当前,双离合自动变速器的应用越来越广泛, 而双离合自动变速器相对于手动变速器的装配要求更为严格,应用一些相应的防错技术,可消除装配过程中错装、漏装等潜在风险。防错技术的合理应用,对有效提高产品品质、降低生产成本、提高企业在市场上的竞争力,发挥着重要作用。
防错技术的意义及主要方法
图 1 所示,智能料架上设置有捡料传感器,装配时智能料架上相应零部件的捡料传感器显示绿色,人工拾取该零部件;当取料错误时,捡料传感器为红色并报警提示,在人工拾取正确的零件后,工件上方的激光指示灯会指示装配位置,人工将零部件装配到相应的位置,完成装配后进入下一个循环,依次进行装配。智能料架和激光指示灯防双离合变速器装配线包含齿轴类零件的装配、错属于传感器类的防错,区别于一般的取料防错。
液压模块的装配和壳体附件的装配。其中,齿轴类零部件主要包含同步器、轴承的压装和齿轮的装配;液压模块的装配主要包含电磁阀的装配;壳体附件主要包含螺栓的拧紧、轴承的压装等。同步器、轴承以及电磁阀类零部件极其相似,不能仅靠人工进行装配的防错识别,而且很多变速器零部件为过盈配合,一旦出现错装漏装,将会造成制造成本的增加和产品质量的缺陷。目前 , 在双离合自动变速器装配线上,主要有设备防错和人工防错两种方式。其中,设备防错又包含特定控制程序防错、工装防错及传感器防错等。人工防错主要是采取本工位的自检和后续工位的互检来协作完成。有些防错还需要设备和人工两方面共同完成,优秀防错方法的实施,能避免众多的失效模式,保证变速器的制造品质。
双离合自动变速器装配线上防错技术
1. 智能料架和激光指示灯防错
DCT 液压模块装配主要包含电磁阀的装配, 齿轴装配主要包含齿轮和同步器的装配。由于这类零部件的外形极为相似,因此在装配时采用智能架防错和激光指示灯相结合的防错方式。如图1所示,智能料架上设置有捡料传感器,装配时智能料架上相应零部件的捡料传感器显示绿色,人工拾取该零部件;当取料错误时,捡料传感器为红色并报警提示,在人工拾取正确的零件后,工件上方的激光指示灯会指示装配位置,人工将零部件装配到相应的位置完成装配后进入下个循环,依次进行装配。智能料架和激光指示灯防错属于传感器类的防错,区别于一般的取料防错。我厂的液压模块装配线通过激光指示灯的指示防错,可以指示零部件的相应位置,操作人员从防错料架上取下零部件并按照激光指示灯的指示进行装配,不需要人为识别装配位置,在实际生产中取得良好的效果。
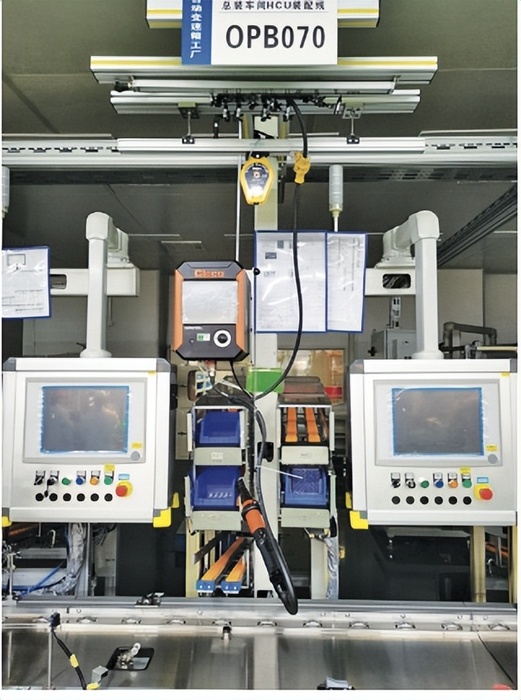
图 1 激光指示灯与智能料架
2. 压装防错
压装是变速器装配过程中的重要工艺,在零部件压装过程中的防错主要通过机械防错和传感器防错相结合的防错方式。通过零部件外形尺寸的差异,进行压装装置的仿型防错,错误的零部件不能安装到压装装置上进行压装。同时,采用高精度伺服电缸进行压装,伺服电缸内置压力传感器和位移传感器,具备压力和位移监控功能,只有正确的零部件压装时压力和位移合格,在防错压漏压的同时也具备零部件质量监控功能。
3. 拧紧防错
双离合自动变速器装配线过程中,有很多需要拧紧的固定组件都需要拧紧枪来完成。拧紧固定配件是安装装配线过程中极为重要的工作内容,拧紧的质量对变速器的质量有直接影响。在变速器的安装过程中无论是机械拧紧还是人工拧紧都存在着一定的风险,为了防止出现错漏,在安装变速器装图 1 激光指示灯与智能料架配线过程中要使用拧紧枪的防错技术。
(1) 人工拧紧
人工拧紧主要使用的工具是手持式电枪。拧紧技术要分段进行:首先高速拧紧到达中间值,再用正常速度拧紧 , 最终实现拧紧要求。在变速器生产过程中,要充分考虑生产要求与生产节奏的要求,多种需要拧紧的配件有时会出现在同一个地方,这增加了拧紧难度,加大了操作风险 , 从而容易出现由于操作失误而产生的错拧、漏拧现象,进而影响了变速器的质量。如图 2 所示,为了避免这种错误发生,要使用防错技术收集单轴电枪拧紧后的合格信号。当单轴电枪进入到目标后,将拧紧合格信号发送到防错装置中,防错装置对合格信号的数据进行对比,防止出现错漏。
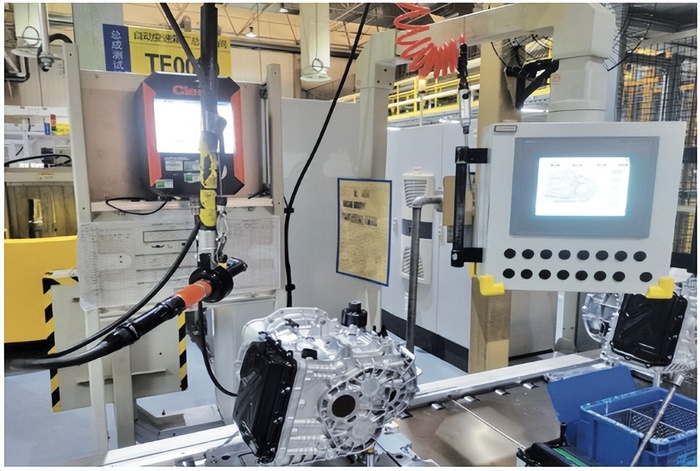
图 2 电枪与防错装置
(2) 自动拧紧
自动拧紧主要是用多轴拧紧机同时拧紧的原理进行操作。这里需要注意的是,多轴拧紧机相 较于单轴电枪拧紧装置在程序上多加了一项同步拧紧步骤,防止不同拧紧步骤中造成的零部件变形,从而影响变速器的质量。在拧紧时倘若出现漏装现象,那么将会使防错系统不能检测到同步信号,进而使后续拧紧程序无法进行,拧紧装置自动报警,使拧紧程序结束。拧紧系统无法将错误信号发出,使防错装置不能接受到拧紧合格信号,从而显示拧紧不合格,使造成的缺陷不能向后面的工作传递,达到了自动拧紧程序中漏拧的防错目的。
4. 视觉系统防错
机器视觉通常采用照相机摄取检测图像,将其转化为数字信号,再采用计算机对图像数字信 号进行处理,从而得到所需要的各种目标图像特征值,并在此基础上实现模式识别、坐标计算和灰度分布图等多种功能,从而来辨别零部件特征以及装配质量的正确与否,杜绝缺陷。
机器视觉系统主要有以下优势:一是降低人工检测的强度、减轻人工的压力;二是采用统一标准模板,自动进行检测,稳定性强;三是在现代高度自动化的流水线上,采用机器视觉系统可 快速对产品进行全检;四是能实现高精度检测;五是能将检测的数据及时进行上传和分析,利于信息的收集。
在双离合自动变速器装配过程中,视觉系统防错防漏技术主要应用于轴系总成的外观检测、 涂胶胶线检测和壳体合箱前外观检测。轴系总成装配完成后通过齿轴照相进行外观检测,对比该 轴系的外轮廓与合格标准件的外轮廓差异,一旦超差就表示有错装出现,报警提示并将不合格品下线。壳体结合面涂胶视觉系统检测,主要检测胶线的轨迹、胶线的直径和有无断胶等缺陷。如图3所示,壳体合箱前外观检测主要检查O 形圈、垫片等有无漏装。由于壳体合箱为过盈配合, 如果有漏装现象,将无法检查或者返修,一旦出现漏装情况,将会造成工件的报废。因此在上述工位设置视觉系统检测,可以防止错装和漏装的情况。
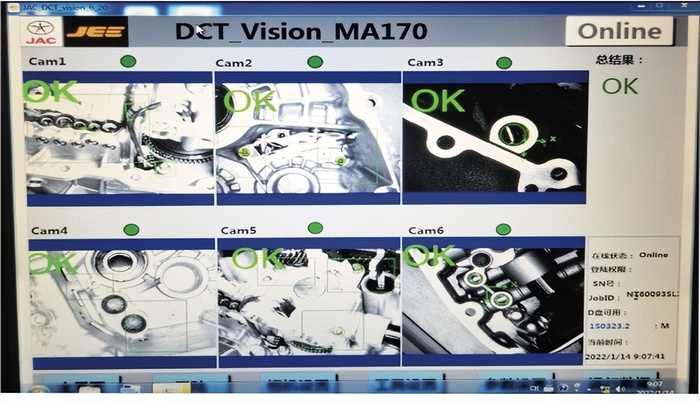
图 3 零部件错漏装检测
总结
防错技术已成为汽车制造业今后的发展趋势。在质量管理中,工艺技术人员应理论联系实际, 广泛开展防错技术的研究并推广应用,以零缺陷的目标和零缺陷的标准打造零缺陷的产品工艺过程设计,减少生产中人为差错发生的机会,避免差错形成缺陷,切实提高企业质量管理和质量改进工作的主动性,从而使质量管理和产品质量上一个新的台阶,推动我国汽车工业的发展。
评论 0
没有更多评论了