车身设计要点
本文所研究的某新能源车型充分利用原型汽油车的车身,仅更改了前机舱和侧围,以及车身地板的部分零部件,实现了与原汽油车共线生产。其车身设计主要有以下特点:
1) 充分利用车身原有零件,对前机舱、地板、侧围进行重新设计。
2) 对前端框架进行局部重新设计,满足车型的使用。
3 ) 慢充口充分利用原加油口的位置,节约成本。
4) 通过分析和现场验证,使两个车型共线生产。
5 ) 增加侧围装饰板,遮挡外露的电池。
6 ) 在原有车型涂胶防水技术的基础上,加强对涉水性能的提升。
1、车体设计
新能源车型与汽油车共平台,多数零件可以通用,可降低平台车型的开发成本。如四个车门、发动机舱盖、行李舱盖、机舱内部零件等。对于后桥采用扭力梁悬架的车型,车身上车体没有变化;后桥采用多连杆悬架的车型,车身上车体的后轮罩和纵梁需进行重新设计( 图1)。
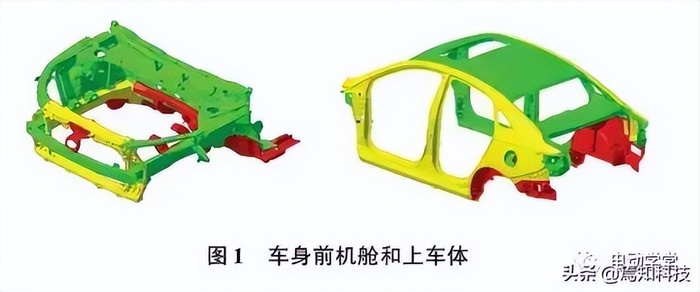
新能源车身开发因动力总成变化,增加了电池,导致地板的更改较多。车身需满足离地间隙的要求,故地板相较汽油车向上抬高,且结构也为适应电池而有所改变。这些零件都要重新设计,不能借用汽油车的零件( 图2)。
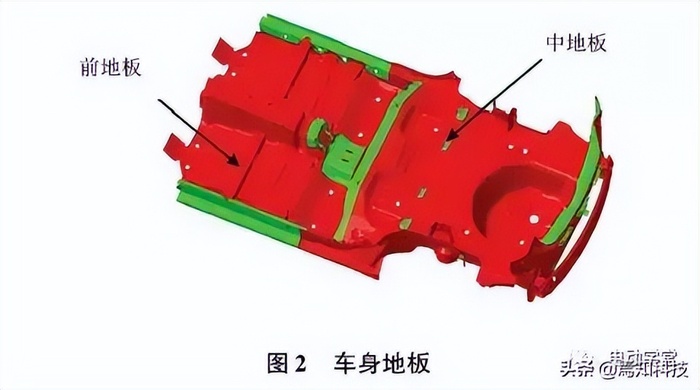
由于新能源车电池较厚,为保证人机工程,前地板纵梁、横梁、座椅横梁需要做相应的减薄或取消。同时结合C A E 分析,将关键部位的安全件进行相应增强,如中通道罩和前地板加强版的料厚增加0.6 mm。车身地板下安装电池,为了承担电池的重量,在前地板的下面左右两侧新设计了两个电池安裝纵梁( 图3)。
2、前端框架结合CAE 计算设计
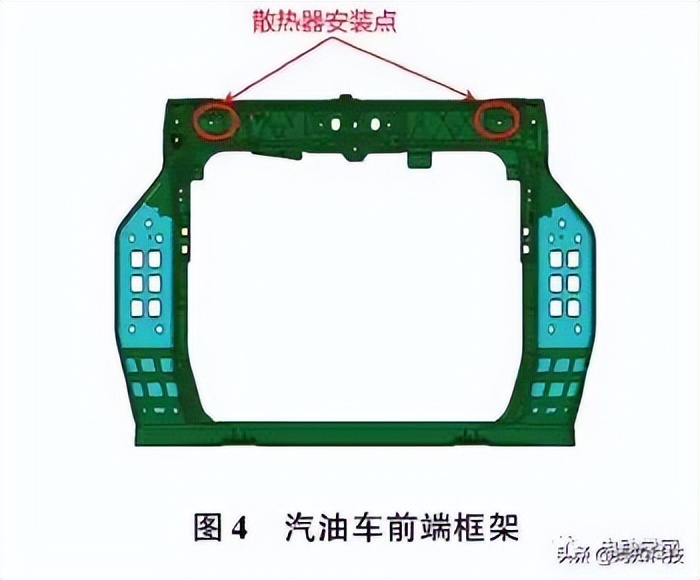
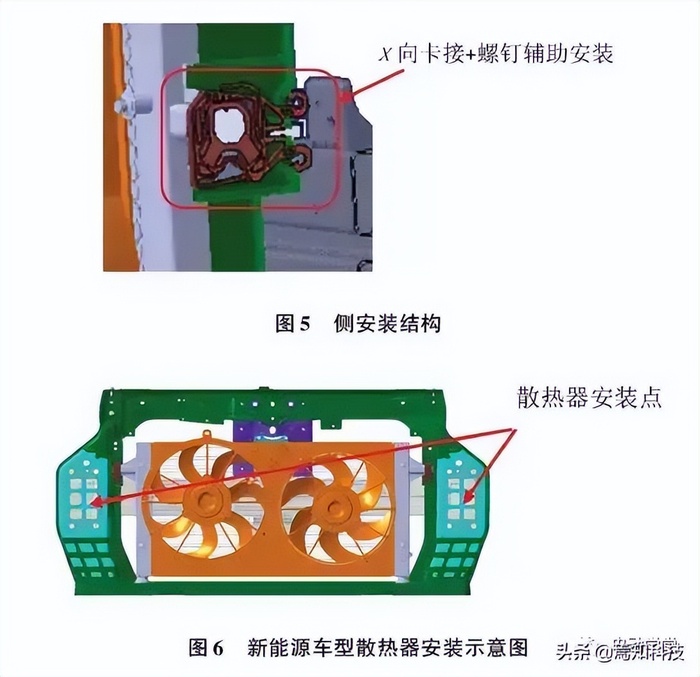
3、快、慢充电口的布置
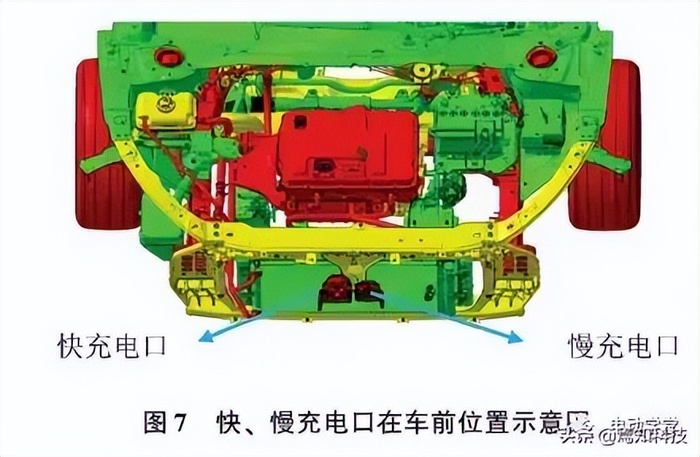
通常新能源车需要布置两个充电口: 快充电口和慢电口。新能源车的快、慢充电口多布置在车头前( 图7) 。而某车型慢充电口因通用化原因,并且考虑到慢充电口放在车头与快充电口一起,快、慢充电口的盖比较大,也将会破坏格栅整体性( 图8) ,故选择在原加油口的位置,固定的零件只做相应微调,以便安装慢充电口座( 图9 ) 。
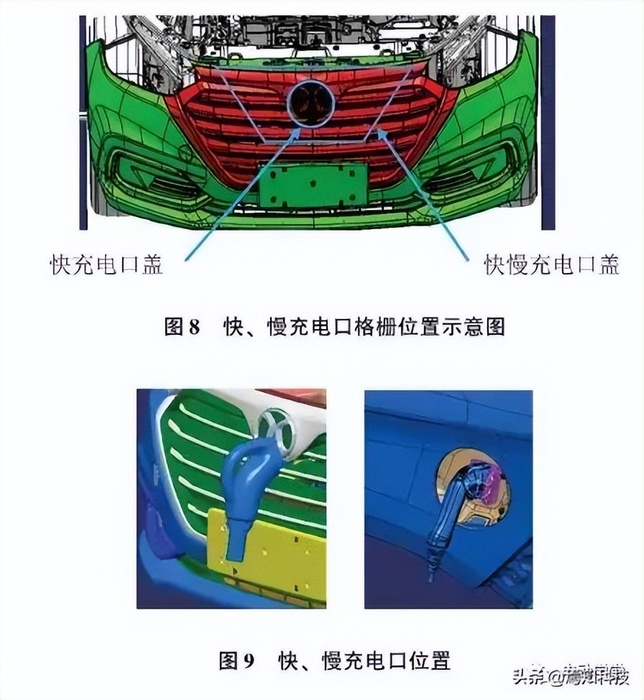
4、下车体满足原车型共线的生产要求
新能源车型的生产通常需要其具有平台化、通用化的能力,且能够实现与汽油率共线生产。某新能源车一共有两个车型,分别最扭力梁版和多连杆版。扭力梁版车型与原型汽油车一致,焊装、涂装及总装能够通用。多连杆板车型后地板后横梁则较原型汽油车离地降低了36mm,装焊车间相关夹具需重新开发,总装车间的抱具沿用基础车型,涂装方面,如图10所示,车型需要共用滑撬,故后横梁上的定位孔设计满足共用需求。
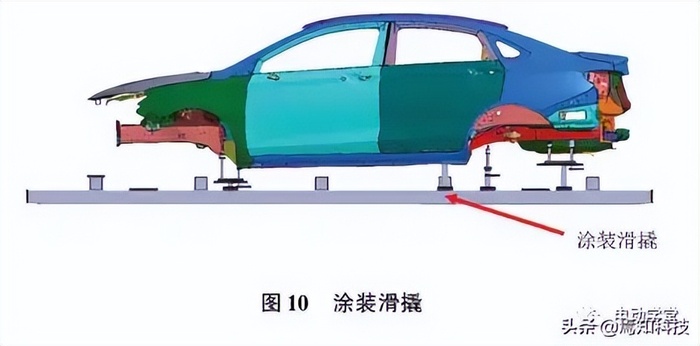
经论证,两个车型所用滑撬的前点均沿用基础车型(图11) ,后桥采用多连杆的车型的后点定位点X方向向前移动2.6 mm(图12) 。因后横梁的Z 方向定位面比原型汽油车低36mm,所以当白车身放在滑撬上时,后横梁先接触滑撬后定位销,然后才是白车身接触前定位销,造成了多连杆版车型在滑撬上与原型汽油车和扭力梁版车型平放的姿态有所不同,是前低后高。经涂装车间的走线验证,完全满足设计要求,无脱落风险。
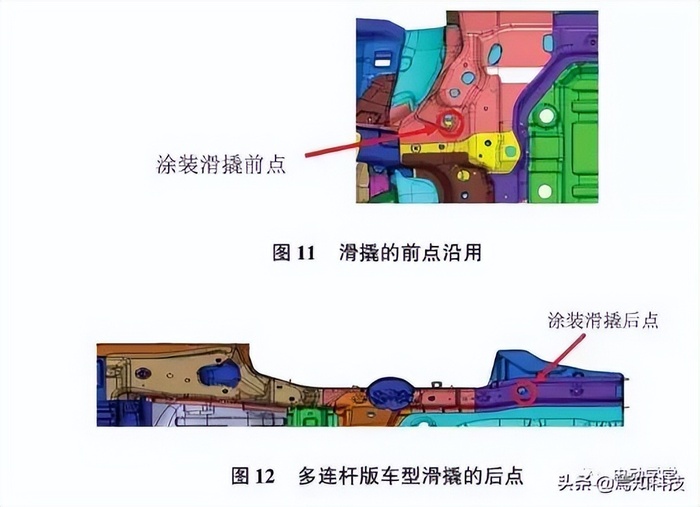
5、车身边梁增加装饰板
为满足车身离地间隙而抬高地板高度,导致从车身侧面可以看见吊挂的电池( 图1 3) 。为解决这个问题,在侧边梁上增力口装饰板,同时相应地更改前后保险杠的造型,使新能源车在下部的造型成为一体( 图14),达到遮盖电池的目的。
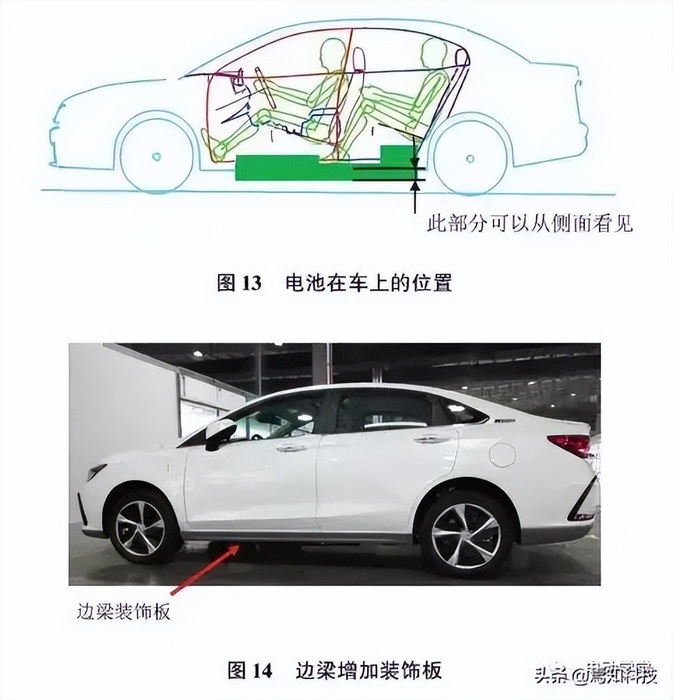
6、提高车身防水设计
在某新能源车试制阶段进行的涉水试验中,发生了地板进水现象( 图15)。通过对试验漏水车辆进行现场试验跟踪和漏水现象的排查,发现新能源车的涉水试验较汽油车严格,涉水试验时间比汽油车增加1~ 2 倍,同时检查漏水试验车辆,发现在边梁下部的涂胶明显不足,没有按照设计要求在边梁与前地板的搭接处涂抹点焊密封胶,漏液孔和工艺孔也均未被封住( 图15)。
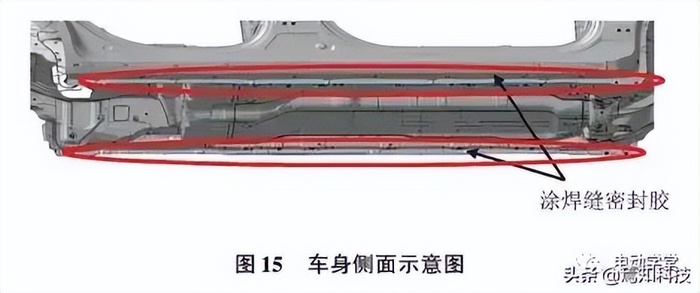
在试验过程中,发现在车内和车外的地板上,有多处漏水点,且每台车都有所不同,因此判断在这些位置点焊密赫胶和焊缝密封胶涂抹不够( 见图16) ,黑色线是焊缝密封胶,黄色线是点焊密封胶)。解决方法是在重点部位加大涂胶量,在车外的地板上加厚涂焊缝密封胶( 图17),对生产车进行严格的质量把控,从而使涉水试验车通过验证。
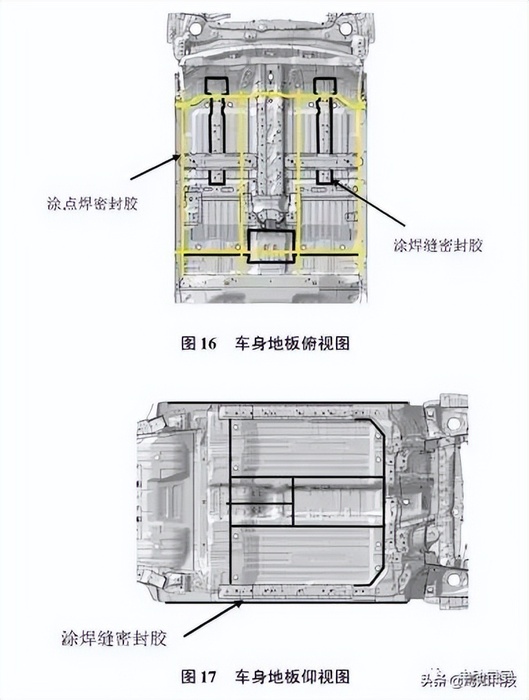
以上实例说明车身的防水是十分必要的,从目前车身工艺的发展来看,对车身地板和侧围的涂胶都是各个车型的重要工作,从设计之初就把防水作为首要考虑的问题,以保证车辆在各种天气情况下正常使用。
结论
车身的设计至关重要,一个设计良好的车身,是达到新能源车基本性能、满足各种装配要求、具有良好制造工艺性的保证。本又重点针对汽油车改新能源车车身开发过程中重要的几个方面进行说明,依据车身地板、前端框架、充电口、侧围等部位的改动自结出一种以燃油车为基础,系统的、通用化车较高的新能源车设计方法。
评论
加载更多