近年来,随着互联网技术的飞速发展和物联网、5G、大数据和人工智能等新一代数字技术的不断涌现,汽车行业逐渐步入数字化转型时代。数字化转型不仅是汽车行业全面升级的必经之路,更是未来行业发展以及竞争的主要来源。
汽车行业数字化转型是汽车产业在信息化、网络化和智能化方面的融合发展,不仅可以提高汽车制造业的效率和产出质量,还可以优化汽车的销售和服务模式,提高客户体验和满意度,同时也有利于实现汽车产业的可持续发展。数字化智能化发展迅速,为我国制造业提供了新的发展契机。
研究背景
数字化技术是实现汽车行业中的生产制造环节数字化转型的基础,其在工业网络的赋能下,可以助力汽车制造商实现精细化生产。
汽车产业的数字化转型是一场革命性的改变,影响着汽车制造商、供应商、销售商及以终端用户等各个环节。通过数字化技术和数据驱动的方法,汽车产业实现了从传统制造业向智能制造业的转变,为行业带来了更高效、智能和可持续的发展。
为此,我公司重庆车身车间针对现有生产管理进行数字化转型,通过自主研发,主要包括生产管理系统、能源监控系统、车身用水管理系统以及侧围生产管理系统,取得了很好的效果,流程简化,工作效率高、结果输出好。
工业数字化在车身制造中的实践
结合车间生产线的结构,我们主要对生产管理系统、侧围自制件盘点系统、能源监控系统、车身用水管理系统以及侧围生产管理系统进行了技术改造。
1. 生产管理系统
改善前,车间现场存在以下缺点:
1)现场生产信息和计划完成情况必须使用计算机通过公司内网去手动查询PTS系统数据后计算分析,使用过程极为不便。
2)对于现场的生产效率缺乏数据信息,不利于生产计划安排和效率提升。
3)整车工厂的各个车间的滞留车数据获取需要手动查询。
基于上述主要问题,我们通过开发Python爬虫程序实时获取制造计划与跟踪系统(PTS)数据;将收集到的数据上传至简道云平台,通过数据报表形式向管理人员展示各个工段的生产效率以及当前生产进度,如图1所示。
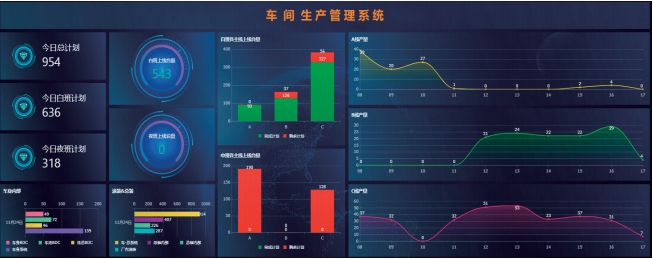
图1 生产报表界面
如图2所示为数字化无人工位开发结果,通过简道云-知识库,上传安全的安全操作规程、危险危害源等文件,上传岗位SOS、安全人等签批文件,通过生产二维码将工位文件无纸化;通过简道云流程,实现TPM、一分钟质量检查和凿检记录等流程化;数字化工位以工位平板为展示,实现信息互通,通过简道云和PLC实现工位信息的输入,工位通过流程上传TPM和质量现场的问题,实现问题的升级。
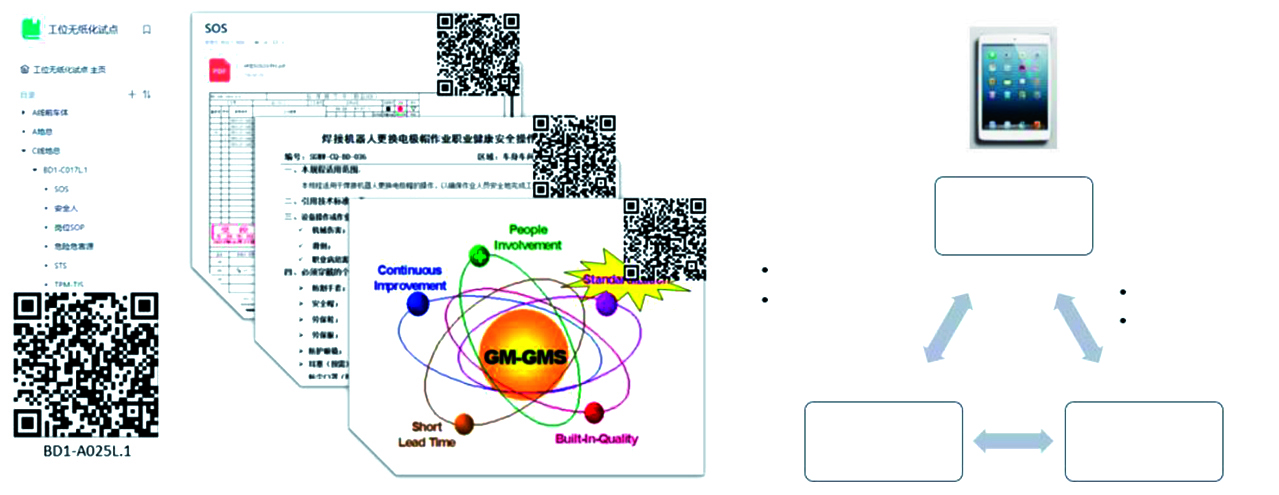
图2 工位无纸化
2. 侧围自制件盘点系统
在车身制造车间中,A线左右侧围生产根据A主线生产进行匹配生产,通过侧围总成缓冲数量来计划生产,但是侧围工段的节拍和生产台量没有进行统计和跟踪。
通过在PLC建立侧围生产统计标签,将网络读取标签数据存储至MySQL数据库;Python爬取数据库数据,处理后上传简道云;简道云通过存储每小时和每天侧围的产量信息,制作出可视化的生产报表,如图3所示,可通过企业微信App、微信简道云小程序或者网页进行查阅。
改进后:
1)A线侧围每天和每小时台量都可查阅。
2)侧围每小时台量可以和A地总每小时台量进行对比,可以实时进行生产策略的调整。
3)A线侧围每天、每月的生产下线台量可以用来核对冲压出库的冲压零件数量,便于控制冲压自制件的成本。
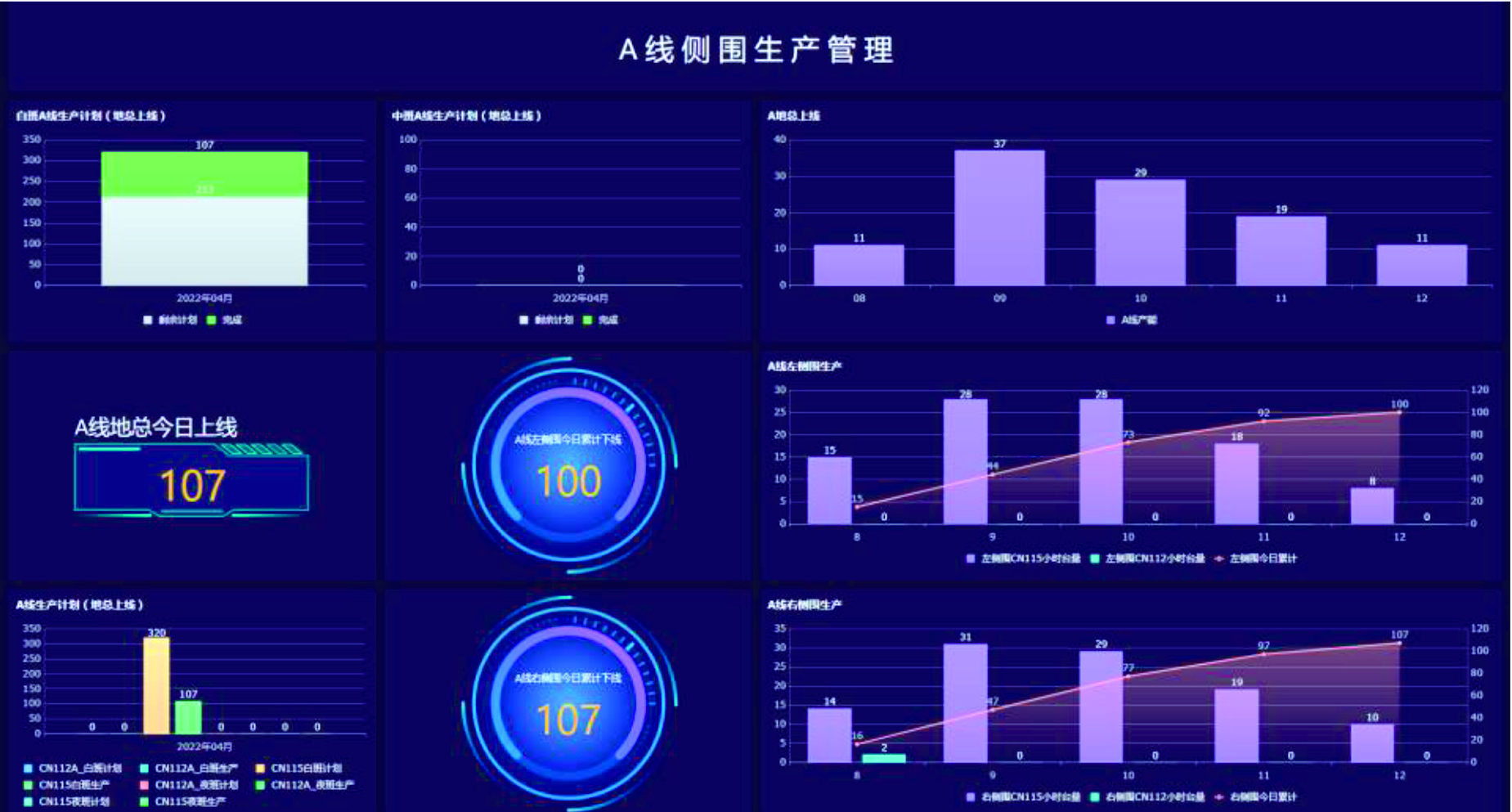
图3 侧围生产报表界面
3. 能源管理系统
在原始的能源监控机制中,对电耗、压缩空气和水消耗统计需要进行人工抄表,然而在抄表过程中,各个表之间的距离偏远,行走时间长,浪费工时,且人工读取表会出现读错的情况,导致数据出现误差;由于人工读表消耗过程时间较长,一周进行一次,导致人工读表实时性较差;另外,人工读表时需要登高和靠近高压区域,存在跌落和电击的风险。
基于上述问题,车间通过自主设计的Python程序,利用数显表的RS485通信功能结合物联网技术,将收集到的数据上传至简道云平台,通过数据报表形式向各个工段区域实时展示用水/电/气情况,如图4、图5所示。
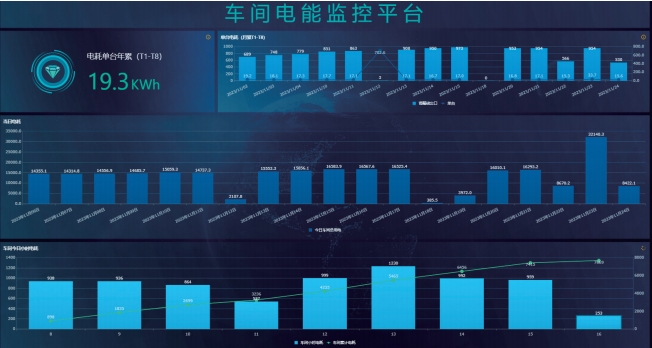
图4 电能监控平台
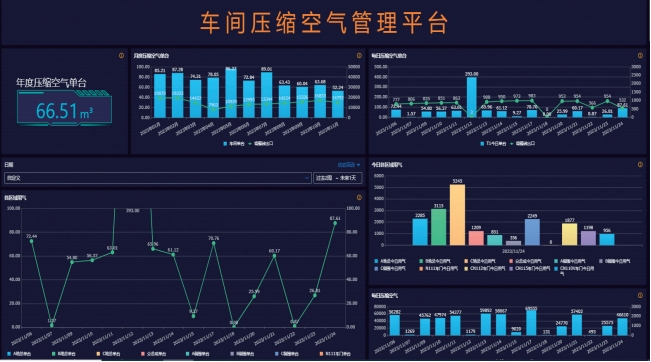
图5 能源管理系统界面
系统优点:
1)实时显示各区域能耗表当前读数。
2)实时显示各个区域当日水/电/气使用情况。
3)各区域对于本区域当前能源消耗情况能够及时发现漏水/气/电或者异常消耗并整改。
4)实现优化1名能源抄录人员,节约12万元/年。
4. 质量数字化智能管理系统
改善前,质量管控中存在以下缺点:
1)机器人焊点数量多,员工较难记忆,容易造成机器人焊点漏焊、人工漏检、缺陷逃逸等风险。
2)车身调整线动态线运行车型复杂且混线过线,面对多种车型区分,人工较难100%准确地将对应门盖与白车身进行匹配装配,容易造成错装等质量风险。
3)由于车辆底盘件后部下车体尺寸波动对后工序装配影响较大,无提前监测手段,往往后工序有问题只能被动往前查找车辆底盘件后部下车体尺寸变化,对车间效率和产品质量影响较大。
基于上述问题,我们开发出4类质量数字化系统提升质量输出,分别是:低成本在线凿检目视系统、补焊线低成本智能焊点视觉系统、调整线车型配置扫码识别提示系统及尺寸在线检测系统。
低成本在线凿检目视系统中,目视化系统根据不同车型对凿检位置进行了合理选择,有效降低了作业过程中的人为因素,得到在单次循环中各车型焊点凿检全覆盖的最优解,将凿检信息与车型相结合,凿检位置选择更合理更全面,从而形成了对制造过程中产品质量的动态监测。凿检目视化系统如图6所示。
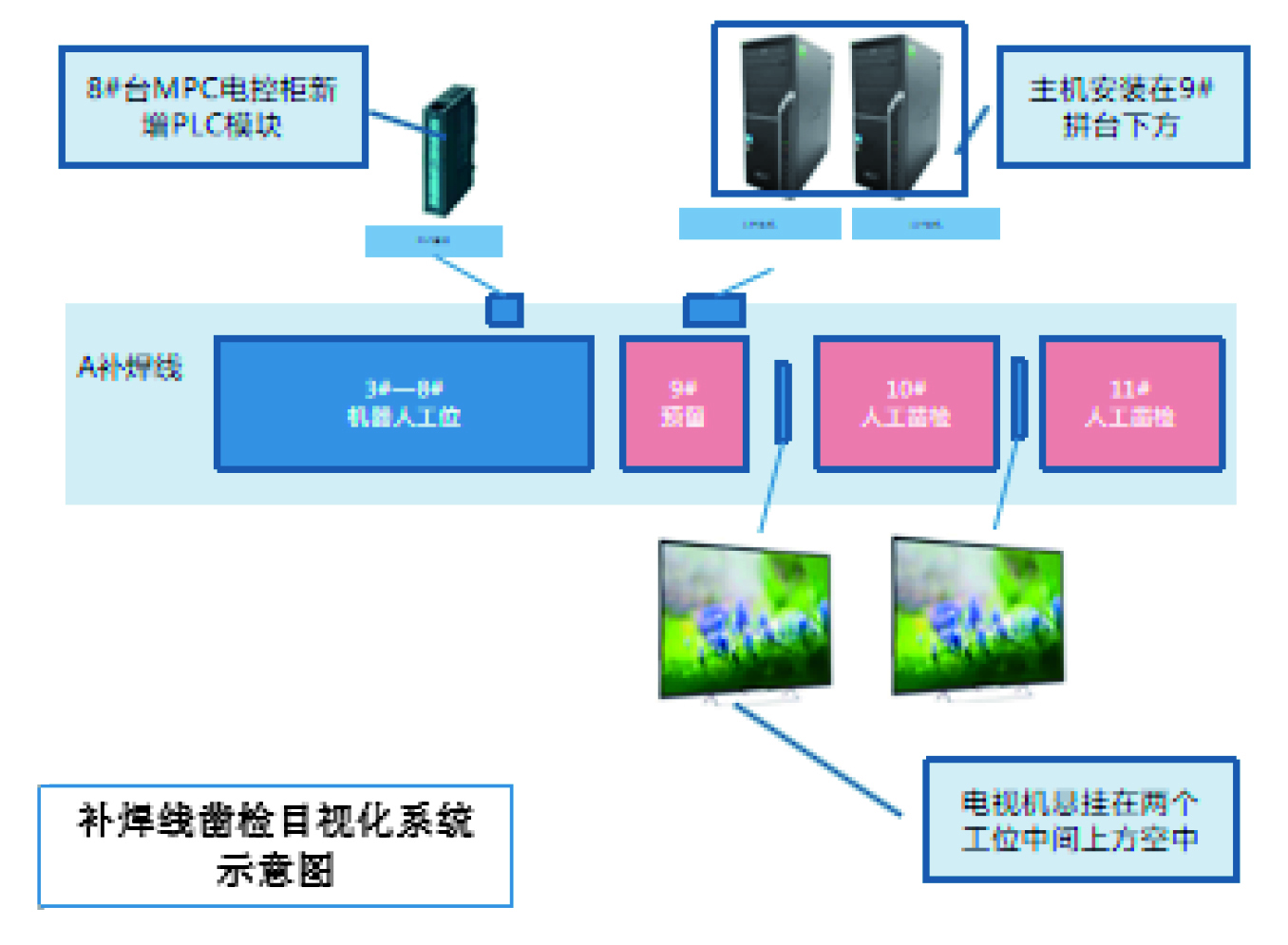
图6 凿检目视化系统示意图
补焊线低成本智能焊点视觉系统(图7)采用计算机视觉处理技术对白车身焊点进行识别,通过机器识别辅助人工检测,多车型全自动、高精度全覆盖,可靠性更强,有效降低人工劳动强度,顺应智能制造趋势,是计算机视觉在工业场景的一次成功应用。
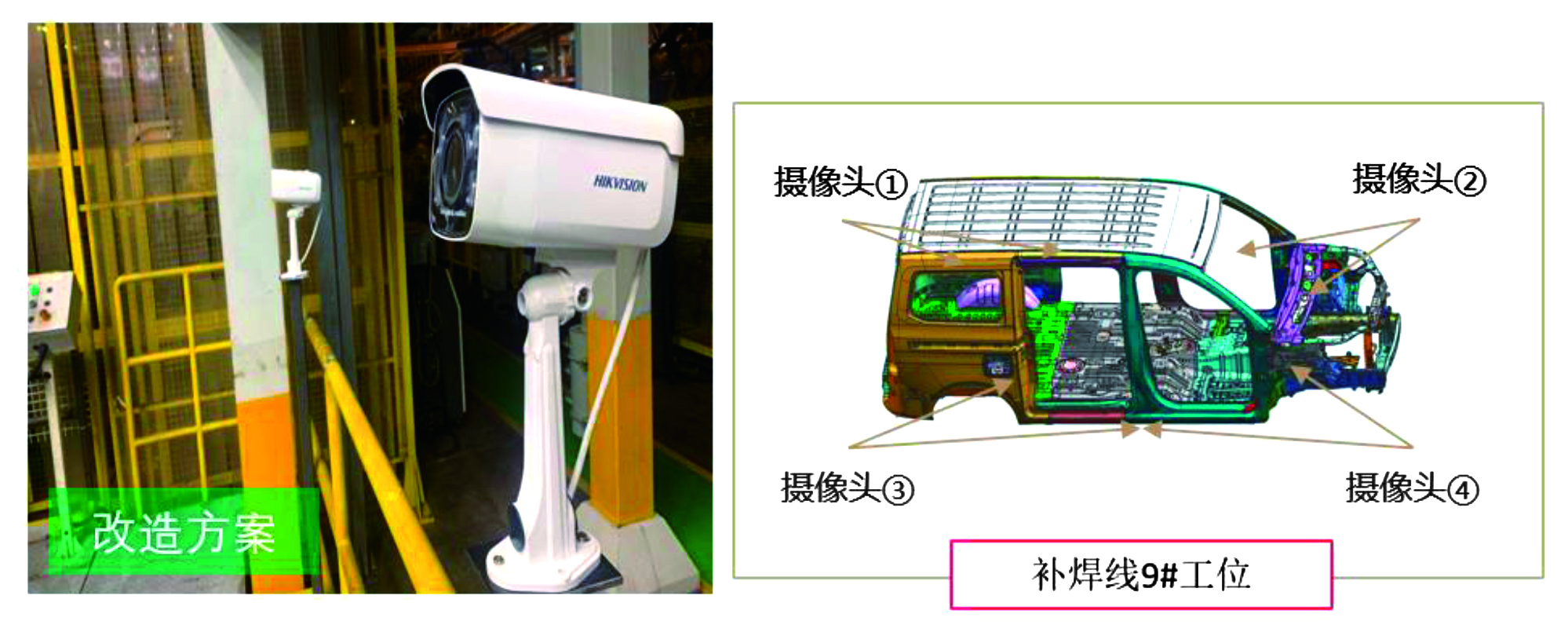
图7 补焊线低成本智能焊点视觉系统
调整线车型配置扫码识别提示系统(图8)通过智能扫码获取车型信息,替代传统实物车型提醒标识,消除制造过程中的冗余操作,实现车型信息数字化传递,将实物转化为数字信息,实现产品周期数字化。现场取消“随车挂牌取牌”。3个地总线每个打码工位优化工作要素10s,1个调整线优化工作要素6s,调整线门盖装错PPH降为0。
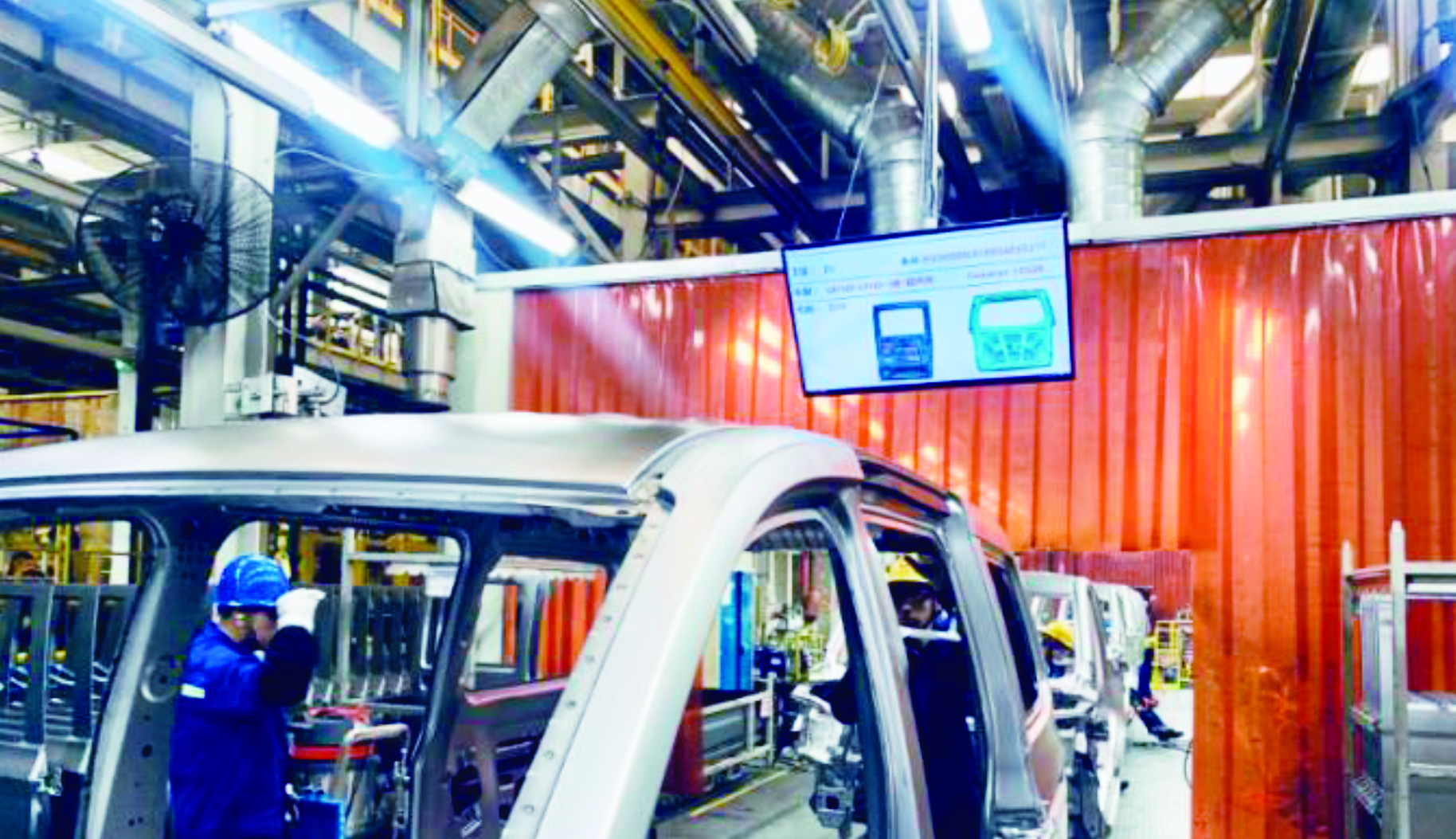
图8调整线车型配置扫码识别提示系统
以后部下车体轮罩区域钣金尺寸作为白车身尺寸波动的痛点为例,我们设计开发了一种白车身关键区域尺寸在线监测与分析的装置。可快速检测过线的每一台白车身后部下车体轮罩区域钣金尺寸偏差,并汇总统计。由程序判定该区域是否尺寸稳定,并对监测异常点快速报警。
该系统由位移传感器、数据处理器、扫码设备及工作站组成。工作站由数据采集软件与数据分析软件组成。位移传感器安装在工位上,过线的每台车均进行扫描,利用扫描数据进行长周期内的零件尺寸偏移分析,流程是:台车到位—位移传感器工作收集数据—数据处理器处理—数据采集软件读入数据—数据分析软件记录该点状态—台车输送下工位—进入下一循环。
其中,扫码器扫描白车身大梁条形码,反馈软件系统,识别当前车型。位移传感器布置在焊接拼台上,对应感应钣金件当前位置尺寸信息。可根据需要安装位移传感器数量及位置。针对后部下车体零件,本系统图示安装三处,监测后轮罩的前、中、后三个位置。数据处理器收集位移传感器信号,经过处理传输至软件单元。数据收集软件:根据扫码器扫描的大梁条形码,按车型分别记录传感器数据。
数据分析软件(图9)抓取数据收集软件数据。按照6σ统计学,整合分析各个传感器数据,输出SPC控制图。针对数据变异之处,自动向相关负责人进行推送及报警。
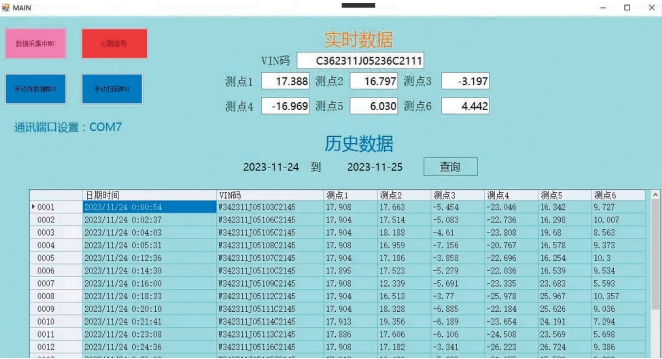
图9 数据分析软件
结语
在工业数字化时代下,汽车制造行业正从传统密集型产业朝着智能制造方向发展,利用智能制造技术可实现汽车生产制造的数字化、网络化与可视化,达到企业生产管理部门数据共享与协同,极大地提升了企业的生产效率。因此,汽车制造企业应不断加强对智能制造系统的应用与管理,并从自身实际出发,围绕数智化目标进行企业发展规划,提升汽车产品质量,推动制造企业可持续发展。
本文为“AI汽车制造业”首发,未经授权不得转载。版权所有,转载请联系小编授权(VOGEL100)。本文作者:郭晓伟 陈守团,单位:上汽通用五菱汽车股份有限公司。责任编辑龚淑娟,责任较对何发。本文转载请注明来源:AI汽车制造业
评论
加载更多