企业智能制造产线/车间/工厂介绍,行业及政府认定
1.项目思路
SMC制造的自我革命、数智低碳改造之路:
持续坚持精益制造理念,寻找更优的经济批量,为实现JIT的生产节奏而努力;
贯彻《智能制造2025纲领》要求,夯实数字化、自动化的基础上,优化计划生产的管理模式,积极探索柔性生产、智能制造的方法;
以低能耗、低污染、低排放为纲领,引入外部节能技术,活用自有气动节能技术,响应全球绿色低碳制造的号召,建设绿色生态工厂。
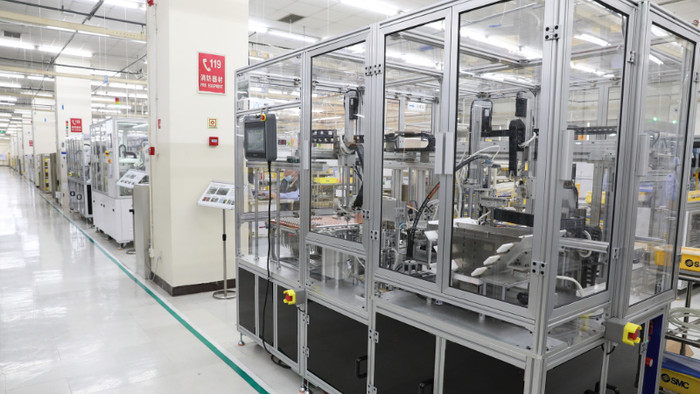
2.项目实施内容
①加工、装配生产线自动化、数字化
通过互联网接收生产指示,依据指示自动切换生产所需参数,元件配料、成品生产过程、包装入库实现ALL自动化。
②系统集成、互联
实现车间生产要素包括人、设备、自动化装置等与信息系统之间的互联互通。通过MES系统进行管理,以MBOM和工艺数据为基础,高效执行工单配发与订单交付。同时满足批次质量追溯的数据采集和管控要求。
③仓储物流智能化
引入了PDA个人数字助理、APS高级排产系统、WMS仓储管理系统、供应商平台管理系统及AGV智能搬运系统等,仓储物流效率显著提升。仓储物流人员大幅减少,仓储空间利用率再次提升20%以上。
④能源管控
通过计量仪表的智能化、数字化,建立公司内部的能源数字化管理平台,实现能源精细化管理、配电室无人值守、附属动力设备运行、故障数字化诊断等数字化转型。
⑤活用外部低碳技术及自有气动节能技术
绿电的大范围应用,老旧设备更新与节能产品导入,环保的冷媒技术替代,泄露治理与能源二次利用等。通过以上多措并举,实现了空压能耗降低28%、蒸汽用量减少6成以上的综合成果,并在“北京市节能技改专项课题项目”中也获得很高认可。
3.主要创新点
①以人为本,以沉淀出一支优秀的管理、技术、技能团队为最大价值,以培养出优秀的、解决实际问题的团队为价值观,实践长效以人为本的工厂智能化、合理化改良改善的企业文化。
②核心设备柔性化、互联化,自动装置标准化、模块化、通用化
以汽车制造装备元件-自家气动产品和技术为基础,建立符合自身生产需求的自动化生产线,并致力于提高设备自动生产和柔性生产能力,同时自主研发的自动装置以标准化和模块化为基本要求。
③IT工具持续导入,以自开发系统为主,最大限度满足生产的灵活需求。
4.显著成果
项目实施完成后,绩效指标方面及成果如下:
- 经济效益:生产年产量增长66%;
- 生产效率:工时效率提升12%,单位面积生产效率提升93%;
- 质量管控:产品合格率进一步提升,符合6Σ要求;
- 设备稼动率:由84%提升至88%,提高4%;
- 实现空压能耗降低28%、蒸汽用量减少6成以上的综合成果;
- 综合能耗由0299吨标煤/万元,下降至2021年的0.0168吨/万元,下降44%,碳减排数据可观。
- 近些年来,SMC公司成体系化的八大气动节能方案、一站式多品类的节能气动产品供给,公司专业团队已向近200家汽车及零部件制造业用户提出了行之有效的改善方案并实施。