0 前言
各大汽车主机厂要应对日益严格的环保法规和快速变化的市场需求,同时还要保持产品质量和性能,不断降低整车成本,以保证产品竞争力。制造成本是整车成本的重要一环,直接决定了企业的盈利能力、市场竞争力和未来发展潜力。因此,如何有效降低汽车制造成本一直是汽车制造行业的重要课题。
本文旨在深入探讨降低汽车制造成本的策略及相应的解决方案。通过建立整车设计工时核算系统,对产品从集成化设计、标准件优化、固定点优化、工艺定位优化和新结构工艺优化五个方面进行分析,以期达到降低制造成本的目的。
1 多能源动力汽车共线生产装配成本
据统计,装配工作量占主机厂整个产品制造工作量的20%~70%,平均为45%,装配时间占整个产品制造时间的40%~60%,装配成本占制造成本的30%~50%。装配线上通常人工较多,人员工资已经从2013年的每人10万元/年上涨至2023年的每人20万元/年,装配成本随之逐年上升。
随着汽车技术的发展,各种多动力能源汽车(ICE、HEV、PHEV、SHEV和EV)车型共线生产将逐渐成为汽车行业总装车间的趋势。不同动力能源汽车之间,由于零件数量和设计工时差异大,导致共线生产节拍不平衡的问题越来越突出,产线人员闲忙不均问题严重。
G公司M系列车型,各种动力能源车型混线生产时,整车装配设计工时的总装总岗位数如图1所示。
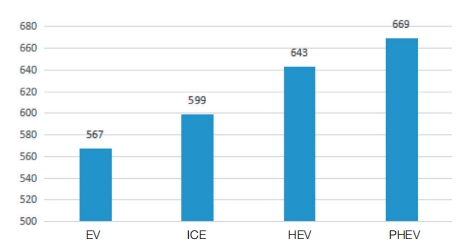
图1 G公司M系列车型总装线总岗位数
EV车型相比PHEV车型,岗位数相差102个,相当于纯电车型基础上增加20%人员作业。折算人工成本,如果EV与PHEV共线生产,混线比例1:1,则浪费人员51人,折合人工工资1020万元/年。产线年产量20万,EV10万台/年,则EV单车制造成本增加约100元/台。
标准工时的概念,很多IE专业人员已经做过完整的分析,如MOST标准工时等。本文着重介绍标准工时内,由产品设计结构确定,在产品开发设计阶段着重考虑的设计工时的削减问题。
2 设计工时核算系统
产品在开发设计阶段,无法进行掐表测算装配工时,需要根据EBOM进行整车设计工时的核算,以确定共线生产时的总工时与现有量产车型工时的差异。平衡整车设计开发成本关系。
某汽车设计研究院,基于产线装配实际生产模型,建立了77种不同装配关系的标准工时库,再创建自动识别程序,根据EBOM,自动区分零件重量、类型以及装配方法,并赋予单件装配工时,从而自动核算整车装配工时,在设计阶段仅根据零件数量和零件类型核算整车设计装配工时。从而建立了各车型统一的设计工时标准,在设计开发阶段就可以核算开发车型的设计工时,科学、合理地制定产线各岗位工时优化目标。
3 设计装配工时优化方案
G公司研究院工艺人员分析了十数款车型的开发设计,认为设计装配工时优化,可以从集成化设计、标准件优化、固定点优化、工艺定位优化及新结构工艺优化这五个方面进行开展。
3.1 集成化设计
集成化设计主要在设计端开始进行管线合件、零件合件等。
(1)管线合件
通过工艺改善及对布置进行约束,减少工艺分段点,实现降本,如图2所示。
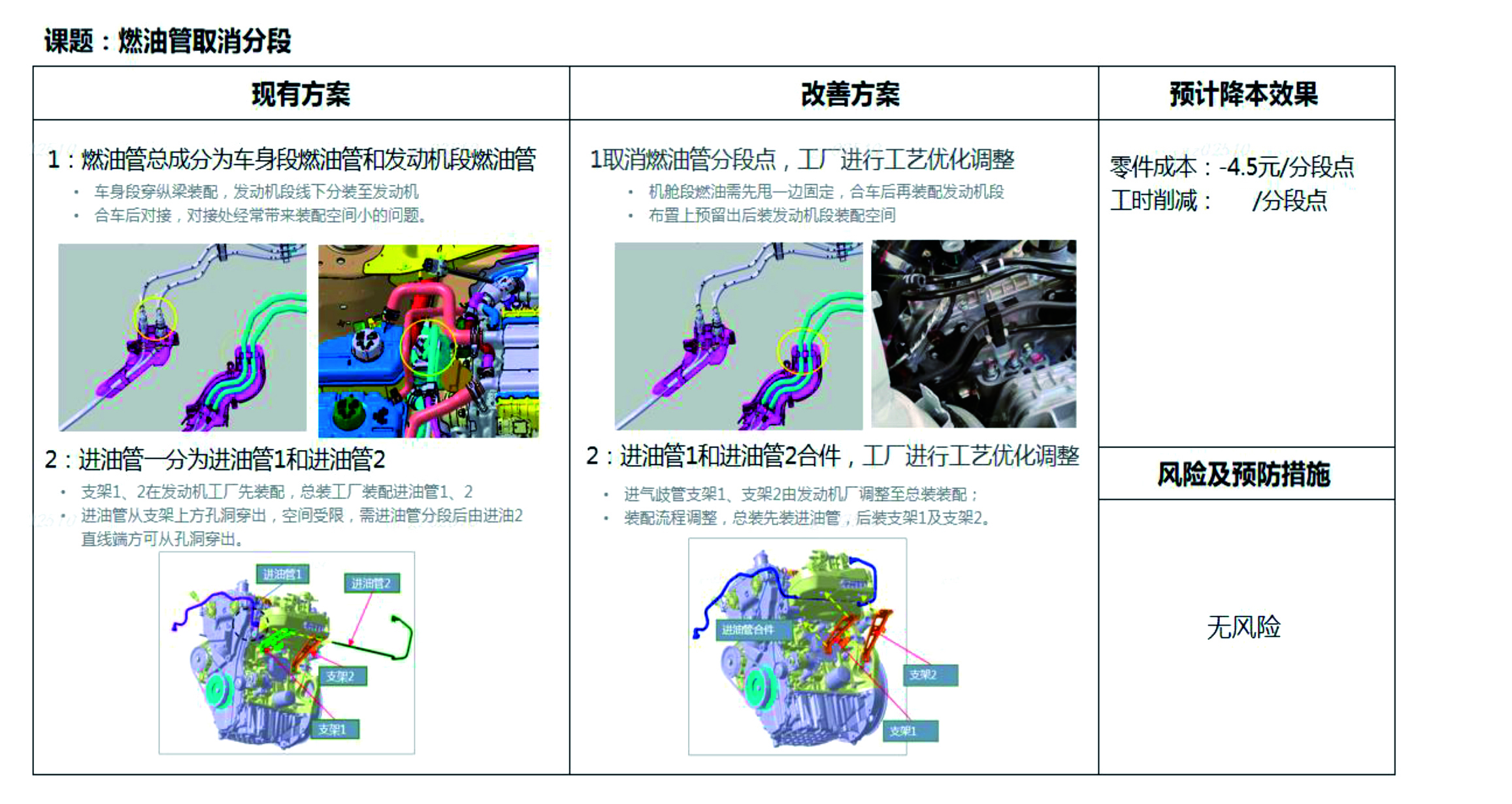
图2空调管取消分段
通过对管线固定点(胶塞)的合并,以实现零件成本降低和装配工时降低,如图3所示。
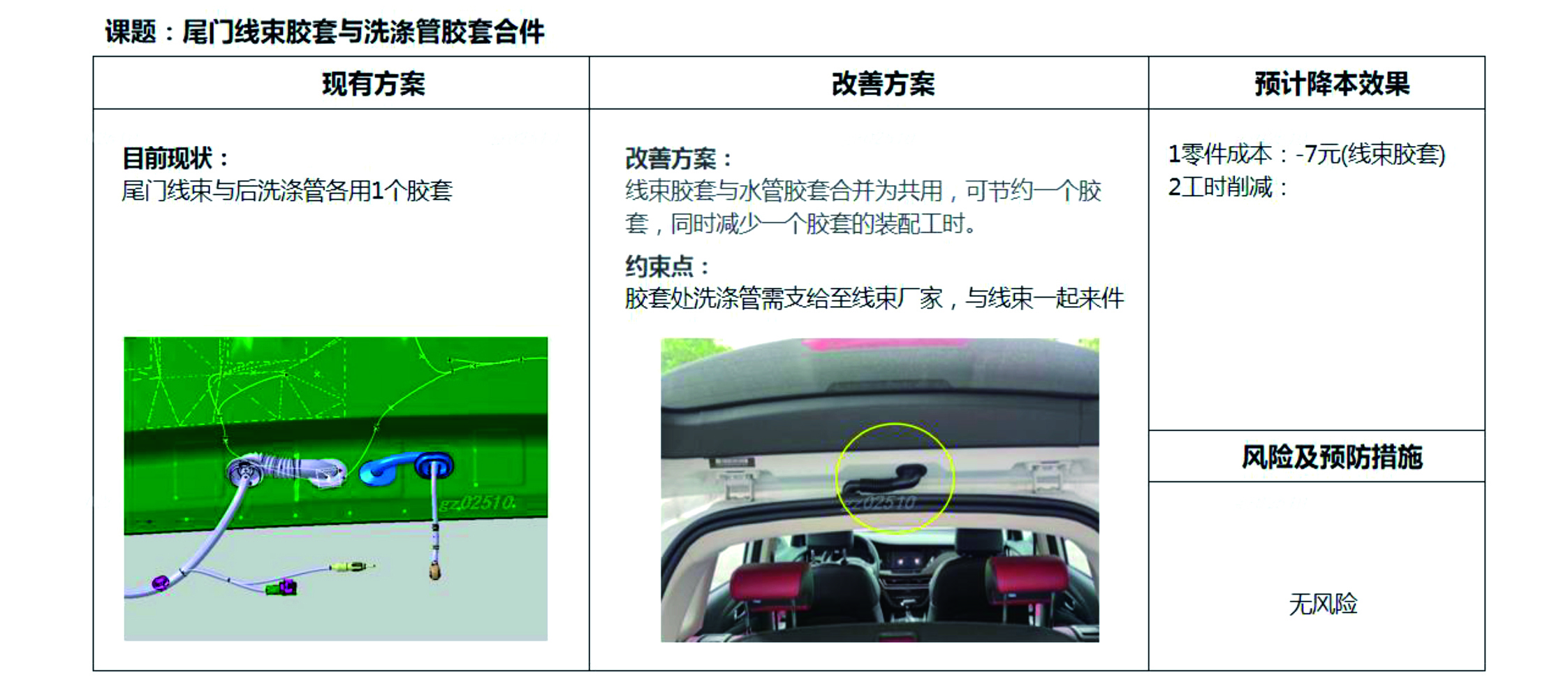
图3水管线束护套合并
(2)零件合件
通过对零件进行合件,以实现零件成本降低和装配工时降低。如A柱下饰板与门槛护板合件,背门饰板合件如图4所示,警示标签合件如图5所示。
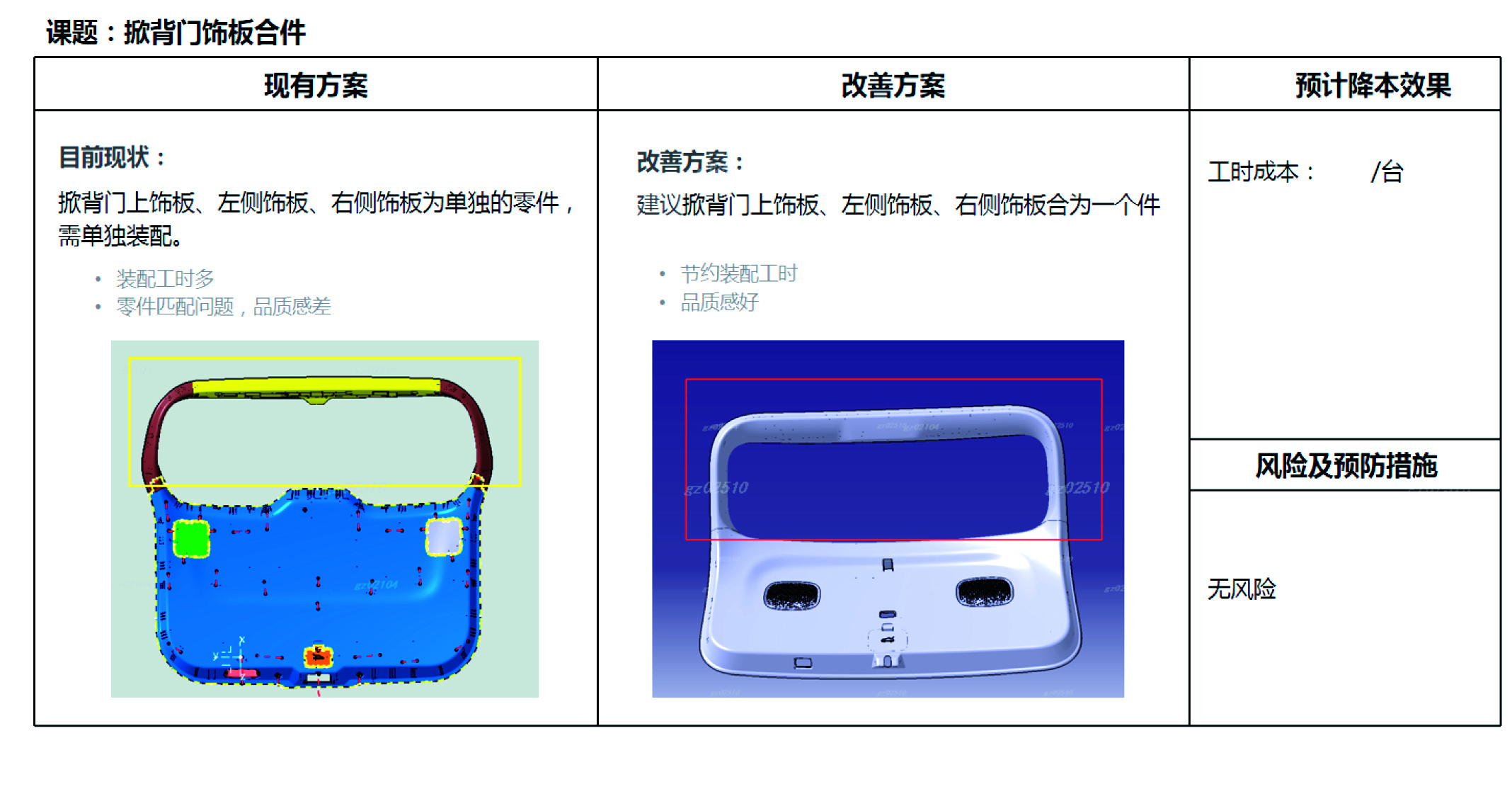
图4 背门饰板合件
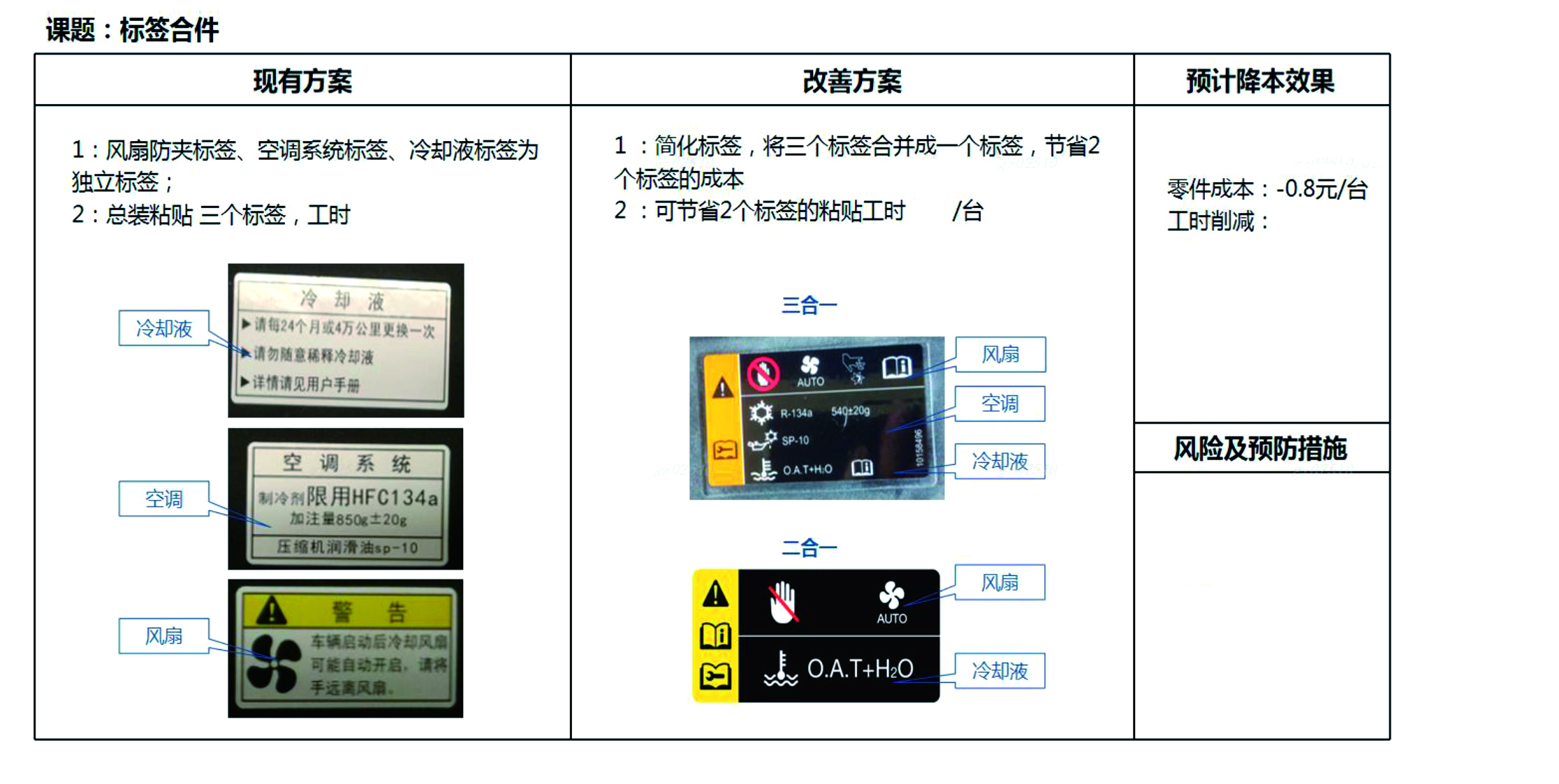
图5 警示标签合件
3.2 标准件优化
标准件优化主要从四个方面进行。
(1)标准件长度
优化减小标准件露出长度,建议露出长度控制在5mm内,可减重降本,节约工时。
(2)削减标准件种类
优先用六角法兰面螺栓、减少弹性垫圈的使用、螺栓和垫圈配合选用组合件,尽量不开发新标准件。
(3)标准件统一
相同安装点位标准件统一,可实现工具统一,工时减少;相同工位标准件统一,可实现工具统一,工时减少。
(4)力矩统一
力矩值统一,可实现工具统一,工时减少;力矩重要度统一,可实现工具统一,工时减少。
3.3 固定点优化
固定点优化主要也包括四个方面。
(1)螺接改卡接结构
尽量使用自身卡接或卡扣连接结构,可减少安装架及安装螺栓,降低零件成本和装配工时,如各种控制器(模块)、壶体、饰件以及其他塑料件(遮阳板固定)等,如图6所示。
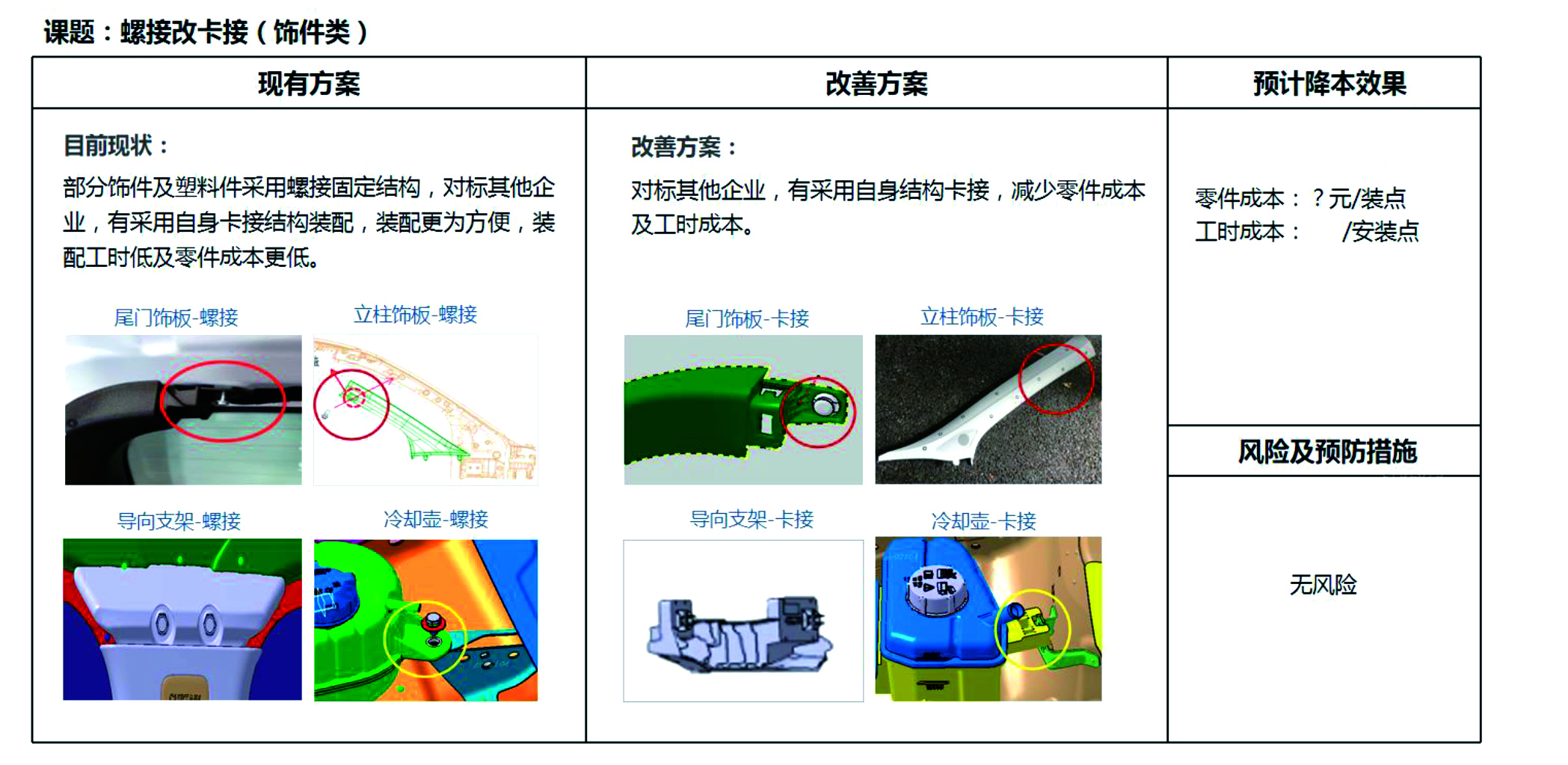
图6 螺接改卡接
(2)螺接改焊接结构
螺接改为焊接一体件,可减少标准件数量,实现零件成本降本及工时降低;螺母改为焊接件,可提升装配便利性,降低操作工时,如底盘摆臂螺母焊接至摆臂上等。
(3)螺母改内攻螺纹
采用螺栓加螺母组合的连接点,建议取消螺母,用内攻螺纹连接,可节约1个螺母并减少装配工时,如发电机、悬置支架等。
(4)安装点削减
取消部分多余卡扣安装点,实现成本降低及装配效率提升;减少部分多余螺栓固定点,实现成本降低及装配工时减少,如取消天窗排水管固定卡箍。
3.4 工艺定位优化
工艺定位优化也是四个方面进行。
(1)去工装化
尽量采用自定位,能不用工装就不用工装,如图7所示。
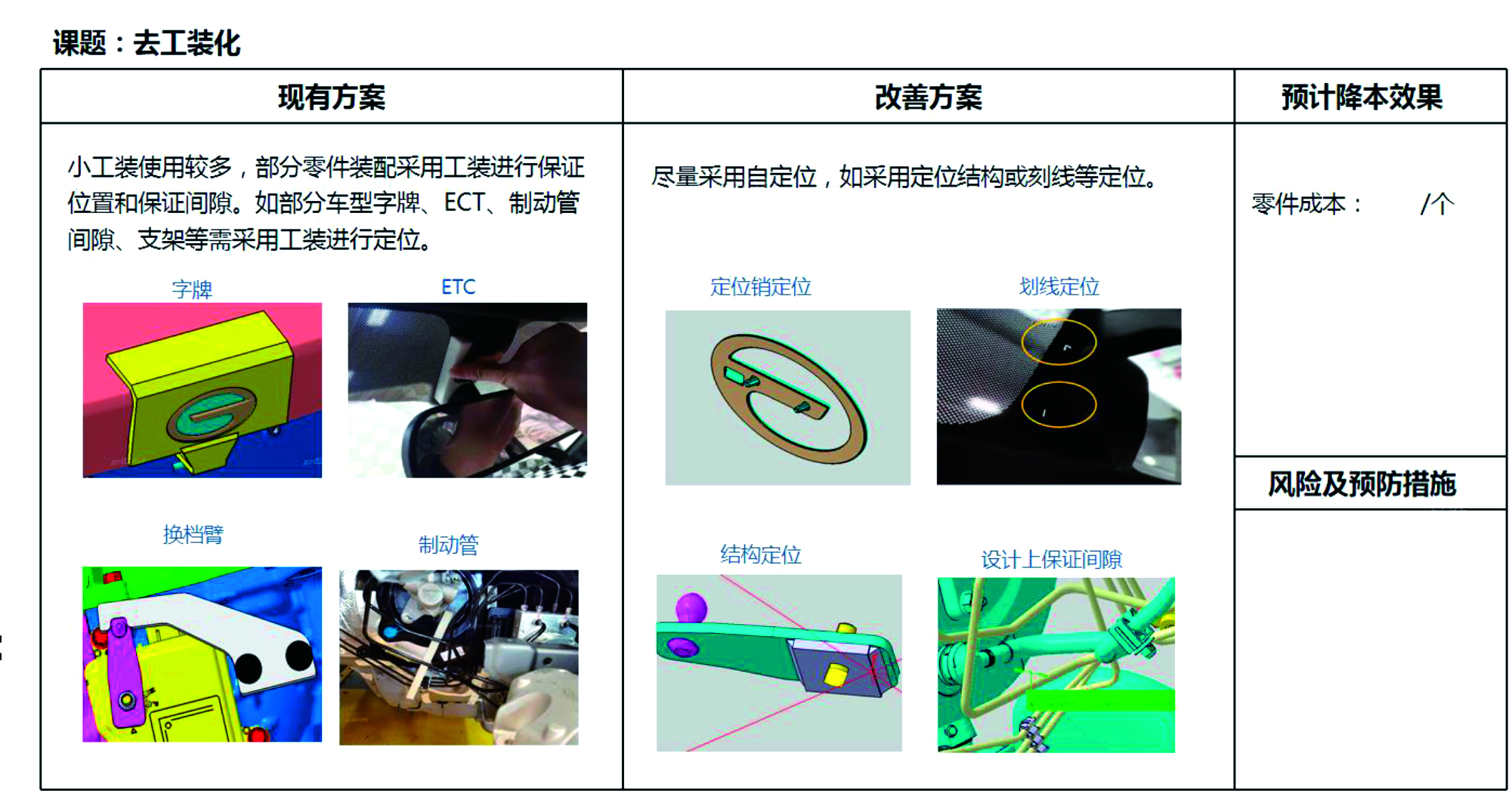
图7 去工装化
(2)去调整化
尽量取消不必要的调整,装配精度、间隙面差通过定位销、面等靠设计保证。
(3)定位结构优化
用工装的,尽量采用本体开定位孔或翻边限位,避免专用定位支架;取消多余的定位槽、防转槽和定位卡脚。
(4)预挂优化
尽量采用安装螺柱实现预挂,避免采用专用的预挂结构;尽量采用工装实现预挂,代替结构预挂,实现降本。
3.5 新结构工艺优化
通过对一些新工艺的开发及运用,实现成本降低和装配工时削减;使用一些低成本的、装配便利的新结构,比如增加转向盘与转向管柱刻线,增加束角调整螺栓处副车架划线等以减少对位作业工时;雷达支架粘接改为摩擦焊等,从而减少整车装配工时,降低整车制造成本。
4 总结
人员密集型工作是汽车总装的重要特性。工艺人员研究总装工艺,最重要的就是研究人的作业。作业工时是总装工艺人员作业的数据化展现。设计工时作为作业工时最核心的部分,从设计端开始研究,在数模设计阶段体现,往往能取得事半功倍的效果。
G公司在混动车型与常规燃油车共线生产问题研究上,从设计端开始,各类方案同步推进,最终实现单车设计工时削减880s。按年产量11万台计,总装阶段可节省人员14人,折合人工成本为280万元/年,零件降本66.7元/台,取得了巨大的经济效益。后续此方案将会推广至各平台车型,包括燃油、混动以及纯电车型,以期进一步降低整车制造成本,提升产品市场竞争力。
参考文献
[1] 杨阳.基于产品工时对车型装配成本削减的应用研究[C]//2021中国汽车工程学会年会论文集.
[2]TUANS,TanJ,etal.Improvementofworkflowandpro-ductivitythroughapplicationofMaynardoperationse-quencetechnique(MOST)[C]//Proceedingsofthe2014InternationalConferenceonIndustrialEngineeringandOperationsManagement.
本文为“AI汽车制造业”首发,未经授权不得转载。版权所有,转载请联系小编授权(VOGEL100)。本文作者:万小飞 张健均 郭称勇 ,单位:广州汽车工业集团汽车工程研究院 。责任编辑龚淑娟,责任校对何发。本文转载请注明来源:AI汽车制造业
评论 0
正在获取数据......