针对国产4G1气缸体铸件加工性能差的问题哈东安展开调查与分析,通过分析比较进口气缸体铸件(以外资工厂铸造为代表)熔炼工艺,本文指出了影响4G1气缸体加工性能的主要因素,确定了改善其加工性能的主要方向。
4G1系列发动机为日本三菱公司1.3~1.6L系列灰铸铁气缸体产品,是我公司主导产品,供给DAE生产一线及其二线,其工装、刀辅具均为进口,加工自动化程度高,且为高速加工。采用外资工厂和日本进口件的气缸体铸件加工,自动化生产线能高效率生产出高品质的缸体,而采用我公司的缸体铸件进行加工时,因铸件材料加工性能差,刀具使用寿命仅为进口铸件的40%,降低了生产效率,显著增加了刀具损耗,引起了加工厂的抱怨,强烈要求改善铸件加工性能。
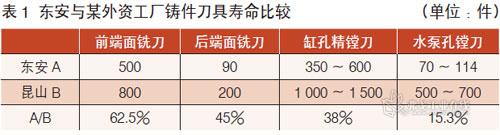
4G1缸体加工性能影响因素分析
为此,我们针对DAE生产一线几个关键工序,比较进口铸件刀具寿命作了一个数据统计(见表1)。从表1可以看出,加工厂刀具损耗抱怨主要反应在以前后端面为代表的粗加工铣刀组,以缸孔加工为代表的精加工镗刀及其他复杂加工部位的加工工序。对此,我们围绕加工废刀原因展开分析。以精加工镗刀为例,我们跟踪该工序刀具补偿量,发现外资工厂铸件刀具补偿量明显要优于我公司生产的铸件(见图1)。
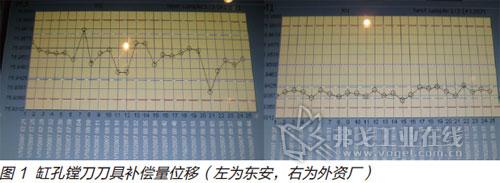
经过与DAE现场工程师联合分析发现,该工序镗刀磨损主要表现为锯齿状掉渣磨损,所以刀具补偿量波动幅度才会很大。我们初步怀疑其为铸件组织不均匀或存在硬质点所导致。
灰铸铁铸件组织性能较大程度是受其合金成分影响的,我们最先对我公司4G1缸体铸件的合金成分进行了分析,经欧洲知名INSTITUT DR.LORCHER权威检测机构得出检测数据(见图2);然后与外资工厂和日本进口件合金成分数据及力学性能进行比较。
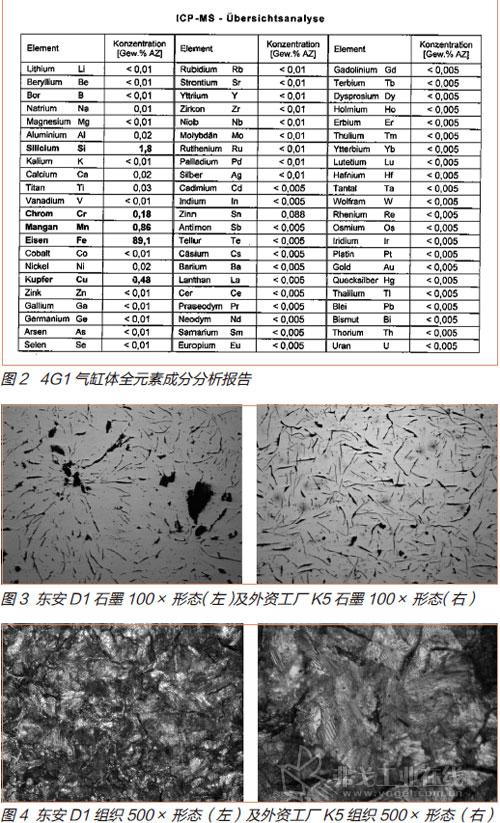
从上述数据可以看出,合金成分是东安铸件和进口铸件之间差异特性之一,也是相对比较重要的因素之一,它还直接影响了铸件的力学性能。材料合金元素比例不佳,易造成合金偏析,不利于机械切削。相对来说,进口铸件化学成分控制要比我公司铸件要求严格得多。
同时,我们还比较了两种铸件的金相组织(见图3、图4)。分析得出,合金元素对铸件组织性能有较大的影响,原来不合理的合金元素控制要求,使铸件组织中形成较多B、E型石墨,珠光体含量也偏低,且片层间距较小,倾向于粒状珠光体,极不利于机械加工。
合金元素控制不好,还容易在铸件组织中产生硬质点,基体组织中的白色“硬点”如图5所示。因此我们取铸件试块做SEM扫描分析,白色硬点被确定为Ti化合物。经过对试块做化学分析检测,发现铸件中Ti含量不大于0.03%,按照理论分析认为低于此含量,不会对组织造成影响。而且外资铸造厂虽然对Ti含量的指标有要求,但也是控制在0.03%以下。
据相关资料记载,灰铸铁基体组织的“白区”即不被4%硝酸溶液腐蚀的部分,有可能为以下几种:铁素体、渗碳体、Ti合金、SiC以及SiO2等,其中最可能的则是铁素体和Fe3C。而Fe3C作为游离态存在于基体中,极容易造成打刀。所以除了稳定铸件化学成分外,对一些合金元素,尤其是Ti、Al等有害元素也要严格控制。
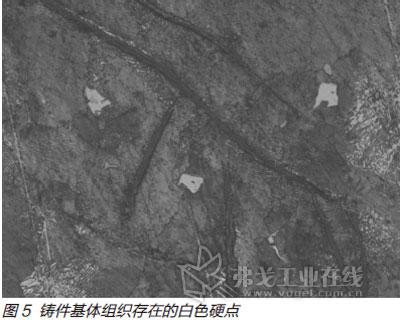
4G1缸体铸造工艺改善
围绕外资铸造厂进行理化性能及合金元素分析的同时,我们开展了对我公司熔炼工艺要求的改进试验。试验结果显示,效果还是比较显著的,同时也总结了一些实践经验。
1.化学成分控制要求改善
试制时,我公司对4G1气缸体化学成分要求都进行了细化:对S元素进行了严格控制,因为S含量低时铁液共晶成核难、长大难,容易过冷出现D、E型石墨,但S含量高时以自由状态存在阻碍石墨长大,使铁液过冷生成渗碳体。而对于Cu、Cr等强烈石墨化元素调整,主要考虑成本因素,含量满足要求即可。
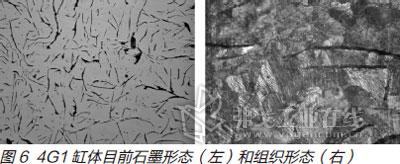
2.Si/C的实际影响作用
研究表明,在相同的CE下,Si/C比不同将导致石墨形态的不同。CE一定时,Si/C比从0.5→0.7→0.9变化时,石墨片分布类型由E型→A型→D型变化,基体组织由P+Le→P→P+F变化。试验中发现,当保持CE在3.85~4.0时,Si含量上升至2.35%时,会在铸件表面形成一层铁素体层。高Si/C比使铸铁最先凝固的表面层,析出奥氏体枝晶与过冷石墨,同时在Si的作用下,基体中的C易扩散到石墨上聚集,因而形成铁素体层,使铸件表面层软化。而这层铁素体层恰好充当铸件机械加工余量时,故可改善切削加工性能,而不影响使用性能。但同时需要注意的是,Si/C比达到0.8以上时,石墨会明显减少,性能也会发生很大的变化,也会不利于加工性能。试验中,我们在加工缸孔部位时会出现“麻点”,经分析确定为石墨块,该状态下基体硬度一般会在HB150以下(一般灰铸铁铸件要求HB180~220)。
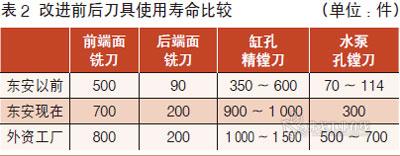
3.孕育处理变更
孕育的目的是细化灰铸铁组织,是提高气缸体薄壁类铸件机械加工性能的重要途径之一。我公司原使用传统孕育剂:稀土镁+硅锶合金+孕育硅铁复合孕育剂,这种孕育剂的优点就在于具有较强的石墨化能力,同时孕育时效长,但其最大的缺点就是成本高。目前我们使用增碳型孕育剂(C%≈35%、Si%≈45%)+Si-Ba-Ca复合孕育剂,总加入量约为0.42%。这种孕育剂特点是成本低,但其缺点就是渣量大,所以我们根据其特点改成倒包孕育,就是在浇注前倒包时加入孕育剂,同时清掉熔渣,这样做的好处就是可以有效地降低浇注温度,我公司孕育温度可控制在1450~1485℃。生产中一般认为含硅量在1.0%~2.5%时,铁液温度在1450~1500℃时含氧量保持在15~25ppm,是铁液最好的孕育时机。
4.熔化炉中成分的稳定控制
生产过程中对化学成分控制是至关重要的,一般厂家都会通过光谱仪去检测反馈,有的厂家增加CS分析仪,而这种控制仪器主要是用来监控孕育后的铁液成分,也就是说是检测产品特性的重要手段。但在实际生产过程中,对成分的控制重点是在炉中,所以我们引进了C/Si分析仪——炉前铁水质量分析仪,它的原理主要是通过检测铁液在冷却过程中的共晶和共析转变的液相温度来反馈出CE值,再通过数据库计算C%、Si%值。它的最大特点就是速度快、测量稳定,不会像光谱仪对仪器的使用环境及试样本身要求高。
除了检测仪器的使用外,最重要的还是工艺要求的细化。在保证原材料入厂合格的情况下,尽量要将配料及配料顺序明确化,这样可以提高一次出水合格率和原材料的利用率。铁液在高温情况下(一般是1500~1550℃),合金元素是在时间的推移下不断烧损的,传统的做法是通过光谱仪检测结果反馈后往炉内补料,实际上这种做法对铁液净化是非常不利的。试验结果表明,灰铸铁中的主要元素C%、Mn%等在正常出水保温1 h下烧损0.15%左右,Cr%、Cu%约是其烧损程度的一半,Si%基本不减少。
根据上述情况,我公司在出水前追加补碳。我公司使用8t中频感应电炉,每炉出水约9~12包次,我们采用每次打水后往炉内添加增碳剂的方式,补充正常的C%烧损量(正常出水下每包次间隔约8min,C%烧损为0.01%~0.02%)。这里值得注意的是,为保证补加增碳剂充分熔解,粒度尽量要控制在3mm以下。
5.其他方面的改善
(1)加工余量要合适 4G1缸体前后端面局部飞边厚大,加工余量达5mm,会造成粗加工刀具磨损大。
(2)加强现场过程控制 每浇注包铁水量要控制,主要是稳定孕育效果,使用铁水包电子秤;浇注温度尽量控制在合理范围,主要是控制铁液的过冷度;浇注后铸件的打箱时间最好在1.5h左右。
(3)砂芯涂料会对铸件表面层造成激冷效果,所以根据需要可以调整涂料工艺。4G1端芯水泵孔不涂涂料后该处刀具使用寿命从200件/刃提高到300件/刃。
改善效果
通过持续的对比进口铸件的组织及性能检测,围绕现场工艺调整试验,4G1气缸体改进后刀具磨损显著降低,与改进前相比,刀具寿命提高到3倍(见表2)。通过对现场过程操作细化及稳定控制,我公司铸件产品组织性能批次检测一次合格率能达到98%以上(见图6)。
国产铸件与外资公司及进口铸件比较还有一定差距,分析主要原因是现场过程控制及人员质量意识还要进一步加强,另外如人、机、料、法和环中的环境、设备影响也不容忽视,所以后期要对现场的工艺更加细化,对设备、环境的变动加入工艺控制文件中,做到现场可控。
结语
为改善铸件加工性能,我们可以主要从以下几个角度着手:选择合适的合金成分,尤其是对有害元素的控制;选择合适的Si/C比;对炉前对化学成分的稳定进行控制;运用合适的孕育处理方式。
哈尔滨东安汽车动力股份有限公司 哈尔滨东安汽车发动机制造有限公司
龚淑娟
李峥
评论 0
正在获取数据......