汽车变速器是一个技术和资金密集的产品,它直接影响和决定汽车的行驶平顺性、燃油经济性和动力性,是汽车动力系统的核心部件。产品生命周期涵盖产品研发、试验验证、前期规划(量产工艺设计、生产线设计、物流仿真和包装设计等)、生产制造与管控及售后服务。VR技术是虚拟测试系统的仿真系统,以及虚拟测试系统中的测试技术,本文主旨是将虚拟现实技术优势渗透到变速器产品研发中与VR技术相结合,达到降低新项目沉没成本、提高设计效率、缩短设计周期、降低开发成本、降低制造成本、提高客户满意度及增强产品竞争力的目的。
通过大量前期调研和试用国内外、各行业的虚拟现实软硬件及应用,依据变速器产品全生命周期技术和管理要求,选取了适用于汽车零部件制造行业,国内外知名软件商的行业标杆软件平台。在信息化方面,本设计引入了“VR技术”概念,实现了信息化、自动化、智能化与生产制造过程的紧密结合,通过VR技术应用,帮助研发工程师提高设计效率,降低设计失误,减少或避免设计缺陷,在VR技术领域又迈进了新的一步。
01软件模块功能
1)能够对超大三维CAD模型的自动轻量化导入,提高实时渲染速率,具有场景制作渲染能力,内置了丰富的材质库、天空盒等场景生成工具。
2)能够实现照片级的渲染质量,用于专业的造型设计评审,软件内置高精度物理引擎,可以用于凹凸多边形零部件之间的碰撞分析,可以模拟刚体零部件之间的碰撞,以及刚体与柔体、柔体与柔体之间的碰撞关系。
3)能够支持多种VR外设,比如数据手套、力反馈及全身动捕等,结合全身动捕和软件的人机工效功能可以实现可视性、可达性和舒适性分析,以及作业时间、作业强度、作业疲劳度及腰脊椎受力等人机工效算法。
02VR产线实施过程
工程技术人员通过工具化的应用软件,在产线到位前利用虚拟现实技术1:1还原了真实产线场景,实现了在VR端编辑(比如挪移、测量、复制和创造实体)及云端会议功能,以此审核产线并设计配套料架。相较于之前使用的纸箱产线模拟,它更灵活,场地需求少,人员投入少,是一种全新的前期规划及审核工具。这种应用软件加强了规划人员与最终用户间的交流沟通,体现了以用户为导向的主旨,用于改善产线人机功效,查找规划问题,消除安全隐患。
1)基础模块能使制造企业在一个交互的3D环境中设计制造工艺。基于使用和易于客户化的平台,能够根据用户的定义客户化用户界面。能够方便地创建和确认制造工艺,贯穿从概念设计到详细工程整个过程。它能够改进、获取和重复利用工艺规划,工艺设计团队能够比较不同方案改进和选择最好的制造策略以满足特殊的商业要求。基本应用中已经包含了一些很好的功能,提供了一个很好的工艺设计环境。
2)线平衡允许快速将操作分配给工位,从而提高生产线利用率。操作者按照给定的指导方针和约束条件执行这项任务。
3)基于规划、同步工程和模拟数据现在可以克隆并用于多个可选方案。这缩短了工作流程,同时使工程师能够轻松地验证多个备选场景,并且能够规划和设计复杂的装配设备、生产线和工位。产品支持层次结构,从工厂布局、仿真到生产线布局、到单个工位的详细设计和优化。
4)能够对产品装配和拆解过程进行设计、分析和验证。它具有分层装配树,允许创建和模拟装配路径和操作序列,并启用碰撞检测,以及2D和3D断面和测量分析。
5)能使用户创建非常复杂的机器人制造区域。机器人仿真工具提供了设计所有机器人无干涉路径的能力,并能通过在一个区域中的多台机器人同步来优化循环时间;并且连续制造过程规划仿真,提供了一个从粗规划阶段到详细规划阶段和离线编程的整个连续制造过程的开发工具。
6)能够允许用户使用准确的人体模型分析工作场所的人体工程学,可以使用不同比例的男性和女性人物分配任务。可以进行人体工程学评估,可视区域和干涉检查,通过在一个工作单元内使用真实PLC程序来验证包含机器人、设备环境之间的关系;VR模块还支持通过HTCVIVE进行虚拟现实查看,包括测量、移动和运行仿真等功能。
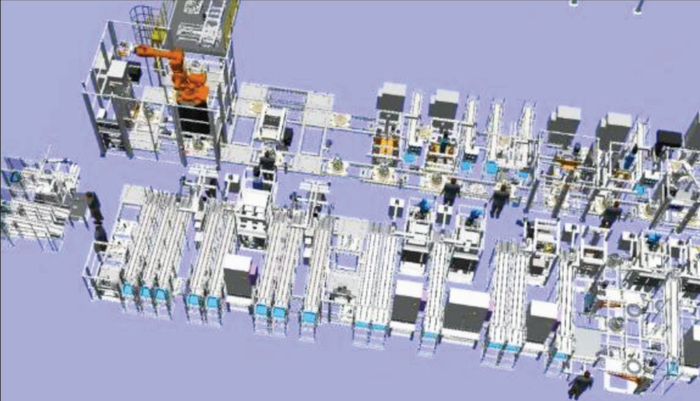
VR 产线设计图
实施和模拟后,我们相比以前设计,提高了产线平衡率,优化了工艺,减少了人员数量,产线更加柔性和灵活,现在的生产线爬坡速度更快。通过模拟,对设备的布局更合理,兼顾了设备维修和物流路线各方面因素,对产线设计更方便,更加直观。
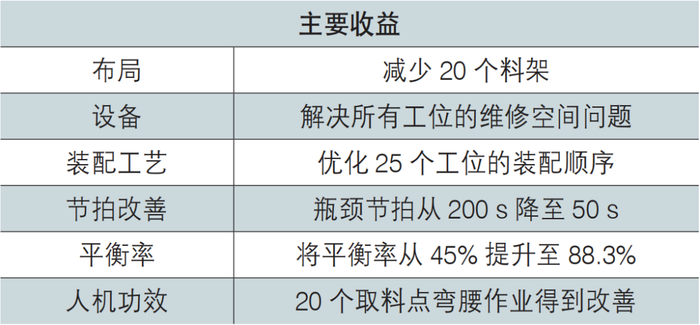
产线收益
03VR物流实施过程
VR技术在物流的软件模块是工程师、管理者和决策人基于“关于操作、流程及动态系统的方案”进行试验、评估和视觉化的工具,超强的3D虚拟现实(3D动画),直观的、易懂的用户接口,卓越的柔韧性,它能使决策者轻易地在个人计算机中建构及监控任何工业及企业的分布式流程。通过该软件将能率先找出未来工业及企业流程的模式。
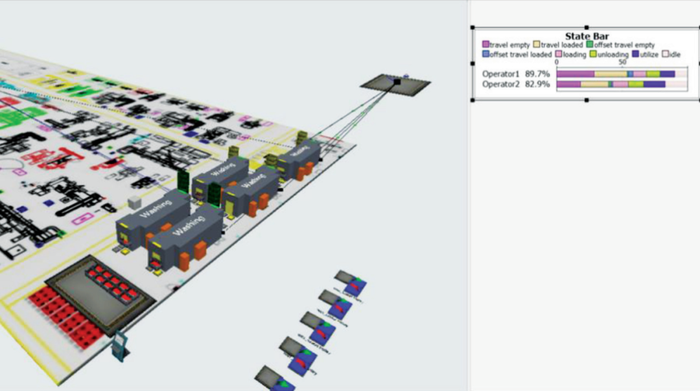
VR 物流设计图
虚拟现实技术与物流工程相结合使我们能够在虚拟环境中仿真物流过程,并轻松描绘出制造过程的优点和缺点。它具有系统假设可调、时间受控(更慢/更快)、分析随机模型、仿真数据的收集具有多维度性、仿真更优于理论分析、便捷的方案调整等优点。
操作者检查现场操作员的循环移动,以确定要遵循的最佳路径,计算移动距离,并确保操作员正确移动,模拟多种方案使得操作员率在可接受范围内约88%;追求和基本实现低成本自动化(机器人)应用于作业单元与操作者的活动结合,从而最大化每小时产量。
评论
加载更多