由汽车业发展现状可知,节能减排是大势所趋。在燃油消耗量日益增加的当下,要想抢占市场份额,从事汽车制造及相关工作的企业必然将燃油设计、轻量化设计提上日程,在确保汽车功能不被影响的前提下,通过减轻部件质量的方式,避免燃油被大量消耗。只有落实轻量化设计,才能推动汽车业朝着持续发展的方向前进,由此可见,本文所讨论内容有突出的社会价值。
1 底盘悬架概述
底盘悬架是弹性连接车轮和承载系统的装置,其作用不仅有衰减振动、传递载荷,还有缓和冲击,另外,对处于行驶状态的汽车而言,底盘悬架往往可用来调节车身位置,避免安全事故出现。
现将其核心功能概括如下:①向车架传递车轮受路面作用所产生应力,如支承力、制动力、驱动力和侧向反力,当然,上述应力带来的力矩同样经由底盘悬架向车架进行传递,这点易被忽视;②缓冲并吸收不平路面给行驶中汽车带来的冲击、振动,为车载货物的安全性提供保证,乘坐体验也会得到一定程度优化;③确保车轮和车身的关系始终满足动态几何特征,具体来说,就是车轮按照特定规律跳动,车身自然可以按照预期轨迹运动。
现有汽车的底盘悬架,以非独立悬架较为常见,该悬架主要分为两部分,由稳定杆、减振器等部件组成的前悬架以及由缓冲块、平衡轴等部件构成的后悬架,其中,后悬架结构以平衡结构为主。
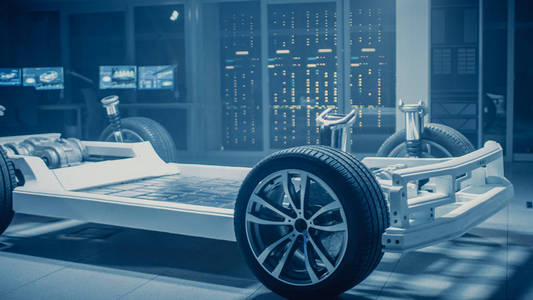
2 轻量化设计探究
2.1 优化策略
要想使底盘悬梁达到轻量化设计所提出的要求,有关人员应着重考虑结构、工艺及材料的优化,以下将逐一对其进行介绍,希望能够给人以启发。
2.1.1 结构优化
对于底盘悬架而言,结构优化既能够实现轻量化设计目标,又可使零件质量与成本处于平衡状态。在计算机技术渗透到各行各业的当下,利用计算机对结构进行仿真设计和优化成为大势所趋。随着尺寸优化及形状优化手段被引入,汽车业可在成本维持不变的前提下,尽量降低结构质量。经由CAE 确定材料密度分布优化方向,得出符合扭力梁主体需求的方案,通过对尺寸加以优化,掌握结构、管梁厚度的最佳参数,可使汽车质量显著降低,这也是轻量化设计被提出的初衷。
2.1.2 工艺优化
要想使轻质材料得到广泛运用,其前提不仅是保证产品可靠且稳定,对制造工艺进行优化也很有必要。例如,由于不同部件需要达到的承载力、功能结构要求通常有显著差异,只有运用不同工艺,完成设计输入的相关工作,才能避免不必要问题出现。对铝合金部件而言,工艺优化方向可被概括为:以现有工艺为依托,同步开发零件承载力与结合方案,确保设计工艺优势均可得到充分发挥,由此而获得设计方案,自然可使行业要求得到最大程度满足[2]。
2.1.3 材料优化
设计底盘悬架部件时,“出镜率”较高的方法是运用轻质材料,该法拥有良好的发展前景,这是因为其既能为汽车运行的可靠性提供保证,还可使底盘质量减小。在合金制造技术趋于完善的当下,以铝合金、高强度钢为代表的诸多材料,均已被用来制造汽车,冲焊零件固有优势通常可因此而得到充分发挥。例如,在对B 级汽车进行设计时,有关人员选择运用铝合金制造控制臂及副车架,汽车质量降低幅度明显,与此同时,底盘悬架功能的实现并未受到影响。由此可见,对中端和低端汽车而言,材料优化是轻量化设计的关键
2.2 设计方法
2.2.1 集成设计
要想使汽车业具备实现持续发展目标的前提条件,将产品质量提升到更高水平,前提是对设计方案加以调整,现阶段,橡胶悬架、空气悬架均已得到推广,二者的优势主要是以悬架承载力达到行业要求为前提,通过对质量进行大幅降低,将制造成本控制在合理范围内。上述提到的橡胶悬架,强调用橡胶弹簧替代钢板弹簧,通常由推力杆、均衡梁及橡胶主(副)簧组成,其优势往往表现在三个方面,分别是无需维护、舒适性能佳、满足轻量化要求。在落实轻量化设计的相关工作时,有关人员往往将集成设计作为首选方案,通过细化分工的方式,使部件拥有更为理想的兼容性及实用性。在传统观念里,兼用性并非细化分工需要考虑的部分,因此,多数汽车的底盘部件均有明显界限,其中,界限最为分明的部件主要是前纵梁和弹簧支架,即便空间分布十分紧凑,仍然无法达到轻量化要求[3]。而引入集成设计理念,通常可使上述问题迎刃而解,有关人员以零件集成应用为切入点,通过系统优化的方式,获得集成零件。事实证明,这样做可使零件质量得到有效降低,轻量化设计初衷随之实现。
2.2.2 等边界设计
事实证明,将等边界设计用于底盘悬架部件设计,对其质量的降低有突出效果。由底盘部件所用材料表现出的力学特征可知,以等边界条件为前提,参考现有制造工艺,对结构进行优化,通常可使轻量化设计优势得到充分体现。例如,控制臂适用减重方案,强调利用高强度钢材料替代原有材料,通过比对不同车型所用控制臂的方式,确定顺利通过验证的设计方案,随着减重设计得到落实,汽车沿用率往往有所提高。而底盘悬架质量减轻所带来的积极影响还有降低成本和增加效益,这点应当尤为注意。
2.2.3 等应力设计
有关人员考虑到底盘悬架质量与设计效果的关系,遂决定经由等应力设计的方式,在确保底盘悬架有效性的基础上,对其质量进行减轻,通过优化结构、科学分布材料等手段,将强度冗余维持在理想范围内,随着零件位置与结构得到约束,设计效果自然可以达到预期。其中,最应当引起重视的部件是控制臂、转向节。以转向节为例,在对其进行设计时,有关人员将铸铝材料作为首选,在CAE 结构的辅助下,弱化低应力区域并强化高应力区域,确保零件拥有均衡应力,而这样做所带来的积极影响,通常表现为:使提高效果的目标成为现实,均衡的零部件应力为质量降低提供了保证。
2.3 发展方向
2.3.1 引入计算机
在汽车业快速进步的当下,轻量化设计走入人们视野,如何科学选用轻量化材料与技术,确保汽车制造及相关工作得到顺利开展,现已成为亟待解决的问题。由上述内容可知,对铝合金、高强度钢等新型材料加以运用,可使底盘功能得到保证,此外,汽车油耗也会随着质量的降低而降低,这与社会倡导的节能减排理念不谋而合。
信息时代的来临,使计算机技术呈现出迅猛的发展势头,对底盘悬架进行设计时,如果条件允许,有关人员可引入计算机技术,通过辅助设计优化的方式,使零件质量大幅降低,在优化制造效率的基础上,将验证零件需要投入的成本控制在合理范围内,这样做可使产品更具竞争力。由实践经验可知,计算机的运用方向主要有概念设计、方案设计等,具体如下:对概念设计进行拓扑优化,使部件拥有更为理想的空间布置方案及结构;以动力学为切入点,对方案进行设计并优化,确保悬架部件空间与载荷均衡;比对并优化结构,对设计成熟度有显著的提升效果;在汽车进入量产前,运用计算机优化已成型工艺,通常能够赋予产品更为理想的稳定性及工艺性[4]。
2.3.2 控制设计成本
研究表明,要想使汽车制造表现出更为理想的经济效益,既要对底盘悬架进行轻量化设计,还应当以制造成本为依据,通过评估现有方案的方式,确保汽车兼具实用性及经济型。简单来说,就是全方位、多角度衡量技术成本和材料成本,确定符合实际需求的方案,通过推动轻量化发展的方式,为汽车业注入动力,使其拥有更大的影响力和竞争实力。
2.3.3 加大产品开发力度
在开发底盘悬架部件时,有关人员应将轻量化设计作为指导思想,确保该原则贯穿产品制造的各个环节,为产品功能性与安全性提供保证。除此之外,以下内容也需要加以了解:以优化开发全过程为前提,通过建立开发标准,确保悬架及其他部件始终处于均衡状态,随后,结合不同目标所表现出的特征,拟定切实可行的提升方案,通常可取得事半功倍的效果。
3 结论
综上所述,对悬架关键部件进行轻量化设计,其效果能否达到预期,主要取决于两个方面:设计工作是否贯穿制造及验证始终;设计方案是否做到工艺、材料与成本的平衡。只有满足上述要求,才能使设计目标具备达成的条件,在未来一段时间内,上述内容仍然是讨论的重点,有关人员应对此引起重视。
【免责声明】本文摘自网络,版权归原作者所有,仅用于技术分享交流,非商业用途!若有涉侵权等告知,将及时删除,感谢关注!
评论 0
没有更多评论了