新能源技术是目前汽车行业最炙手可热的技术之一,电驱动的动力总成是这场革新的重要基础,其中又以围绕着电池的能源传输与管理最为关键。为了同时实现大电流、高可靠性的要求,就需要对电池的单体充放电进行管理和监控,特别是对电池单个模块内的温度、单个电芯的电压进行采样。
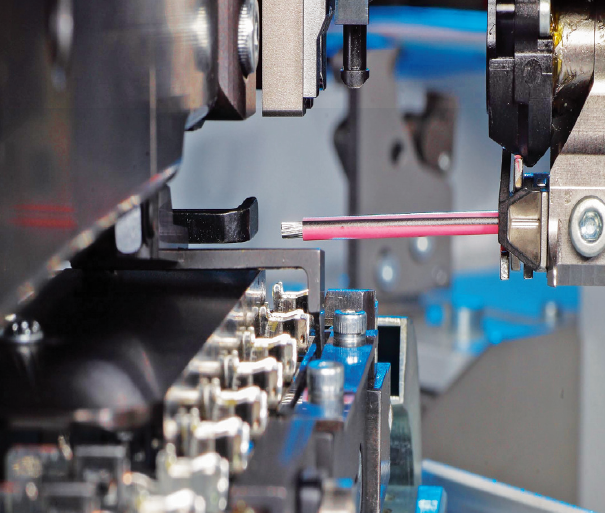
TE 可靠高效的LITEALUM 压接技术为铝吧—铝线连接方案提供保障
为了更好地实现上述功能,同时减少电池包的整体体积和重量,可以通过两种途径来实现:首先是在批量生产的电池模块内,大量应用铝作为导体,来串/并联电芯单体,利用铝的高导电性和低密度优势,来替代传统的铜条,以承载数百安培的大电流;其次是大量应用电子技术,对并联最小单位的电芯进行电压采样,同时监控电池模块内典型位置的温度,通过适当的调整充放电、平衡电流来管理电池的性能和寿命,以符合安全需求。为了监测到尽量多的电芯状态,越来越多的传感控制器件会被集成到电池模块内部。
应用背景
传统的车内电气连接技术多是围绕着铜材质的导线、电路板来开发研制的。而铝作为轻量化的导体,有助于车辆整体减重设计,在传统内燃机传动链的领域也已被大量应用,但在电池包这样大量使用铝连接的环境下,需要有新的考量。一般来说,按照电池管理系统(BMS)安装布置位置的不同,所对应的连接方案也会有所不同。
1. 情况一
当BMS位于电池模块以外时,即:利用较复杂、功能齐全的BMS统一管理多个电池模块时,电池模块内主要需要的连接形式是将铝吧上采样的信号电流电压以及充放电需要的平衡电流,通过接口连接器作为电池模块的整体界面,与外部BMS联系。需注意的是,界面连接器以及电池模块外连通BMS的线束,通常是较传统的铜材质。
2. 情况二
现今越来越趋势化的一种应用,即:BMS需要将部分甚至全部电子器件集成到每个电池模块内,目的是降低电池模组的整体高度,实现整体电池包体积的小型化、外部控制线束的简化,提高电池包整体的能量密度并全面监控,以满足更高的安全需求。这样,传统的铜基电子电路板需要和铝吧在电池模块内部进行连接。
目前的典型连接方案
对于以上这两种应用情况,都需要铝和铜之间进行稳定有效的电连接。
铝虽然导电性好、重量轻,具备成本优势,但尚未能广泛应用在电连接领域,主要挑战在于:
1. 由于铜和铝之间的元素电势差,容易发生电化学腐蚀;
2. 铝表面容易氧化,形成不导电且硬度很高的氧化层,不利于一般的连接技术,如压接、锡焊等;
3. 其他风险,例如铝的机械强度弱,长时间、高温等情况下的蠕变,铝和铜在高温时可能由于这两种元素间存在中间化合物,存在界面电阻上升、变脆的风险。
针对上述问题,采用铜铝连接后的后处理可以有效规避风险。如:在连接点进行封胶,形成气密的条件,阻断电化学腐蚀的形成要素——电解质;避免铝包铜的机械连接、在摩擦焊等工艺上控制焊接温度等。

经过内部转换后,与铜质PCB控制板互连的TE Multispring型Press-fit端子也是铜材质
这样,就可以总结出目前比较典型的连接方案。针对BMS集中布置的情况,典型的传统方案是通过铜质导线,利用摩擦焊或者电阻焊工艺连接到铝吧上,封胶后统一利用线束接口对外。针对铜制电子电路板布置在电池模块内时,也可以通过铝线引线键合(wire bonding)、铜线焊接、乃至螺栓连接等途径连接,后续再进行封胶。
上述手段虽然满足了应用,但是特殊的焊接工艺和后续的滴胶等工装设备的投入增加了成本,降低了生产效率,同时就体积而言,在寸土寸金的电池包内也不被看好。
创新解决方案
针对诸多挑战,TE Connectivity(以下简称为“TE”)提供了多种新思路来实现性能可靠、生产高效的铝—铜连接方案。
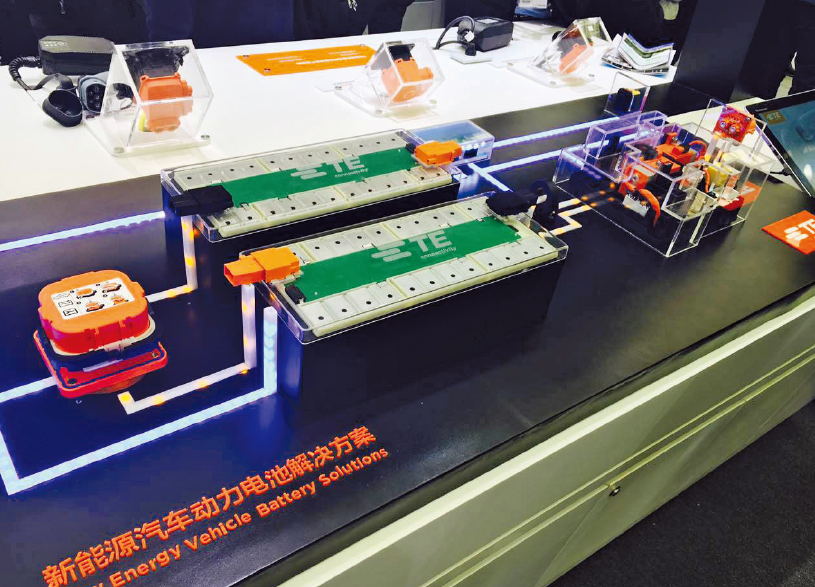
TE 电池内部互联板(ICB)总成
针对情况一,TE提供LITEALUM铝线压接技术——这种技术兼容传统高效的端子压接工艺,利用结构优化的铜制端子,稳定有效地压接各种线径的铝导线,已经被广泛验证并应用在传统动力汽车中。利用LITEALUM压接的铝质线束,可以直接焊接在电芯连接的铝吧上,由于铝—铝之间同元素的连接,无需担心前面提到的风险。
针对情况二,TE提供完整的经过铝—铜转换的内部连接板ICB总成。凭借先进的技术手段,TE实现了ICB内部铝吧与铜质press-fit(免焊压接)压针的连接,并且整体包胶注塑。用户只需将完成的电子器件组装的电路板总成机械地压入ICB,即可完成组装与连接,无需焊接等工艺,不损伤BMS电路板,还可满足三次的BMS电路板拆装更换需求,以便用户最大程度降低昂贵的电池模块的替换成本。
未来,TE还将提供更多的选择,例如铜—铝双金属转换连接等技术,以满足客户更多样化的需求。
总结
电池内大量应用铝材质,虽然给传统连接技术带来了新的挑战,但是只要针对可能存在的风险采用对应的技术手段,新的方案和思路会更有助于成本的优化和效率的提升。传统的连接技术也将为新能源汽车事业的发展保驾护航。
评论
加载更多