0 引言
目前,智能制造正在取代传统制造,成为制造业的主导制造方式,智能制造对于整车车身工艺规划的精益性提出越来越高的要求,差异化车型共线生产对生产线工艺规划的柔性也提出了新的挑战。如何在满足高柔性、差异化生产的同时满足精益性、智能化成为车身工艺规划的研究重点。
在车身车间,为了节约上料面积和时间,零件对中上料工艺被大量应用,但是随着车间引入车型越来越多,差异化越来越大,传统的固定对中台越来越难以满足柔性制造需求,本文介绍如何应用伺服机构设计多车型柔性伺服对中系统,使车身零件的对中上料在满足高柔性、差异化生产的同时实现精益性与智能化。
1 零件对中系统
零件对中系统,是将零件限定在特定空间位置以供其他机构自动取出的定位系统。基于白车身零件工艺顺序(图1)和自动化生产需求,以及解决多车型共线生产带来的线旁空间问题,零件对中系统大量应用于车身车间。传统零件对中系统见表1,主要包括转毂对中系统和固定对中系统。以车顶零件对中系统为例,传统零件对中系统及限制如表所示。
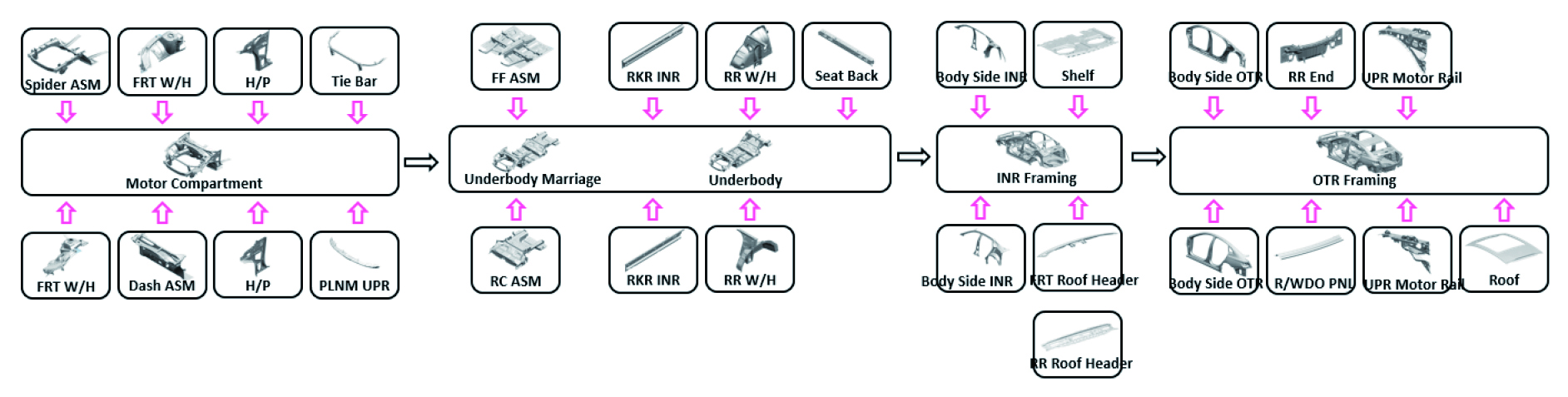
图 1 白车身零件工艺顺序
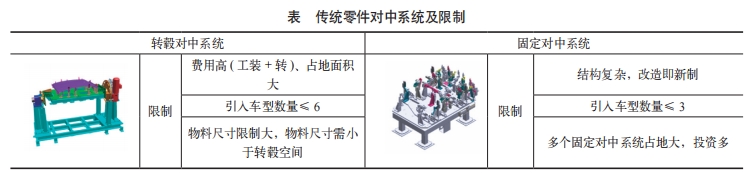
随着共线生产的车型越来越多,零件差异化越来越大,对工艺规划的精益性包括线旁空间、投资和改造周期提出了越来越高的要求。在白车身多车型共线生产过程中,传统的零件对中系统限制越来越难以满足制造需求,多车型柔性伺服对中台的设计和应用不但解决了对中台共用难度大,也解决了因场地面积不足和投资费用不够不能满足放置更多对中台等问题,而且还满足多车型共线的柔性需求,缩短引入新车型所需改造时间,降低设备维护成本。
2 设计要求及总体方案
多车型共线生产时,同一个工位需保证不同平台的多个车型共用,共用工装设计改造不仅难度大、改造成本高,而且当工装无法共用时,需新开工位,占用更多空间,调试复线时间较长。
以某车身车间总拼车顶上料区域为例,现场使用一个转毂零件对中台,但由于引入的新车型车顶尺寸大于现有转毂容纳的尺寸且场地限制,无法共用原有零件对中台且无多余场地安置新的对中台。根据设计要求,需要通过使用柔性可调的伺服机构,设计一套简单布置的多车型柔性伺服对中系统,实现多个车型车顶零件的对中台共用,后续通过程序调试即可完成新车型的引入。
多车型柔性伺服对中系统是需要PLC读取车型信息,然后根据车型信息调取已编制完成的对应车型离线程序,触发控制器,控制器驱动执行器运动到位,系统工作流程如图2所示。
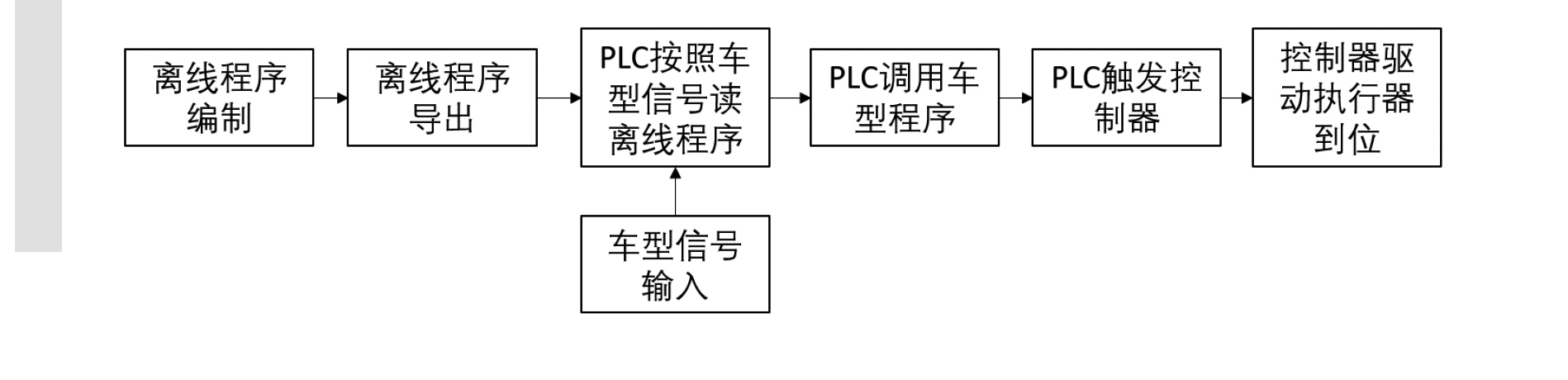
图 2 系统工作流程
3 系统组成和工作原理
3.1 系统组成
多车型柔性伺服对中系统如图3所示,其组成包括底座、BASE板、零件支撑面、固定零件限位、伺服机构、伺服零件限位、操控面板和控制器等。其中,零件支撑面用于支撑不同型面的零件,伺服机构及其控制器用于不同尺寸零件的对中定位,操控面板用于对中台的优化与调整,以及后续新车型引入时的程序调试。

图3 多车型柔性伺服对中系统
3.2 工作原理
多车型柔性伺服对中系统原理,是通过可交互控制系统,控制多组无级可调伺服机构,驱动容差定位单元到达不同的空间位置,实现对不同尺寸零件的对中定位。
以车顶多车型柔性伺服对中系统为例,其工作原理是伺服控制器通过EthernetIP与PLC、HMI相连,控制器接收PLC下发的产品信息和程序信息指令,完成动作后,在HMI上实时显示控制器状态和反馈的位置信息。控制面板和HMI,均可用于对中台日常标定、优化,以及后续新车型引入时的程序调试。固定零件限位及伺服零件限位控制所有车顶的X向、Y向和Z向自由度。伺服机构及其控制器,将对伺服零件限位调整至不同尺寸零件所需的定位位置。零件支撑面采用较大曲率的球形尼龙支撑面,与零件点接触以适用对中台上不同型面的车顶零件。Base板和底座支撑整个对中系统。PLC、控制器及伺服机构协调配合,循环完成不同车型零件的对中定位。
4 定位系统设计
根据实际工作要求,多车型柔性伺服对中定位系统需要通过限制零件自由度来保证零件对中约束。定位系统主要由BASE板、可调伺服机、固定式限位机构和零件支撑面组成。其中可调伺服机的选型比较复杂,需要考虑零件质量和运行速度,最后计算工作节拍时间,并验证是否满足工位节拍设计。系统工作节拍时间是由加速时间、匀速时间、减速时间和稳定时间决定的,其中加速时间、减速时间和匀速时间由设备运转条件求得,稳定时间因电机种类、负载及定位宽度等条件而不同,选定参考值为0.2s。速度、时间和行程关系如图4所示。

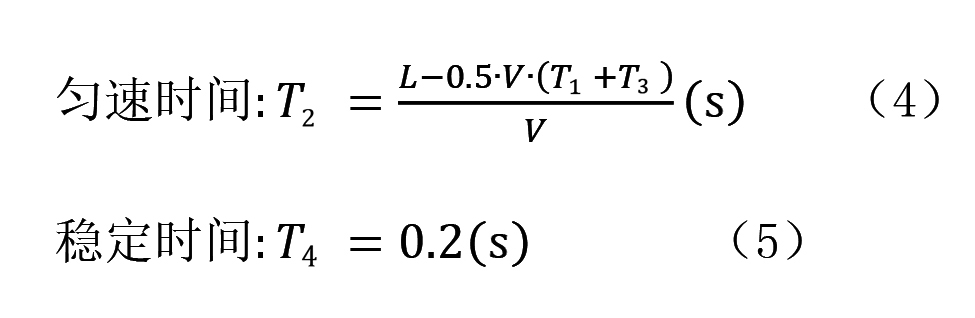
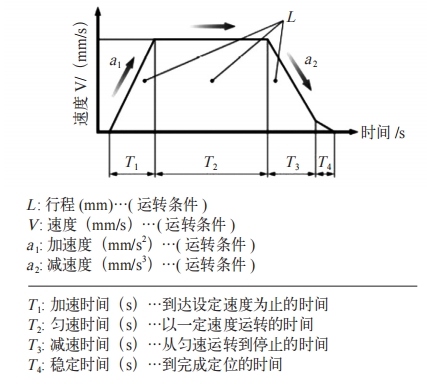
图4 系统工作节拍时间计算方法
除了考虑可调伺服机的选型,定位系统设计的难点还包括定位单元的设计。以车顶多车型柔性伺服对中定位系统(图5)设计为例,在车顶前端设置X向固定定位边单元,所有车型以此为共用基准。在车顶左右两侧设置Y向可调定位边单元,以适用不同宽度车顶。
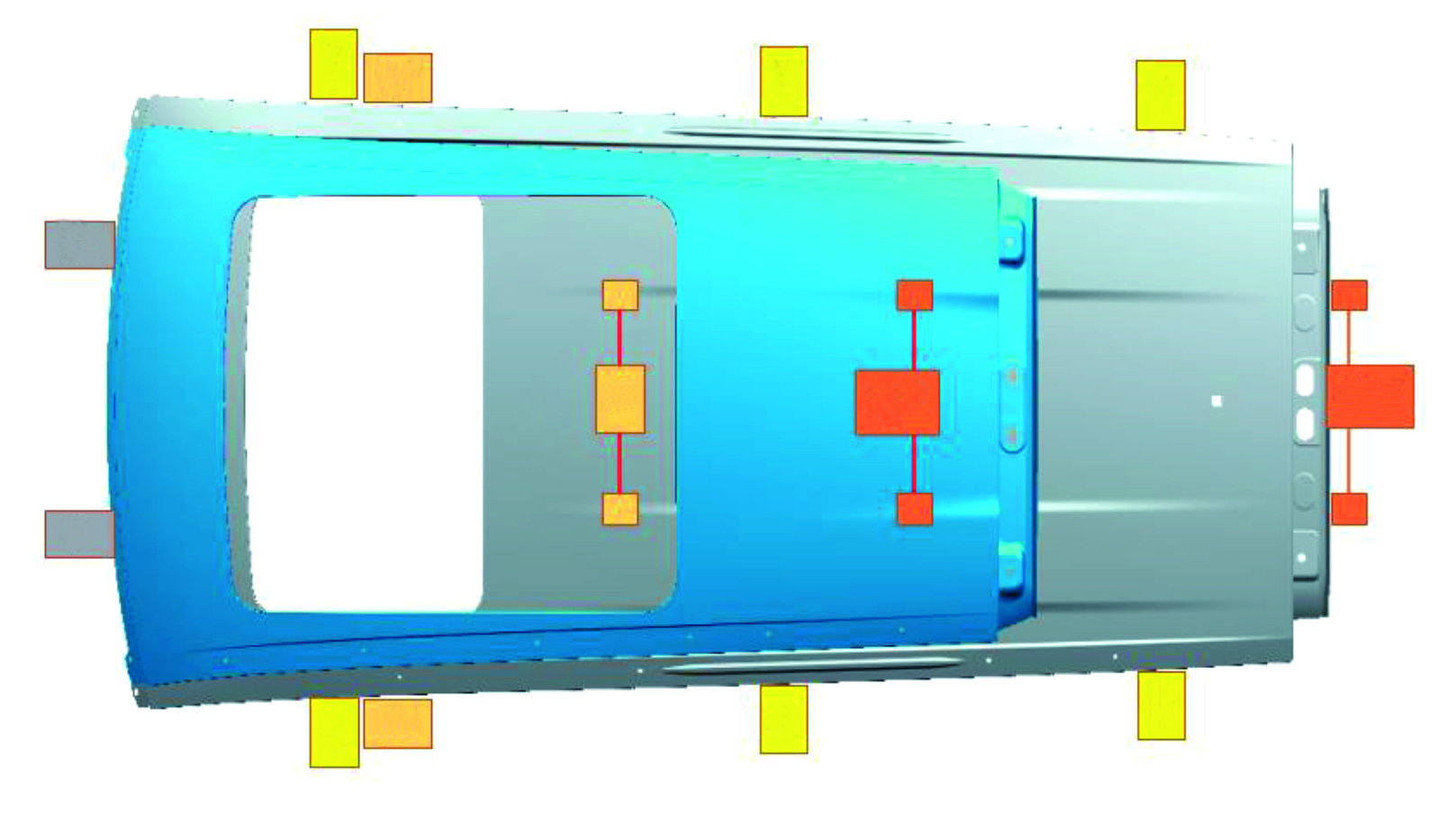
图5 车顶多车型柔性伺服对中定位系统
在车顶中部设置Z向可调定位面单元,以适用不同高度车顶。在车顶后部设置X和Z向可调定位面单元,以适用不同高度和长度车顶。针对面和边的定位单元,我们还开发了大曲率的球形和圆柱形容差定位单元,通过点接触的方式来实现不同型面零件的柔性定位,具体如图6所示。
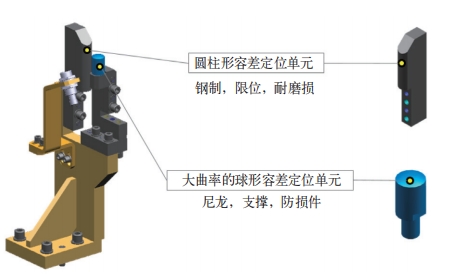
图6 定位单元
5 控制系统设计
根据系统工作流程,控制系统应用工控机对伺服机构进行编程控制,也可通过离线编程将预设程序导入此系统,PLC作为主控制系统,与产品车型和轨迹程序进行数据信号通信,通过对一轴、两轴和三轴伺服机构运动位置及速度的便捷、精确控制,驱动定位单元到达不同的空间位置,实现对不同尺寸零件的对中定位。零件的定位位置信息也会实时反馈给PLC,PLC会对反馈的位置信息处理,优化调节零件下次对中位置。PLC还与HMI连接,实时交换和显示控制器状态和反馈的位置信息。控制系统原理如图7所示。
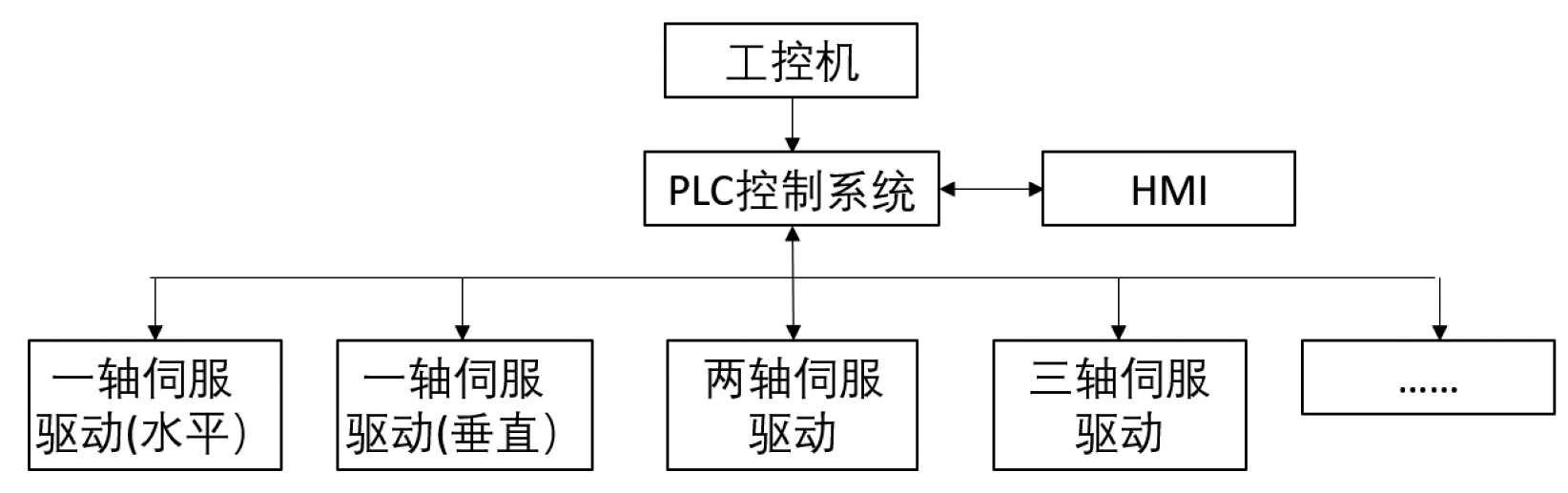
图7 控制系统原理
为了满足不同车型零件的生产需求,系统可选用手动控制模式和自动控制模式。在更换不同车型零件时,在手动模式下对设备进行运行调试。设备调试后,可以进入自动模式,系统开始自动收集相同零件的多次定位数据进行后台处理,自动优化和校正驱动系统位置。
6 结论
在车顶上料工位设计多车型柔性伺服对中系统(图8),安装调试设备后,可放置6种不同尺寸车顶。长度尺寸最小为1320mm,最大为2530mm。运行结果表明,系统可以高效地完成各种尺寸车型的柔性对中。
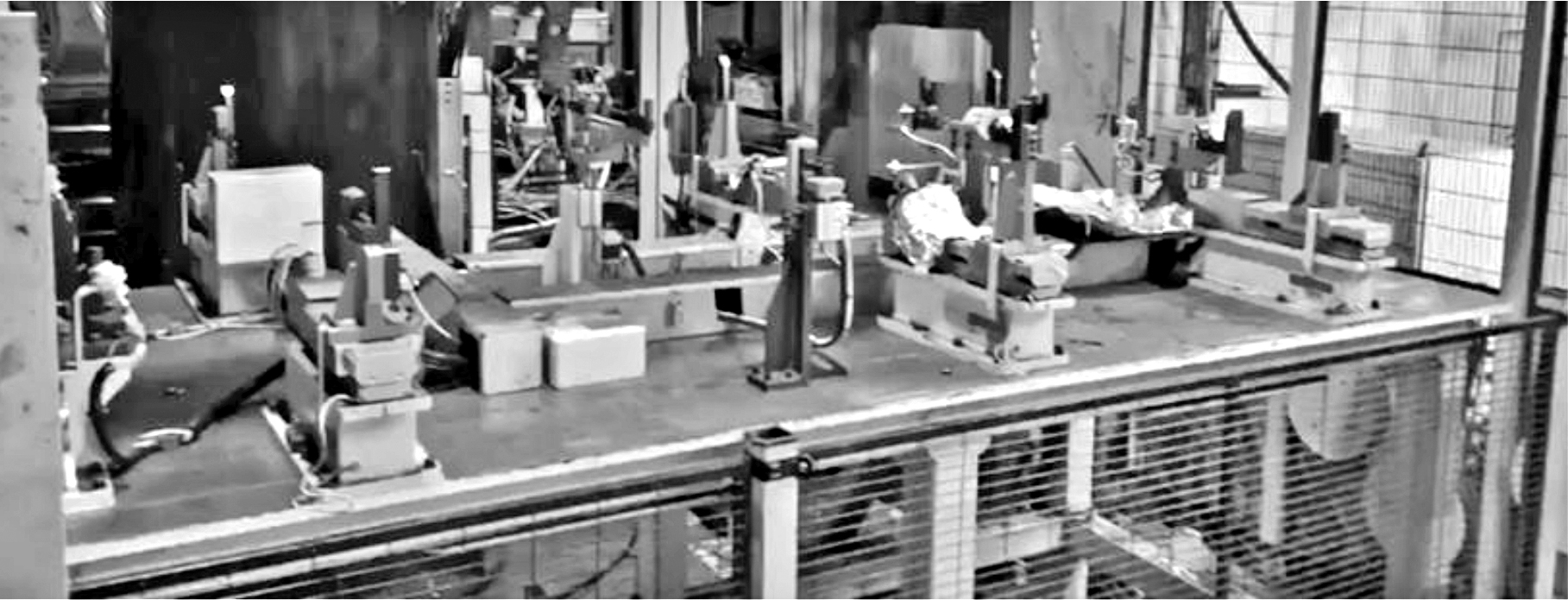
图 8 车顶多车型柔性伺服对中系统
该多车型柔性伺服对中系统具有高柔性、可编程、切换速度快、自动优化位置、定位精度高和综合投资低等优点,在有效解决差异化车型生产带来的导入产品周期长、线旁空间不足问题的同时,还可大大降低新产品引入成本,对于推动汽车行业高柔性、智能化生产有重要意义。
参考文献
[1] 聂建军,吕亚磊,李辉,等.多回转阀门智能电动执行器传动机构的开发[J].机电工程技术,2015,44(3):6-8.
[2]李鑫,袁爱进,刘洲.基于DSP实现的智能电动执行器的设计[J].仪表技术,2008,(3):2l-23.
本文为“AI汽车制造业”首发,未经授权不得转载。版权所有,转载请联系小编授权(VOGEL100)。本文作者:陈丹丹 田生,单位:上汽通用汽车有限公司。责任编辑龚淑娟,责任较对何发。本文转载请注明来源:AI汽车制造业
评论
加载更多