当传统生产线的产能出现不能满足销量需求时,采取的措施是提高瓶颈工序设备的产出。通常采用的方法为:增加瓶颈工序设备数量;提高瓶颈工序设备的切削参数,以达到加快设备生产节拍的目的。但是增加瓶颈工序设备数量需要增加投资和设备面积等;提高切削参数会造成相应的加工质量风险,并且会降低刀具寿命,增加刀具成本,并且令换刀及换刀后检查停机的次数增加,影响实际产出。
本文以神龙汽车公司前轮毂3线为例,阐述如何在不增加设备、不提高设备切削参数的情况下,采用精益化生产改善方法提高生产线产能。
生产线改善前的情况
1.工艺方法情况
(1)工艺流程
前轮毂3线沿用法国PSA公司生产工艺方法,工艺流程如图1所示。
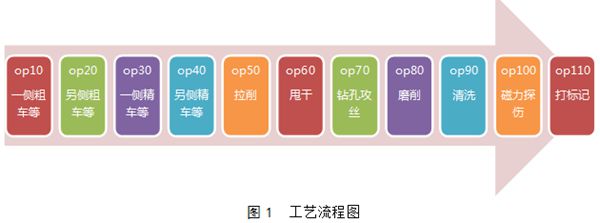
(2)加工特点
从图1可以看出,前轮毂3线工序安排情况,主要有车削、拉削、磨削以及特殊工序,共有11个工序组成,其中OP10、OP20、OP30和OP40是4个工序车削加工。
2.产能情况
影响生产线产能的因素有工艺能力、生产组织、设备故障和质量损失等,而决定生产线产能的主要因素是工艺能力。前轮毂3线各个工序的工艺能力如图2所示。
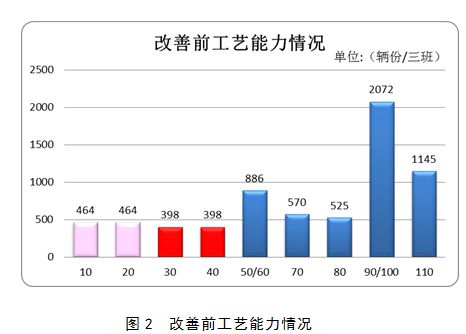
从图2可以看出,工艺能力最低的工序集中在OP10、OP20、OP30和OP40这四个车削加工工序。该生产线生产的瓶颈工序为OP30、OP40,次瓶颈工序为OP10、OP20。这4个车削工序制约了整个生产线的产出,最低工艺能力为398辆份/3班。前轮毂3线年工艺能力只有11万辆份。(我公司机械件产品发展纲要规定:年工作时间276天,工作班次为3班,日工作时间为1260min)。
生产线改善前的瓶颈分析
1.车削加工工序改善前平面布置
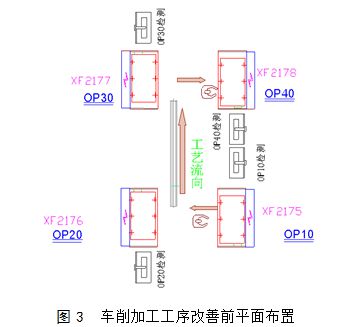
从图3所示的平面布置可以看出,该生产线前轮毂车削加工的工艺流为OP10→OP20→OP30→ OPp40,设备布置是串联模式。车削工序需两个操作工操作设备,一个操作工负责OP10、OP20,另一个操作工负责OP30、OP40。每个工序各有一个检查台,线旁共布置有4个检查台,需要人工往返设备和检查台来检查零件。
2.改善前工艺能力分析
工艺能力计算公式:工艺能力=工作时间/循环时间C。
车削工序工艺能力的构成如图4所示。其中,循环时间C=节拍CI+换刀及换刀检查+检查时间+其他。所以,工艺能力=工作时间/(节拍CI+换刀及换刀检查+检查时间+其他)。
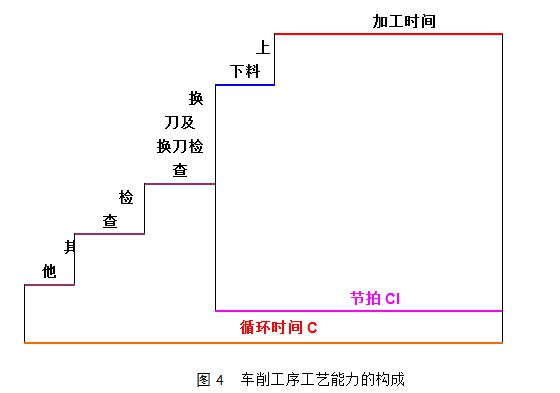
提高前轮毂3线的工艺能力,就需要对车削工序进行精益改善,按照我公司机械件产品发展纲要的规定,工作时间是保持不变的,因此提高工艺能力需要减少循环时间C,所以提高工艺能力就是需要降低车削工序节拍CI、减少换刀及换刀检查时间和检查时间。
前轮毂3线车削工序各项时间、工艺能力情况如表1所示。
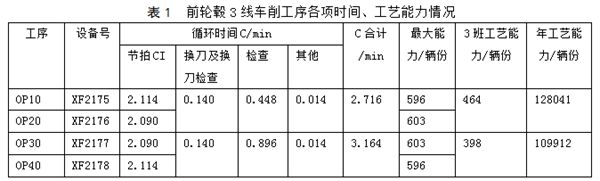
从表1可以看出前轮毂3线车削工序工艺能力情况如下:OP10、OP 20年工艺能力12.8万辆份,OP30、OP40年工艺能力11万辆份;故车削工序最小年工艺能力只有11万辆份,达不到该生产线产能的需求。
3. 改善前的加工分析
如表2所示,OP10~OP40总共需要9把车刀,换刀及换刀检查时间合计0.28min/辆份。

4.改善前的检查分析
OP10~OP40总共76个检查项目;总共需要43个检具检查,需要4个检查台。检查时间合计1.344min/辆份。
生产线瓶颈改善
1. 车削加工工序精益改善方法
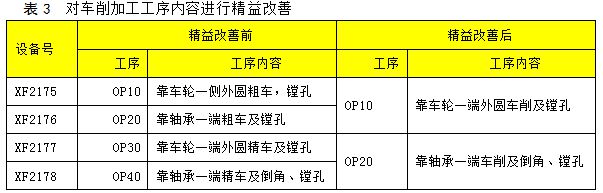
对车削加工工序内容进行精益改善(见表3),将原OP10、OP20、OP30和OP40内容重新安排(分配),工序重组为OP10和OP20两个工序,设备布置改为并联模式。车削工序操作工保持两名不变,一个操作工操作OP10两台设备(设备号:XF2175/XF2176),另一个操作工操作OP20两台设备(设备号:XF2177/XF2178)。生产线减少了2个检查台,线旁只保留2个检查台,平面布置如图5所示。
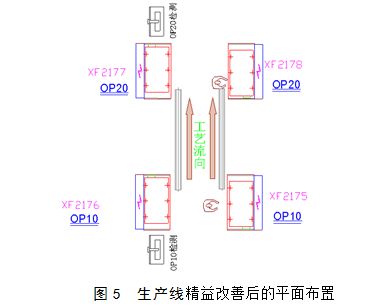
2.车削工序工艺精益改善后情况
(1)精益改善后OP10~OP20刀具的加工内容如表4所示。
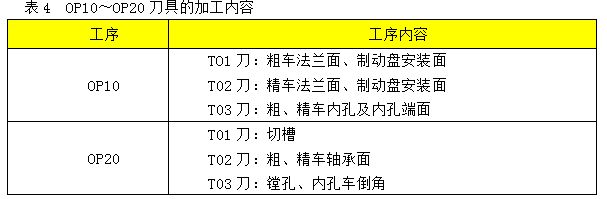
OP10~OP20为完成所有加工内容,总共需要6把车刀,相比改善前减少了3把刀,刀具数量减少了33.3%。换刀及换刀检查时间合计0.235min/辆份,相比改善前下降了16%。
(2)检查精益改善
通过对检查的精益改善,检查项目改善后改为46项,相比改善前减少检查项目30项;检具改善后为24个,减少了19个检具;检查时间合计0.25min/辆份,检查时间减少了1.09min/辆份。
3. 改善案例
以OP10为例:从表5可以看出,OP10通过精益改善,加工节拍CI时间减少了0.581min/辆份,换刀及换刀后检查时间减少了0.019min/辆份,检查时间减少了0.32 min/辆份,循环时间C减少了0.933min/辆份。
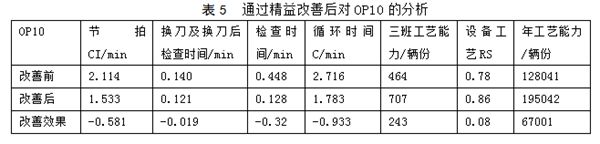
基于加工、刀具和检查时间的改善,OP10工艺能力得到了很大的改善:3班工艺能力由改善前的464辆份提升到707辆份,提升了243辆份;该工序的工艺RS由改善前的0.78提升到0.86,提升了0.08;该工序年全年工艺能力由12.8万辆份提升到了19.5万辆份,该工序产能提升了52.3%。
改善效果
1.车削工序改善后的情况
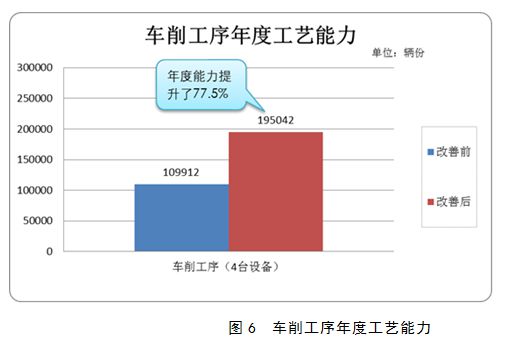
前轮毂3线通过精益改善,车削工序由原来4个工序(1台设备/工序)优化为两个工序(2台设备/工序),并对车削工序的刀具、检具也进行了相应的精益改善。通过这一系列的精益改善,前轮毂3线车削工序年工艺能力由11万辆份提升到了19.5万辆份,车削工序工艺能力提升了77.5%(见图6)。
2.生产线改善后产能效果
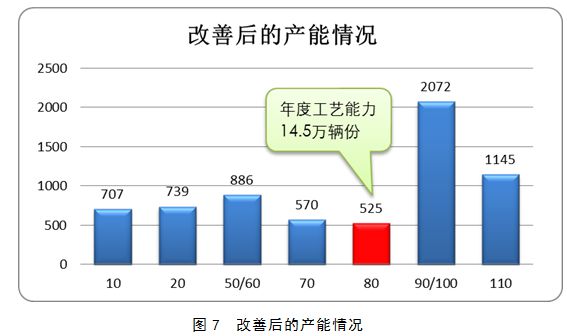
从图7可以看出,通过精益改善,车削工序工艺能力已经提升到了707辆份/3班,该生产线瓶颈不再是车削工序,瓶颈已经转为OP80工序,而OP80工序工艺能力为525辆份/3班,该工序年工艺能力已经达到14.5万辆份。通过精益改善,前轮毂3线年工艺能力由11万辆份提升到14.5万辆份,实现了该生产线工艺能力提升32%。
前轮毂3线车削工序通过精益改善,将原先的一序一机重组为一序两机,而上下料方式不变,实现加工时间占工序节拍CI的比率由改善前的72%上升到83%,从而达到降低机床的主轴转速和刀具的进给速度、减少刀具的磨损,可相应提高刀具寿命,减少换刀次数,减少换刀及换刀检查引起的停机,降低了刀具和生产的成本,实现了产能提升。
通过精益改善,实现工序合并,减少了中间尺寸的加工,减少了刀具数量,从而减少了换刀及换刀检查引起的停机;也实现了减少中间尺寸相应的检查项目,减少了相应的检具,同时减少了检查台的物流面积,同时由于减少了检具实现减少停机检查的时间,实现了产能提升。
结语
在实际生产中,我们通过对现有的生产线通过精益化工艺改善,在经过全面的分析论证后,将工序内容合并重组,采用一序多机的生产模式,使工序内容更加集中,实现了提高生产线产能的目的。
在前轮毂3线上,通过采用精益化生产改善方法,可以实现:
1.减少了工序的装夹次数。工件在一次装夹中可加工多个表面,可减少装夹所造成的误差,有利于保证这些表面之间的相互位置精度,利于保证表面间的位置精度,在加工质量更稳定的同时减少了工人上下料操作,使工人劳动强度大大减小。
2.减少工序数目,缩短了工艺路线,也简化了生产计划和组织工作。
3.减少辅助操作。采取工序精益改善后,减少了中间尺寸的检查,减少了相应的检具,减少了检查时间和相应的工艺停机时间。
4.采用一序多机,设备布置由串联改为并联模式,可提高生产线柔性化水平:一序一机模式,当 1台设备维修,产能损失达100%;而一序两机,当 1台设备维修,产能损失只有50%。
精益化生产要求工艺方法充分考虑产品增值有效的原则,消除生产中不增值操作,提高工厂生产柔性化,达到产能提升。前轮毂3通过精益改善,车削工序实现一序两机生产模式,减少刀具33.3%,减少检具44.2%,该机加生产线的工艺能力提升了32%。实现了产能、质量、效率的同步提升,合计节约成本约46.9万元/年。
评论 0
正在获取数据......