车身车间的连接方式主要有点焊、螺接、弧焊、SPR 和 FDS 等。螺栓连接作为其中的一种主要方式,优点是操作简单、可拆卸重复加工、可达性好及强度高,经常用在一些焊枪不可达区域以及门盖与车身的连接。而螺栓拧紧合格与否,最直接的判断方式就是确认扭矩是否符合产品设计要求。近年来市场竞争日趋激烈,对整车质量控制提出了更高的要求。本文介绍了基于大数据的车身扭矩控制方案并在新项目中进行了验证。通过大数据平台,对车间内部各工位的扭矩进行实时监控。车身车间各个拧紧工位通过网络将拧紧扭矩数据传输至车间内部服务器并上传至云端大数据平台。车身扭矩工程师、质量工程师和售后服务工程师可通过大数据客户端查询、分析扭矩数据。
螺栓连接定义
螺栓连接主要通过螺栓与螺母之间的配合,将两个或者多个零部件连接在一起,如图 1 所示。典型的拧紧过程主要有快速拧紧、驻车制动、终拧紧、返松四步,而对于自动化程度较高的拧紧工位还有自动送钉认帽、进枪寻孔等步骤。
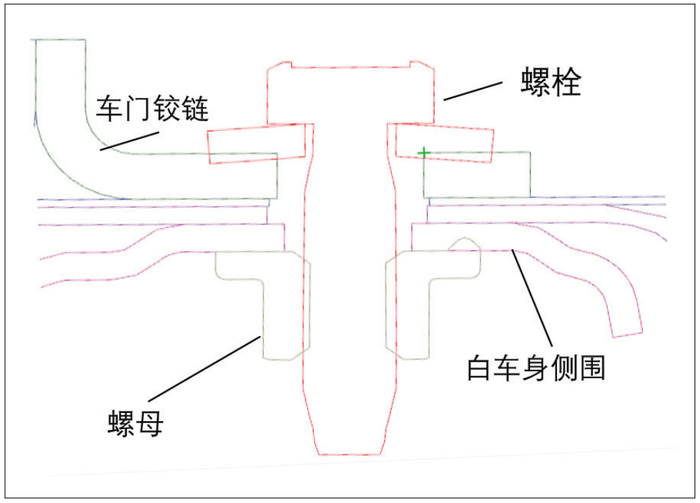
图 1 四门与侧围螺栓链接
根据所连接的零部件状态对扭矩的影响程度,螺栓连接可分为软连接、硬连接和联合连接。拧紧过程中螺栓先拧紧到零部件贴合点,从贴合点拧紧到目标扭矩的过程中螺栓转过的角度小于30 °的为硬连接;从贴合点拧紧到目标扭矩的过程中螺栓转过的角度大于 720 °的为软连接,例如塑料件安装等;处于 30 °与 720 °之间的为联合连接。目前车身车间内螺栓连接主要为钣金支架与车身及门盖与车身之间的连接,属于联合连接。
螺栓拧紧过程中产生的力矩一般称为扭矩。软连接由于连接的零部件比较软或者连接的零部件中存在橡胶等弹性元件存在扭矩衰减。而硬连接由于是刚性连接,一般不存在衰减,甚至可能存在反冲。
扭矩分为动态扭矩和静态扭矩。动态扭矩是螺栓/螺母拧紧过程中工具设备端输出的扭矩,是由产品工程师根据产品性能需求设定的扭矩值。静态扭矩是指在一个紧固件被固定好之后,需要将其在紧固方向上继续旋转的瞬间所需要的扭矩,通常使用表盘式扳手检测紧固件获得。动态扭矩是产品扭矩,由产品直接定义;静态扭矩是工艺扭矩,是车间现场实际测量得到的扭矩。
正式生产过程中的静态扭矩是根据 SPC 统计方法原理,用试生产阶段采集的静态扭矩计算得出静态扭矩的上限、下限及目标值。
拧紧系统组成
拧紧系统主要由拧紧驱动系统、数据存储及交互系统、数据传输系统和质量反馈系统组成,如图2所示。
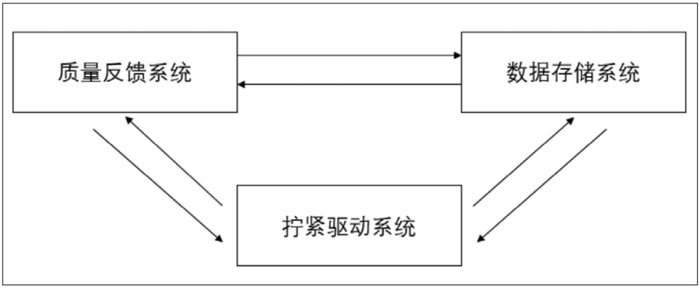
图 2 拧紧系统构成
1.拧紧驱动系统
拧紧驱动系统根据动力源分为气动拧紧枪和电动拧紧枪或拧紧轴,如图3和图4所示。
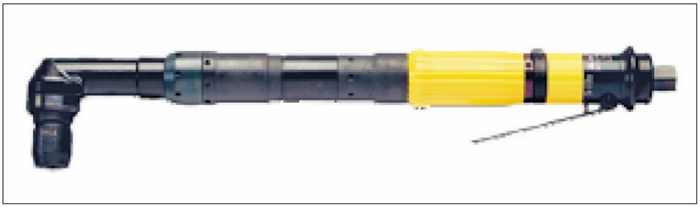
图 3 气动拧紧枪
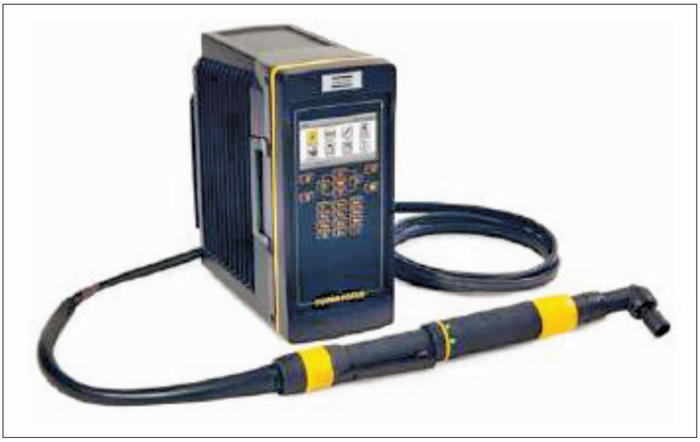
图 4 电动拧紧枪
电动拧紧枪和拧紧轴可以由控制器进行拧紧参数的设定及调整。电动拧紧枪由于精度高、工作噪声小同时可实现拧紧数据收集等优势,使用范围越来越广。
2.数据存储及交互系统
数据存储及交互系统主要负责扭矩数据存储及与客户端的数据交换。它主要由车间内部服务器、质量暗灯系统服务器、大数据平台服务器及客户端组成。
车间内部服务器负责收集、分析各工位扭矩枪控制器传输过来的扭矩信息并将扭矩信息上传至云端大数据平台。如图5所示,车间内部服务器主要有数据收集、数据分析及网络客户端模块。
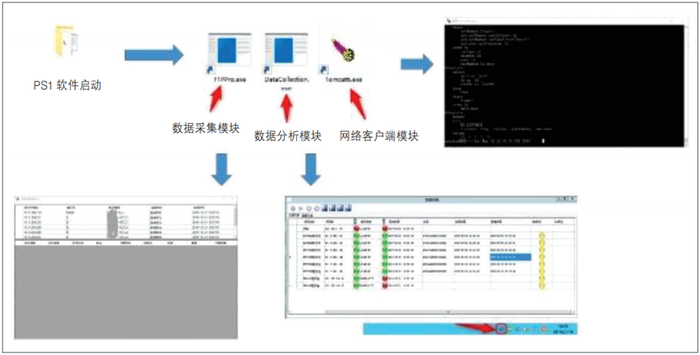
图 5 车间内部服务器模块组成
通过客户端,车间扭矩工程师可在线管理拧紧设备、定义扭矩枪参数、定义工艺信息、查询单车扭矩信息、对生产车辆扭矩合格率及扭矩趋势进行分析,如图6所示。
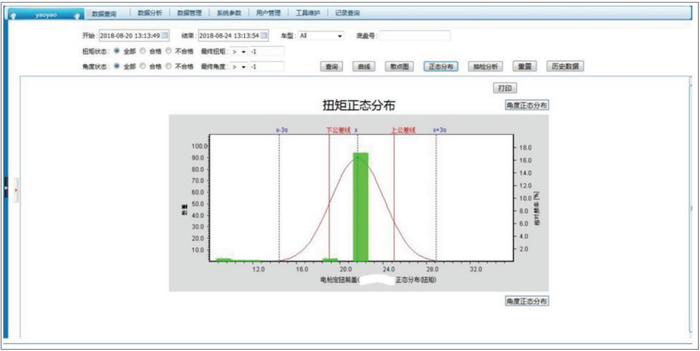
图 6 扭矩正态分布
大数据平台服务器主要负责收集并处理车间扭矩服务器上传的扭矩信息及满足外部客户端对扭矩信息追溯。
上传至云平台的扭矩信息数据中包含拧紧时间、车辆VIN码、拧紧过程曲线、最终拧紧扭矩、最终拧紧角度以及拧紧状态判定。车型信息反馈、扭矩数据上传、报警信号反馈都需要通过数据传输系统实现。
主流现代化车身车间内PLC与扭矩枪控制器及暗灯系统之间的车型信息、报警信息通过总线进行传递。扭矩枪控制器、车间内部服务器、云端大数据平台服务器之间的扭矩信息通过IT网络传递。
3.质量报警反馈系统
质量报警反馈系统服务器主要负责对记入质量系统的缺陷车辆扭矩信息进行收集同时满足质量客户端对返工车辆制造过程相关信息进行追溯。
拧紧工艺的工艺流程
基于大数据的车身扭矩拧紧流程主要分为:拧紧、检测、信息传输。螺栓拧紧工艺流程如图7所示。
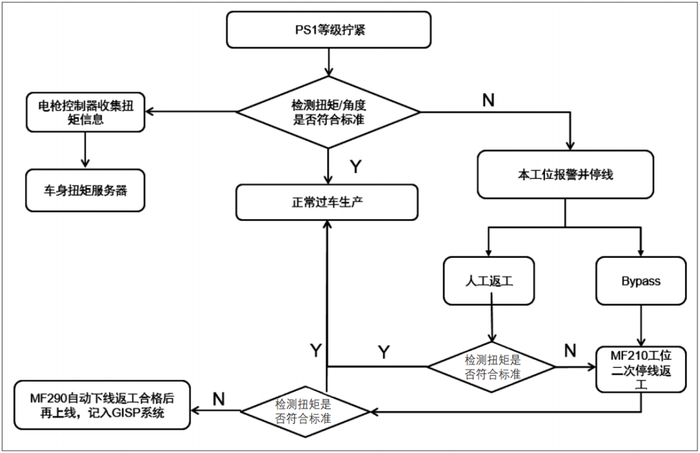
图 7 螺栓拧紧工艺流程
人工或机器人拧紧螺栓后,扭矩控制器自动检测终紧扭矩及终紧角度。扭矩及角度检测合格后正常生产,如检测不合格扭矩控制器反馈报警信号至线体PLC,线体停线。
停线后人工在线返工并检测扭矩,如符合标准则正常造车。人工返工后扭矩检测不合格或者Bypass时在后道工位二次停线返工。如二次返工不合格则自动下线返工,同时车辆信息记入质量管理系统。
拧紧枪拧紧完成后,枪控制器在收集拧紧信息同时与PLC传递的车型信息进行匹配后通过IT生产网络上传至车身车间内部扭矩服务器。车间内部扭矩服务器将数据进行编码转换后上传至云端大数据平台。
车身车间扭矩工程师通过客户端访问扭矩服务器进行设备管理、工艺监控及扭矩分析。
扭矩控制流程
根据PFMEA中评估的潜在失效模式及后果,可将扭矩控制等级划分为不同等级。第一类是扭矩失效后影响人员安全;第二类是扭矩失效后非直接影响人员安全或功能丧失,但违反有关政府法规;第三类是扭矩失效后不影响人员安全和功能丧失,但是会引起用户强烈的抱怨;根据划分失效等级不同,对应控制措施及要求不同。
产品工程师在项目初期发布动态扭矩、初始静态扭矩及扭矩控制等级,项目工程师根据产品释放的扭矩信息发布试生产扭矩标准及制定相应控制措施。车身车间在试生产阶段对已发布的试生产扭矩进行验证,并根据SPC统计方法,收集并计算静态扭矩的上下限及名义值。在车型量产时根据计算的静态扭矩值由项目工程师发布量产扭矩标准,发布的量产扭矩标准需经过项目、工厂及质量部等会签生效。
在日常生产中由于产品变更、工具维修、工具更换等造成静态扭矩变化。车身车间扭矩工程师需对静态扭矩进行分析并组织项目工程师、质量工程师进行会签,并由项目工程师更新扭矩标准。除因产品变化而重新释放,其他情况下动态扭矩一般不会发生变化。
车身车间应定期对拧紧工具进行能力验证。验证结果应达到规定要求,当工具验证不合格时需更换工具,并重新验证新工具动态扭矩及静态扭矩。
总结
本文对现代化工厂车身扭矩控制方式进行了研究。介绍了车身拧紧系统架构以及基于大数据平台的车身扭矩控制方式。通过大数据平台可实现车身车间内部拧紧设备在线管理,车身扭矩在线监控、分析。基于大数据平台的车身扭矩控制方式可大幅提高工厂管理水平,提升整车质量保证能力。
评论 0
正在获取数据......