模块化装配是指将整车定义为由若干个主要部件组成,提前将这几个部件预先组装起来,成为几个模块,然后在主线上将这些模块装配至车身上。采用“模块化装配”的生产方式有利于提高汽车的装配质量,缩短汽车的生产周期,降低总装生产线的制造成本。
电动汽车总装模块化装配的内容
电动汽车总装模块化装配主要包括:前保分装总成、前端模块总成、仪表板分装总成、玻璃分装总成、座椅总成、顶棚分装总成、车门分装总成、后保分装总成、车轮分装总成、后悬分装总成、动力电池总成及前悬分装总成等。在精简了总装车间作业内容的同时有效地提高了生产效率。
总装模块化装配简介
1. 前保分装总成
(1)主要组成部件:前保本体总成、格栅分总成、雾灯总成、前保险杠线束、雷达和摄像头等。
(2)前保分装总成通常作为排序件,在分装区装配成总成后,按照生产车序排列至排序料架上并配送至线侧,作业人员按料架上的序列编号依次取用。
2. 前端模块总成
(1)主要组成部件:前端框架、散热器、冷凝器、前组合灯、前端线束、前防撞梁、前机盖锁、空调高低压管及进出水管等。
(2)前端模块化装配的优点
1)集成前组合灯安装骨架,前组合灯安装和调节简单。
2)机舱前部敞开,便于机舱前部零部件装配,避免作业人员跨入机舱内。
3)便于底盘模块与车身合装,提高底盘整体合装效率。
(3)前端模块与车身定位及装配的基本要求
1)车身需有定位孔,用于装配夹具定位。
2)前端框架或者前防撞梁应有安装工艺孔及安装助力机械手抓取点,以便抓取,同时应有分装工装支撑点,以固定框架,便于装配。
3. 仪表板分装总成
(1)主要组成部件:仪表板本体、组合仪表、智能终端、中控面板、组合开关、储物盒、雨量光传感器、仪表板横梁、仪表板线束、熔丝盒、空调主机、空调风道、转向管柱、安全气囊及相关控制模块等。
(2)仪表板分装总成模块化装配设计要求
1)仪表板分装线吊具的工装设计需考虑如下因素:①仪表板横梁上工艺孔的数量及位置。②仪表板分装总成模块在装配零部件时,模块在分装线吊具上调整姿态是否需要作360°的翻转。
2)仪表板分装总成模块的输送装置需考虑如下因素:①在仪表板横梁上的吊点位置;②吊点的牢靠程度;③仪表板分装总成模块的重量;④运送到主线时与安装助力机械手的转挂工艺孔位置。
3)安装助力机械手需考虑如下因素:①机械手的抓取方式是在仪表板横梁的两端采用销孔抓取式,还是在仪表板横梁的管梁下方采用支座托起式;②仪表板分装总成模块放置机械手后的宽度和高度是否能从门洞通过;③机械手进入车内,仪表板分装总成模块是否能方便固定,并且机械手能否顺利撤出,门洞通过性示意图如图1 所示。
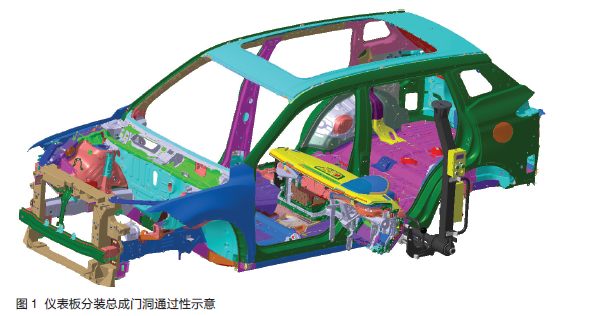
(3)仪表板分装总成模块化装配的优点
1)可保证与车身准确定位,提高与相关部件间隙控制。
2)减少作业人员进入车内频次,降低门槛、门洞等漆面划伤。
3)能实现总成电检,降低返修率,提高一次交检合格率。
4. 玻璃分装总成
(1)主要组成部件:风窗玻璃总成、胶条、底涂及玻璃胶。
(2)风窗玻璃一般采用机器人自动涂胶。
5. 座椅总成
(1)主要组成部件:座椅骨架、面套发泡、头枕和安全带锁扣等。
(2)座椅总成通常采用总成供货的方式,采用准时化配送,根据消耗情况(即时拉动)提供,直接由供应商的成品仓库配送到主机厂内靠近总装车间使用点的垛口或者临时缓存区,然后通过空中输送线转运至主线相应工位进行安装。
6. 顶棚分装总成
(1)主要组成部件:顶棚、顶棚线束和顶灯。
(2)顶棚分装总成通常在分装区完成装配后,转运至主线相应上线工位安装至车顶。
7. 车门分装总成
(1)主要组成部件:车门总成、门锁、车门把手系统、玻璃升降系统、密封系统、车门内护板、外后视镜、车门线束、闭锁器、限位器、扬声器、内开启手柄及控制模块等。
(2)车门分装总成模块化装配设计
车门分装总成模块采用在分装线上进行分装,然后通过安装助力机械手将车门安装至车身上。
(3)车门分装总成模块化设计时需要考虑的因素
1)实现车门模块化拆装的基本要求。
2)可用通用工具实现拆门、装门的工艺要求。
3)必须确保装门后,门的间隙面差得到保证。
4)确保线束连接简单可靠,且不影响其他零部件的装配。
5)确保可进行车门模块的电器检测。
6)车门线束连接要求:目前主流工厂车门合装在二次内饰线上完成,要求车门合装后不进行室内零部件的装配,同时可实现在所有内饰件装配完成后,在侧围外侧进行车门线束与整车线束的连接。
(4)车门模块化装配的优点
1)确保室内零部件装配的接近性,提供大件装配空间。
2)提升产品质量,减少面漆划伤,减少门的开关操作。
3)简化机械化结构,吊具和安全网等不需要避让车门。
4)提高生产线宽度方向的利用率,取件便捷,提高装配效率。
8. 后保分装总成
(1)主要组成部件:后保本体总成、倒车雷达线束、倒车雷达及后回复反射器等。
(2)后保分装总成通常作为排序件,在分装区装配成总成后,按照生产车序排列至排序料架上并配送至线侧,作业人员按料架上的序列编号依次取用。
9. 车轮分装总成
(1)主要组成部件:轮胎、轮毂、气门嘴(带胎压传感器)和平衡块。
(2)车轮分装总成通常采用全自动轮胎分装线进行装配,然后通过车轮输送线(空中输送)转运至主线(底盘线或二次内饰线)进行安装,车轮分装流程如图2 所示。
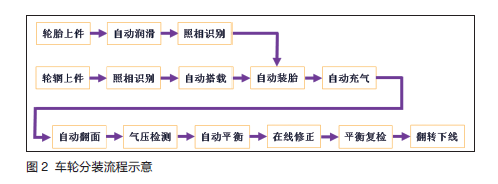
10. 后悬分装总成
(1)主要组成部件:后副车架、电驱动总成、等速驱动轴、后制动器、下摆臂、上摇臂、控制臂、后驻车制动拉索、后制动油管、后轮速传感器、螺旋弹簧及后减振器等。
(2)后悬分装总成模块化装配设计时的必要因素
1)后悬上有合适的吊运点位置。
2)后悬的放置角度满足工艺要求。
3)各零部件装配工序安排合理顺畅,不影响后续零部件装配。
11. 动力电池总成
(1)主要组成部件:电池包壳体、电池单体模组、BMS 管理系统及MSD 等。
(2)动力电池总成通常采用总成供货的方式,总装车间在上线装配前进行绝缘检测。
12. 前悬分装总成
(1)主要组成部件:前副车架、前稳定杆总成、转向器带横拉杆总成、左/ 右下摆臂总成、左/ 右转向节带制动器总成及左/ 右前减振器总成等。
(2)前悬分装总成模块化装配设计时的必要因素。
1)模块放置到合装托盘上固定牢靠,无滑落风险,吊运链条吊点操作方便。
2)装配时,工具的操作空间要满足要求。
3)组装的零部件装配工序安排合理顺畅,不影响后续零部件装配。
底盘模块整体合装装配设计
1.底盘模块整体合装内容:后悬分装总成、动力电池总成及前悬分装总成。将后悬分装总成、动力电池总成和前悬分装总成分别吊装至整体合装托盘上,整体合装托盘与车身的装配位置对准后,通过液压举升装置将托盘升起,进行前悬、动力电池和后悬模块同时装配,如图3 所示。
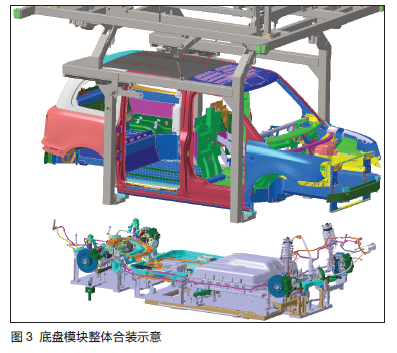
2. 整体合装设计时的必要因素
(1)合装托盘上需设计前副车架、后副车架及动力电池总成的定位销、前副车架和后副车架,动力电池总成上设计对应的定位工艺孔。
(2)合装托盘上需设计车身总成的定位销,车身上设计对应的定位工艺孔。
(3)车身在吊具上需考虑必要的压紧,防止整体合装托盘升起的过程中车身被顶起,影响定位精度。
3. 模块化装配设计的原则
(1)把装配零部件的数量减少到最少。
(2) 考虑零部件拆装的简易性。
(3)考虑最优的连接方式。模块化装配的常规工艺布局如图4 所示。
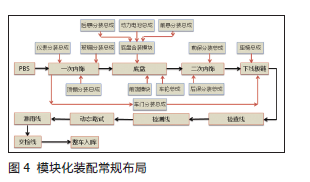
结论
模块化装配可缩短主线长度,降低产线投资,简化工艺布置,能有效提高主线使用效率,便于混线生产各装配工位生产节拍的平衡,能有效降低车间PC 区及线旁零部件仓储量,充分有效利用现有人力资源,避免忙闲不均,降低整车工时及单车制造成本。
评论
加载更多