0 前言
在双碳政策的影响下,电动汽车在市场的份额逐年增高。随着电动汽车市场保有量的增加,对电动汽车的安全性也提出了更高的要求。目前,主流的电动汽车用动力电池包的成组方式为单体电池—模组—壳体—整包。电池包结构强度必须要满足安全性的要求。
本文以某圆柱铁锂电池为模型,以标准GB38031-2020中对电池进行振动测试的载荷PSD功率谱为计算边界,采用模态叠加法,计算电池壳体结构的强度是否满足要求。
1 随机振动分析
随机振动是在一定的时间范围内,振动信号的幅值和频率是不确定的、随机变化的。汽车在全寿命范围内行驶在不同的路况中,车辆受到来自道路的作用力正是这种随时间变化的杂乱无章的载荷。随机振动的特点是无法通过确定性的数学模型来描述,因此,需要采用统计方法进行分析。
在求解随机振动载荷问题时,一般有两种分析方法:时域法和频域法。时域法中经典的雨流循环计数方法被认为是最准确的方法,但工作量巨大,不适合实际的工程应用;在工程实践中,通常使用频域的谱分析法对结构进行随机振动分析,从应力功率谱密度出发,得到应力幅值的概率密度函数,进而进行随机振动疲劳分析。
功率谱密度是一种概率统计方法,是对随机变量均方值的量度。一般用于随机振动分析,功率谱密度是结构在随机动态载荷激励下响应的统计结果,是一条功率谱密度值-频率值的关系曲线,其中,功率谱密度可以是位移功率谱密度、速度功率谱密度、加速度功率谱密度或力功率谱密度等形式。数学上,功率谱密度值—频率值的关系曲线下的面积就是方差,即响应标准偏差的平方值。随机振动分析可以是单点也可以是多点,在单点随机振动分析时,要求在结构的一个点集上指定一个功率谱密度;在多点随机振动分析时,则要求在模型的不同点集上指定不同的功率谱密度。本文采用单点随机振动分析。
2 电池包随机振动分析
2.1 有限元模型
为了节省计算资源,有限元建模时对整包模型进行了必要的删减,网格模型主要包括下壳体、上盖、等效模组、模组钣金件以及模组拉杆。电池包有限元模型采用CTRIA3(S3)、CQUAD4(S4)、HEX8(C3D8R)单元,网格基本尺寸为2mm;模组采用简易模型,进行配重;焊缝采用壳单元与本体共节点,材料属性为本体的80%;螺栓连接采用刚性连接。电池包网格模型如图1所示。
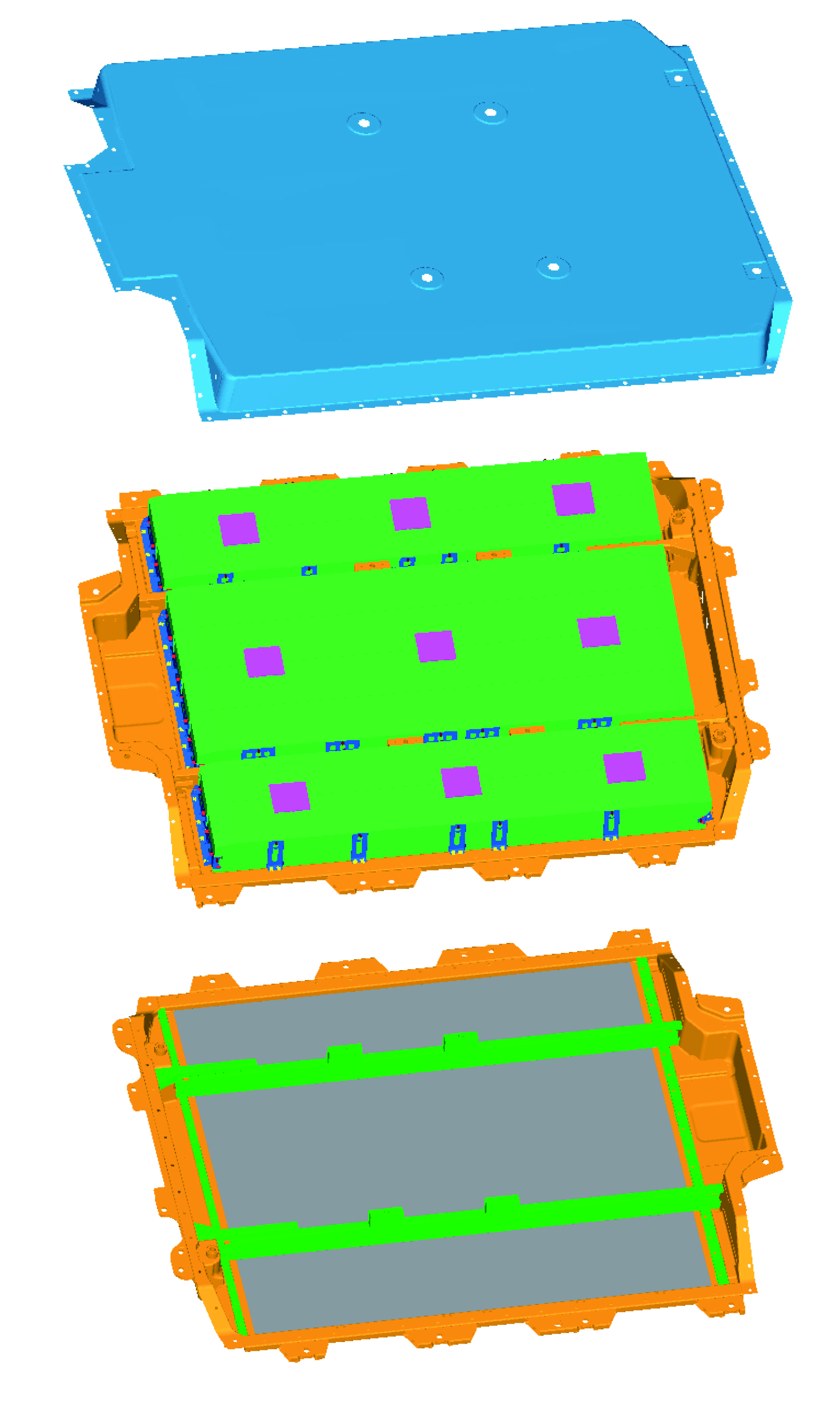
图1 电池包有限元模型
2.2 载荷与约束边界
随机振动分析建立在模态分析基础上,因此,分析设置两个载荷步:一个是模态分析步,一个是随机振动响应分析步。模态求解采用Lanzcos法,模态分析时对电池包与车体安装点进行全约束,随机振动响应分析步在安装点上分别施加Z/Y/X方向的加速度功率谱密度。本文参照GB38031-2020中规定的功率谱密度(PSD),如表1所示。
表1 加速度功率谱密度
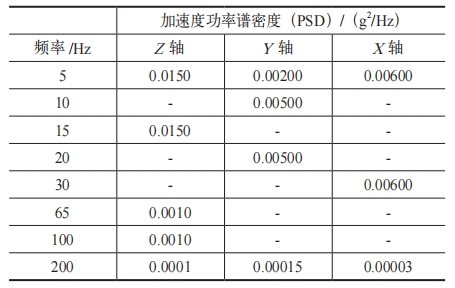
2.3 分析结果
整车坐标系为:X向是车辆前后端;Y向是车辆左右端;Z向是车辆与道路垂直接触端。对于电池包来说,Z方向的道路载荷是引起电池包失效的关键因素,因此,我们在计算时一般先进行Z方向的随机振动分析,如果Z方向结果通过,再进行其他两个方向的计算。如果Z方向不通过,则先优化改进,再重新计算。
电池包前10阶固有频率如表2所示。
表2 电池包前10阶固有频率
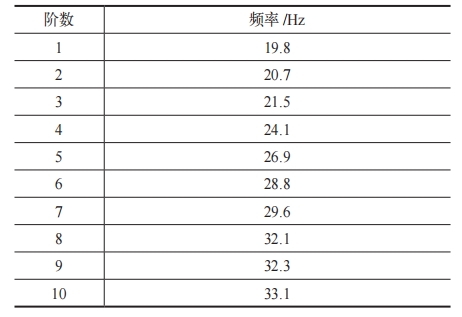
结合结果中的质量参与系数和模态阵型可以得到前10阶模态中,前6阶均为局部模态,第7阶为我们关注的模组第一阶模态,其值为29.6Hz,如图2所示。
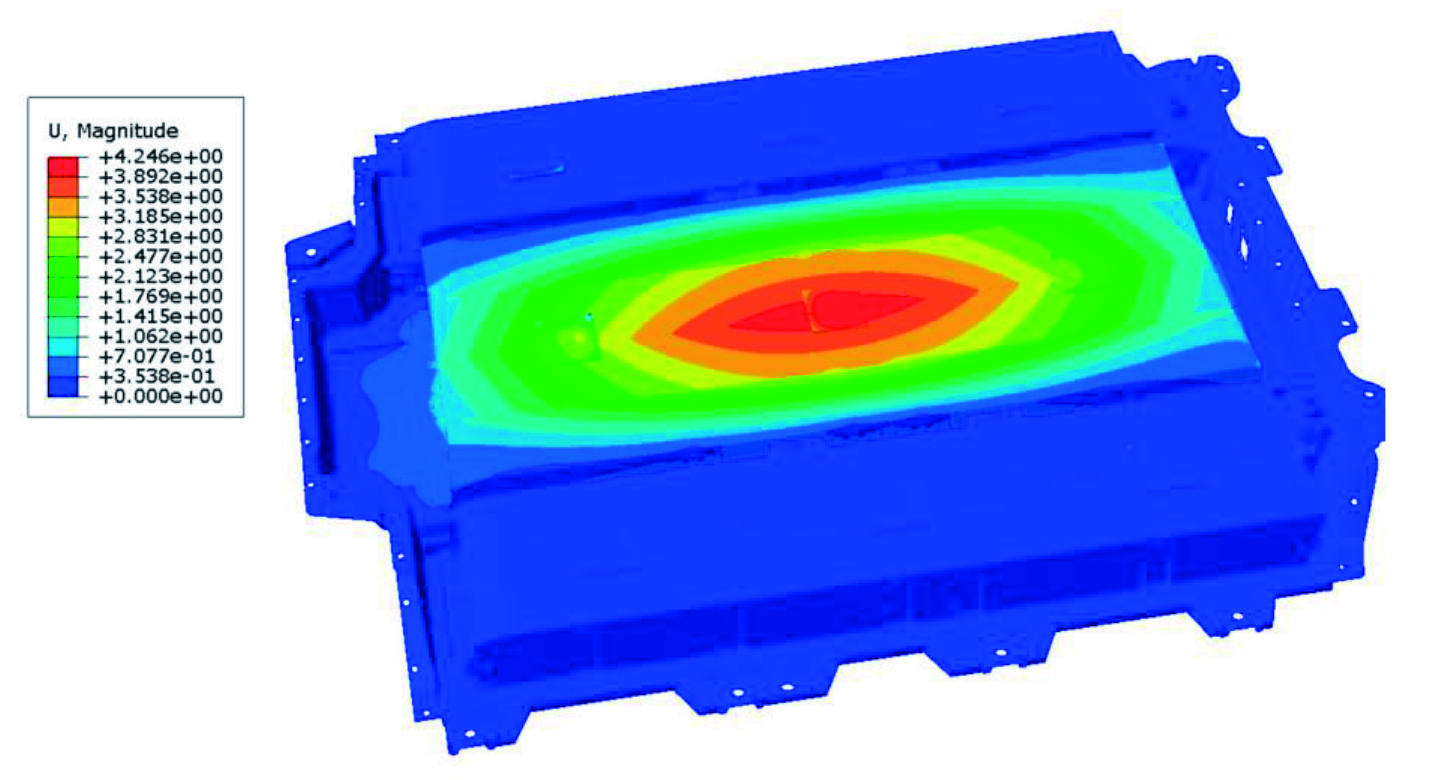
图2 模组第一阶模态振型
在随机振动分析中,我们主要关注电池包上盖、下壳体和模组钣金件的强度。Z方向随机振动工况下,下壳体最大Mises应力为130MPa,钣金件最大Mises应力为118MPa,均超出9σ评价准则规定的极限应力值,在全寿命周期内有失效风险。各部件的应力分布如图3所示。
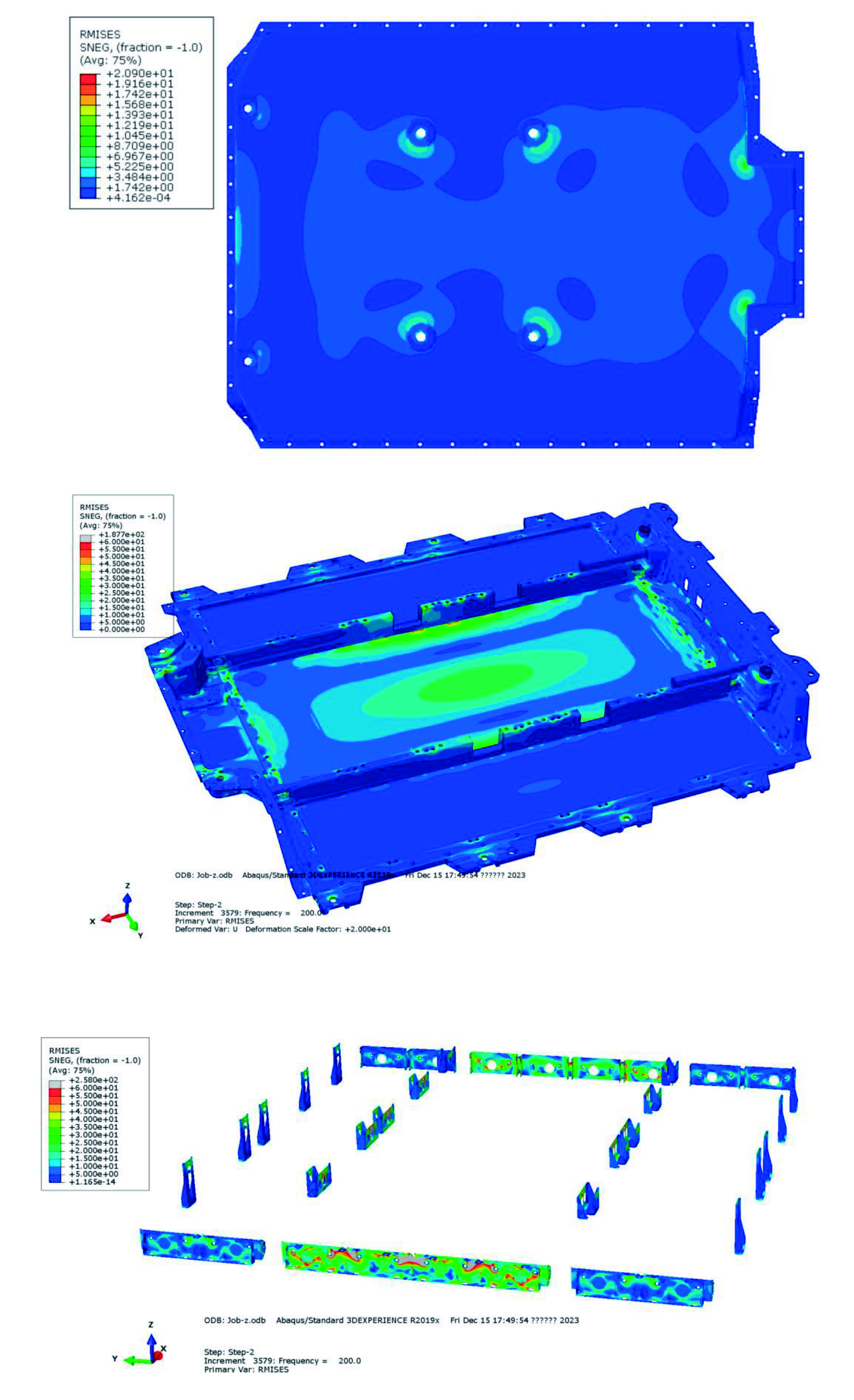
图3 电池包主要结构件应力分布
3 刚度优化
根据设计和试验经验,一般要求乘用车用动力电池包第一阶模态频率要高于35Hz,本模型中模组的第一阶模态频率为29.6Hz,有可能会导致低阶频率共振,需要对电池结构进行刚度提升。
3.1 优化方案的确定
观察模组的第一阶模态振型,模组间的连接主要依靠5根拉杆,且拉杆相对于模组的位置偏上,导致模组整体刚度不够,因此,优化思路主要集中在提升模组的整体刚度上。环氧树脂板具有黏附力强、收缩力强的优点,因此,选择将模组下端胶粘在0.5mm的环氧树脂板上,以达到提高模组刚度的目的,如图4所示。
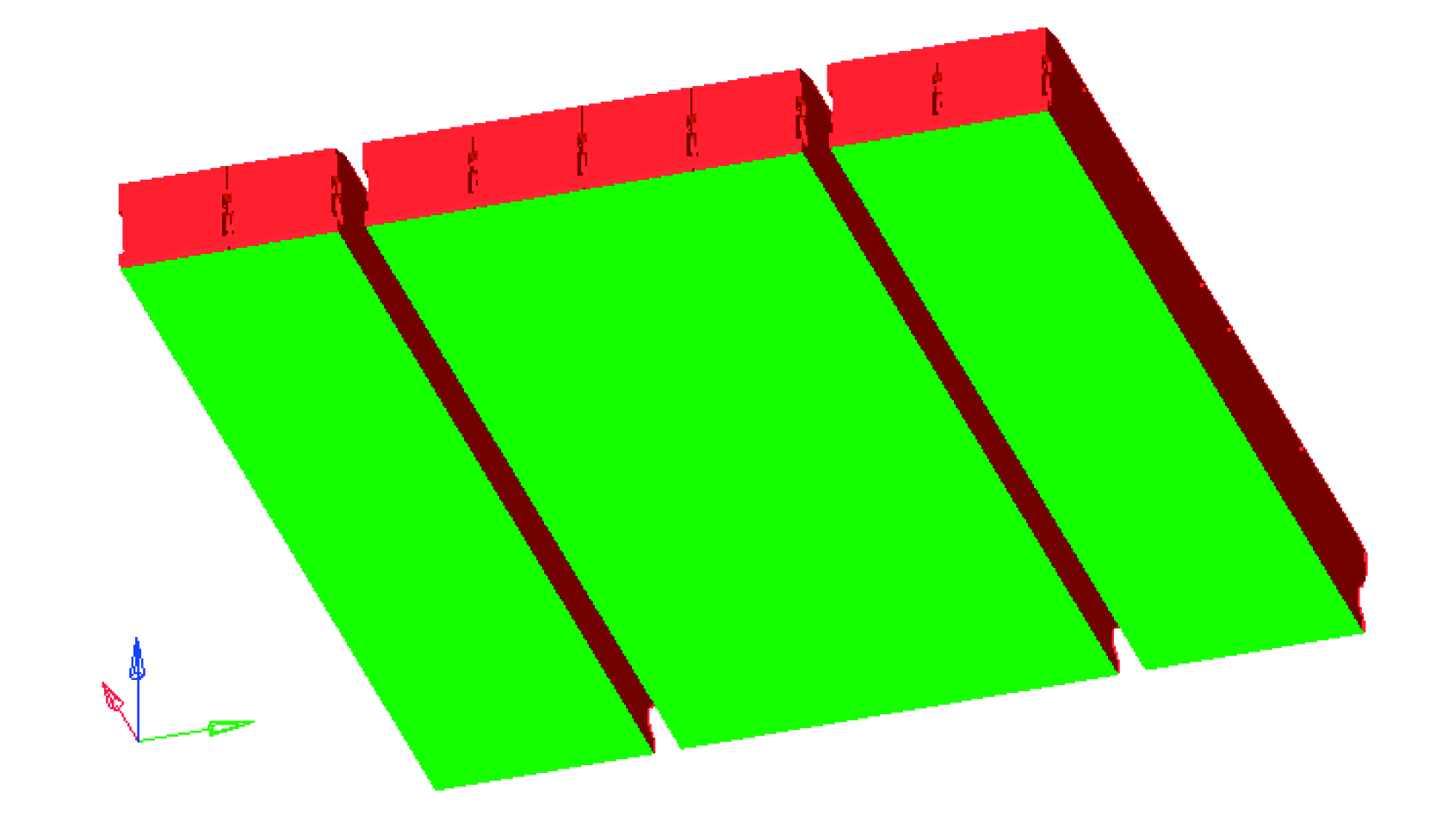
图4 在模组下端胶粘环氧树脂板
3.2 优化结果
优化后模组第一阶频率为55Hz,相较于之前的29.6Hz,频率显著提高,表明优化思路正确合理,如图5所示。
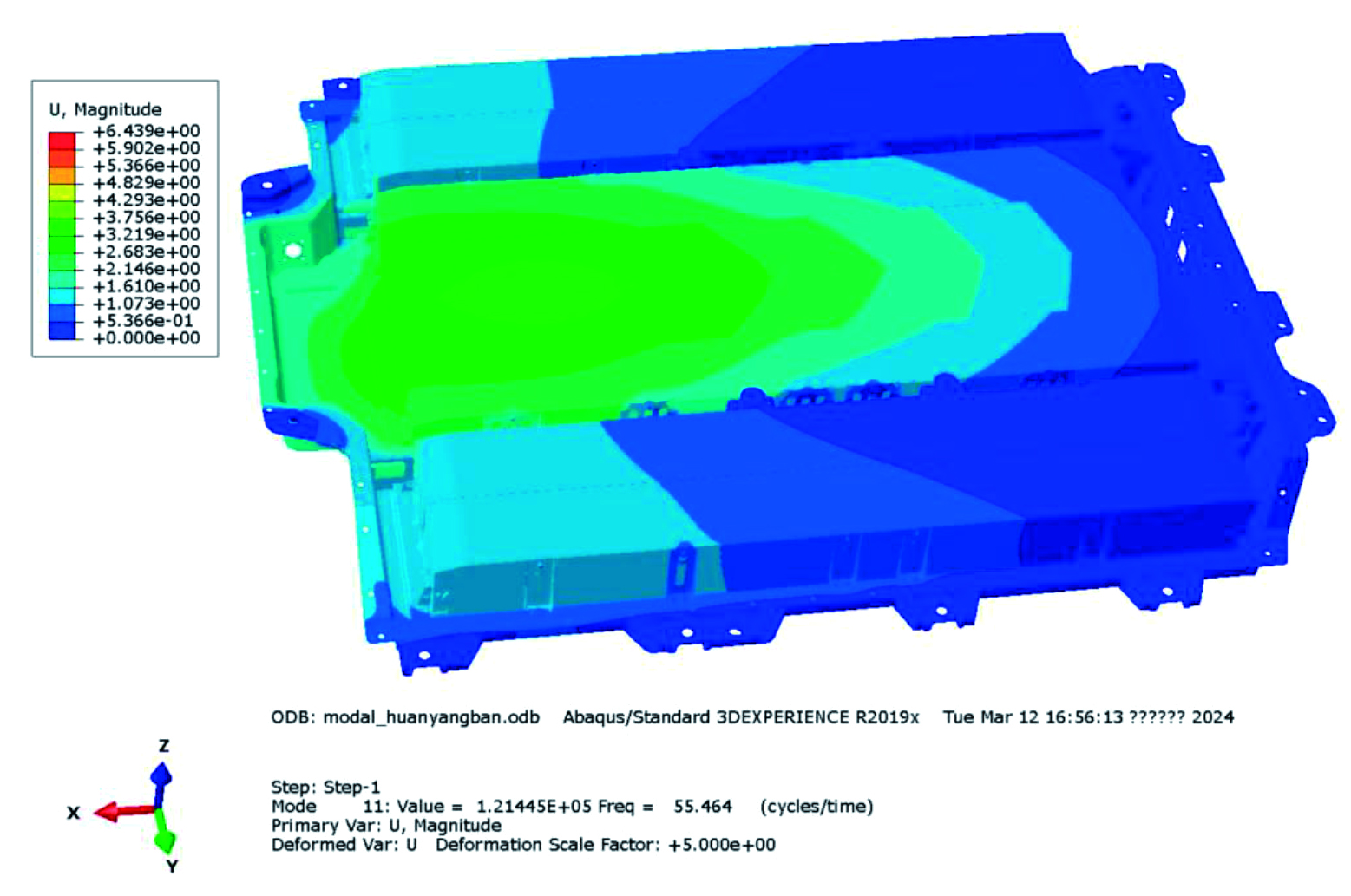
图5 优化后模组第一阶模态振型
优化后Z方向随机振动工况下,下壳体和钣金件的应力显著下降,下壳体最大Mises应力为49MPa,钣金件最大Mises应力为23MPa,符合9σ评价准则,满足强度要求,应力分布如图6所示。
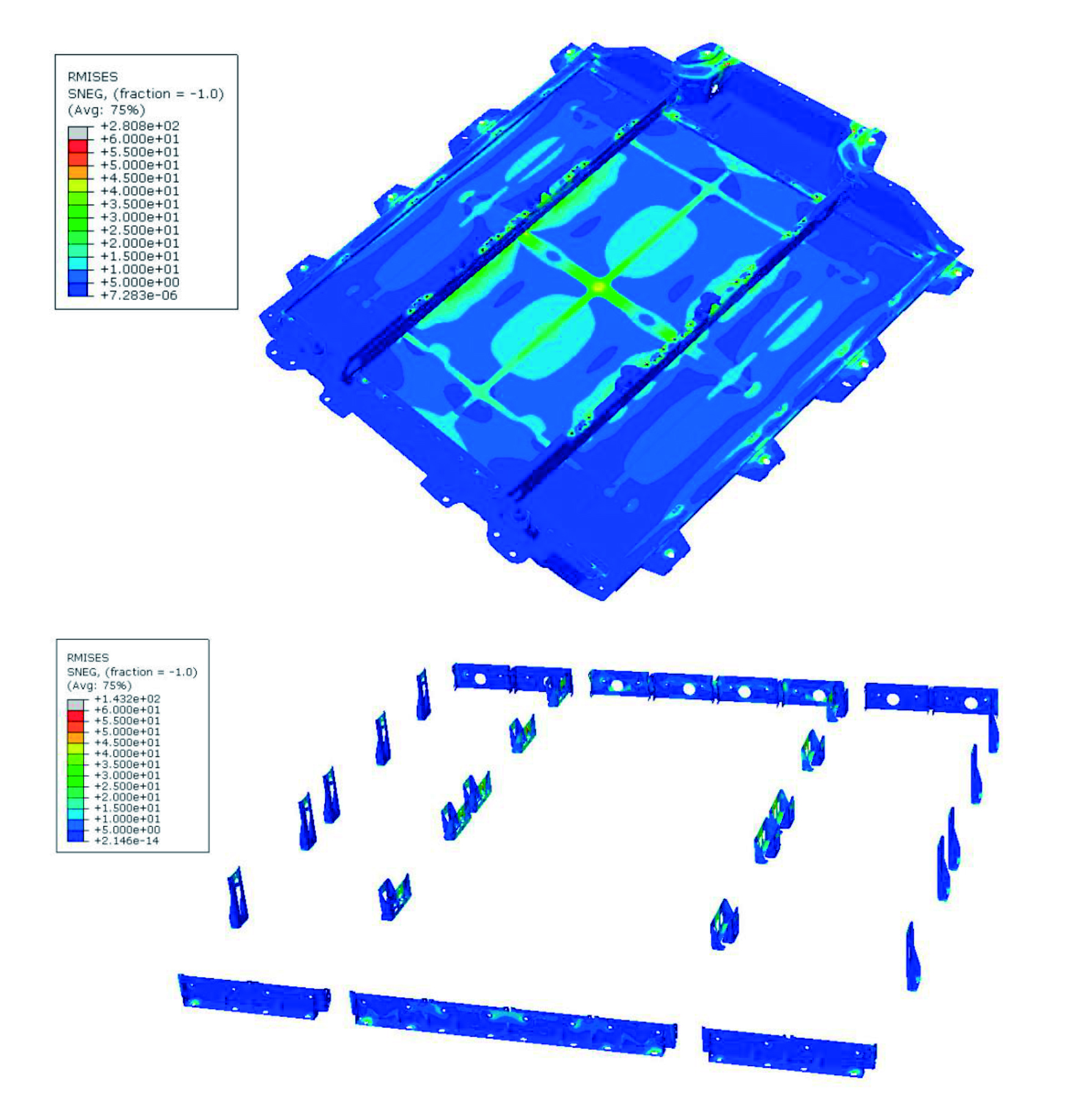
图6 优化后的下壳体和钣金件的应力分布
4 结语
本文对动力电池包进行模态分析和随机振动仿真分析,在初始分析中,模组第一阶频率低,仅有29.6Hz,无法避开车架传递过来的外激励频率,存在低阶共振的危险。通过对模组第一阶模态振型的分析,找到提高模组下端整体性的优化思路,优化后模组第一阶频率显著提高到55Hz,下壳体和钣金件的应力也下降到极限值以下,说明优化思路正确,优化效果明显。
参考文献
[1] 黄晓婷.多轴随机振动频域疲劳方法的研究与应用[D].成都:西南交通大学,2015.
[2] 谭祥军.从这里学NVH:噪声、振动、模态分析的入门与进阶[M].北京:机械工业出版社,2018.
[3]国家市场监督管理总局,国家标准化委员会.电动汽车用动力蓄电池安全要求第8部分电池包或系统安全性试验方法:GB/38031-2020[S].北京:中国标准出版社,2020.
本文为“AI汽车制造业”首发,未经授权不得转载。版权所有,转载请联系小编授权(VOGEL100)。本文作者:昂金凤 刘舒龙 陈康伟 王鹏显 ,单位:安徽江淮汽车股份有限公司 。责任编辑龚淑娟,责任校对何发。本文转载请注明来源:AI汽车制造业
评论 0
正在获取数据......