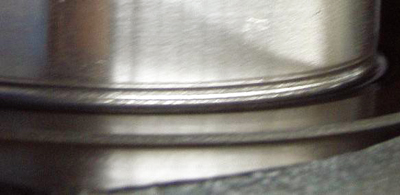
图1 圆角不成形,过渡不光滑,表面粗糙度差
针对沉割槽加工中存在的缺陷,本文从理论和实践两方面对影响加工质量的主要因素进行了分析,提出了相应的解决办法,并制定了相关企业标准,使圆角滚压强化工艺真正成为曲轴“以铁代钢”的重要手段。
曲轴是发动机中的关键零件,工作时承受很大的弯曲应力和扭转应力,其常见的失效形式为轴颈磨损和疲劳断裂。轴颈磨损通过采用离子氮化等工艺可以得到很好的解决,疲劳断裂则往往比较棘手。国内外的生产实践证明,圆角滚压对提高曲轴疲劳强度有显著作用。目前汽车曲轴以及工程机械用发动机曲轴越来越多地采用圆角滚压强化工艺,国外轿车发动机曲轴几乎全部采用圆角滚压工艺。由于圆角滚压可大幅度提高疲劳强度,并可大幅度降低材料成本,因此曲轴圆角滚压强化工艺已成为提高产品竞争力的重要手段。
圆角滚压强化工艺最常用的方法是先在轴颈过渡圆角处沉割出与滚轮半径大小相同的圆角进行滚压。采用圆角沉割的方式滚压可以使应力分散,是最为成熟的加工方法。此方式滚压对沉割槽的加工质量要求较高,沉割槽质量的好坏是圆角滚压强化效果优劣的关键因素之一。
沉割槽常见缺陷及其影响因素
在实际生产中主轴颈圆角沉割槽是在精密车床上用成形刀车削而成,一般出现的圆角沉割槽缺陷有两种:一是圆角不成形,过渡不光滑,表面粗糙度达不到工艺要求,如图1所示;另一种是圆角沉割振纹,如图2所示。这两种缺陷都将造成圆角滚压时圆角表面不能充分与滚压轮接触,滚压效果很差,导致曲轴的抗疲劳强度降低,给曲轴在发动机中的运转埋下了安全隐患。
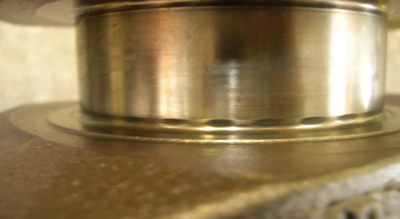
图2 圆角沉割振纹
1. 圆角不成形,过渡不光滑,表面粗糙度差
(1)刀具不成形,刀刃粗糙度差。当采用手工操作、内R规对刀的方法磨刀时,往往达不到规定要求,而且手工操作磨刀刀刃较粗糙。这时加工出的圆角沉割槽就存在不成形、表面粗糙度差的缺陷。
(2)刀具刃磨频率低,出现烧刀现象。圆角沉割工序刀具切削力较大,切削面广,很容易发生烧刀现象,如不及时磨刀,就会出现所加工沉割圆角表面粗糙度差的缺陷。
(3)刀具后角太小,刀刃安装高于机床主轴中心高。刀具后角太小,切削刃就不锋利,容易产生挤刀现象;刀刃安装高于机床主轴中心高,切削时刀刃不吃劲,这时将出现沉割圆角表面粗糙度差,甚至出现拉毛、挤伤等缺陷。
(4)机床主轴轴向窜动超差。机床主轴轴向窜动超差,造成刀具切削环境变差,势必造成圆角沉割槽表面粗糙度差、与轴颈和侧面过渡不光滑等缺陷。
(5)曲轴材质及表面硬度的影响。材料延伸率较高和表面硬度较低的曲轴在进行圆角沉割加工时较容易,质量也好控制。遇到高硬度脆性材料时出现缺陷的几率会增加。
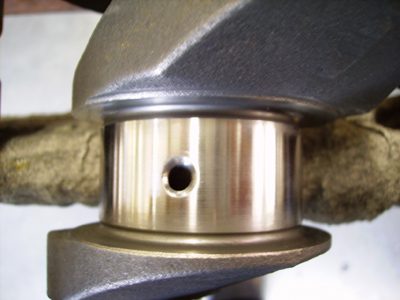
图3 沉割槽质量明显改善
2.圆角沉割振纹
圆角沉割振纹的主要原因是机床振动造成的,从振动的本质上来划分可分为强迫振动和自激振动两大类。
(1)强迫振动:强迫振动是由外来的周期性或非周期性的刺激力所引起的。主要有以下特点:①强迫振动本身不能改变刺激力,刺激力一般与车削过程无关(除由车削过程本身所引起的强迫振动外)。刺激力一旦消除,振动就会停止。②在一般情况下,强迫振动的振动频率与外界周期性刺激力的频率相等,或是它的整数倍。③刺激力的频率与工艺系统的固有频率相等或接近时,产生共振,振幅达到最大值。④强迫振动的振幅与刺激力、工艺系统的刚度及阻尼大小有关。刺激力越大,刚度及阻尼越小,则振幅越大。
(2)自激振动:俗称颤振,是在没有外来周期性刺激力的条件下所产生的振动,是由振动系统本身在振动过程中激发产生的交变力所引起的不衰减的振动。即使不受到任何外界周期刺激力的作用,振动也会发生,当车削运动停止时,振动才会消失。自激振动的特点有:①自激振动的频率等于或接近于系统的固有频率。按频率的高低可分为高频颤振(一般频率为500~5?000Hz)及低频颤振(一般频率为50~500Hz)。②自激振动能否产生及其振幅的大小,决定于每一振动周期内系统所获得的能量与阻尼消耗能量对比情况。③由于维持自激振动的刺激力是振动过程本身激发的,故振动中止,刺激力及能量补充过程立即消失。
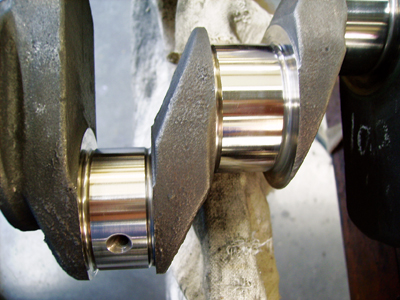
图4 采用磨削沉割槽的加工效果
振动产生的根源
1.强迫振动产生的根源
(1)由于机床传动零件的缺陷所引起的振动。主轴前端卡盘的径向跳动值超差,必然会引起旋转时振动,沉割曲轴时容易产生振纹。
(2)由于旋转的工件和机床零部件(皮带轮、卡盘等)不平衡时,因离心力的作用在运转时产生周期振动。这主要有以下几个方面:①曲轴工件在车削前不平衡量太大,造成振动。②机床主轴组件本身不平衡, 包括皮带轮不平衡等。③由外部振源传给机床的振动,例如其他机床振动通过地基传递给本机床。
2.自激振动产生的根源
自激振动是在车削过程中产生的,它所消耗的能量是靠车削过程中来维持的。因此,自振系统可看成是一个由固定能源(电机)、振动系统(工件及机床)和调节系统(动态切削过程)所组成的闭环反馈自控系统。
引起自激振动产生的原因,主要有以下几个方面:
(1)车削过程中,由于外来干扰产生的强迫振动或前一次切削在加工表面留下波纹时,就会引起车削厚度的变化带来切削力的变化而引起的振动,即“再生振动”。
(2)在车削加工过程中,刀具与工件间相互位置受到干扰,使它们间除作正常的车削运动外,还作周期性颤动。
(3)刀具被铁屑堵塞或磨钝后不及时磨刀,车削曲轴时会使刀具与工件表面产生挤压,从而诱发自激振动。
防止缺陷产生的措施
针对圆角沉割槽缺陷的特点和产生缺陷的根源,必须采取措施予以消除和控制,通过制定《圆角滚压曲轴滚压前沉割槽质量验收标准》等执行严格的检查制度。在生产实践中采取以下措施:
1.刀具要及时修整。实践证明,车削20条四缸曲轴时,就必须修磨一次刀具,个别磨损时应及时修磨。
2.保持机床应有的精度,三爪卡盘精度丧失后及时更换卡盘。
3.尾座顶尖更换较大的型号,以提高曲轴的夹持刚性。
4.试验采用弹性刀杆,避免自激振动的产生。
5.增加磨削沉割槽的方式代替车削。
6.对工序更换操作者时实行岗位技能培训,合格后方可上岗操作。
我厂通过采取了一系列行之有效的措施,圆角沉割槽质量得到了明显的改善(见图3)。采用磨削沉割槽的方法,效果更佳(见图4)。
结语
曲轴圆角沉割切削属于成形加工,切削质量与刀具和机床有着密切的关系。针对不同的曲轴材质和沉割槽参数,制定合理的加工方案,才能改善曲轴圆角沉割槽的质量,使圆角滚压强化工艺真正成为曲轴“以铁代钢”的重要手段。
评论
加载更多