近年来,新能源汽车在整个汽车市场占有率上一直呈快速上升的态势,未来一段时间内仍将进一步提速。
目前的新能源汽车用户在使用中的主要痛点还是在于“里程焦虑”。为了应对这一痛点,行业内主要在动力电池能量密度以及电池容量两个方面上进行研发和探索。不过在动力电池能量密度无法短期内迅速提升的情况下,进一步增大电池容量是当前比较直接且见效快的方案,被行业内广泛采用。因此,设计更大尺寸的动力电池,并且能够在汽车底部布置下大尺寸的动力电池,是比较主流的方案。
传统底盘工艺装配线的瓶颈
随着目前车载动力电池尺寸逐渐增大,整车制造工厂中动力电池的装配挑战在不断上升。而在整车制造生产线中,对负责进行动力电池装配的工艺线体——底盘工艺装配线,主要面临共线生产问题。整车总装的工艺线体,需要考虑新能源车与传统燃油汽车共线生产的问题。传统燃油汽车仍然在市场上占据较大比例,当前阶段还无法全部切换到新能源车型,特别是对于一些老工厂,共线的压力比较大。在共线情况下,涉及传统燃油车制造策略和新能源车制造策略的兼容。为了给动力电池留出更大的独立空间和预留快换电池功能的操作空间,目前我们把制造策略孔从传统燃油车仅在地板总成上扩展到新能源车的地板总成加上外门槛兼有。车辆在底盘工艺装配线时,传统燃油车仍靠地板总成上的制造策略孔定位,新能源车则由外门槛策略孔定位替代。这种新策略针对性比较强,对于动力电池装配释放了充足的空间。不过如何实现两种制造策略在底盘输送吊具上的共存,是传统底盘工艺线目前遇到的瓶颈。
设备瓶颈的解决方案
考虑到同时存在两种制造策略共线生产,因此底盘输送吊具需要一个适应两个制造策略孔布置位置的方案。目前,我们将底盘输送吊具改造成具有切换功能的新形式吊具,底盘吊具切换方案的对比具体可见表1。
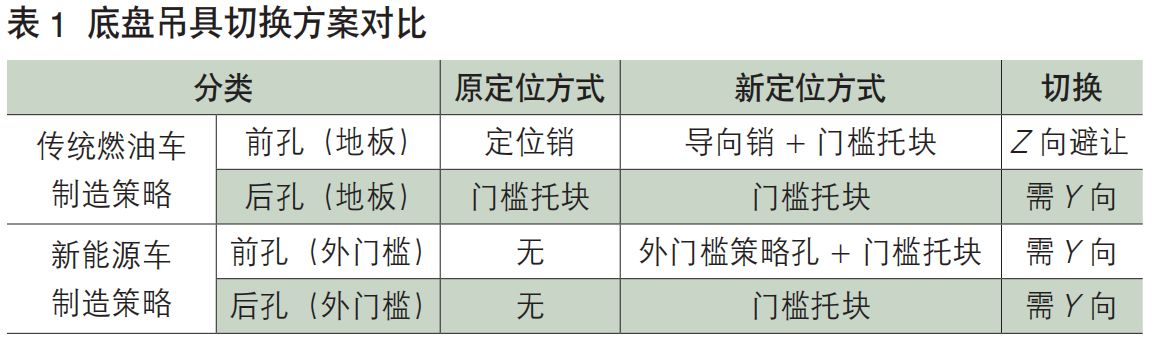
整线布置上,在底盘输送吊具接车的工位前,布置吊具切换站,实现不同制造策略孔的切换共存。在吊具切换站,上位系统将生产队列车型信息导入,控制系统指挥切换站完成对底盘吊具的解锁、切换和上锁三个动作,并完成到位检测。整个切换在“机器思考”下完成,实现“人脑分析判断+机器生产制造”转变为“机器分析判断+机器生产制造”的工业4.0目标的方式,切换后的底盘吊具,进入接车工位,随后走完整条底盘线并返回,在切换站前,等待切换下一循环的车型位置。
根据新定位方式,可以发现除传统燃油车前制造策略孔可以通过Z向高度重新分配实现避让外,其他都需要做切换功能。因为不同车型按照平台的不同、销售目标人群不同等因素,车辆的设计宽度会做改变,导致外门槛位置也会随之相应调整。根据对现有车型平台架构的梳理,并与研发总院的同事交流后,把左右外门槛策略销孔的Y向间距作为划分参数,并对这项Y向间距参数做了系列化。将目前在产和预计投产的中型车,也是车型最多的品种,系列化成Y向1520mm间距、1580mm间距。在这基础上,向上扩展了适应中大型车型的Y向1620mm间距以及适应大型车型的1660mm间距;向下扩展了适应中小型车型的Y向1470mm间距。底盘吊具及切换单元机构式样示意如图1所示。
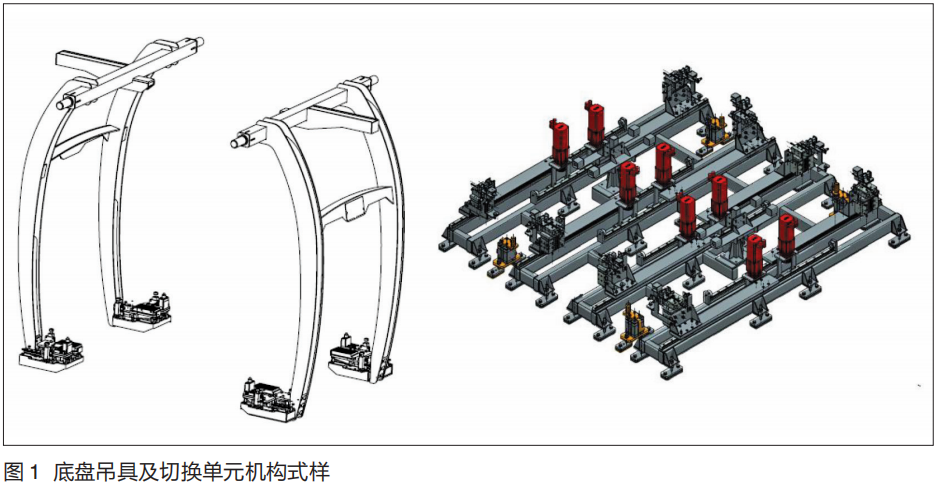
设备的过程能力指数
所有的产品都是过程的结果。统计过程控制就是根据产品质量的统计观点,运用数理统计的方法对生产制造过程的数据加以收集、整理和分析,从而了解、预测和监控过程的运行状态和水平。过程控制是指为实现产品生产过程质量而进行的有组织、有系统的过程管理活动。其目的在于为生产合格产品创造有利的生产条件和环境,从根本上预防和减少不合格品的产生。1931年,学术领导人休哈特(WalterA.Shewhart)出版了他的代表作:《加工产品质量的经济控制》(EconomicalControlofQualityofManufacturedProducts),标志着统计过程控制时代的开始。统计过程控制(StatisticalProcessControl,SPC)是应用统计技术对过程中的各个阶段进行评估与监控,建立并保持过程处于可接受的并且稳定的水平,从而保证产品与服务符合规定的要求的一种质量管理技术。
本次研究的目标设备是切换站和吊具切换机构。切换方案在N基地总装车间首次应用时,有三个前提条件需要一一对应满足。首先,需要实现已经在产的传统燃油车型和实施了新能源车型新制造策略的车型。其次,需要实现按新型制造策略设计的新款新能源车型的导入。再次,通过具有Y向切换能力的多档位托块以及外门槛销座,实现该车型Y向外门槛策略孔1580mm间距档位的适应。同步基于此方案,设计完成了吊具切换机构的设计,使用共四组伺服电动机及齿轮齿条驱动,分别实现前托块Y向多档位切换功能、前外门槛策略销多档位切换功能、后托块Y向多档位切换功能。
切换站和吊具切换机构在完成设计并安装到现场后,经过了各项测试与调试工作,运行逐步稳定。当切换设备处于稳态后,我们统计了每日该切换机构的切换成功次数,按每日来分组。每天的生产计划量基本是一致的,但是切换机构的使用,并不是每过一次底盘吊具就必须切换。整个切换机构通过读取生产队列,系统只有在底盘吊具前次生产车型与当次生产车型不一致时,才启动切换功能,将当次生产车型所需底盘吊具状态调整完成。所以,每天总的切换次数,将会因为生产队列的变化,产生每天不等的切换站使用次数。
综合切换机构的以上运行特点,并查询国家推荐标准《GB/T4091-2001常规控制图》(已被标准GB/T17989.2-2020替代,本文仍采用旧标准),在该机构进入稳态后,我们计划使用不相等样本量的过程能力指数来尝试评估该切换机构的能力。根据国家推荐标准《GB/T4091-2001常规控制图》,p图是控制过程的不合格品率的控制图。p图的统计基础是二项分布。在整个切换单元机构的调试过程中,我们按天统计底盘吊具切换次数作为检验数量,通过统计的不成功次数的情况,来识别整个切换单元机构的功能是否可控或者可满足要求。根据国家标准的定义,p控制图的界限为:
根据现场的统计数据,分别计算值,随后确定上控制限UCL和下控制限LCL。对切换机构每生产日切换次数和切换不成功数的统计表见表2。使用Minitab软件计算后,得出该切换机构切换过程的不成功次数均值为p=0.00144,并得到p控制图如图2所示。此时,通过查询Cpk不合格率换算表,得到该切换机构的过程能力指数Cpk=1.45。查过程能力评价表,属于Ⅱ级1.33≤Cpk﹤1.67,过程能力充分,应继续维持。因此,该切换机构可以继续投入生产使用状态。
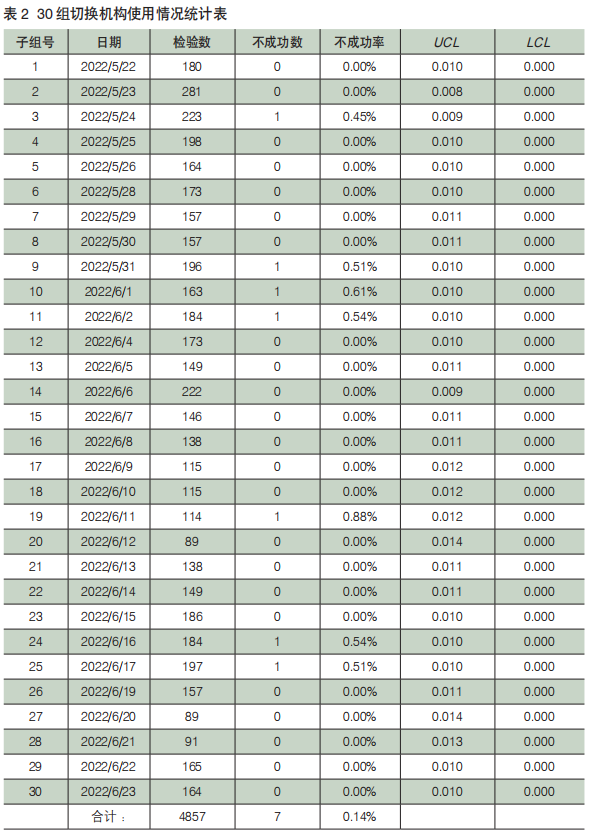
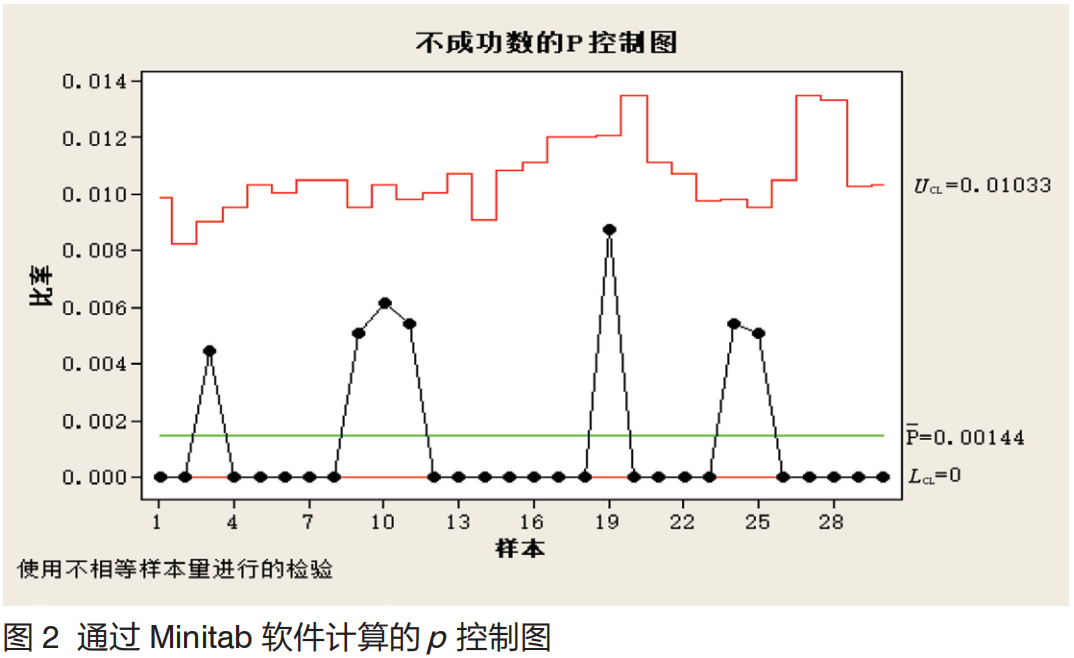
结论
整个切换方案在N基地的试用中,初步实现了底盘工艺线上同时生产传统燃油汽车制造策略和新能源新架构制造策略的共线兼容问题,证明切换方案是具备可实践性的。在切换机构处于稳态后,过程能力指数Cpk位于Ⅱ级,过程能力充分状态。在此基础上,未来N基地可以进一步导入满足制造策略的车型,逐步实现从传统燃油汽车制造策略向新能源汽车制造策略的平稳过渡。整个切换机构通过“机器思考”的叠加,具备了自我查询、自我控制、自我检查及自我纠正的能力,是“工业4.0”目标下的一个验证场景。
评论
加载更多