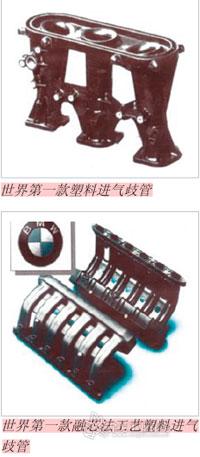
汽车进气歧管采用塑料代替金属铝来制造具有很多优势,该技术在国外经过30多年的发展已经非常成熟,但在我国却因起步晚、底子薄以及缺少发动机主机厂的支持等原因,使得国内塑料进气歧管企业的技术水平普遍较低。本文在介绍塑料进气歧管的发展历程以及两种主要生产技术的同时,指出了国内塑料进气歧管企业存在的问题,并提出了提高我国汽车塑料进气歧管制造水平的建议。
进气歧管是汽车发动机的关键零部件之一。长期以来,国内的发动机进气歧管都是采用铝合金材料来铸造生产的,但因这种制造工艺无法避免内壁粗糙和沙眼多的问题,从而导致使用时空气阻力大以及涡流、湍流不稳定,进而造成噪声大、燃料燃烧不充分及废气排放多。与这种传统的铝合金进气歧管比较,国外早在20上世纪70年代开发成功的塑料进气歧管(如今已发展了多种工艺方法,下面会有所介绍)则可以克服这些缺点。它不仅将重量减轻了50%,同时,因塑料进气歧管的气道光滑,空气流动阻力小,改善了发动机的动力性能和排放功能,提高了燃油的利用率,油耗可因此降低2%~5%。此外,塑料进气歧管的减振和降噪效果更好。基于此,近些年来塑料进气歧管受到了国产汽车发动机主机厂技术开发人员的重视。
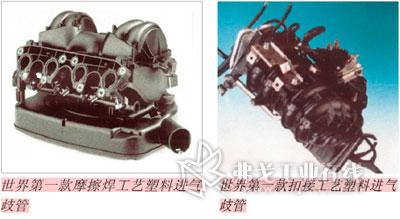
塑料进气歧管制造工艺的发展历程
1972年,世界第一款汽车塑料进气歧管诞生,被装配在Porsche(保时捷) 911车型上。它采用直接注塑成型(滑块和抽芯)工艺被生产而出。
1985年,世界第一款融芯法工艺生产的汽车塑料进气歧管诞生,被装配在BMW(宝马) 车型上。该歧管较铝合金歧管的制造成本降低了10%、 重量减轻了60% 、性能提高了2%,而且气道内壁光滑,产品一致性好。
1990年,世界第一款摩擦焊工艺生产的汽车塑料进气歧管诞生,被装配在VW(大众)车型上。该歧管由6片结构组成,较铝合金歧管重量减轻了50%,性能提高了5hp,噪音降低了3dB,制造成本较融芯法歧管降低了20%。
1998年,世界第一款扣接工艺生产的汽车塑料进气歧管诞生,被装配在通用Opel(欧宝)车型上。该歧管由2片结构扣接组成,较铝合金歧管重量减轻了50%,制造成本较摩擦焊歧管降低了10%(减少了集成成本)。
两大主要生产工艺介绍
目前,在国际汽车制造业中,融芯法和焊接法是两种使用最多也是最为成熟的塑料进气歧管生产工艺。
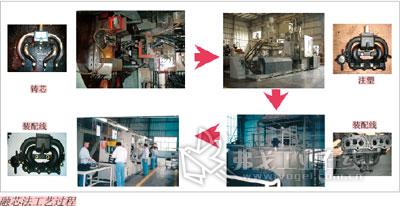
1.融芯法生产工艺
这种工艺与金属铸造非常相似。首先用低融点的锡合金制成进气歧管的内腔芯核,然后将其装配在模具中,再向模具内注入尼龙材料。注塑过程完成后,由尼龙注塑而成的进气歧管的外型就将内腔芯核包覆在内。此时,将内部带有金属芯核的进气歧管放入融化池内,以使金属芯核融化。由于金属芯核的熔点较低(一般为140℃),而尼龙的热变形温度相对较高(一般为240℃),因此在内部芯核熔化的过程中,塑料进气歧管的外形保持不变。
采用融芯法生产塑料进气歧管的优点是:进气歧管的内壁完整光滑,提高了气体的流动性,从而能够最大限度地发挥发动机的性能。由于是一次注塑成型,进气歧管的气密性好,成品率高。融芯过程可消除塑料进气歧管在注塑过程中产生的残余应力,使得进气歧管具有更好的机械性能。另外,融芯技术使塑料进气歧管的设计非常灵活,可以实现无缝单片的塑料进气歧管的设计,且不受复杂需求的影响,任何可以用金属铸造的进气歧管都可以采用融芯工艺来制造。融芯技术甚至可以被用来实现用铝金属铸造工艺无法实现的设计。无缝式设计可以使塑料进气歧管获得优异的抗爆裂能力,从而避免了因采用其他融接工艺而带来的抗爆裂测试的失效。抗爆裂测试是塑料进气歧管的主要测试项目,主要用来模仿发动机的逆火。
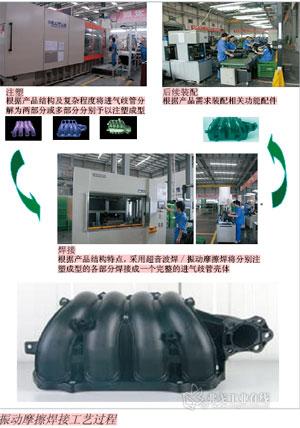
融芯法的缺点是成本较高,主要是能耗较高。尽管与铝金属材料的铸造工艺相比,该技术具有一定的成本优势(低融点合金和融化液可以重复利用),但在金属芯核的铸芯和融芯过程中,需要消耗大量的电能,因而使得融芯法生产塑料进气歧管的成本相对较高。
2.焊接法生产工艺
随着玻纤增强PA66焊接技术的日趋成熟,目前世界上多数汽车制造商开始使用振动摩擦焊接工艺生产进气歧管,即分别注塑成型2或多片歧管零件,然后将它们焊接成为一体。该技术的兴起,极大地推动了进气歧管的塑料化进程。
焊接成型的进气歧管实际上就是利用振动焊接技术将两片或更多片外壳焊接在一起。这些外壳通常拥有一致的平面,采用通常的注塑工艺即可成型。在振动焊接的过程中,两个部件的接触面互相摩擦,从而使接触面材料熔化并熔合在一起。在两个部件熔合的过程中,随着摩擦停止并冷却后,两个部件即焊接为一体。
与融芯工艺相比,焊接工艺最大的优势是成本相对较低,其总的成本只有融芯技术的5/6:从设备投资来讲,振动摩擦焊接法比融芯法小很多;从生产环节费用来看,因融芯工艺过程中的铸芯和浴芯的电能消耗很大,造成其用电成本远高于振动摩擦焊接法;另外,对于单个焊接成型的进气歧管而言,由于每一片外壳的成型周期较短,而且在下一个成型周期的注塑过程中就可完成前一成型外壳的焊接工艺,再加上没有类似于融芯工艺那样的材料损失(制造芯用的合金及油浴),因此单个焊接成型的进气歧管的生产成本相对要低很多。
振动焊接工艺的缺点是,焊缝处的强度低、外观不好及气体流动性相对较差。而且为了保证两个部件的接触面充分摩擦,每一个接触面都必须是平面,这就大大降低了进气歧管设计的自由度。另外,在振动焊接时,为了保证两个部件的接触面能准确地定位在一起,以实现良好的结合,要求每一个部件的接触面都必须留有5~10mm的焊接边缘。在狭窄的发动机周围,这种多余的焊接边缘常常给进气歧管的装配带来困难。
3.两种工艺的选择
虽然在成本方面(特别是用电成本)振动摩擦焊接法要低于融芯法,但从开发费用上来看,振动摩擦焊接法要比融芯法相对大一些,特别是分片数越多差别越大。融芯法只需要2套模具(1套铸芯模、1套注塑模),而振动摩擦焊接法则需要3套注塑模和2套焊接夹具。如果模片超过3片,振动摩擦焊接法则还要多出3套模具和夹具的投资。因此,仅就成本而言,加工商也不应一定选择振动摩擦焊接法,况且在产品性能上融芯法还具有一定的优势。加工商在选择工艺时的正确做法是:依据歧管复杂难易程度确定采取哪一种工艺方法。一般来讲,造型复杂、价值较高车型的歧管采用融芯法生产为好,而造型简单、价值较低车型的歧管则采用振动摩擦焊接法生产为佳。
国内领先的塑料进气歧管制造商
重庆宗申汽车进气系统制造有限公司(以下简称“宗申公司”)是国内最早进入塑料进气歧管生产领域并在这一领域一直占据领先地位的制造商之一。2002年,该公司从国外引进了融芯法生产线,随后全新设计开发了微车465发动机塑料进气歧管,从而填补了国内制造塑料进气歧管的空白。2004年,宗申公司为上海汽车集团开发了具有EVIC-iii 3段式可变进气结构,内部带有可调进气蝶阀片、蝶阀开闭拉杆及精密电子元件等特性的塑料进气歧管。这也是迄今为止结构最复杂、性能最先进的国产塑料进气歧管,该产品的生产同时采用了融芯法、超声波焊接和振动摩擦焊接3种工艺技术。
塑料进气歧管是一种高技术含量的产品,其中包含了很多发动机方面的关键技术。宗申公司作为国内塑料进气歧管生产企业中的佼佼者,不仅拥有正向设计开发能力,而且对于融芯法和振动摩擦焊接法两大生产工艺均能熟练运用。
提高我国塑料进气歧管生产水平的建议
总体而言,目前国内的塑料进气歧管制造企业的发展存在着许许多多的困难:一是自身有开发设计能力的企业不多,多数企业只能仿制国外非主流的产品;二是国内OEM主机厂的技术开发人员,由于其自身研学的都是金属加工技术,对塑料进气歧管开发技术的了解欠缺。面对时间紧、开发任务重的困难,他们大多不具有对进气歧管开发进行指导的能力,而且不相信国内企业有开发设计的能力,不愿给国内制造企业锻炼的机会,于是就不论成本,高价通过外资企业在国外进行设计。实际上,宗申公司为国内一自主知名品牌正向开发设计的一款振动摩擦焊法塑料进气歧管,其设计费要比拿到国外设计节约近100万元。因此,国内塑料进气歧管制造企业需要走的路还很长,不仅仅只是投资几百万建一条或几条生产线的问题,而是要将重心放在配合主机厂提高开发设计能力、培养专门人才上。只有这样,才能够真正提高企业的综合竞争力。同时,我们也呼吁国内主机厂能够摒弃固有的对国内塑料进气歧管企业技术水平的偏见,大胆将设计开发项目交给国内有开发能力的民族企业,这样不仅节约了成本,而且也有利于尽快提高我国的塑料进气歧管制造水平。
评论 0
正在获取数据......