技术先进性、创新亮点、应用前景
背景介绍:热成形钢作为车身超高强材料,在汽车安全设计中扮演着至关重要的角色,堪称“汽车安全堡垒”的代言人。目前,市场上的主流车型车身主要采用1500MPa级别的热成形钢,以兼顾强度和安全性。然而,为了进一步推动汽车轻量化并提高燃油效率,近年来2000MPa热成形钢逐渐被引入车身结构件中。尽管强度的提升有助于减轻车重并增强结构强度,但这种单纯追求强度的做法也带来了显著的性能平衡问题。最突出的是氢脆引发的延迟开裂风险大幅增加,以及韧性明显下降。氢脆现象会使材料在潮湿环境或应力状态下失效开裂,进而影响其长期耐用性和安全性。这些问题限制了2000MPa热成形钢的应用场景,导致其无法广泛应用于量产车型,阻碍了轻量化技术在汽车领域的进一步推广。因此,如何在提升强度的同时,优化韧性并抑制氢脆现象,成为了高强度热成形钢研发中的关键技术难题。
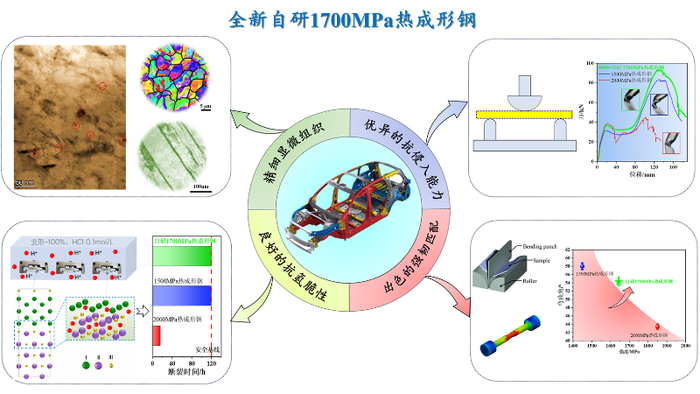
技术先进性:理想汽车携手清华大学与马鞍山钢铁股份有限公司,经过数年联合研发,成功推出了强度达到1700MPa的高强度热成形钢。该材料不仅比1500MPa热成形钢高200MPa,而且抗氢脆性能和弯曲韧性基本不损失,远超2000MPa材料。这项技术为全球首创,填补了行业空白,标志着热成形钢技术的重大突破,推动了汽车材料在轻量化与安全性领域的进一步发展。
创新亮点:摒弃传统的成分设计思路及显微组织结构分布模式,采用经济高效的多元合金成分设计,巧妙引入多尺度析出物对基体进行强化,同时实现晶粒细化。该析出物不仅有效提升了材料的强度与韧性,还能捕获材料中的游离氢,从而大幅降低氢脆敏感性。在此基础上,摒弃传统的单相组织设计,通过优化生产工艺,引入多相组织结构,进一步改善其韧性和氢脆性能。这种多组织结构设计在保留高强度的同时显著提升了材料的整体韧性,这一创新设计为解决高强度-高韧性-优异抗氢脆性能之间的技术矛盾提供了全新的思路,开辟了一条有效的技术路径,为新一代高性能材料的发展奠定了坚实基础。
应用前景:目前,1500MPa热成形钢在白车身中的应用占比约为10-40%,在车身结构的关键部位起到了重要的承载和保护作用。随着强度更高的1700MPa热成形钢材料的成功研发,它能够直接替代现有的1500MPa材料,在不牺牲韧性和抗氢脆性能的前提下,提供更高的强度。这一材料的广泛应用前景极为可观,尤其在汽车轻量化、安全性提升和燃油经济性改进等方面,将成为下一代汽车制造中的关键技术。
市场表现及未来发展趋势
1700MPa热成形钢的应用将助力汽车制造商降低生产成本、提升车辆性能,使其在高端车型和电动汽车中具备更强的竞争力。其高强度、优异的抗氢脆性能和良好的韧性,使得它成为下一代车身设计的首选材料,满足了市场对高安全性与高效能的双重需求。随着汽车制造向智能化、电动化转型,这类先进材料的市场份额预计将持续增长。
未来,随着汽车轻量化趋势的深化,1700MPa及以上强度级别的钢材将在更广泛的车身结构和部件中得到应用,尤其是在碰撞吸能区等关键安全部件上,预计其占比将逐步提升。另外,由于新能源车对轻量化要求更加苛刻,1700MPa热成形钢将在电动车及混合动力车的车身设计中扮演重要角色,为车辆续航里程提升和电池布局优化提供支持。