随着用户对车辆安全要求的不断提升,汽车的安全性正在快速地提高与完善,它也成为了用户在选择车型时的第一考量要素。除了主动安全的搭载,能让事故防患于未然之外,车企对于车辆本身的被动安全的开发也愈发重视了起来,车身作为保护乘客的最后一道防线,其相关技术也在不断进步。与此同时,减轻车身重量,以达到节能减排目的,也成为主流主机厂与供应商之间努力的方向。为适应这种发展趋势,各大相关企业开发出了应用于车身部件的高强度钢材,同时也产生了高强钢材在常温下成形困难的问题。由此,热成形技术应运而生。
诚然,热成形技术早期主要针对高强钢板而开发,其工艺过程为:首先将常温下强度为500~600MPa的硼合金钢板加热到850~950℃,使之均匀奥氏体化,然后送入内部带有冷却系统的模具内冲压成型,最后快速冷却,将奥氏体转变为马氏体,使冲压件得到硬化,大幅度提高强度至1200~2000Mpa,以达到设施安全性的目的。正是因为高强钢的使用让车身越来越坚固安全,同时相比其它材料,热成形钢有着更高的性价比,所以它的使用也在近几年不断提升,热成形技术也逐渐发展成为应用于车身的黑科技。
但是对于汽车车身的设计开发者而言,在保证安全性能的同时仍需不断实现车身轻量化,因此随着设计能力的提升及功能要求的进步,近些年适用于车身各个位置,满足各部功能需求的热成形新工艺、新材料、新设计也顺势而出。本文盘点了五大结合新工艺与新材料的时下主流冲压热成形技术。

一体式车身冲压,图片来源:特斯拉
短流程热轧热成形钢
从可持续发展的角度而言,汽车行业的低碳化已经不能仅仅依靠汽车服役过程的节能减排,同时需要从设计、制造、使用到回收利用的全生命周期各个过程均低碳化。有着低耗能优势的短流程轧制技术逐步走进了汽车产品工程师的视野。薄板坯连铸连轧流程与常规热轧流程相比能耗降低约50%以上。薄板坯连铸连轧快速凝固、直接轧制的工艺特点,特别适合开发薄规格热轧高强钢产品。
据了解国内主流钢厂已开发出CSP(compact strip production)短流程热成形钢,性能与现有热成形钢几乎无差别,应用部位也可与现有热成形钢一致。此类材料一大特点是降低了原材料生产过程中的能源消耗,是未来可持续发展的方向。凌云股份通过热成形技术已经取得了一汽奥迪Q5、一汽大众CC、X55热成型项目;已实现不等厚板热成型产品在大众车型的供货;获得比亚迪14种20件热成型产品定点。
变截面热成形技术
变截面热成形技术,是指用一张板料的截面厚度是有变化的板进行热冲压,热冲压成形工艺过程与传统热成形无差别。这种截面厚度变化的板材,可根据零件受力变化特点来设计板带材的厚度过渡,通过定制产品在保证性能的前提下实现结构减重。2006年,道奇 Calibre 和BMW X5成为首批在车身中采用定制轧制和冲压硬化部件的汽车。
分段强化热成形技术
欧洲知名车身供应商海斯坦普在该项技术上研究最深,并且该公司在近期已获得相关专利技术。在传统多工位冲压的基础上,海斯坦普把不同工步的模具合并到一个工位,它可以连续走完这个热成型的技术,也意味着在模具轧机的技术上是一次革命性的研发。因为材料强度的问题,要保证它在传统冷压的工艺和效率的基础上达到热冲压的技术,故海斯坦普把冷冲压的连续冲压和热冲压的技术结合到了一起。此外,在材料方面,现在的应用是多种材料的合成运用。比如有铝的应用,还有碳纤维的应用,既要满足传统的安全需求,又要满足轻量化的需求。在热冲压技术上,海斯坦普多年来一直在一体式门环的技术上不断革新。
值得一提的是,海斯坦普在国内早有布局,其与我国知名汽车零部件供应商海纳川在中国合资企业于2018年就已投入运营,新工厂投资超过5,000万欧元(3.9亿人民币),拥有员工250余人,致力于汽车白车身与底盘部件的冲压成形和组装。

激光拼焊热成形技术
2019年讴歌RDX车型上热冲压激光焊接内外前门环系统被第一次应用,将激光拼焊热成形技术深深印入了国内汽车材料工程师的脑海中。其实早在2014年,讴歌MDX车型就向世界展示了激光焊接外门环。
激光拼焊热成形技术,是指在热冲压工艺之前,用激光能源将不同材质、板厚、镀层的板材拼合并焊接而形成一块整体板材然后整体进行热冲压的技术。拼焊板技术的出现解决了超宽板及不同部位不同工艺性能要求的问题,对减轻车身重量、降低整车成本、节能环保等都有着重要的作用。目前对于激光拼焊热成形钢材的主流供应商主要有:安赛乐米塔尔、蒂森克虏伯钢铁、新日铁、宝钢股份。
高强度铝合金热成形技术
虽然鉴于车身强度要求、轻量化材料价格及加工技术水平等问题,钢材作为汽车车身主要材料的地位短时间内难以撼动,但是车身作为轻量化潜力巨大的领域,采用铝合金则能减重约 40%,仍有不少企业在高强度铝合金热成形领域不断打破边界。
高强铝合金热成型+淬火技术(HFQ专利)这一变革性铝合金热成型技术由英国Impression Technology公司研发,通过长春吉文引入国内,并在国内建立了一条大型量产生产线。该技术低成本、高效益、低投资、高性能的铝合金热冲压成型轻量化制造技术。其通过冲压件集成及使用高强铝合金减小部件厚度的方式来实现轻量化减重,鉴于设计制造的模具个数和零部件数目的减少,实现了总投资成本的降低。该技术可实现部件减重20%-40%,同时成型的冲压件没有回弹,冲压件及模具的设计均不要求考虑回弹补偿,大幅缩短开发周期,增强高水平产品尺寸精度的重复性和可控性,极大地提高了工程团队设计的灵活性。
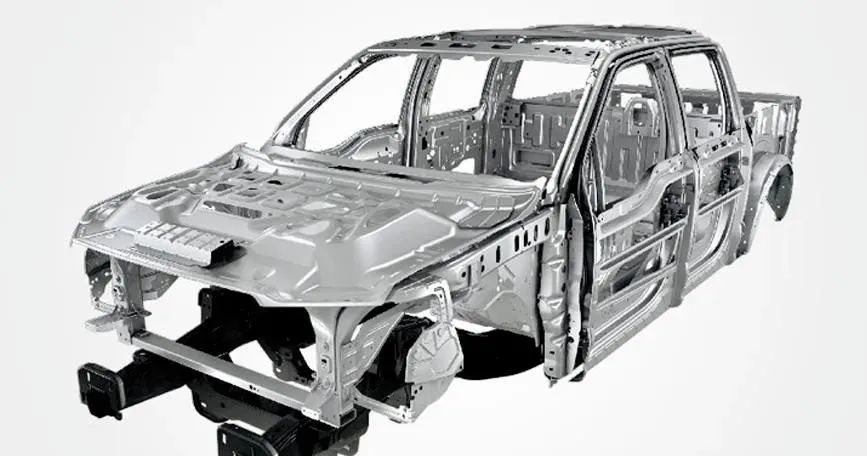
新工艺新材料创热成形新市场
中国汽车产量持续攀升,轻量化节能减排的要求以及日趋严格的汽车安全法规,为热冲压成形钢提供了广阔的市场机遇。相对于镁铝合金、碳纤维等轻量化材料,热成形钢相对较低的生命周期排放,使得其不仅在制造阶段减排较少,在汽车使用阶段也保持相对有竞争力的减排能力,有利于实现汽车全寿命周期的节能目标。智能化汽车的发展,虽然一定程度上减少交通安全事故等传统的主被动碰撞问题,然而新的网络信息安全隐患将在智能化汽车领域出现,因此一旦出现安全事故,乘客将可能受到更加致命的危害。
因此,被动结构安全仍将是汽车最基本的设计要求,依然需要使用高强汽车钢增加安全性能。国内外诸多企业都展示过其在热成型方面的创新解决方案,从设计到生产各个单位均有自己独特的应用思路。
【免责声明】本文摘自网络,版权归原作者所有,仅用于技术分享交流,非商业用途!若有涉侵权等告知,将及时删除,感谢关注!
评论
加载更多