项目要点及显著成果
中国汽车市场进入激烈竞争的下半场,发动机生产制造的成本和效率管控尤为重要。传统生产管理通过精益生产方式及6σ理念的技术应用继续发挥着关键作用,但当下主要受制于人员、市场等综合因素影响,制造业的降本增效压力很大。鉴于此,上汽通用五菱(SGMW)动力总成团队,组建自主的数字化团队,开展效率分析,能源管控,设备管理提升等数字赋能提升应用及自主打造低成本的AI视觉防错应用。
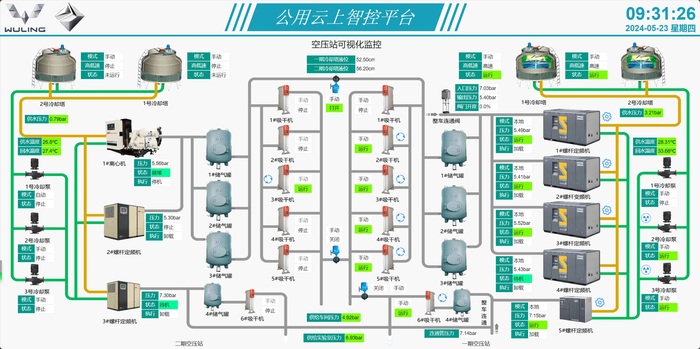
1、项目要点:
(1)统一数据需求。针对SGMW各分公司的业务,打造统一的数据需求,围绕效率提升,成本管理等各方面梳理相关数据类型,采集逻辑,存储要求等;
(2)统一采集架构。整理分析动力总成生产线各类设备通信协议,利用C#工具打通modbus,FOCAS,OPC等通讯协议;程序开发架构化,模块化,各生产基地可快速部署;
(3)统一分析架构。为提升用户使用体验,方便数字化应用模块在基地间推广,统一了基于VUE前后端分离的数据分析架构。进而在生产模块,能耗分析监控模块,设备健康管理,异常实时通知模块;
(4)统一的AI视觉开发。生产线各工位,需要投入更多的视觉检测工序,公司投入压力大。利用2D开源视觉目标识别的算法优势,学习消化后集成低成本视觉硬件,大幅降低视觉投入成本。
2、项目成果:
(1)自主打造的数字化采集分析系统,直接赋能生产管理,设备管理,能耗管理,人员优化等应用:
1)生产管理模块通过设备运行时间记录,可自动分析停机时间,停机状态,空满位状态。以手动工位为例,员工操作节拍是否符合设计标准,有无改进空间可通过详细数据分析展示出来;通过整体工位分析,从而为工艺改进,人员优化做精准数据支撑。整体实现员工优化10%,装配线线速提升2JPH,节拍操作符合率提升25%。
2)基于能耗指标探索最佳生产模式。通过自动采集生产线能耗数据,并与产量数据匹配,在对生产进行有效管控的同时进而获得能耗跟踪的小时,天,周,月的指标,为生产探索最佳的排产模式提供数据基础;运行能耗成本整体降低10%。
3)探索设备健康管理的应用。基于关键部件的动作时间,负载等自动采集对设备动作,加工异常进行有效监控,方便设备管理团队精准维护设备进而减少设备停机时间;对电机电流,运动部件振动数据等开展时域,频域分析应用,为高价值部件的维护、更换提供精准数据支持;
4)生产运行过程监控异常,通过飞书,微信等实时通讯传达到相关人员,方便生产运行团队迅速响应。
(2)低成本AI视觉防错的开发。学习消化yolo等开源视觉算法,利用modbus等与工位PLC通信,以上汽通用五菱重庆分公司为例,通过应用自主开发的视觉防错模型,实现了在生产线批量防错应用,并在整车场景中实现推广,节约成本投入220万元,并向供应链推广。
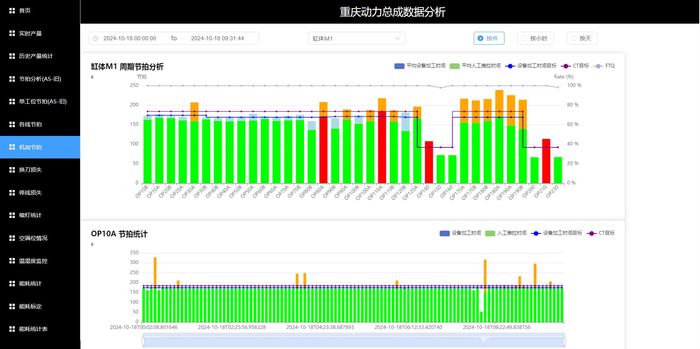