气缸盖是内燃机零件中结构较为复杂的箱体零件,也是关键件,其精度要求高,加工工艺复杂,且加工质量直接影响发动机整体性能。内燃机气缸盖的制造,虽然制造系统各不同,但加工工艺及工艺设计中所采用的工艺技术仍有许多共同之处。
进、排气导管和座圈底孔的加工是气缸盖加工中的关键工序之一,通常采用钻—半精铰气门导管底孔、半精镗气门座圈底孔—精铰气门导管底孔、精镗气门座圈底孔工艺。其中,导管底孔圆度不合格涉及工艺系统的许多方面。本文通过对某缸盖排气导管底孔圆度不合格问题进行的系统分析,阐述了如何对所涉及的影响因素进行逐一验证及排除。
排气导管底孔圆度超差
某缸盖OP50工序主要加工进排气导管、座圈底孔、挺杆孔和上结合面等内容,该OP50工序是整线的关键工序,也是瓶颈工序。在恢复生产时出现OP50.1机床加工排气导管底孔圆度不合格(圆度产品要求0.008),而进气侧导管底孔均合格。
该缸盖进、排气导管底孔各8个,其特性编号分别为:排气侧12H1/3/5/7/9/11/13/15,进气侧11H1/2/5/7/9/11/13/15,正常生产时只使用三坐标测量两个导管底孔的相关尺寸。表1所示为失效件进、排气侧导管底孔圆度实测值的对比。从表1可以看出,排气侧导管底孔圆度不合格为12H15,为了确认其他孔是否合格,我们将排气侧8个导管底孔均进行了检测,从表2的检测结果可知,8个导管孔中仅有1个孔的检测结果合格。
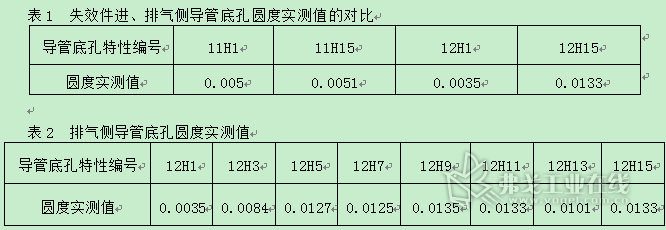
采用常规思路对问题进行排查
通常,孔的圆度不合格涉及工艺系统的许多方面,针对此问题我们展开了一系列排查及验证工作。
1.机床方面
(1)主轴静态精度 对该机床主轴静态检查,其结果均合格,如表3所示。
(2)主轴动态精度 现场检测OP50.1与OP50.2(加工合格)两台机床的主轴动态精度进行对比分析,结果如表4、表5所示。
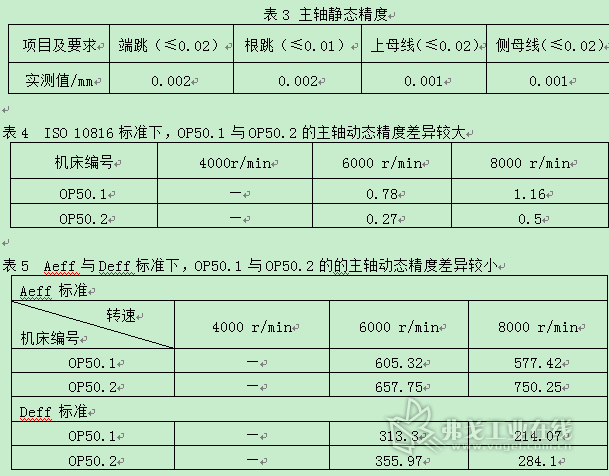
根据上述对比结果,将OP50.1精加工排气导管底孔刀具T6504转速从8000r/min调整到4000 r/min,同时降低进给,加工验证送三坐标进行检测,排气导管底孔的圆度仍然不合格。
(3)机床X、Y、Z和B轴抖动 将机床X、Y、Z和B轴移动,手摸感觉其抖动情况,未发现明显异常抖动问题。
(4)机床几何精度 对机床几何精度进行检测,其结果均合格。
(5)机床液压系统不稳定 咨询机床厂家分析可能是机床液压系统不稳定,即工件在加工过程中夹紧压力存在波动导致加工导管底孔圆度不合格。对调OP50.1与OP50.2这两台机床的液压站进行加工验证,OP50.1仍然加工不合格,OP50.2加工合格,排除了机床液压系统的问题。
2.夹具方面
OP50利用液压夹具实现工件定位装夹,其定位夹紧方式为排气侧“一面两销”及进气侧夹紧。很多情况下,我们在解决加工孔圆度超差问题时,大部分问题均与工件夹紧变形相关。针对排气导管底孔不合格,我们对夹具方面进行相关排查。
(1)夹紧压力该工序液压夹具夹紧方面主要有主夹紧和辅助支撑,对OP50.1和OP50.2主夹紧压力和辅助支撑压力检测并进行对比,两者基本一致。为了验证辅助支撑力对加工是否存在影响,调整OP50.1夹具辅助支撑力至10MPa、6MPa和4MPa进行加工验证,排气导管底孔圆度加工仍然不合格。
(2)夹紧点位置 经检查OP50.1夹具夹紧时,工件夹紧点存在异常,对调OP50.2夹具压板,确认夹紧点正常并加工验证排气导管底孔圆度仍然不合格。
在上述检查验证过程中发现夹具在工作台交换回转位置夹具管路有漏油现象,于是将其漏油进行修复,同时调整夹具压板保证夹紧点正常,并检测其关键部位的夹紧变形量,结果均满足要求(精加工工序夹紧变形量≤0.02mm),但再次加工排气导管底孔圆度仍然不合格。
3.测量方面
测导管底孔圆度时,改变步距,分别取0.1、0.01和0.001时,圆度分别为0.013、0.0152和0.0152,检测结果显示无明显差异,步距选取对圆度测量值无明显影响。
4.刀具方面
(1)刀具内、外冷压力 现场查看OP50.1排气导管底孔精加工刀具的内冷情况(见图1),该刀具内冷无异常。检测发现机床外冷断续喷出,调整正常后加工验证:排气导管底孔圆度仍然不合格
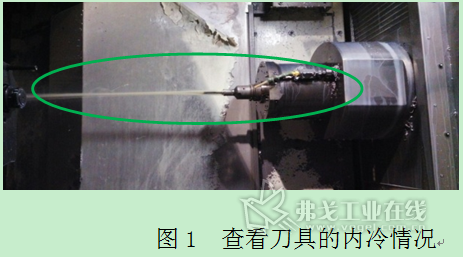
(2)刀具跳动 检测OP50.1精加工导管底孔刀具的跳动为0.005mm(要求≤0.005mm),将刀具跳动调整为0.002mm后加工送检,排气导管底孔圆度仍然不合格。
5.切削液方面
现场对OP50.1切削液检查发现,其机床内切削液表面有较多油污,同时对OP50.2机床切削液进行检查,具体如图2所示
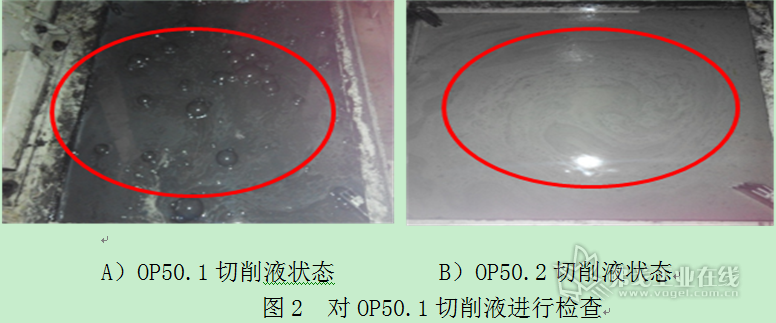
对OP50.1机床切削液更换后加工验证,排气导管底孔圆度仍然不合格。
6.加工工艺方面
OP50工序加工排气导管底孔相关工艺流程如表6所示。
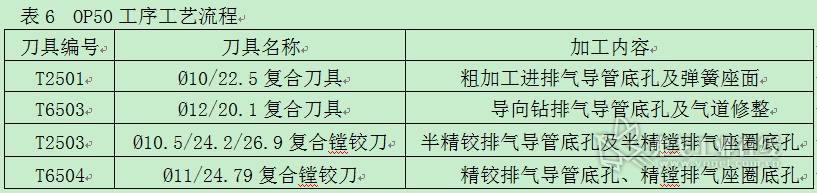
对此工艺流程进行分析,排气导管底孔粗加工T2501从缸盖上结合面的方向进行加工,半精加工T2503和精加工T6504均从下结合面的方向进行加工,两者可能存在加工错位问题,导致排气导管底孔加工不到的问题,从而反映导管底孔圆度不合格。根据三坐标测量结果分析,两把刀具加工的位置基本一致,无明显错位现象。
在上述一系列排查验证工作无任何明显改进效果的情况下,对OP50.1排气导管底孔半精加工刀具T2503和精加工刀具T6504与OP50.2机床的同样两把刀具进行对调加工验证,OP50.1加工排气导管底孔圆度仍然不合格,OP50.2加工排气导管底孔圆度合格,此次验证又排除了刀具T2503和刀具T6504的影响。
转换思路进行分析
此问题长时间未得到解决,问题产生原因无法进行锁定。为了尽快找到问题的症结,工艺工程师需打破思维定势,从失效件的测量报告及外观方面试图找到差异点。表7所示为OP50.1与OP50.2加工排气导管底孔Ø12mm导向孔状态。
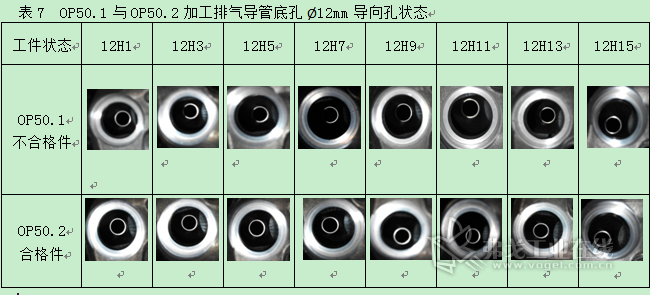
从合格件与不合格件的对比分析可以看出,OP50.1加工不合格的排气导管底孔孔口Ø12mm导向孔的孔口不完整,而OP50.2加工合格的排气导管底孔Ø12mm导向孔的孔口完整。
从加工工艺分析,导向钻排气导管底孔及气道修整的刀具T6503存在异常则会导致Ø12mm导向孔的加工不到位,对OP50.1机床T6503的刀补进行核对,其前后对比及加工验证结果如表8、表9所示。
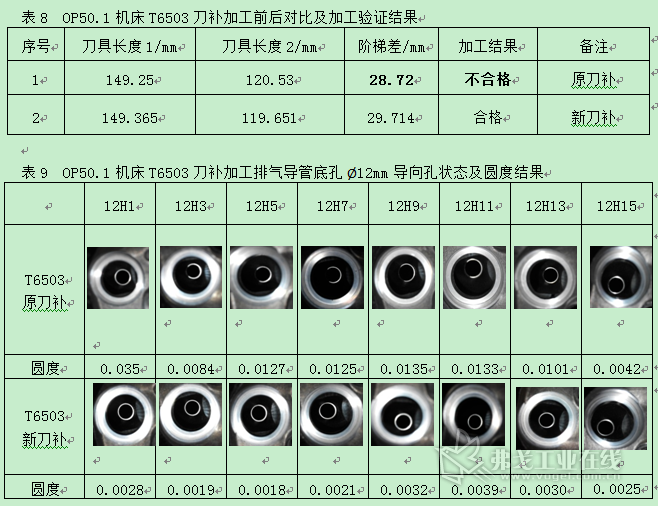
OP50.1机床T6503刀补核对后加工排气导管底孔导向孔状态及导管底孔圆度均满足要求,连续跟踪几个班次排气导管圆度均合格,问题得以解决。
结合再次核对刀具T6503及T6504的刀具布置图,我们发现当刀具T6503加工不到位时,外观表现为Ø12mm导向孔的孔口不完整及气道修整不到位,使得排气导管底孔精加工刀具T6504与气道干涉,从而导致T6504加工过程让刀,进一步导致排气导管底孔圆度不合格。
结语
通常情况下,孔的圆度不合格涉及工艺系统的许多方面,往往按照常规的问题处理思路及经验,我们会重点关注于机床、夹具等相关因素,过程中逐一检查及调整验证等并未得到预期想要的结果,问题得不到快速解决,直接影响到工艺工程师处理问题的信心。
此次排气导管底孔圆度不合格问题给予工艺工程师新的启发,对现场问题需要重视细节,尤其是对失效件与合格件的对比分析。另外在刀具验证的过程中,不能忽略任何一把与加工孔相关的刀具。我们需要对其加工工艺流程充分了解,快速排除刀具对加工的影响。

评论 0
正在获取数据......