0 前言
强制流水与柔性化相结合的生产模式,根据定制 化产品需要,采用流水线固定布局 + 无固定布局,工 位既有固定布置,又有灵活布置,既有定序生产,又 能结合客户需求灵活布置,快速实现。本文基于业内 最新主流规划设计的新能源汽车总装车间,对该生产 模式进行分析与探讨。
1 总装车间的任务
我公司新工厂总装车间负责完成纯电动乘用车的物料准备、车身内饰、底盘装配、整车总装、部分部 件装配、出厂检测和调整、返修及报交等任务。
该车间采用双班工作制度,年工作 250 天,每班 工作 8 h,生产节拍为 45 JPH。
2 工艺设计原则
2.1 规划定位
总装车间的规划定位为高度柔性化,在关键或差 异化工位采用装配岛的方式 , 其余工位采用传统成线 的形式进行装配,同时结合国内外同类型工厂的优点, 采用适合本公司特点的工艺方法和检测技术,在确保 产品质量、提高劳动效率的前提下,以经济性的投资 创造出良好的效益。
2.2 车间内的工段分工
按产品结构特点和工艺要求,总装车间划分为 5 个工段。
1)准备工段:负责各个线物料的分拣和发送。
2)内饰工段:负责车身的内饰装配及相关部件分装。
3)底盘工段:负责整车底盘装配,相应底盘部 件的分装,如电机的分装、前悬架和后悬架、电池 合装。
4)最终工段:负责整车的最后装配、液体加注、 下线前的检查和调整。
5)检测返修工段:负责整车下线后的出厂检测、 调整、故障排除以及产品质量评审等工作。
2.3 车间布置
根据厂区内各车间之间的生产流程关系和总平面 布置,结合总装车间的工艺流程,合理地确定总装车 间的平面布置,使车间物流顺畅,功能分区清晰,且 具有良好的采光通风条件。
2.4 设备选用
在满足生产使用要求和保证产品质量的前提下, 优先选用国产设备,非标准设备的选型和设计尽量具 有通用性或稍经修改就可适应新产品的生产,以满足 多变的市场需求。对国内暂不能提供或不成熟的设备, 为保证产品质量拟进口。本设计方案中拟进口的设备 有:抽真空加注机、组合拧紧机、玻璃涂胶机器人及检 测线等。
3 主要工艺
3.1 工艺布置
为保证车间物流与厂区物流相适应,且便于生产 组织和今后的发展,我们对总装车间进行了如下的平 面布置:生产线采用并列布置,呈东西走向,位于车间 的中部;车间的南侧和西侧分别设置卸货雨棚;各线的 物流区靠近主线布置;整车检测和返修位于车间北侧, 靠近试车跑道。
3.2 主要生产线选型
车身储存线,目前各大同级别车企常用的有平库 和立库。相对于平库,立库具有更多的优势:提高了车 身的排序响应速度,减少了出错率,更易于扩展,柔 性化更高。此次规划中,车身储存线选取的是立库形式。
内饰线采用 AGV 输送形式。AGV 输送线与传统的 滑板线功能类似,但有更多的优势:AGV 可与车型信 息进行绑定,实时知道生产车辆的准确位置,更加信 息化、智能化;可实时调整工艺速度及工位节距,同时 方便有装配质量问题的车辆下线处理,更加灵活、柔 性化;生产线不用做地坑基础,可节约土建施工费用及 缩短项目建设周期;生产线后期线路改造或搬迁,更简 单容易且费用低。该规划中内饰线采用 AGV 输送线, 如图 1 所示。
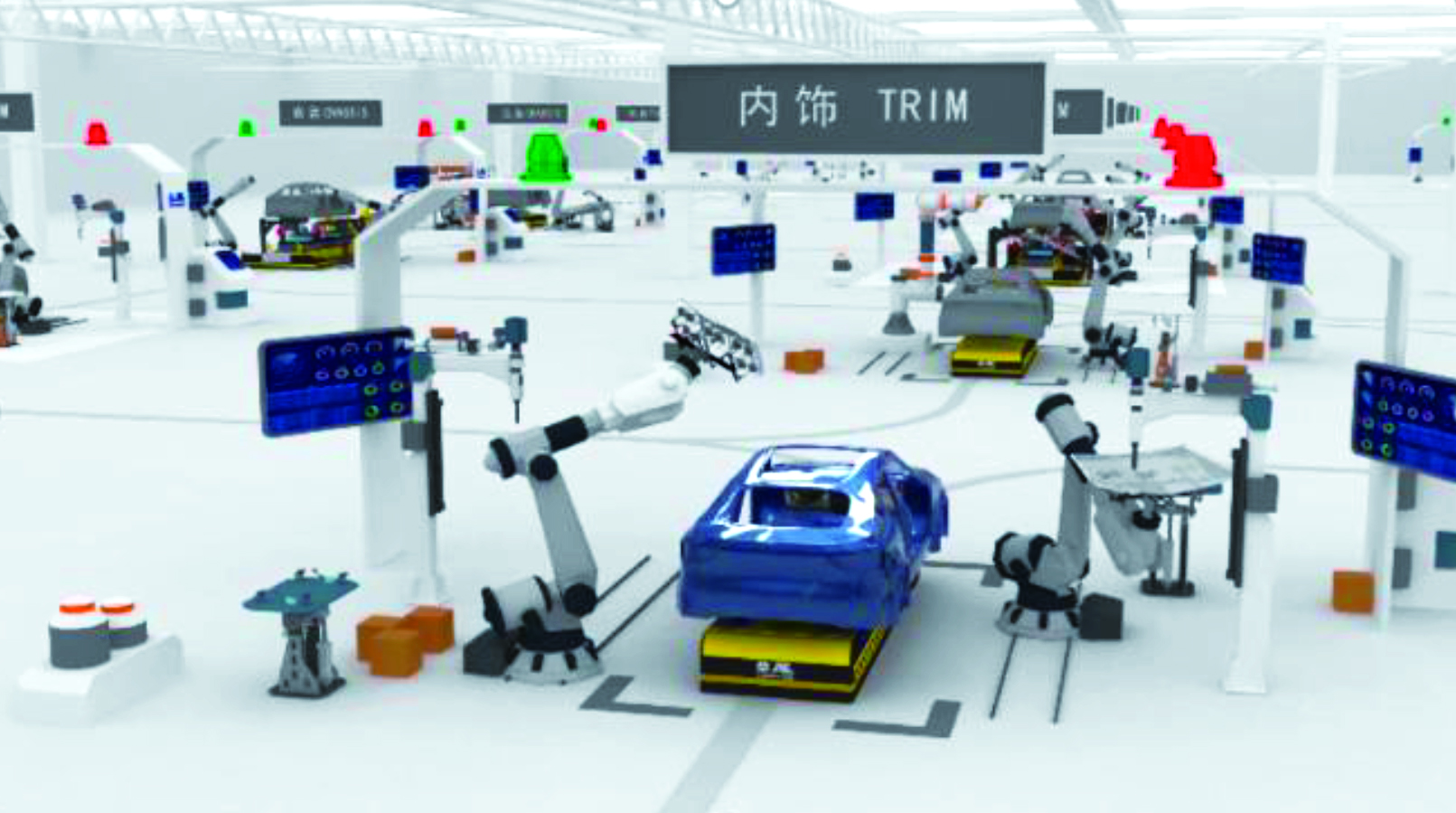
图 1 内饰线(AGV 输送线)
底盘线采用高柔性、可根据车型适配升降高度的 可升降吊具线(EMS+VAC),如图 2 所示。该装配形 式具备卓越的装配人机工程受到业内主机厂的高度推 荐。底盘拼合是整车总装最关键的工序,采用柔性的 EMS+VAC 和 AGV 组合完成,如图 3 所示。
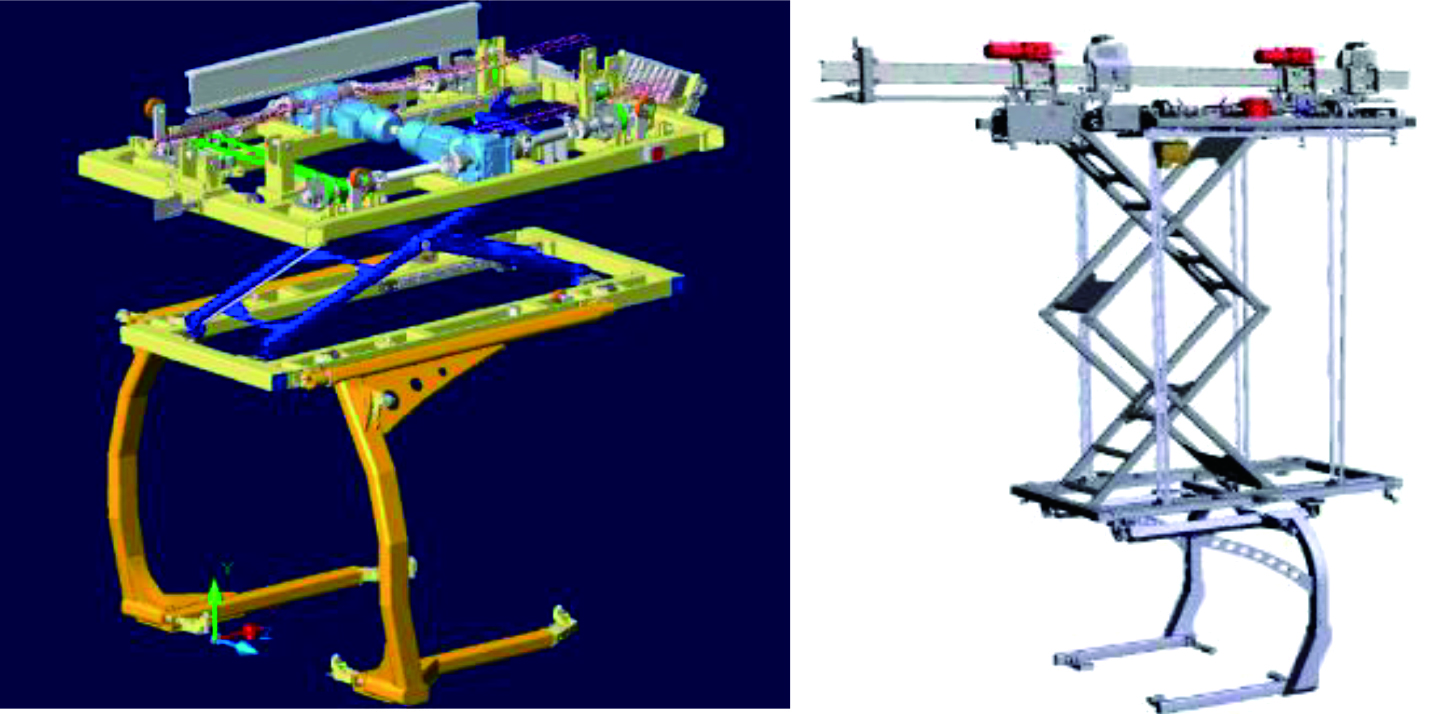
图 2 底盘线(EMS+VAC)
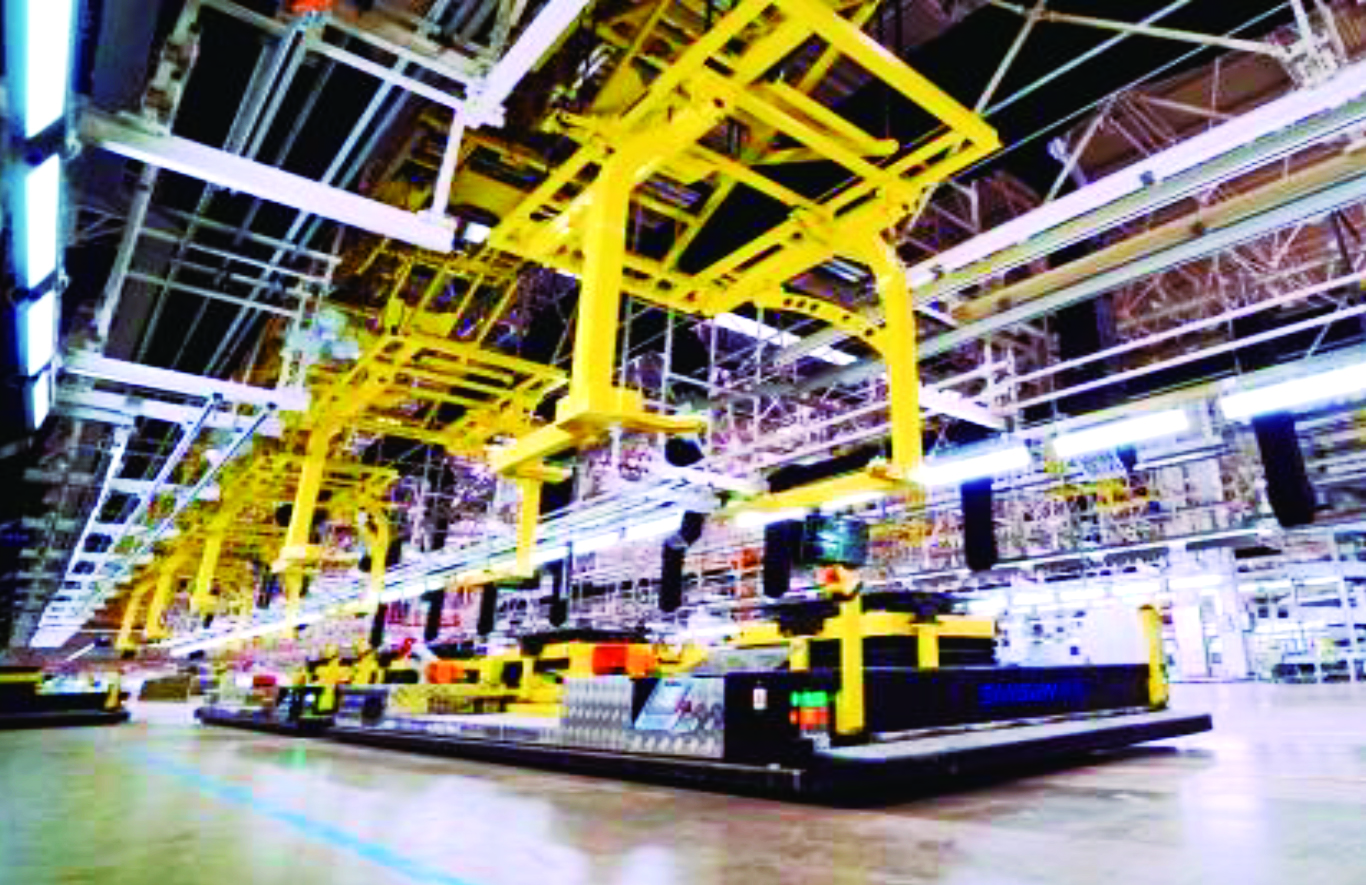
图 3 底盘拼合(EMS+VAC+AGV)
最终线主要负责完成座椅、车门的安装以及液体 加注、下线前的检查和调整,这些工作都是车身外围 的工作,相对于传统的滑板线或者板链线,AGV 输送 线完全可以实现,且更具优势。
检测线主要完成整车功能性及性能性指标参数检 测。比如:四轮定位、侧滑、制动、综合转毂测试及整车密封性测试等,以满足国家相关法规规范。
在关键或差异化工位 , 采用装配岛的方式,主要涉 及车门、风窗玻璃、天幕、侧窗玻璃、座椅和轮胎等装配。
该规划方案中内饰线、底盘线和最终线都采用成 线的形式,与传统强制流水线一致,在各个线中间, 根据关键或者差异化工位需求,穿插一些手动或者自 动装配岛,实现高度柔性化生产需求。这种强制流水 与柔性化相结合的工艺生产模式,根据客户定制化产 品需要,采用流水线固定布局 + 无固定布局,工位既 有固定布置,又有灵活布置,既有定序生产,又能结 合客户需求,灵活布置。
其余分装线、车门线和前后悬分装线等都采用 AGV 线,兼顾效率与柔性,报交线采用塑料板链。
整体规划的主要生产线选型如表所示。
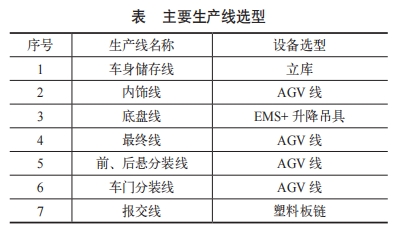
3.3 工艺规划
总装车间工艺流程如图 4 所示。
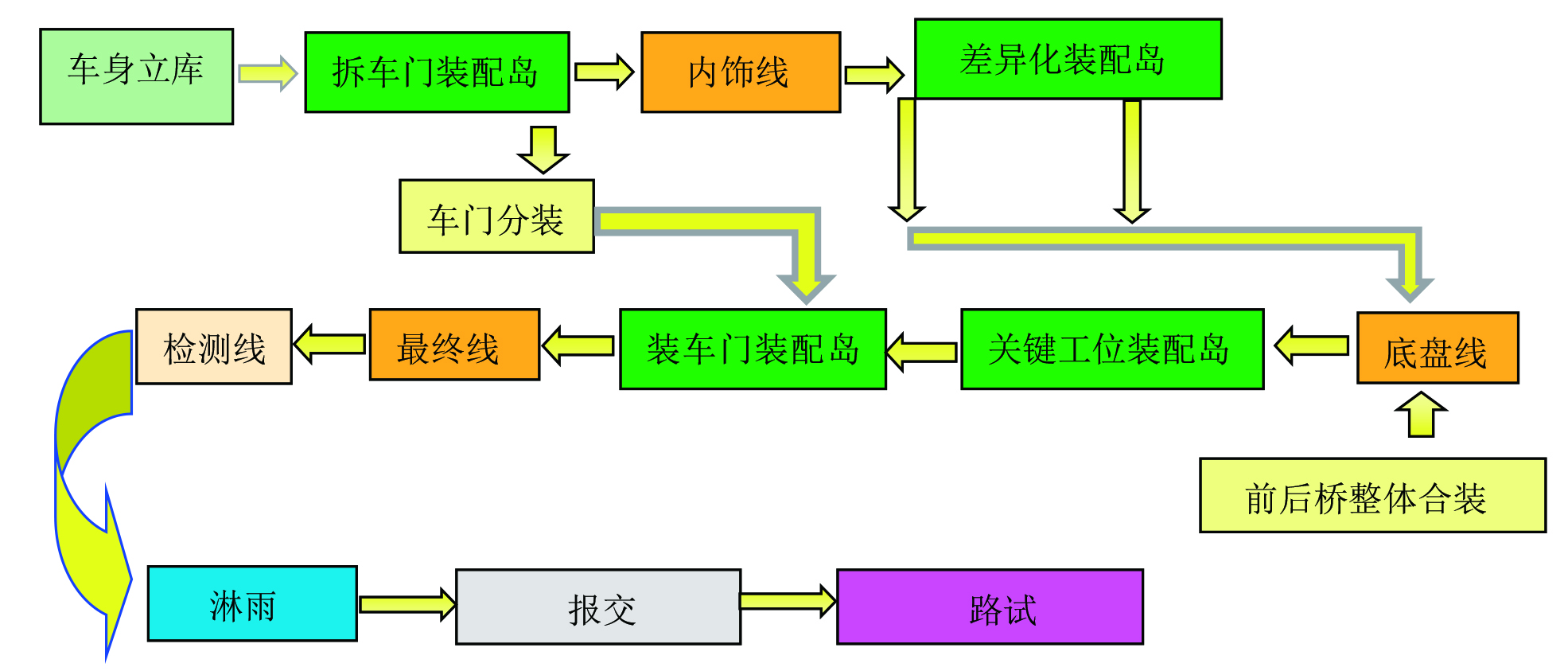
图 4 车间工艺流程
(1)车身从立库通过输送线转运到达总装车间, 在内饰转接工位通过机器人把车身放到内饰 AGV 上。
(2)内饰线采用装配岛 +AGV 线 + 装配岛形式。 在内饰 AGV 线前设置拆车门装配岛,然后是内饰线 AGV,进行内饰通用件的装配,然后进入差异化装配 岛(选装)或直接进入底盘转接工位。通过升降机转 入底盘线,进行底盘装配,内饰线的 AGV 返回到起始 端转接位接下一个车身。
(3)底盘装配采用可升降吊具(EMS+VAC),符 合传统的吊挂方案。底盘合装采用整体 AGV 合装 方式。
(4)最终装配采用装配岛 +AGV 线,完成底盘装 配的整车随吊具进入转接升降机,通过升降机将车身 落到最终线 AGV 上。AGV 带着车身进入车门装配岛, 进行车门装配,然后进入关键工位装配岛,进行轮胎 装配、自动加注等作业,完成自动装配后,进入 AGV 流水线进行最终装配,包括外观检查和调整,最后 下线。
(5)整车下线后进入检测线进行出厂检测,测试 项目包括四轮定位、前照灯、侧滑、转毂(DVT)试验、 制动测试、底盘检查,然后进行整车密封性测试和淋 雨试验,最后通过报交线进行交付性检查。
3.4 物料输送
(1)内饰线、最终线、车门线的物料采用 SPS 小 车配送,物流人员根据生产顺序将每辆车所需的零件 进行分拣、排序,SPS 小车随对应车型一起前进,直 到小车内零件装配完成。该物流输送方式在降低工人 装配强度的同时,也提高了装配效率。
(2)轮胎、座椅、保险杠、仪表板等大件采用AGV 直接输送到工位。
4 结论
本文基于我公司目前规划的新工厂总装车间工艺 需求,对强制流水与柔性化相结合的工艺生产模式进 行了分析。该生产模式相比于传统的强制流水生产 模式,有更好的灵活性,可以更好地适应客户定制 化生产需求,相对于全柔性生产模式,可以兼顾效 率。该生产模式中,内饰线、底盘线、最终线按照传 统的固定成线布置,中间穿插自动装配岛和人工装配 岛,对不同的产品实现差异化装配,以适应多种产品 共线生产需求,该生产模式更加灵活,且具有可拓展性。
本文为“AI汽车制造业”首发,未经授权不得转载。版权所有,转载请联系小编授权(VOGEL100)。本文作者:蔡自凡,单位:云度新能源汽车有限公司上海分公司。责任编辑龚淑娟,责任较对何发。本文转载请注明来源:AI汽车制造业
评论 0
正在获取数据......