发动机厂装配线翻转机翻转缸体时容易造成定位不良及分度器过度损耗,经统计2015年,我公司全年翻转机停机维修了38次,单机维修时间953 min,导致总线停线813 min。故障的具体表现为:A151装配线翻转机故障多发,掉落发动机直接造成缸体或整机报废,引起停线维修;分度器异常损坏,A151线已更换2台分度器。
缸体翻转的动作流程是:托盘举升机构升起到位后,翻转机翻转电动机反转,抓取机构翻转复位到零位;升降机构下降,夹紧气缸动作,抓取机构定位销进入发动机(或翻转辅具)工艺孔;夹紧到位后,升降机构升起,翻转电动机正转,发动机翻转;到位后升降电动机动作,升降机构带动发动机下降,发动机工艺孔进入托盘定位销,夹紧气缸动作;夹紧机构松开发动机。
经调查发现,以下的翻转动作流程存在如下问题:翻转复位到零位不准确,抓取定位销进入不了发动机(或翻转辅具)工艺孔,停机报故障;发动机翻转不到位,下降翻入托盘无法进入定位销,夹紧机构松开,发动机掉落到辊道或地面损坏。
为解决上述问题,我们设定了改进目标:保证翻转机翻转精度,避免发动机装配线报废率,降低生产成本;降低设备故障停机率,减少保全维修次数,提高生产效率。围绕这一目标,我们开展了一系列的工作。
要因解析
要因解析过程中,我们发现工作中存在如下问题:联轴器选型不合理,容易松动且收空间限制调节不方便;分度器旋转控制方式不合理,没有完全使用分度器的功能,不能准确封堵定位。
分度器输入轴和输出轴联动存在着如下关系:在输入轴360°范围内分两个区域,即联动区和空程区。联动区是在270°范围内驱动输出轴旋转,空程区是剩下90°输入轴旋转但输出轴锁止。正常的工作方式是,停止时输入轴完全越过区域的临界点,输出轴处于锁止位,这样分度器的锁定安全可靠,抗冲击负载大。
原检测方式只检测输出轴角向,原理上可以设定在任意点,如果停止在非锁定位,分度器抗冲击负载能力弱,冲击负载会对分度器造成很大的损伤。A151线已损坏2台分度器正是这个原因导致的。
对策方案
针对以上分析,我们制定了解决方案,具体如下:
1. 重新选型联轴器
翻转机工作过程中由于发动机整体惯性较大,对连轴节的冲击也大,原连轴节(见图1)经常出现松动,调节时需要轴向空间不能下工具,只能拆掉减速器和分度器整体,维护时间长。采用新联轴器(见图2)后,在径向拧紧的维护中,不再需要拆除其他零部件,方便操作,维护时间很短。
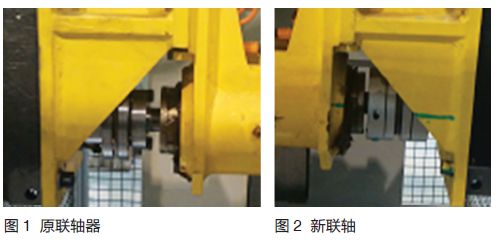
2. 设计新的控制方式
我们增加了对分度器输入轴角向检测机构(见图3、图4),同时检测分度器输入轴和输出轴,保障分度器停止在修改控制程序。
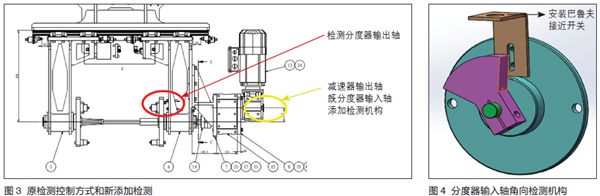
3. 添加对应输入轴检测机构的响应程序。
由于分度器输入轴直接插入到减速器输出孔,加速器输出轴是中空轴,连接分度器对侧面有连接凸缘面和轴孔,此处可以直接安装添加的检测机构(见图5)。
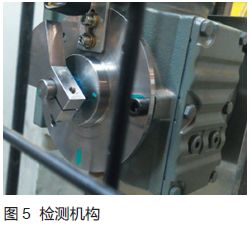
改善效果
新的检测机构安装在A151线的四台翻转机上,修改了响应的控制程序,实际使用完全正常,无故障出现。通过本次改善有效降低了A151装配线的故障率,提高了生产产量,节省了维护成本。
结语
综上所述,该项目中存在的问题是,联轴器选型维护不方便,增加维护难度,属于设计不合理;分度器控制方式不完全符合分度器基本原理,在使用过程中频繁出现故障。在改善过程中,我们进行了如下总结:非标设备的结构设计和标准见的选型需要充分考虑使用维护方便性,降低维护难度,提高维护效率;关键部件的使用符合使用原理,防止异常损坏和出现工件损伤。
该项目的成功实施后,我们进行了总结和推广,在标准化及水平展开方面取得了显著成就。
评论 0
正在获取数据......