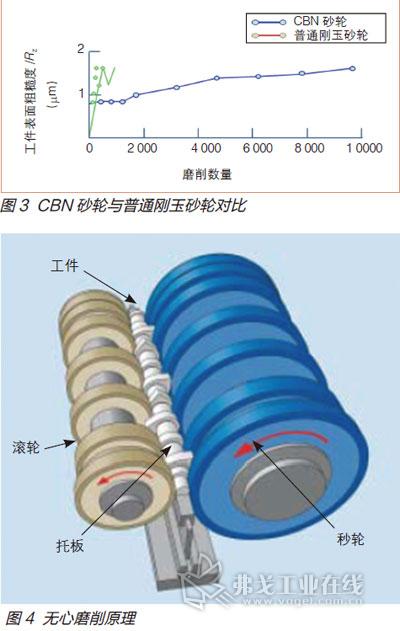
轴颈粗/精加工设备
1. 轴颈粗加工设备
轴颈粗加工的设备种类较多,包括普通卧/立式数控车床、内/外圆铣床和以磨代车的粗磨磨床。
数控车床应用的历史最早,范围最广。选择卧式车床还是立式车床,根据设备选用基本原则考虑如下:(1)适用性 卧式数控车床可用于各种轴类零件的轴颈粗加工,适用于发动机主机厂的大批量生产要求,目前卧式车床已向高复合式车削中心方向发展;立式数控车床主要用于加工直径大、长度短的大型、重型工件和不易在卧式车床上装夹的工件,因太重的工件在卧车不易装夹,且由于本身自重,对加工精度有影响,采用立车可以解决此问题。立式车床广泛适用于重型机械制造厂的小批量生产。
(2)先进性 卧式车床技术成熟,工艺应用最广,随着先进伺服控制系统的应用,卧式车床不断优化主传动及进给系统,可实现刀盘伺服控制和快速移动,同时有着与加工精度相匹配的监控装置。
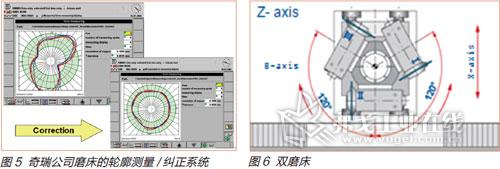
(3)经济性 国产卧式数控车床的制造技术已相当成熟,宁夏小巨人、长城车床、济南机床厂和沈阳机床厂的数控车床在各轴类加工厂广泛应用,较低投资即可满足高效、高精度的加工要求。德国进口车床以设备稳定,加工效率高等特点,也具有明显的经济优势。立式数控车床因适用于加工较重型工件,对工作台面、定位精度均有着较高要求,实现相对较快的效率以及高精度的要求下,设备制造难度较大,故立车的制造商较少,选择空间较小,设备价格也较高(进口立车费用约为国产车床的15~17倍)。选择数控车床时,需结合前后序加工精度和基准的选择,来确定卡盘、顶尖孔的形式和中心架的选用(立式车床可不必配备中心架)。
2.轴颈精加工设备
凸轮轴的轴颈精加工是在轴颈已完成粗加工的基础上,对轴颈再进行小余量的加工,以达到较高的表面粗糙度、尺寸精度及圆柱度等要求。这一工序业界多选用普通外圆磨床,以中心孔定位夹紧,以一个或多个中心架作为辅助支承。磨削要保证效率和质量,就要正确选取砂轮的类型,CBN砂轮以其高效(磨削速率可达200m/s)的特点在近代被广泛地应用于数控磨床上。虽然CBN砂轮价格较普通刚玉砂轮高出数倍,但耐用度高,比一般砂轮磨削相比,效率提升了六七倍,同时加工工件的质量也有显著提升(见图3)。
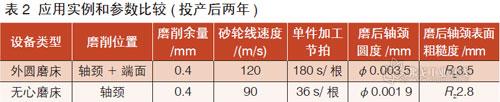
20世纪70年代以来,由欧洲厂商研发出来的无心磨削技术(见图4),以其高精度、高尺寸和几何精度的特点,进入了发动机制造领域。奇瑞公司也在2004年购入了一台由德国勇克公司(JUNKER)生产的无心磨床,并使用至今,单根凸轮轴加工节拍达36s。
根据表2可看出,无心磨床在加工精度、加工节拍上均优于普通外圆磨床,但不适于多品种零件的加工,因柔性相对较差,故设备选择时要根据工件精度、结构特点、产量的大小和柔性的要求进行选择。
凸轮加工设备
国内外各发动机工厂均已使用CNC随动磨床来完成凸轮的加工,随动磨床已经彻底取代了过去的偏心夹具方式磨削。随动磨床不仅可以实现粗、精磨所需的不同转速,也可以在凸轮/曲轴摆动不同曲线段进行自动变速,从而保证型面上每一个磨削点的磨削力、磨削量一致。大大增加了磨床的柔性、效率和精度,例如凸轮型面的误差由原0.015mm(双靠模)提高到了0.007mm。
CNC随动磨床应用已十分广泛,关于凸轮的磨削工艺设计,可依托设备供应商解决。磨床先进的设备制造商众多,如德国勇克公司、肖特、LANDIS公司、日本丰田工机公司(JTEKT)和日本NTC公司等。随动磨床的选择,需与设备供应商重点确认,如何根据提供凸轮的0~360°离散点,运用三维数据转换和测量监控系统,将离散点变成连续的封闭曲线,并将生成曲线转为磨削曲线。图5为磨床的轮廓测量/纠正系统。
凸轮轴上如具有凹面凸轮(也被称作“负曲率半径(NROC)凸轮”)的情况下,可选择双磨头凸轮磨床(即带B轴磨床)或两台装载不同尺寸砂轮的单磨头凸轮磨床。双磨头磨床(见图6)可一次装夹,加工完成凸轮形面,精度和效率均较高,且只增加一个磨头的硬件和软件控制的费用(欧洲磨床的单个磨头费用约25~30万欧元),经济性较好。
结语
随着发动机技术日新月异的发展及市场竞争的不断加剧,发动机产品不仅要提高性能和质量,同时要在利润和成本上寻求最大化,只有这样才能在当今的市场上占据一席之地。这就对加工设备有了更高的要求:既要实现高精度、高柔性和高效率,还要具有较强的经济性,所以,设备合理选型对一个项目是否成功至关重要。
评论
加载更多