由宝马公司领导的一个研究项目正在引起人们的注意。12个项目合作伙伴开发了一条数字网络化、全自动的3D金属生产线。这就是汽车批量生产的突破口吗?
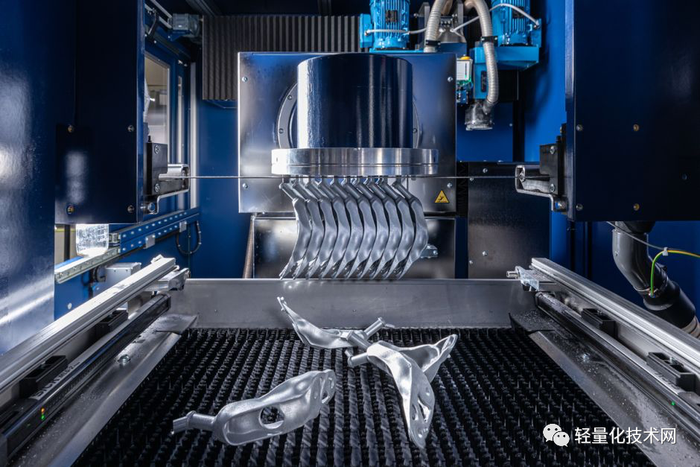
3D金属打印为批量生产做好准备-在宝马公司的领导下,项目参与者全面改进了从3D部件的开发和设计、在线过程监控、AI评估到数字孪生的整个过程链(来源:BMW)
慢慢地,一个高度复杂的组件在闪烁的激光中从无到有地建立起来。任何第一次看到3D金属打印工艺演示的人都会着迷。然而,到目前为止,阻碍系列化使用的不仅是缓慢的建立速度,而且还缺乏自动化概念、数字化战略和金属粉末。位于德国汉堡弗劳恩霍夫增材制造技术研究所的负责人柯巴萨教授强调:"仅仅优化工艺是不够的,需要的是对整个工艺链的整体改进,包括硬件和软件之间接口的标准化。
每年50,000个组件:这只是个开始吗?
这位科学家提出的建议于2019年得到了德国政府部门的重视。在德国联邦教育和研究部(BMBF)的资助下,在IDAM项目(增材制造的工业化和数字化)框架内,位于波恩的吉凯恩冶金公司和位于Oberschleissheim的宝马集团增材制造园区创建了两条数字联网的全自动生产线,采用25年前由位于亚琛的弗劳恩霍夫激光技术研究所ILT发明的激光粉末床熔融(LPBF)工艺。在三年内,12个项目合作伙伴,从业主管理的小企业到大公司,都成功地建立了3D金属打印生产线,并将其整合到系列生产中。它们可用于每年以高生产率的方式生产5万个相同的部件和超过1万个单独和备用的部件。由于采用了模块化设计,年生产量可以根据需要进行扩展。
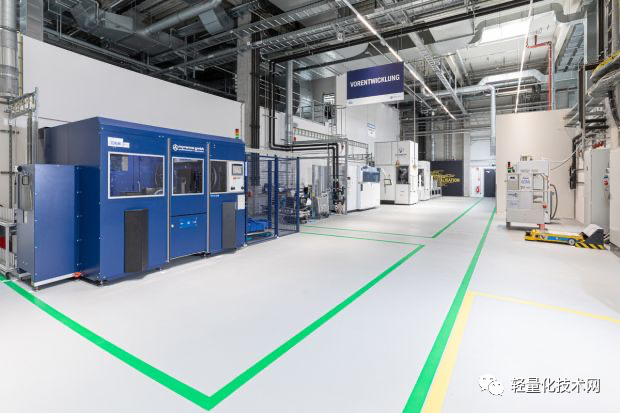
在波恩的吉凯恩冶金公司和位于奥伯施莱斯海姆的宝马集团增材制造园区,在IDAM项目(增材制造的工业化和数字化)中创建了两条数字网络化、全自动的生产线(来源:BMW)
成功因素:定制的金属粉末
项目参与者从三维部件的开发和设计、在线过程监控、人工智能评估到数字孪生体,全面改进了整个过程链。
IDAM项目的参与者,来自波恩的GKN添加剂有限公司的Simon Höges博士说:“不仅是工艺,就连金属粉末也必须是定制的。”
在亚琛举行的AKL'22国际激光技术大会上,这位负责金属3D打印主管介绍了DPLA金属粉末,这是为LPBF工艺量身定做的,以低合金双相钢DP600为基础,广泛用于汽车工业。据GKN公司称,新开发的产品不仅具有与DP600相当的机械性能,而且据Höges称,它还可以进行"面向应用的热处理":用户可以通过有针对性的热处理工艺来改变强度等重要性能。
来自福特公司的Raphael Koch在AKL'22上也指出,打印部件的质量与粉末的选择和材料的硬度有关。这位增材制造研究工程师在为底盘领域开发功能性LPBF原型方面获得了第一次经验。他开发的产品是副车架和叉骨,传统上由热轧多相钢制成。
3D金属打印:不适合大规模生产
Koch的经验让人吃惊:他不主张定制原材料,而是从市场上购买3D打印金属粉末,因为这样可以减少开发时间和成本。然而,打印的部件应该具有与传统的底盘金属板类似的性能。屈服强度应达到700至800兆帕,伸长率超过10%,密度为7.85克/厘米³。基于3D金属打印在底盘领域的首次良好经验,现在可以想象 "用金属3D打印部件取代传统原型"。一般来说,3D金属打印也适用于小型和中型部件或混合版本,但不建议用于大规模生产。
通快公司的增材制造应用、材料和咨询主管Severin Luzius说:"增材制造的进一步发展只有在设备、粉末和工艺的相互作用中才能实现。他举例说,使用集成热处理的TruPrint 5000增材制造系统,通过500摄氏度的预热,可以对高碳含量的工具钢进行3D打印。"随着碳含量的增加,钢可以得到更好的硬化,它的磨损也更小,"Luzius解释说。"这也将使用户能够打印在汽车工业中广泛使用的usibor钢的成型工具,并通过接近轮廓的冷却来减少工具的磨损。"
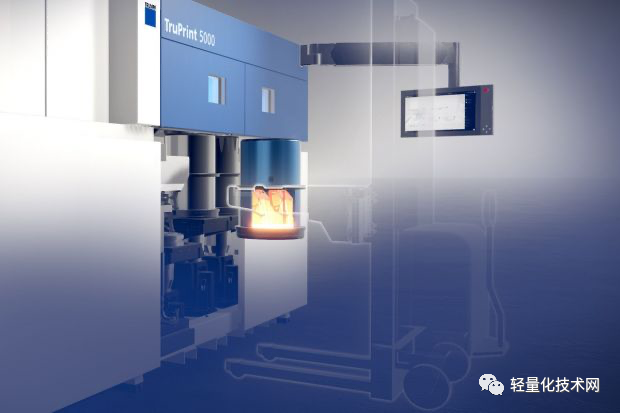
综合热处理-带有集成热处理的TruPrint 5000增材制造系统通过500摄氏度的预热,可以对高碳含量的工具钢进行3D打印(来源: Trumpf)
金属玻璃:强度高、硬度大、弹性好
令人激动的新应用有时只有在与其他公司合作时才会出现。一个项目涉及非晶态金属的3D打印。这些材料也被称为金属玻璃,非常坚硬、牢固,同时具有弹性。换句话说,它们的属性实际上是相互矛盾的。由于其高强度,开发人员可以用非晶态金属设计出更薄的部件,节省材料,因此更轻。这种材料已经在汽车行业的耐磨驱动部件和齿轮、稳定的悬架和注射喷嘴的薄膜中得到了验证。通快公司的材料专家Jan-Christian Schauer解释说:"为了打印非晶态金属,通快公司和Heraeus Amloy共同开发了一种工艺,该工艺可以在非常精细的焦点和极小的熔体量下工作。"热量很快就散去了。这就达到了临界冷却速率,使材料无定形地凝固。"
但传统工艺与金属3D打印的结合提供了更多的可能性。在弗劳恩霍夫ILT的协调下,工业企业在MultiPROmobil研究项目中开发了多功能激光工具,用于切割、焊接和用金属丝堆积焊接(w-LMD)。它们被用于多功能激光机器人技术的单元中,该单元旨在结合数字孪生技术,灵活而经济地生产电动汽车的金属板组件。
进一步开发的组合头能自我适应
重点是一个组合头,已经在半仿生轻量化部件的测试生产中得到了验证。该组合头使用添加剂结构来切割、焊接和加固电动汽车的设计优化的三角控制臂。所有这些都是在不更换刀具的情况下快速完成的,这要归功于风冷组合头,它通过自主喷嘴和自适应光束整形光学系统,快速适应三种不同的加工过程。
评论 0
正在获取数据......