设计策略
实施智能设备联网,建立参照制造企业信息化的管理思路,整合公司以及外部管理专家建议,结合多年的管理信息化项目经验和信息化成果,包括服务器端与网络建设、服务器端软件开发、设备端的程序开发、设备与服务器端标准接口文件的设计,连接公司的MES和SAP来进行数据交换,MDAS端接口和报表系统的开发。
通过大量前期调研和试用国内外、各行业的机加工设备应用,依据变速器产品全生命周期技术和管理要求,选取了适用于汽车零部件制造行业,国内外知名软件商的行业标杆软件平台。在信息化方面,本设计实现了信息化、自动化、智能化与生产制造过程的紧密结合。
整体方案
设备自动化控制系统PLC定义的标准接口协议(OPC协议)及接口定义进行通信:实现MES与PLC之间包括工件到位、保存数据、保存完成及验证完成四个信号交互,其他信息通过PLC或者MES实时地写入定义好的DB地址,由PLC或者MES到标准的DB地址获取对应的信息,实现数据采集、设备监控、生产控制等相应的功能。系统设计如图1所示。
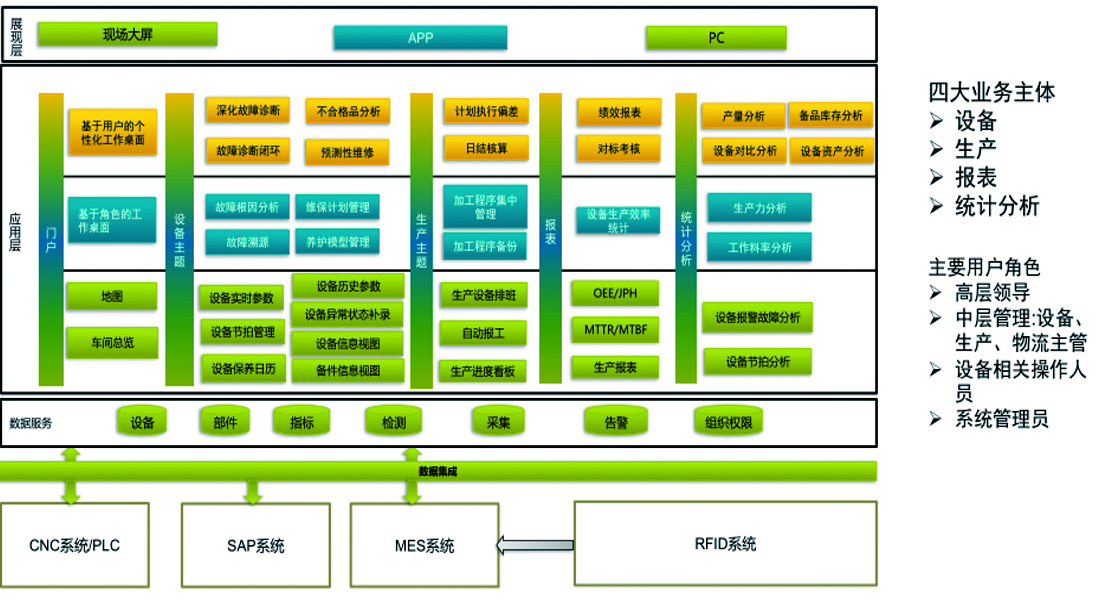
图1 设备系统设计
具体实施内容如下:
1)MDAS根据需求和相关规则,自动分解出自制件缺件数和日生产计划数(投料),由生产调度确认后,下达计划。
2)各车间生产领班定期维护排产相关参数。
3)MDAS根据需求数据、当前在制品和库存数据,考虑排产参数和规则,自动生成设备排产计划,经车间领班确认后,生成生产作业指令。
4)设备排产计划作为后续实际设备OEE计算的基准,并与生产实绩进行跟踪。
5)通过企业微信发送生产安排。
6)设备关键故障信息,通过企业微信进行推送。
网络部署
设备联机采用私有网络,设备通过私有网络连接到服务器机房总交换机,不影响现有生产设备网络,方便维护和管理。
生产局域网络系统所采用的元器件均为国内外知名品牌产品。硬件设备采用经过严格测试的、符合工业环境的硬件产品,抗干扰性和运行环境温度都满足工业现场标准。以太网线等传输介质符合工业现场要求,具有良好的抗干扰性、抗拉伸、抗挤压性。
数据仓库区是平台的核心,为关系型数据提供业务逻辑复杂的计算服务和存储,数据仓库是基于MPP体系架构的。在数据仓库区建立企业级的数据模型,以范式化加工后的数据模型供统计分析类应用使用,包括基础数据、业务数据和指标数据。
实时分析区是实时/准实时业务需求,提供结构化数据或非结构化数据的实时加工处理分析,支撑生产设备的在线实时监测、生产过程监控等应用。实时分析区的分析结果也可以作为数据仓库区的数据源。
设备实施功能
(1)实时监控
展示车间各设备采集的实时数据(图2),包括主轴电流、刀具速度等,可以实时展示该设备采集点明细,并显示该采集点最近10min的实时数据和最近1h的历史数据。在历史数据项,可以选择任意时间段,查询该时间段内的历史数据曲线。同时系统支持多采集点对比展示。同时,超出设备预警线,系统会自动报警,并通过企业微信推送相关人员。
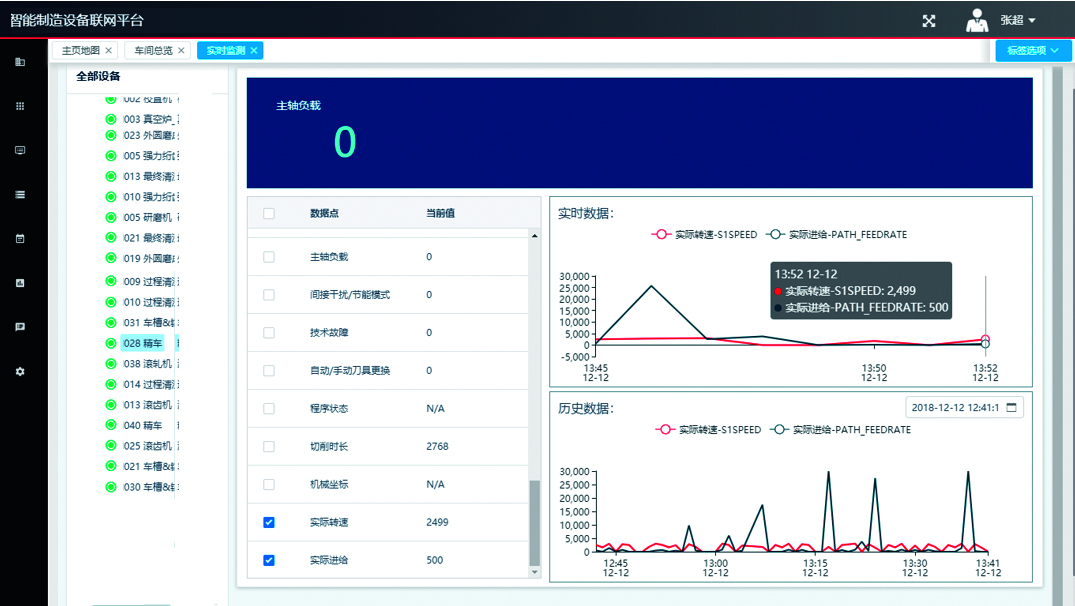
图2 实时监控图
(2)生产报工
汽车零部件制造型的生产属于典型的离散制造模式,针对此情况,该系统实施生产报工及智能排产。系统展示设备主数据、设备维保计划数据,由SAP向MDAS定期同步。在制品数据、订单工艺路线、生产订单和看板数据由MES定期同步到MDAS,并考虑热前第一道工序单张看板数量和单次生产经济批量:单张看板数量的整数倍,根据班产参数和可用的第一个班次开始时间,计算第一道工序计划,超过该班产的数量安排到下一个可排班次上,优先安排当前工序的在制品数计划,然后再根据上道工序的计划完成时间,计算未来当前工序的设备排产计划,各工序从前往后、按照时间先后顺序进行,各工序依此类推。
领班对车间设备排产调整确认,当前生产班次不允许修改;车间领班确认后的设备排产计划,生成或导出生产作业指令:系统自动采集设备已加工零件数量,实时显示在“设备自动计完工数”文本框。若设备自动计完工数>看板卡可报工数,设备自动采集的完工数记到下一看板卡。
(3)设备维护
在设备正常生产时间内,系统识别设备的状态,包括运行、空闲、故障及关机,由操作工对非正常设备状态进行维护,维护的设备状态原因参考车间板报上的JPH损失分类,包括设备故障、检验、待料、产品切换、工装切换、刀具切换、其他及调试首件等。
JPH(每小时工作量)=合格零件数/净运行时间(1)在车间机床设备上的IPC屏幕软件中,设置了当前班次JPH数据查询入口,显示当前班次开始截止到当前时间前一个时间段的JPH数据,对于未达标的数据以红色的颜色醒目展示。
同时,在当前窗口中,以滚动消息的形式,提示操作工有未达标的JPH数据(图3),注意及时维护损失原因状态。
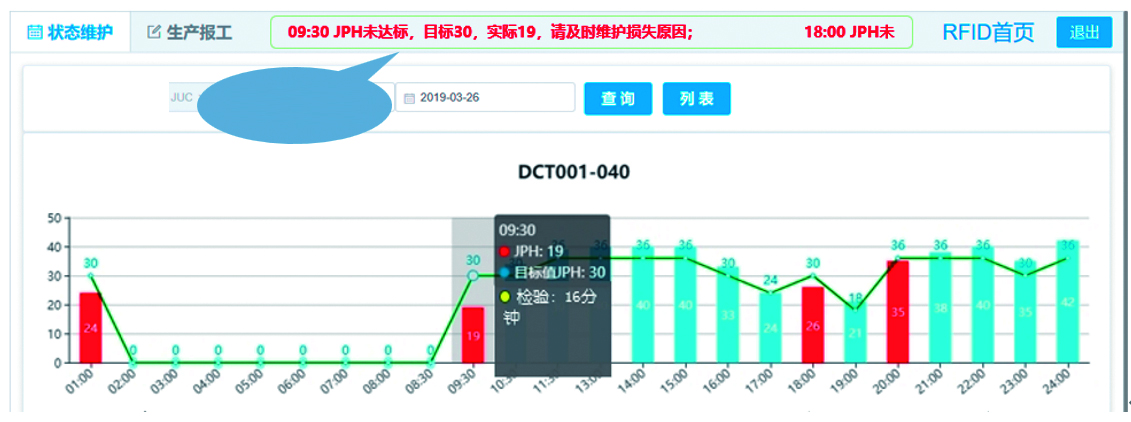
图3 JPH监控图
(4)OEE报表
OEE(全局设备效率)是TPM(全员设备维护)的一个常用指标。它作为设备损失的一个关键指标,由日本设备维护协会(JapanInstituteofPlantMaintenance,JIPM)创建。OEE是对投资价值的一个测量。OEE测量设备的可用率、性能效率和质量合格率。监控和改善OEE的目的是寻找改善机会和归档预期的设备利用率增加,进而增加产出(收入),降低成本,降低库存(要求的运作资金)和降低净固定资产(提高投资效率)。监控和改善OEE的目标是提高设备的整体利用。这会引起高产品产出、低成本、降低的库存和净固定资产(提高投资效率)出来,同时也包含其相应损失。
ΣOEE(设备综合效率)=Σ可利用率*Σ性能效率*Σ质量合格率(2)Σ可利用率=Σ实际运行时间/Σ应运行时间(3)=(Σ班次时间-Σ计划停机时间-Σ非计划停机时间)/(Σ班次时间-Σ计划停机时间)Σ性能效率=Σ理想加工时间/Σ实际运行时间(4)
该系统从组织结构上来看可以是工厂-车间-班组-设备这样来区分,用户可以选择时间维度(日、周、月、年)进行OEE累计查询,系统生成不同车间的OEE累计指标;系统支持点击某个车间的柱状图形,生成该车间下的分班组OEE累计指标;系统支持点击某个班组的柱状图形,生成该班组下的分设备OEE累计指标。
按照工厂进行统计,展示每天表现最差的前10个OEE设备数据,显示包括OEE指标(图4)、设备运行效率、性能效率、不合格率各类指标数据,然后用户点击某台设备,下面显示该设备在这一天的损失情况。
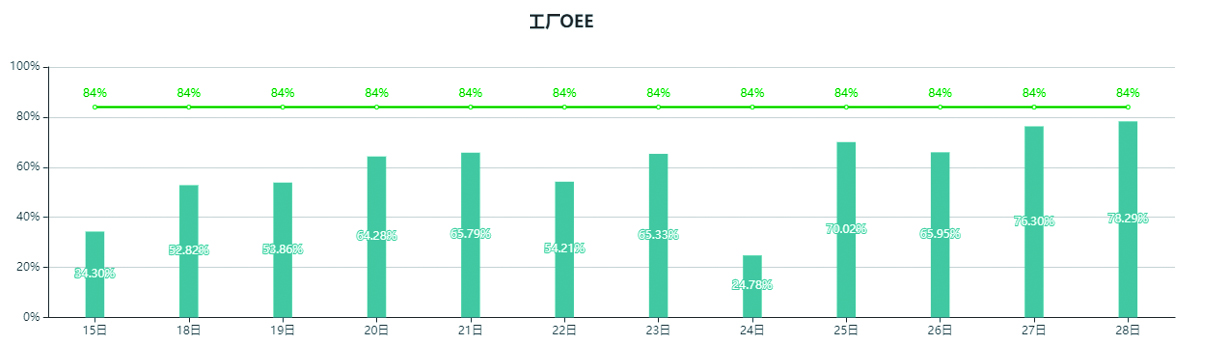
图4 OEE报表
结束语
本文是充分利用智能设备联网技术软件优势、特点,实施数据采集,结合产品确定车间需求,充分考虑未来发展方向、应用数字化和智能化场景落地,形成高效智能的设备联网技术,监控设备状态,优化生产报工及智能排产,实时展示设备OEE;本系统能够有效地帮助工厂进行生产管理、提高生产效率、开展智能化转型,为后续的智能制造奠定了研究基础。
本文为“AI汽车制造业”首发,未经授权不得转载。版权所有,转载请联系小编授权(VOGEL100)。本文作者:黄仁斌,单位:麦格纳(江西)传动有限公司。责任编辑龚淑娟,责任较对何发。本文转载请注明来源:AI汽车制造业
评论
加载更多