曲轴作为发动机的主要动力输出部件,其加工质量对发动机性能有直接的影响。在粗加工过程中,主轴颈粗加工振纹是经常要面对的问题。本文对实际生产过程中出现振纹的问题原因、解决办法进行了详细阐述。
业内曲轴粗加工工位普遍采用车—车拉机床加工主轴颈, 去除主轴颈部位的大部分粗加工余量,其中切槽刀是去除余量的主要刀具。该刀具从毛坯表面开始加工,进给量及切削深度大,切削刚性差,加工状况恶劣,易产生振纹和崩刀等问题,从而导致工件报废和机床停机换刀,是曲轴加工线经常要面对的一个棘手的问题。此类型切槽刀具广泛用于曲轴主轴颈的粗加工,所以我们对此刀具加工中出现的问题进行深入研究,找到问题产生的原因和解决方法,对于提高设备开动率、降低刀具成本并减少工件报废率等具有极其现实的意义。
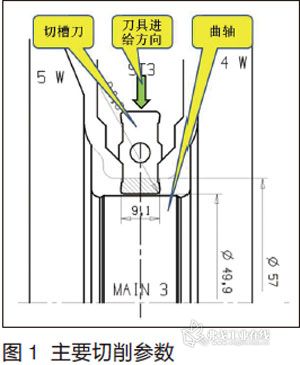
问题背景
我公司发动机工厂一期曲轴线主要生产1.0L和1.2L的四缸铸铁曲轴,设计产能为35万件/年,于2007年9月正式投产。该生产线的OP20工位为德国进口的车—车拉机床,采用切槽刀对主轴颈进行粗加工,刀具宽度为9.1mm,切削深度达到3.5mm左右(见图1)。该刀具加工时噪声及振动大,刀具容易崩刀(见图2),且粗加工完的轴颈表面时常出现振纹,严重时会导致工件报废(见图3)。在投产两年后,该问题发生得越来越频繁,有时换刀后的新刀具加工的工件连续出现严重的振纹,不得不停机查找原因。
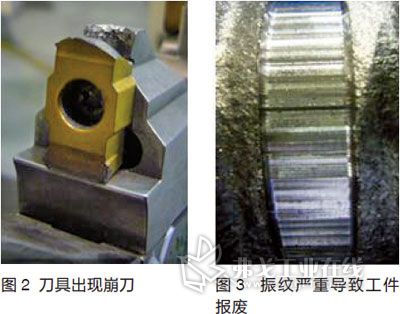
原因分析
由于切削时产生的切削力很大,再加上刀具进给方向与曲轴中心线垂直,导致曲轴切削时受力弯曲变形。在曲轴弯曲且高速旋转的状态下,当刀具切入轴颈时,切削刚性很差,容易使轴颈表面产生振纹,所以我们最初怀疑是机床夹持系统的刚性出了问题。为此,我们首先检查了机床顶尖跳动,检查结果显现检棒全长范围内的跳动值在6~8mm内,是完全合格的。接下来,我们又对机床的中心架进行了检查,发现并无异常,中心架的滚轮也是好的,并没有磨损或者转不动的情况发生。最后,为了提高夹持刚性,我们将中心架的夹紧压力提高了1MPa, 并加工几件工件进行验证,发现轴颈表面还是有振纹,提高夹紧压力的措施基本上无效。
排除机床的原因后,我们将分析重点放在了刀具上。首先对刀片和刀夹批次进行检查,没有发现问题,因为年初以来该批次刀具一直在使用,也没有更换过刀具供应商。然后,为了提高切削的刚性,我们试图通过降低切削参数来减小切削力对工件变型的影响。对此,我们试验了几组切削参数进行效果对比(见表和图4)。
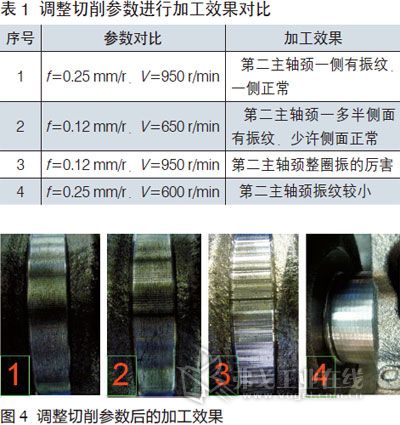
从刀具切削参数试验结果可以看出,改变加工参数效果不明显,不能根本解决问题,说明还有其他因素在影响着刀具的切削状态。对此,我们继续收集加工信息,发现了一个比较异常的现象,就是同批次的刀具有的加工几十件工件后振纹消失了,刀具也可以达到设定寿命,而且加工时噪声和振动情况有显著的降低,切削过程也很稳定。为此,我们各拿一片新刀片和达到寿命的旧刀片去分析刀尖磨损情况,在T8000投影仪下放大40倍的刀尖轮廓如图5所示。
从图5分析来看,新刀片的后角是约为7°的正后角,但是旧刀片后角已经被明显磨损,存在一个负倒棱,相当于实际切削时后角是负值,也就是说,在刀具切入工件时,新旧刀片与工件的接触情况差异很大,旧刀片的负后刀面顶住主轴颈表面后再切削,相当于切削时刀片上有个1mm左右的小平面始终与工件接触,提高了接触刚性,切削更平稳。反观新刀片的切削状况,由于正后角的存在,切削时新刀片只有切削刃与工件接触,相当于线接触,接触刚度较低,所以新刀片更加容易出现崩刀、振纹等问题就不足为奇了。
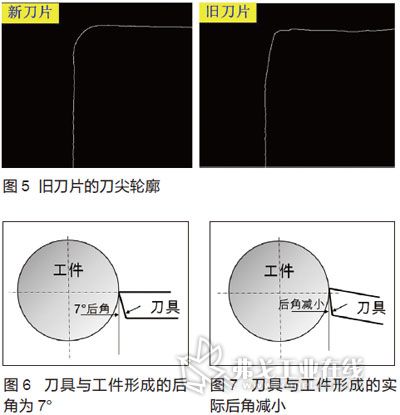
解决措施
经过对新旧刀片刀尖轮廓的分析,我们发现刀具后角对轴颈加工振纹问题有着重大影响。但是,切槽刀片是刀具供应商的标准刀片,如果要更改刀片的刀尖几何形状的话,需要开新的模具或将刀尖磨制后再涂层,费用巨大,且进口刀具交货期很长,所以更改刀片几何形状来解决现场问题的方案很快被否定了。
通过分析,虽然新刀片的刀具后角在制造时已经确定,不能改变,但是刀具切入工件时切削刃与工件加工表面的实际后角是可以通过改变车—车拉刀盘的旋转角度来实现的。如图6所示,标准的新刀片加工时,刀具与工件形成的后角为7°左右。当更改车—车拉刀盘的旋转角度后,使得刀具中心高于工件中心,刀具与工件形成的实际后角减小(见图7),提高了切削刚性。
按照这个思路,我们调整了车—车拉刀盘的旋转角度。原刀盘角度为224°,经过反复调整角度试验,我们发现,当角度增加0.23°后,加工状况比较理想,因此,我们最终将角度锁定在224.23°后验证了3把刀具,加工表面的振纹没有出现,而且加工噪声和振动显著减小,使得问题彻底得到解决。
结语
通过在一期项目对该问题的研究分析,我们获得了宝贵的经验教训。在后续的二期、四期项目加工1.5L发动机曲轴时,我们碰到了类似的问题也迎刃而解。尤其是四期项目中,虽然更换了机床供应商,但是该问题仍然存在,说明这是加工的共性问题,很值得研究。在四期项目中由于使用了比以前项目中小一型号的机床,主轴卡盘的尺寸也小了一号,开始大家都认为是机床的刚性不足,是设计缺陷所致。经过分析、研究和验证,并与刀具供应商一起协同工作,通过更改车—车刀盘的角度(0.4°),最终解决了这一问题。
该振纹问题的解决方案减少了崩刀几率,降低了工件报废率,保障了生产运行的顺利进行。由于该问题在几个项目中都曾出现过,极具代表性,尤其是对于加工刚性较差的铸铁曲轴时,问题发生概率极大。本文的分析研究结果可作为同行遇到类似问题时借鉴交流之用。
评论 0
正在获取数据......