企业在产品过程开发进入到生产准备阶段后期时,机加设备(生产线或单机)逐步进展到预验收、终验收及试生产等过程,这时需要结合过程能力研究理论,对各阶段设备尤其是关键设备的质量保证能力进行研究分析。通过过程有关能力的研究,掌握过程有关能力状况,实施过程控制和改进。
从设备预验收到最后形成正式的生产能力,通常要经历4个主要阶段。在各个阶段,针对对象的不同,进行不同能力的研究和分析,如表1所示。
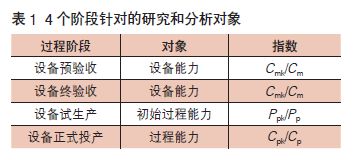
设备能力(Cmk/Cm)研究
1. 设备能力研究条件
在研究设备能力的加工过程中,应满足下列条件:
(1) 保持操作者不变。
(2) 保持设备、夹具、刀具及其他工装不变。
(3) 连续加工过程不允许中断。
(4) 采用的试件毛坯,应尽可能是同一批次和同一炉号的毛坯。
(5) 整个环境温度应尽可能保持恒定,安装地面不受干扰,并能隔离外界的影响。如果评定发现问题明显是由于厂房温度及冷却液温度所导致,则需采取措施。
(6) 所有用于研究的零件,测量前必须经过仔细清洗,以保证清洁,并在测量间经过恒温。
(7) 研究用测量仪器应具有国家计量部门或授权单位发放的合格证书,经过测量系统分析并合格,尽可能在整个验收过程中保持测量仪器不变更。
2.设备能力研究步骤
设备能力研究流程如图1所示,具体步骤如下:
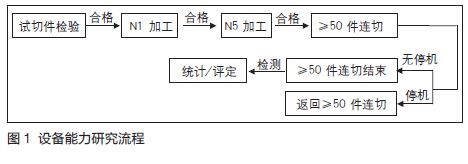
(1) 试切件经过检验,确认合格后进行连续加工,研究验证设备能力。
(2) 加工并测量第1个零件(N1),将测量值与规定极限作对比。一般情况下,如测量值处于规定公差50%幅度以内,设备不必再调整。第1个零件的测量值允许不用于评定。
(3) 加工并测量5个零件(N5)。一般情况下,5个测量值的平均值处于规定公差的1/4幅度以内,而且所有的单个测量值均在规定公差的1/2幅度以内,设备就不需要再重新调整,所有的测量值均可用于评定。但若设备必须进行重新调整,该5个零件的测量值不允许用于评定。
(4) 对于单向的公差(如径向跳动),一般情况下应达到规定公差范围的下半部分,否则就需要重新调整设备。
(5) 上述5个零件验证通过后,连续加工至少50个零件。如果发生停机,必须根据停机的原因决定是否从头开始或从停机时刻起继续开动。每次停机或每次过程改变必须进行记录。
(6) 对于非关键特殊特性,可以不统计评定和验收设备能力,但至少做5次抽样,如表2所示,每次抽样一般由3个零件组成。
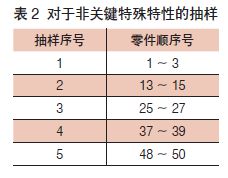
3.设备能力评定
(1) 加工内容相同但有多个夹紧工位的设备,对每个夹紧工位都必须分别评定。对于多台设备平行加工的工序,应该对每台设备分别评定,具体实施时可根据实际情况确定研究的夹紧工位和设备的数量。
(2) 对于多主轴设备,根据情况,如果需要必须分析和评定各个刀具、主轴,并分别进行记录。
(3) 在一台设备上分工步进行加工(粗加工和精加工),一般只针对精加工分析评定。但若在评定精加工时,能力不能满足要求,为了查明误差来源,可对粗加工进行能力评定。
(4) 对于不可调整刀具,可只进行Cm评定。
初始过程能力(Ppk/Pp)研究
1.初始过程能力研究条件
(1) 设备调试、验收完成,过程达到正式生产条件(包括人、机、料、法、环和测各方面),在生产初期进行。通常是安排在两日三班生产中进行数据采集。
(2) 生产线操作者配备完成,工艺文件已正式发放。输入状态符合要求的零件数量准备充分,满足两日三班生产的需求。
(3) 做好用于检测采集数据的测量仪器准备,需提前完成MSA分析,并且MSA结果要符合接受标准。
2.初始过程能力研究步骤
(1) 确定研究的特性范围,初始过程能力研究的特性范围,应至少包含所有的关键和重要的特殊特性。
(2) 确定使用的量检具,要有具体的型号及名称。
(3) 确定抽样频次和样本容量,用于统计计算的数据不少于50组。
(4) 编制初始过程能力研究计划,详细描述工序号、工序名称、特性名称、所用量检具、抽样频次和样本容量、责任人和完成时间。
(5) 进行至少两日三班的小批生产,根据研究计划,进行工件质量检测,采集数据。
(6) 工件检测顺序应按加工先后顺序进行检测,检测结果要做好记录和标识,应能进行追溯。
2. 初始过程能力评定
(1) 初始过程能力评定允许过程因素发生变化,一般按工序输出进行评定,而不固定夹具、刀具和主轴等。
(2) 对于多台设备平行加工的工序,应该对每台设备分别进行评定。实施有难度时,可根据实际情况确定研究的夹紧工位和设备的数量。
(3) 在一台设备上分工步加工(粗加工和精加工),一般只针对精加工分析评定。但若在评定精加工时,能力不能满足要求,为查明误差来源,可对粗加工进行能力评定。
(4) 对于不可调整刀具,可只进行Cm评定。
过程能力(Cpk/Cp)研究
过程能力的研究内容包括:过程能力研究条件、过程能力研究步骤以及过程能力评定。
过程能力研究条件包括过程正式投产;过程稳定、受控;子组内数据连续取值。
过程能力研究步骤如下: 确定要研究的特性; 确定统计过程控制方法,一般采用均值和极差图;建立分析用控制图,进行过程稳定性研究,采取措施消除特殊原因变差;过程达到稳定受控后,定期进行过程能力评定。
过程能力评定要求每次评定使用数据至少为25组、125个样本,具体内容同“初始过程能力评定”。
有关能力接受标准
能力指数数值越大,能力越高。在生产实际中,过高的能力将造成浪费,提高制造成本。因而,对不同阶段的能力指数,应在满足产品质量要求的前提下,来确定相关的能力指数要求。
对标准过程,能力指数一般要求控制在1.67~1.33;非关键特殊特性可根据实际情况适当降低,但不能低于1。
对不适用能力指数评价的项目,可以通过压缩公差进行控制,如形状公差、表面粗糙度等。
有关能力研究的实践
案例一 工件特性:4-39孔直径φ10Z8(-0.042/-0.064);能力现状:Cmk=1.29,Cm=1.58。
原因分析:对单值图(见图2)和直方图(见图3)进行分析,孔径有明显的下降趋势,这表明刀具磨损相对较快。另外,直径分布中心位置也略有偏移。
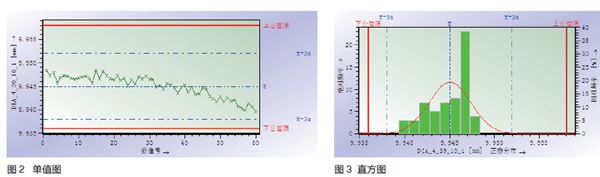
改进措施:选择并验证寿命更长的刀具,同时尽可能将刀具直径设定在要求公差中间位置。
案例二 工件特性:4-11孔位置度φ0.32;能力现状:Cmk=1.32,Cm=1.69。
原因分析:从位置度分解的Y、Z坐标值看,Y坐标单值图(见图4)和直方图(见图5)可以看出,Y坐标加工没有问题,能力也足够,而Z坐标的尺寸(见图6、图7)分布中心有偏移。
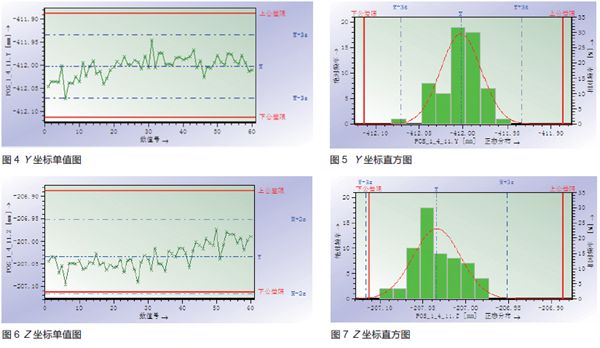
改进措施:调整模板和主轴位置精度,改进Z方向坐标。
结语
综上所述,能力研究一定要注意数据采集的条件,否则研究结果会降低指导意义,甚至可能误导;针对不同特性,能力研究要区别对待,不能一概而论,要从实际出发;设备验收时,为了节省时间和成本,对于同时承担多个品种加工的设备,设备能力验收可以只选择其中的1个作为主产品,也可以根据情况将多个产品在预验收和终验收时分开,交换进行设备能力验收;设备验收时,对于并行设备工序,可将并行设备分开在预验收和终验收时各做一部分的能力研究,两部分合计涵盖所有设备,以节省时间和成本。
评论 0
正在获取数据......