线束数据阶段布置
线束是电器的神经系统,对整车电器电子功能的实现起着至关重要的作用。在线束布置的总体设计中,要充分考虑各相关的边界条件,对车身、动力总成、仪表台、底盘和内饰件必须充分、系统地了解,充分考虑各相关件对线束布置可能产生的影响,并对相关件的设计提出相应合理的要求。同时,我们要充分考虑整车的温度分布和振动,避免线束通过高温区,避免线束剧烈振动。
整车布置的可维修性
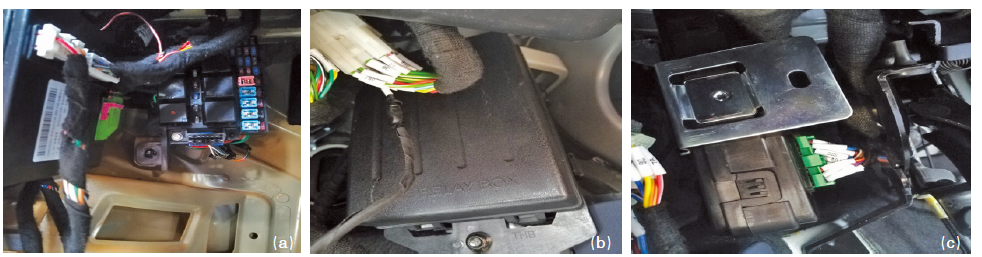
整车布置维修效果
对于整车电器系统,在车辆售出后,不可避免地会存在维护工作,如不同线束间的连接器、电器盒保险丝、继电器的更换、诊断接口的使用、BCM更换VTC以及ICU的检测维护等。
仪表线束是电器功能对接件较多线束之一,同时也必须是布置在难以拆卸的仪表台下方,若不考虑线束布置和相关件的结构,如图中a和b所示,就难以维修(要先将制动踏板拆下,操作不方便,电器盒盖需要强拆卡接位置容易断裂),而如图中C所示的布置维修很方便,是较为理想的状态,根据经验,一般零部件布置安装位置与周边件需保留出一拳的距离,方便工具操作拆装。
整车电子架构的可维修性设计
电气方面的维修性要求主要体现在电气系统方面的故障诊断及各电子控制模块的维修。整车的电子和电气系统的实际维修应能保证快速和准确的诊断。这些要求通过以下要素体现:尽量无需拆卸车上的零部件就可以实现标准的诊断测试端口的接入; 无需复杂的技能培训即可实现车辆诊断及维修;避免使用专门的测试装置和特殊的工具就可以进行诊断和维修。
线束布置和走向分析
1.前舱线束布置和走向分析
前舱线束的布置在整车线束的布置中占有重要的地位,反映整车线束的布置水平。前舱线束所处的环境最为恶劣,要考虑防水、隔热和振动等因素,需要对线束做好充分的保护。
(1)前舱线束通往室内的橡胶件
此处橡胶件容易出现漏水问题,多是因为前舱盖处密封不良,湿区(前舱内)线束布置比干区的线束位置偏高,水通过线束内部进入室内。
解决方案:布置干区的线束布置比湿区的线束高,橡胶件内部的使用灌胶或者防水泥密封。
(2)前舱电器盒处
前舱电器盒为整车用电器电源线较集中的部分,此处线束布置较为集中,且布置的空间较小,实装配时操作难度较大,或者是装配后电器和盒盖难以拆卸和装配,且电器盒布置处于挡水槽下方,在前舱盖密封不良情况下会进水导致电器功能件失效。
解决方案:将前舱电器盒布置于离挡水槽较远处,周围连接线束走向分散。
(3)左右线束枝干处
此处也是前舱线束容易进水的地方之一。前舱盖上积水从左右前纵梁的上的导水槽流出车身,线束一般布置在导水槽左右,当水量较大且车高速行驶时,导水槽排水不及时,水便会蔓延至前舱内,前舱线束多以波纹管和PVC包裹,进水和积水将影响前照灯和雾灯等插件。
解决方案:支干线束布置位置与导水槽保持一定距离;导水槽结构设计需满足承受一定量的水位的能力;线束包裹宜波纹管加PVC密包裹。
(4)前照灯、转向灯插件处
灯具后方操作空间小,前照灯插件连接时难以用力,插接困难,而转向灯插件处容易受水流的直接冲击而进水,导致转向灯进水起雾问题。
解决方案:侧转向灯线束尽量从前横梁下方水无法直接倾泻到的位置通过。
(5)刮水器电动机处
此处常见问题是刮水器线束固定不良,线束和电动机连杆干涉,刮水器运动时连杆对线束产生摩擦,磨损线束导致刮水器不能正常工作。
解决方案:线束与可运动部件保持一定距离,在双方都能保持固定的状态下,至少留出1~2 cm的间隙,防止长时间振动后紧固不良或产生偏移。
在前舱线束的布置中,由于前舱环境较为恶劣,零部件众多,空间相对狭小,布置前舱线束的时候,要充分考虑前舱线束的走向、保护和固定。应注意的问题有:前舱热场的分布、过钣金的保护、线束的固定定位、线束和运动机构的干涉及接插件的固定等。
2.仪表线束布置和走向分析
仪表台集中了全车大部分的操作开关和显示装置,聚集了多个控制单元,同时,线束对接的部分也往往设计在仪表台的两侧,所以,仪表台线束是整车最为复杂的线束之一。
(1)组合仪表后方
组合仪表信号线较多,导线多且较细。组合仪表在仪表台上占用空间较大,留给线束布置的空间较小,组合仪表后方的线束较为拥挤,线束在此处容易和仪表横梁干涉。且组合仪表一般是用自攻螺栓固定在仪表横梁上,线束走向不好会被螺栓攻破。
解决方案:在仪表横梁上设置固定孔,不可使用凸焊螺栓。线束在此位置的扎带全部锁死,不允许存在扎带松动、线束来回串动情况。
(2)仪表电器盒固定处
仪表电器盒同样也为仪表线束的集中点,此处电器盒固定时容易卡线,仪表下方操作空间不足,容易压线或者磨线;导线从电器盒中出来后不确定走向时容易与仪表电器盒支架干涉,受磨损损坏。
解决方案:按照实际装车后的状态调整每个插件分支的长度,确保能装配且不绕线;电器盒必须明确仪表电器盒导线的出线方向,确保装配后,导线不与仪表横梁及电器盒自身支架干涉。
(3)BCM插件处
BCM插件处的线束布置需非常紧凑,因为BCM装配空间一般较小, BCM插头一般较难装配,且返工或者维修BCM操作空间受限。
解决方案:接插件插接位置尽量留出手指能够自由操作易拆卸的空间。
3.室内线束布置和走向分析
室内线束是全车最长的线束,它贯穿整个车身,是在整车的设计中首先要考虑布置的线束。由于它所牵涉到车身问题最多,所需要考虑的过孔问题也最多。
(1)左右B柱处
左右B柱处主要有门线束接头和门接触开关插件。B柱处线束需从室内转移到B柱内外板中间,需过孔,线束保护不好或者走向差就会造成线束被磨断、插头固定不良及B柱内异响问题。
解决方案:在过孔处,线束内外部分都增加定位点,车身上设定定位孔,保证过孔处无线束接触到车身钣金;同时此处使用减噪的绒布胶带和海绵条包裹。
(2)前座椅下方
这里有座椅线束和安全带相关线束。座椅是运动件,且运动轨迹不定,所以前座椅下容易出现的问题有线束被磨破、座椅加热线被磨断及座椅加热线束被后排乘客踩断等。
解决方案:找出座椅各个方向运动的极限距离,保证线束尺寸满足座椅运动;布置线束远离座椅导轨,并且保证线束固定在车身底盘和座椅下方。
(3)后保险杠线束处
后保险杠线束是室内通往室外且有倒车雷达探头等插件的分支。因为探头是分装在后保险杠上的,所以布置时需考虑好后保险杠的装配方式,否则会造成倒车雷达插件难对接问题;另外,此处过孔点容易进水。
解决方案:橡胶件喇叭口放在室内部分,固定部分放到室外,室外部分线束放低,不让水通过导线顺流到室内。橡胶件处适合内部灌胶或者全密封包扎。
前期维修性设计
前期维修性设计,除了积极参与整个产品开发过程,对设计开发提出相关需求,并根据项目不同的阶段进行分析、验证,积极沟通解决发现的问题,使得开发的产品符合市场定位及目标之外,产品设计结果还需要作为售后工程后期开发的输入,进一步进行其他售后交付物的开发。需要强调的是,对产品开发前期全程介入,并不意味着最后结果就一定会获得最佳的维修性,因为发现问题后,最后的项目决策往往是对公司经济或其他方面最有利的决策,而并非是对维修性最佳的决策,因此,所有前期维修性设计与开发的缺憾需要通过后期售后工程的其他交付物去
弥补。
总结
维修性技术要求实施的关键, 在于如何将这些要求系统全面地落实到实际的产品设计开发过程中,使得最后的产品尽量满足先期提出的维修技术条件要求(并非要求百分之百满足或达到)。贯穿于整车开发全过程的维修性检查、验证及问题沟通解决就变得非常的重要。维修性技术开发要求, 往往是多年技术开发的经验积累与技术结晶, 能体现一个企业的开发管理体系要求和现行质量体系的要求。
评论 0
正在获取数据......