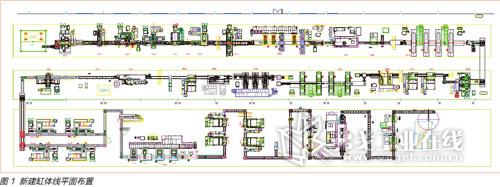
本文阐述了新建4DA/4DB发动机缸体加工自动线的规划思路和工艺设计,介绍了该生产线的技术要求、工艺流程和设备配置情况,分析了生产线重点工序采用的新技术和新工艺。
4DA/4DB系列发动机开发于20世纪80年代,在轻卡、轻客及工程机械等领域有着广泛的配套应用。随着国家汽车排放标准不断提高,该产品经过不断优化改进,达到了国Ⅲ、国Ⅳ的排放要求。为满足产品升级换代后批量生产的要求,我公司决定新建一条4DA/4DB缸体加工生产线(以下简称“新建生产线”)。
总体规划
1.组线形式的选择
当前缸体加工线的组线形式主要有两种。第一种是采用加工中心组成全柔性生产线,其优点是能使制造系统灵活、快速响应产品设计变更和市场需求变化,能实现不同系列、不同型族的缸体多品种共线生产,但一次性投入大,关键工序的生产效率相对较低,生产成本较高。第二种是采用专机和柔性加工单元混合组线,其优点是生产效率高,生产成本较低,一次性投入较小,并具有一定的柔性能力,适用于同型族、多系列的缸体生产,但难以实现不同型族的缸体共线生产。我们在作了大量调研论证后,决定采用第二种组线形式。
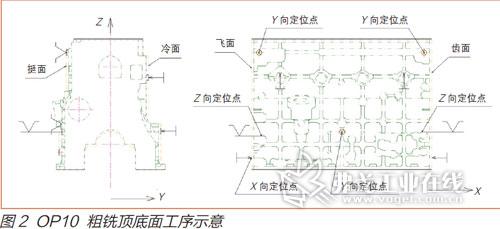
2.建线规划
新建生产线主要承担4DA/4DB国Ⅲ、国Ⅳ缸体的加工,生产能力为8万台/年。按照先进、可靠和高性价比的原则,在多年积累的工艺经验的基础上,我们借鉴国内外同行业的先进工艺,采用一流制造设备,以专用机床为主,配置一定数量柔性加工单元,要求实现全线自动,在确保生产效率的基础上,具备适应产品变化和改进的柔性能力。计划建成一条品质保证好、生产效率高、制造成本低、设备投资少并达到国内同行业先进水平的缸体加工生产线。设计纲领如表1所示。
工艺设计
1.工艺要求
(1)全线实现4DA/4DB系列缸体共线生产,在设计主参数不变的基础上,具备新开发机型缸体的加工能力。已定型的加工部位一般采用专机,变化多的部位和采用专机经济性不好的工序,采用柔性加工单元。通过调整夹具定位块或夹紧行程的方式,实现不同冲程的缸体换型。
(2)在确保节拍时间平衡的前提下,广泛采用多工位设备,提高工艺复合率,减少设备数量。柔性加工单元的选型要具有足够刚性、功率和转矩,确保满足产品设计要求和工艺优化的需求。
(3)设备工程能力指数Cpk≥1.33,部分关键工序按压缩10%~20%公差的方式验收。各段生产线均设置检测工位,配备在线专用检具和量具,关键工序配备自动检测、反馈调整装置。并配备机型识别和自动打标装置。
(4)除线首、线尾人工上下料外,工件全部自动输送,机床之间由机动滚道、自动送料小车连接,部分辅助工序由人工操作。
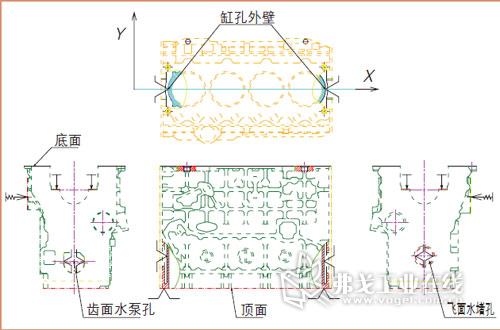
图3 OP50精铣底面、钻铰定位销孔工序
2.工艺流程及设备配置情况
新建生产线工艺流程如表2所示,共有设备共58台,包括主要设备46台(其中自动线7条,卧式柔性加工单元8台),辅机12台。全线设有总集中监控台,各段自动线设有分段控制台。全线各机床具有单机手动、单机自动及联机自动三种工作方式,能自动进行故障诊断并报警。
生产线大量采用了多工位设备,高精度机床的基础部件采用铸件,进给部件均采用伺服滑台。攻螺纹全部采用无靠模NC形式。专机的数控系统及PLC采用三菱公司产品,电气、液压和气动元件均采用合资企业的产品。采用国内外技术成熟的先进刀具。
柔性加工单元的工作行程为800mm(X轴)、630mm(Y轴)、和600mm(Z轴)。主轴为HSK100机械主轴,转速为100~6000r/min,换刀时间5s以内,刀库容量为30把。控制系统采用FANUC-18iMB。
全线采用湿式加工,单机排屑,配置吸雾装置。各段自动线设集中液压站,配置冷却装置,控制阀组分散布置。各机床采用定量容积式集中润滑装置,大流量冷却冲屑,配备独立的切削液处理装置。关键设备切削液处理配置了进口恒温装置。
3.生产线平面布置
新建生产线布置在两跨21m的厂房内,占地面积3845m2。生产线呈S形布置(见图1),两排设备之间留有安全通道,两端采用地面自动送料小车连接。各段生产线之间留有一定的工件存放场地。设备和公用工程全部采用空中布线,废水或切削液排放至集水坑内,再送至污水站处理。
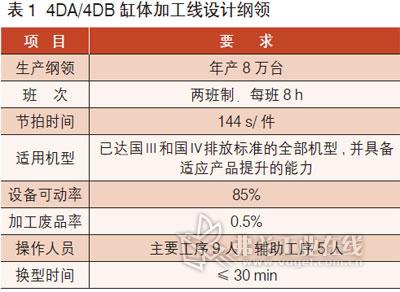
关键工序的工艺特点
1.粗铣顶、底面
OP10工序采用双卧组合铣床粗铣顶、底面,工件卧置,挺面向下。在工艺设计中,选择了挺面上3个搭子,挺面2个凸台侧面和飞面作为定位点(见图2),以保证加工后的底面与内腔缸套孔轴线的垂直度。
为了保证上述定位点与毛坯内腔之间的位置精度,我们对铸造工艺提出挺面上定位的3个搭子面与内腔缸孔外壁中心的平行度小于0.5mm,定位凸台侧面与凸轮轴孔中心的尺寸精度满足±0.5mm的技术要求。经多次检验,加工后的缸孔上下截面壁厚差(以此代表缸孔轴线与底面的垂直度)能够控制在1mm以内,主凸孔加工余量的均匀性也控制在1mm以内。
2.精铣底面、钻铰定位销孔
我们提出了缸孔壁厚差(即加工后缸孔最大壁厚减最小壁厚)最大1.5mm的技术要求。我们对此项要求进行了工艺分析:缸孔外壁是铸造而成的,缸孔壁厚差是铸造和机加工多项制造尺寸链的封闭环。从理论上讲,即缸孔加工的轴线与铸造形成的轴线之间的偏差应不大于0.75mm。底面和2-φ16定位销孔是精镗缸孔的定位基准。
在本工序的工艺设计中,我们直接采用了缸体齿面水泵孔和飞面水堵孔作为Y向的定位基准,采用1、4缸孔外壁作为X向的定位基准,以半精铣后的缸面作为Z向的定位基准(见图3)。
为能实现可靠定位,我们在机床夹具中设计了一种新型定位机构。该机构将轴向推靠功能和径向撑靠功能复合在一起,首先在X向上同步联动推靠两端缸孔外壁,然后在Y向上径向撑开靠紧水泵孔和水堵孔壁,这样两个方向都采用了同步自找中心的定位形式,可以将铸造过程的误差对定位中心的影响减少1/2。通过批量生产验证,本工序定位可靠,质量稳定,缸体壁厚差可控制在1.5mm之内,成为新建生产线中一项重大工艺创新。
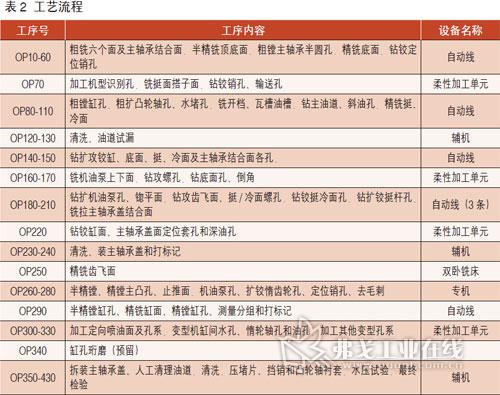
3.钻扩铰挺杆孔
挺杆孔与凸轮轴孔轴线的垂直度要求为0.04,孔的端面至底面距离为253mm。刀具悬伸长,加工难度大。本工序将8个挺杆孔分为两组,采用三台双工位立式机床组成自动线。第一台机床两工位分别进行两组孔的钻加工,第二、三台机床两工位分别完成同一组孔的扩、铰加工。为了保证挺杆孔的精度和对凸轮轴孔的垂直度,在主轴箱上装有刚性导向模架,随主轴箱运动接近孔的端面后开始加工。加工后,凸轮轴孔轴线的垂直度达到了0.04以内。
4.主凸孔、机油泵孔和止推面的精加工
4DA/4DB缸体的主轴孔直径分为φ86mm和φ91mm两种尺寸,凸轮轴孔直径均为φ62mm,精度要求为IT6。在工艺设计中,主凸孔的精加工由两台半精镗、两台精镗机床组成两条平行线完成,机床采用三面复合式。精镗机床夹具两端装有导向模架,采用德国MAPAL内冷式镗杆和导向套。止推面的加工刀具安装在主轴孔镗杆的活动滑块上。精镗主轴孔的动作顺序为:二次半精镗(推镗)—径向走刀车止推面—精镗(拉镗)。这样可使精镗切削余量较小,有利于提高表面粗糙度,且在精镗过程中刀杆受拉力作用,减少了因切削力造成的刀杆变形,同时保证了止推面的加工精度,减少了设备投入。机油泵孔半精、精加工与主凸孔加工在同一台机床上完成,保证了位置精度要求。产品换型时,通过调整镗杆上的刀夹,完成不同孔径主轴孔精镗,通过调整夹紧机构行程,适应不同冲程机型的加工。精加工后主轴孔同轴度可达φ0.02mm以内,凸轮轴孔同轴度可达φ0.03mm以内,表面粗糙度可达Ra1.6mm,孔距位置精度可达±0.02mm。
5.缸面、缸孔精加工及测量
本工序由6台立式机床组成自动线。第一台两轴双工位机床半精镗缸孔,第二台高精度立式数控铣床精铣缸面。精镗缸孔采用了两台两轴立式精镗机床,分别完成1、3和2、4缸孔的加工。每台机床装有两个高精度镗头,由两个数控滑台分别驱动。采用了德国MAPAL的内冷式精镗刀杆,进刀时进行二次半精镗,然后车止口平面、拉镗止口,此工序完后换另一把刀进行精镗。采用了数控测量反馈控制系统控制止口深度,调整精度可达0.005。精镗后缸孔圆柱度可达φ0.01mm,与主轴孔垂直度在φ0.025mm以内,止口深度控制在0.04mm以内,表面粗糙度可达Ra0.8mm,孔距位置精度可达±0.03mm。
精镗后布置了一台缸孔测量机,采用了马波斯公司的测量仪,自动测量缸孔并分组打标识。如测量数据超出控制范围,则自动反馈对精镗刀具进行补偿,补偿精度可达0.002mm,提高了精镗缸孔的精度控制能力。
结语
该缸体生产线建成投产结果表明:生产线达到了各项设计要求,工艺方案先进合理,产品质量稳定,能实现多品种、多系列缸体的共线生产,换型时间短,自动化程度高,操作人员少,生产成本较低,一次性投入较低,经济效益比较明显。
评论 0
正在获取数据......