0 引言
车架总成是整车上最大的零部件,而且是重要的组成零部件之一,而车架纵梁是将整车发动机、油箱、电瓶箱以及板簧等零部件连接在一起的部件,若产品配置不同,安装位置也就不同,纵梁上的孔位和外形也就存在差异。随着客户个性化需求的不断提升,对车架纵梁加工提出了更高的要求,本文从纵梁加工方式入手,通过工艺革新、设备改进,不断提高车架纵梁加工效率及加工质量。
1 纵梁成形加工方式
自建厂以来,我厂纵梁成形工艺经历了辊压成形—折弯成形—模压成形—辊压成形的发展变迁,细究其发展变化源于设备能力提升以及产品的变革、发展。
1.1 简易变截面专用辊压成形
主要产品纵梁为变截面大梁,因同期大型压力机发展水平无法实现纵梁模压成形工艺,因而建设简易变截面专用辊压成形线用于加工变截面纵梁。
1.2 折弯成形
20世纪80年代中期,我公司引进斯太尔产品技术,其纵梁为等截面纵梁(如图1所示),辊压成形线无法满足产品的变化及产能需求,20世纪90年代初期又引进3500t压力机进行纵梁折弯。
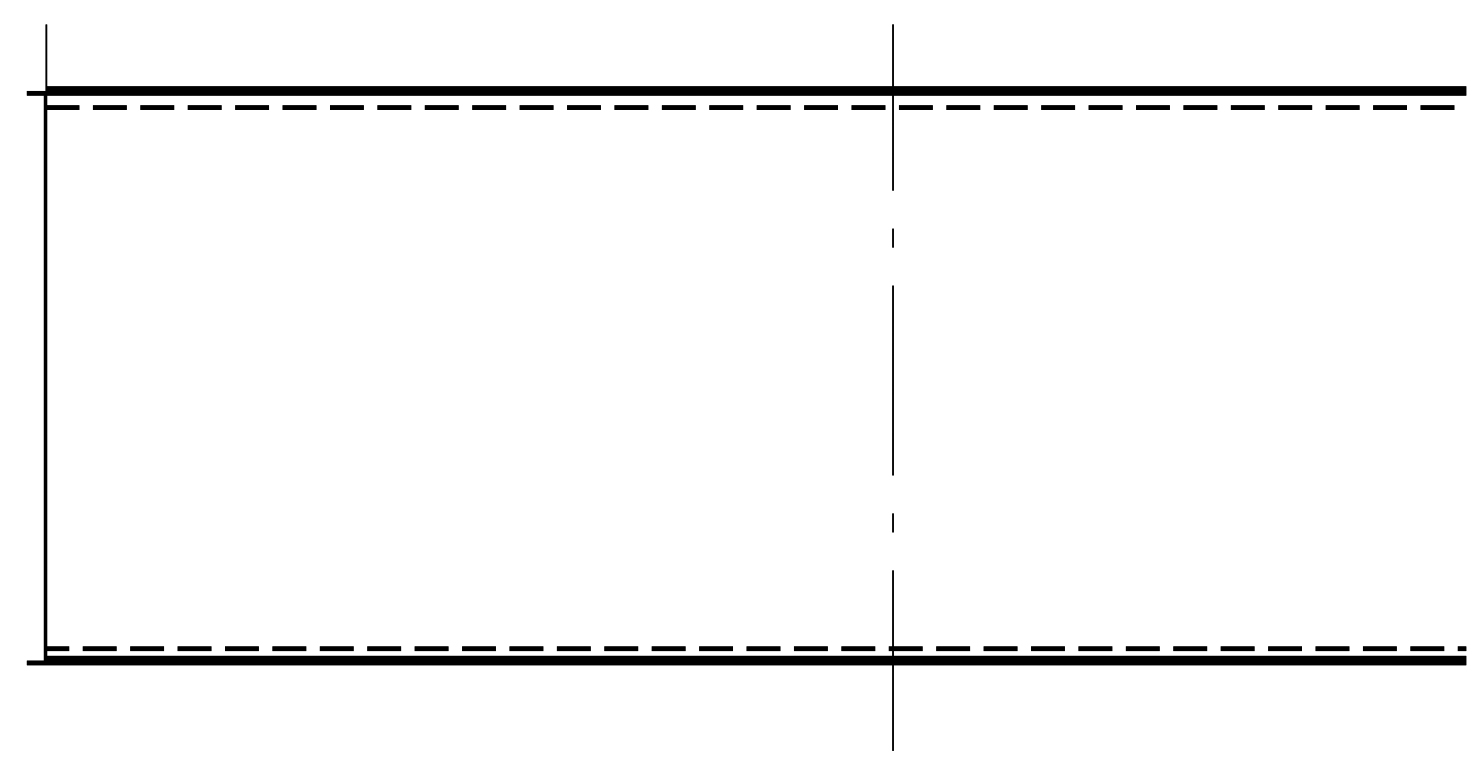
图1 等截面纵梁
1.3 6000t模压
随着产品的换代需求,F2000产品引进了MAN平台纵梁变截面、车架变宽度技术,如图2所示。为实现变截面纵梁成形,开发模压工艺加工变截面纵梁,引进6000t进口压力机及相关模具,实现了此类截面纵梁的加工。
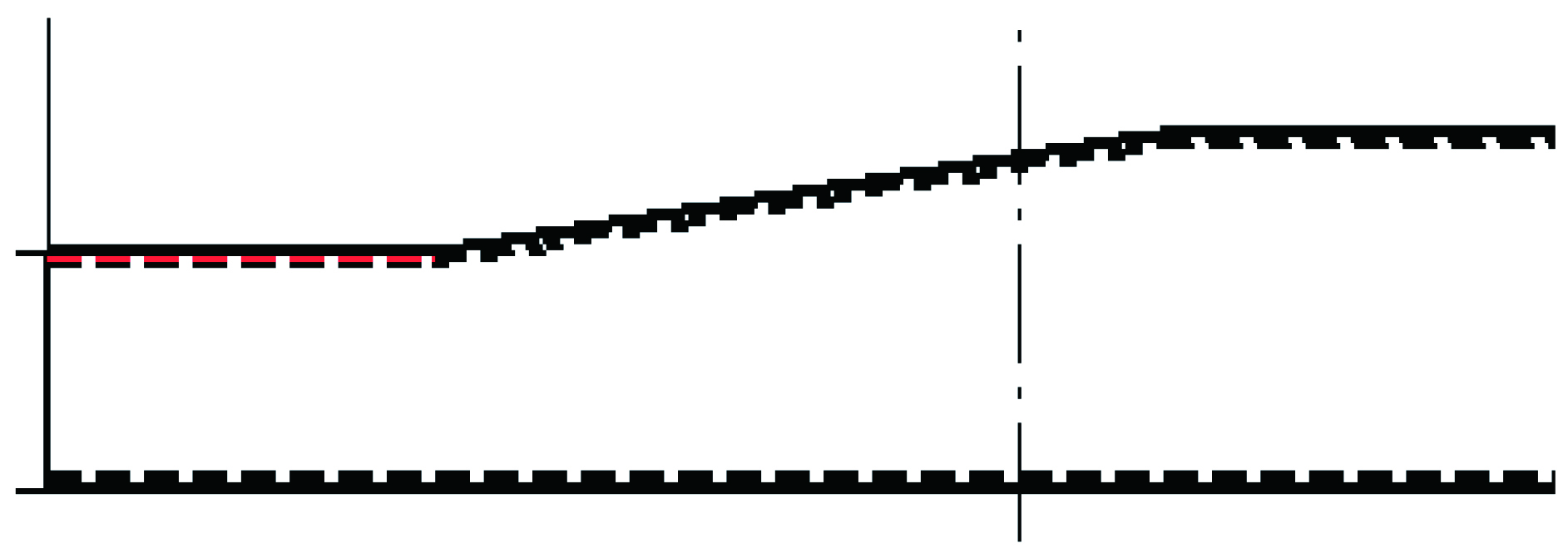
图2 变截面纵梁
1.4 辊压成形
高强钢、直大梁为汽车纵梁的发展趋势,辊压成形工艺在不同规格产品的切换之间具有更高的柔性化,可更好地满足产品质量并能高效适应日新月异的市场需求所带来的产品变革,如腹宽变化和强度提升。为适应产品的不断升级,我厂引进纵梁开卷辊压成形生产线,用于重卡车架等截面U形纵梁及加强梁的辊压成形,将定尺宽度卷料经过开卷、矫平后,冷弯成U形卡车纵梁及加强梁,并根据所需长度将成形纵梁在线冲裁切断,生产效率、加工质量得到明显提升。
2 纵梁孔位加工方式
纵梁孔位加工方式,随着设备的不断更新,方式也在逐渐变化。现在纵梁孔位的加工方式主要有平板冲孔、三面冲孔以及分步冲孔,如翼面冲孔+腹面冲孔,或是三面冲孔+腹面冲孔。
2.1 平板冲孔加工工艺流程
平板冲孔加工工艺流程为:定尺板料—数控冲孔—平板等离子切割—6000t压型。
原材料采用定尺板料,采用数控平板冲孔设备将纵梁上所有孔位冲出,同时需加工压型定位销工艺孔,采用大型压力机将板料压制成U形纵梁,因在板料上进行加工,所有孔位可一次冲出,基本不存在设备死区孔位问题,适应于单品种小批量生产。加工产品类型受模具规格影响较大,考虑到生产成本及加工效率,一般可进行2~3种规格产品的切换,不能满足所有产品的加工。同时加工的孔位精度受数控设备、压型模具以及原材料外形尺寸影响,而且数控工序后会存在大量缓存半成品,同样对车间生产组织、物料配送增加了难度。
2.2 三面冲孔加工工艺流程
三面冲孔加工工艺流程为:定尺槽钢—数控冲孔—机器人等离子切割。
三面冲孔可加工纵梁腹面及两个翼面上所有的孔位,包括小孔及大孔,随着设备升级及加工效率的不断提升,加工的主机由三主机、四主机逐渐升级至现在普遍使用的五主机,加工节拍逐渐提高。
此工艺方式原材料采用定尺槽钢,使用数控三面冲孔设备加工纵梁孔位,适应于多品种小批量生产,可加工不同腹宽、厚度及材质的产品。受模具影响,若孔距翼面或腹面太近,将进入设备加工死区,无法一次冲孔,后续需增加工序进行补孔或是扩孔。
2.3 分步冲孔加工工艺流程
分步冲孔加工工艺流程为:定尺槽钢—翼面冲—腹面冲—机器人等离子切割或者定尺槽钢—三主机三面冲孔—腹面冲孔—机器人等离子切割。
这两种工艺方式和三面冲孔加工工艺类似,结合产品结构特点、设备投入数量及成本,将一步冲孔分为翼面冲孔+腹面冲孔或是三主机三面冲孔+腹面冲孔,其中翼面冲孔+腹面冲孔是将大孔在腹面冲进行加工,虽然两个主机可同时加工,但受大孔主机运行速度影响,效率较三主机三面冲孔+腹面冲孔方式仍有些慢,将翼面孔及腹面大孔直接安排在三主机三面冲进行加工,腹面孔配合双主机双冲,最多一次可同时加工4个孔,整个纵梁的加工效率可提升40%以上。
3 纵梁异性孔位加工方
式纵梁孔位加工中变化最大的就是异形孔的加工方式。车架纵梁上的孔尺寸从φ9~95mm,后来根据产品线束布置优化要求,将线束集中,最大的孔变为φ60mm×120mm的长圆孔,如何保证加工后孔位质量及加工效率不降低,此类孔位加工方式也在不断探索,不断优化,以适应产品要求的不断提高。
异形孔的加工工艺随着产品结构特点的变化也在不断改变优化,从连续冲裁、等离子切割到直接冲孔成形,加工精度、质量在不断提升,纵梁上的异形孔尺寸规格基本都为φ60mm×120mm的长圆孔,现阶段长圆孔有三种加工方式。
3.1 采用φ60mm大孔进行连续冲孔
对于一般的纵梁数控冲孔设备来说,最大可加工孔位的直径为φ60mm,可采用φ60mm大孔进行连续冲孔,实现长圆孔的加工。但采用此种加工方式,加工后孔与孔的接触点会有一个小接茬(如图3所示)无法消除,只能后续打磨处理。若长圆孔的尺寸发生变化时,能否加工还得取决于是否有合适的冲头规格,所以此方式有一定的限制性。
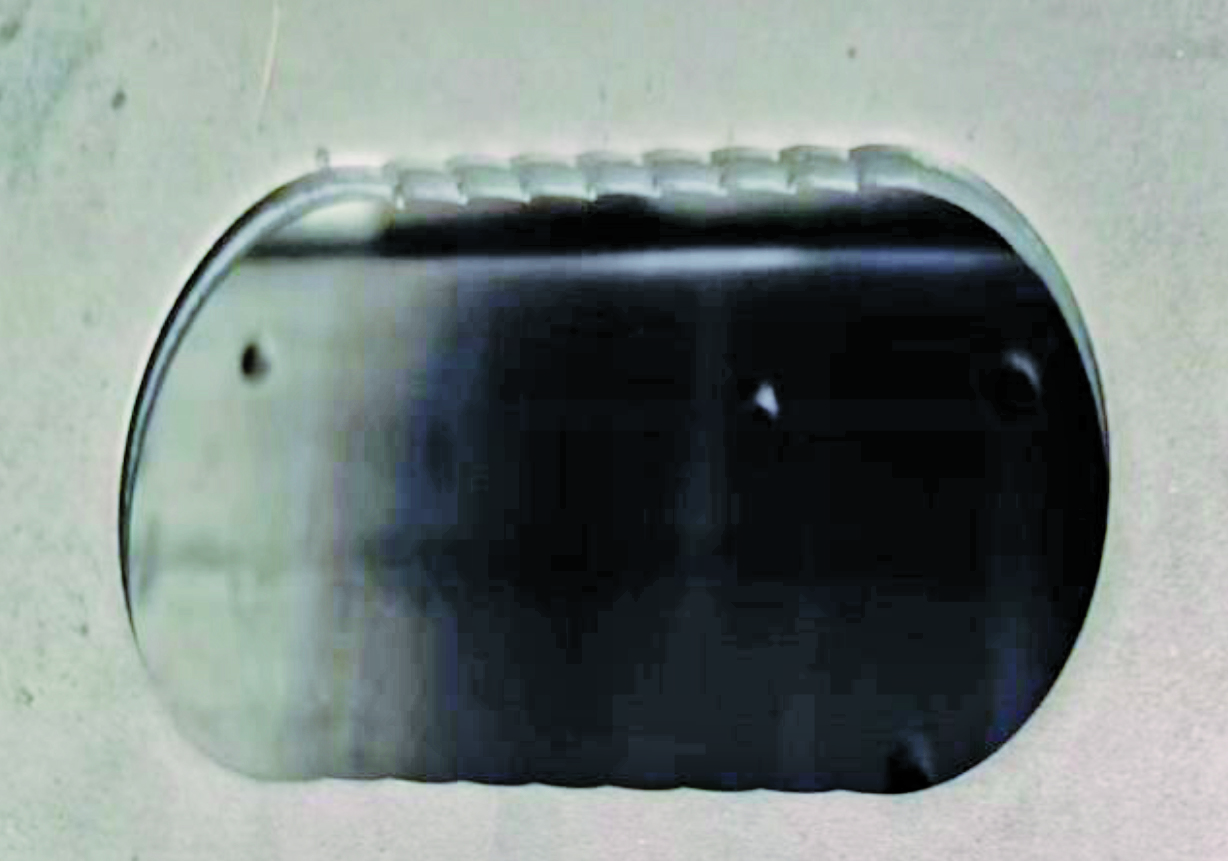
图 3 φ60 mm 孔连续冲孔效果
3.2 采用切割方式一次成形
采用切割工艺方式长圆孔可一次加工而成,在尺寸上没有限制。但对处于双层梁处的长圆孔,因设备精度、原材料状态都会影响加工精度,若内外梁分开切割,合梁后将会出现不同程度的“双眼皮”现象。后来通过在合梁工序引入切割设备,以孔定位,实现了内外梁合梁后的整体切割,确保双层梁处长圆孔平齐,无“双眼皮”现象,加工效率及质量都得了到有效保证。
3.3 采用专用冲头加工
现阶段纵梁上最常见的长圆孔规格为φ60mm×120mm,经过计算,若采用直接冲裁的方式,为保证孔位的正常冲裁,冲孔主机的吨位要求将大大提高,而且直接加工长圆孔,则至少需占用模座中的两个模位,大孔主机可加工的其他孔径规格将减少一个,整个主机的地基强度需增强,下料通道需增宽,需解决一系列的问题方可实现。
为了降低冲裁力并减少冲裁的次数,减少对模位的占用数量,通过不断比对及试验,我们将长圆孔的加工方式改为分步冲孔,先加工中间的矩形,然后加工两侧的圆形。在设计模具各种规格的位置时,考虑到设备的送进方向及冲孔顺序,将矩形模位放在了φ60mm大孔模位的前面,以保证先加工矩形再加工圆孔。在冲孔程序生成过程中,需解决冲孔位置如何识别问题,通过对矩形孔及圆孔中心做好标记,实现特定的加工顺序及内容。加工后长圆孔基本无接茬,加工精度、加工质量都得到了保证,具体如图4、图5所示。
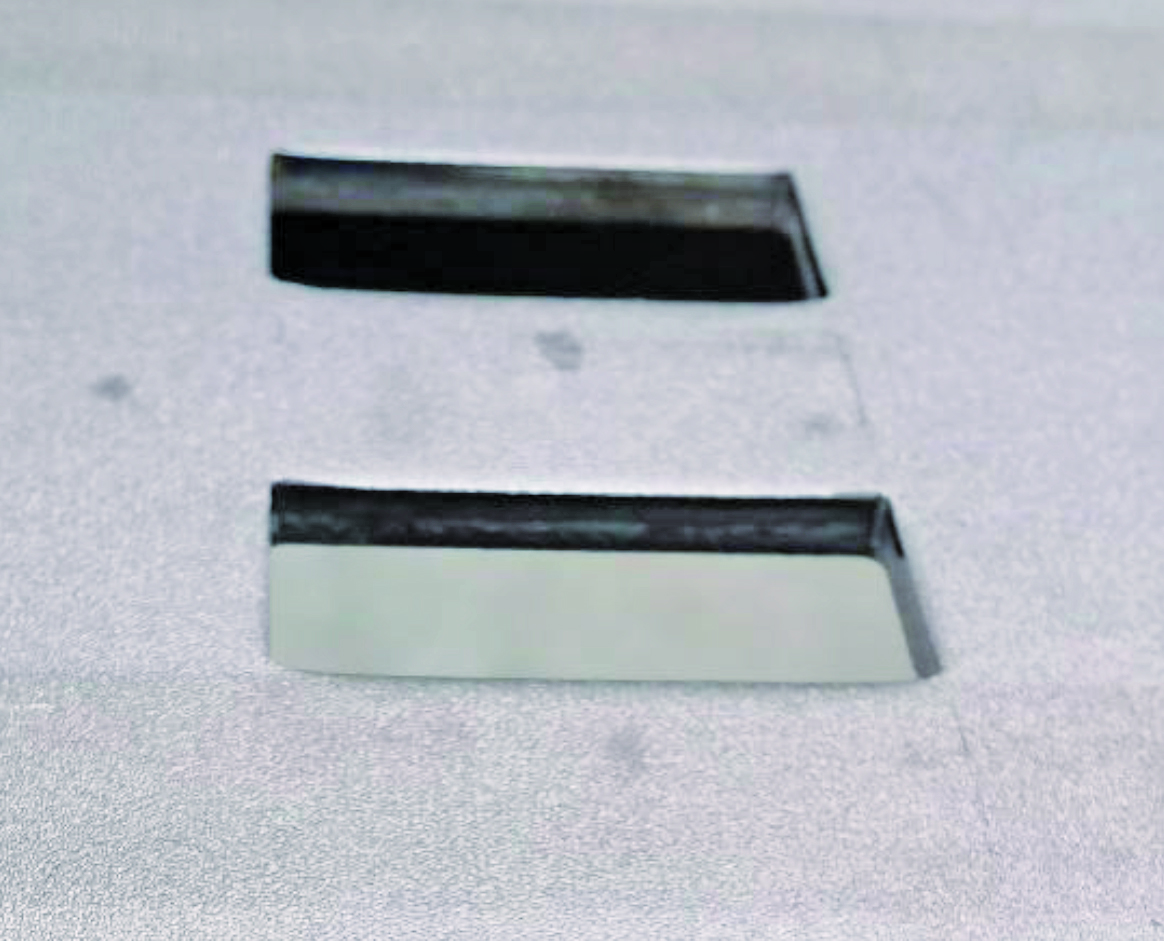
图 4 矩形冲头冲孔后效果示意
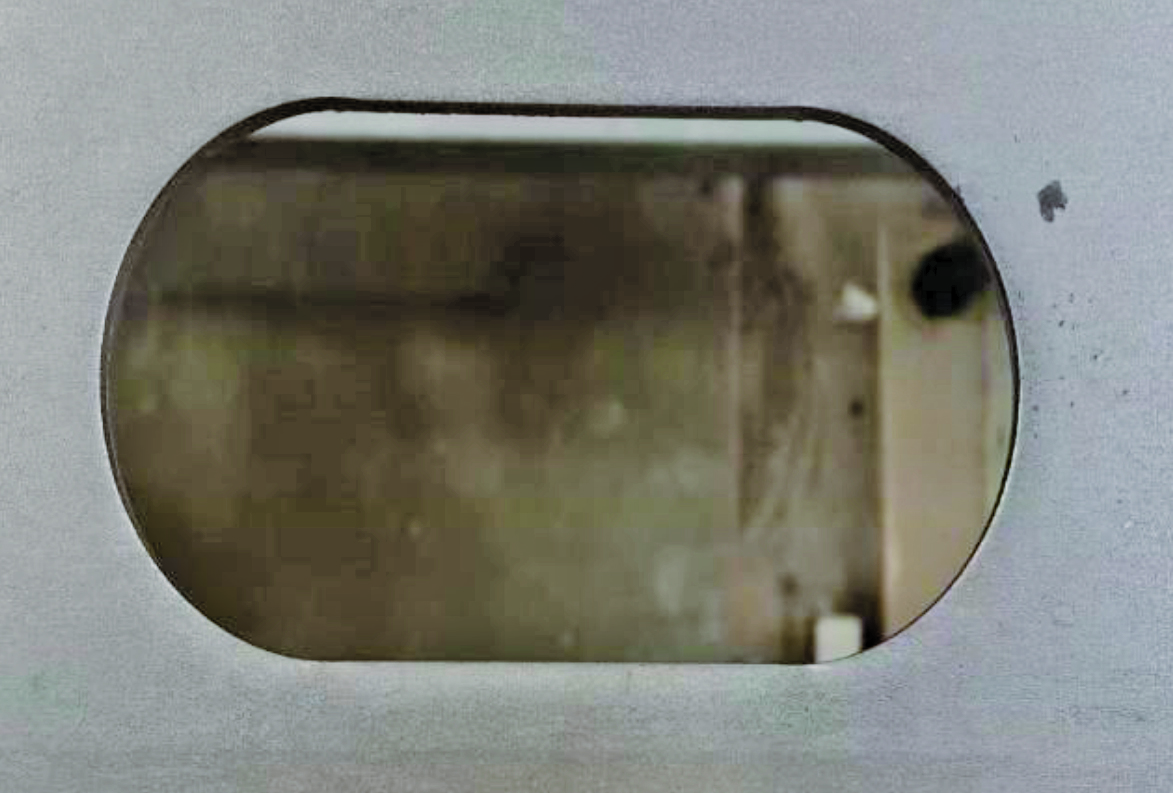
图 5 矩形冲头冲孔后效果示意
4 总结
纵梁是车架的关键零件,随着数控技术的不断提升以及产品更新换代需求,纵梁成形、制孔设备和加工工艺都得到了很大的提升,通过不断进行工艺革新、设备改进,加工效率与加工质量越来越高,纵梁加工工艺也将会越来越成熟。
参考文献
[1]乔战林.汽车U型纵梁三面数控冲孔生产工艺.科技情报开发与经济,2011,21:P221~222
[2]迟志波.汽车纵梁数控冲孔设备在汽车行业的应用.数控机床市场,2010,2:P24~28
本文为“AI汽车制造业”首发,未经授权不得转载。版权所有,转载请联系小编授权(VOGEL100)。本文作者:任泳圭 王旸,单位:陕西重型汽车有限公司。责任编辑龚淑娟,责任较对何发。本文转载请注明来源:AI汽车制造业
评论
加载更多