技术先进性、创新亮点、应用前景
东风日产创新开发的整车车门工艺,通过车门工艺一体式自动化装配、焊接系统,在行业内首次实现一台协作机器人完成拿取、紧固和焊接等不同工艺作业。该系统采用人机协作模式,结合轻量化柔性夹具和视觉精准定位技术,显著提升了装配精度和生产效率。创新的紧固工具设计和铰链输送设备,进一步优化了作业流程,确保了生产一致性和稳定性。
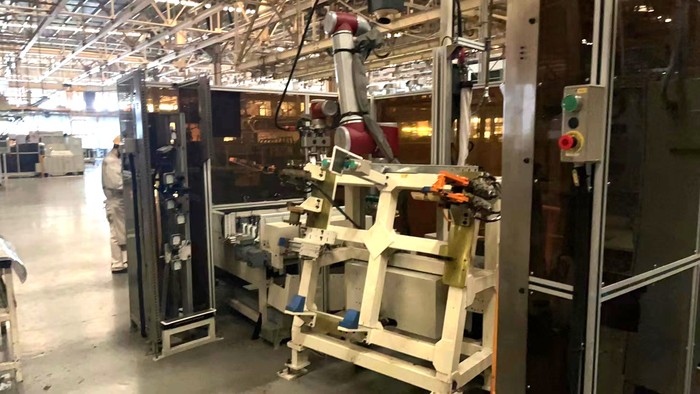
1、项目要点:
(1)人机协作模式,性价比超过的自动化模式,人工主要负责简单、轻松的上料作业,机器人承担了更为复杂和劳动强度大的任务,在视觉系统的引导下,精准地进行定位、紧固、焊接等作业;
(2)轻量化柔性夹具的开发及应用,该夹具采用集成化设计,集紧固和焊接工艺于一体,提升了作业效率。其模块化设计保证了对不同车型的适应性,而搭载低负载协作机器人的应用,降低了成本并提高了操作灵活性,展现了智能制造在汽车制造中的应用潜力;
(3)视觉精准定位的开发及应用,视觉精准定位系统通过工业相机和先进图像算法实现车门组件的快速精准识别。该系统能够自动调整机器人作业轨迹,减少误差,提升装配一致性和可靠性,其灵活性支持多车型生产,增强了生产线的适应性和扩展性;
(4)铰链输送设备及柔性夹具的协同创新及应用,通过精密输送机制和控制算法,实现了铰链的稳定输送和高精度装配。该技术采用仿形模块化设计,适应多种尺寸的铰链,同时夹具的仿形电磁铁机构可根据铰链形状自动调整,确保搬运稳定性。这种协同作业不仅提升了装配精度和一致性,还展现了智能制造在提高生产效率和质量方面的先进性;
(5)紧固工具创新改造,实现一枪多套筒,可变距的高效柔性化紧固模式,显著提升了紧固工艺效率,同时确保每个紧固点的力矩精确无误,提高了紧固的可靠性,并避免因力矩不当导致的质量问题。
2、显著成果:
(1)经济效益:实现了单一工厂二线每年减少劳务成本50万元。目前已经有广州、郑州工厂实施,每年可减少劳务成本100万元。如东风日产所有工厂全部导入该系统,预计每年可以节省劳务成本约450万元;
(2)项目成果:获得了东风集团最佳实践课题,共计挖掘两项专利(1、加工工具固定装置、机械臂及自动加工系统-2021220869890;2、一种拧紧组件、安装装置及安装系统 -2023109078373),这些创新不仅提升了企业的技术实力,也为行业内其他企业提供了技术参考和借鉴。