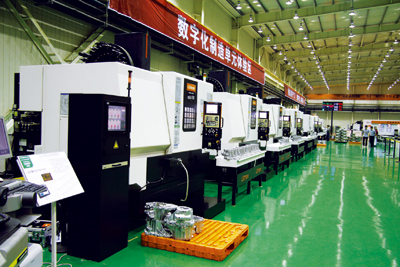
在汽车零部件的批量生产过程中,柔性生产线不仅能够满足多规格品种轮番加工或混合加工的需要,而且具有能够有效帮助用户降低设备投资、可根据市场需求变化随时做调整等诸多优点。
目前,汽车零部件产业正由大批量生产向变种变量的生产方式过度,传统的以生产为主导的生产方式正在向以客户为主导的方式转变,这必然会带来生产方式的变革,自动生产线显然已经越来越不能适应汽车生产厂家的需要,柔性制造系统适时出现了。
汽车零件是典型的大批量生产,为了降低生产成本,生产线必须具有很高的生产效率,传统的刚性线的优势就是生产效率高,因此,如果柔性线要替代刚性线首先要解决生产效率问题。随着数控机床向高速方向发展,加上日新月异的刀具技术和刀具新材料的应用,数控机床的加工效率得到大幅提高。在零件的生产中,一些辅助时间对效率的影响也相当大,因此要求设备具有很高的快速移动速度和加减速度以及尽可能短的换刀时间。现在高性能的数控机床都能够满足这方面的要求,加上通过在机床上设置多工位夹具、采用复合刀具和多功能刀具的方式也大大缩短了辅助时间,柔性生产线的加工效率也能够达到组合机床生产线的水平,消除了柔性生产线的瓶颈,为柔性生产线进入大批量生产领域创造了条件。
柔性化生产主要包含以下几个方面的柔性化:
1. 加工设备柔性化
要求生产设备具有能够适用于多规格品种的轮番加工或混流加工能力,更换规格或品种时不需要调整或调整很少的部位就能够很快适应新产品的加工。为了给客户提供多样化的选择和个性化的需求,根据客户需要在零件生产过程中可能会随时改变零件的加工部位来满足客户多样化的需求,因此,要求生产线能够适应这种需求。目前,以标准数控机床为单元组成的柔性生产线基本上都能够适应这方面的需要。有时虽然产品没有变化,但由于原材料改变或者刀具等工艺方面的改进也会对生产线的柔性提出要求,生产线必须能够适应工艺的变化。
2. 刀具和夹具柔性化
刀具的柔性是指刀具应能够适应多品种和多种材质的零件加工,因此,它还要求机床具有很强的刀具管理和寿命管理功能,比如,小巨人公司生产的机床配备的智能化网络化数控系统,在更换加工零件后,数控系统会对新产品加工需要的刀具和刀库内现有的刀具自动进行比较,并提出哪些刀具可以继续使用,哪些需要补充,哪些刀具刀库里虽然有但是刀具寿命到了,以提醒操作人员及时更换,大大提高了效率。
夹具的柔性表现在尽量设计统一的底板和接口上,在零件差别较小时只简单地更换几个定位和夹紧元件就可实现零件加工的快速转换。在更换的零件差别较大的情况下,可以通过更换定位板、保留基板的方式解决,而定位板和基板之间可以采用快速定位和夹紧装置进行,更换品种的速度非常快且不用重新调整坐标,达到快速调整产品品种规格的目的。
3. 柔性生产线的批量性
由于加工设备大多数都是标准的数控机床,而现在数控机床的性能和复合化程度越来越高,使得零件的加工工序大大缩短,因此,对于批量的柔性化适应能力也大大提高。由于加工工序的减少,生产线也相应缩短,甚至3、4台机床组成的生产单元就可以完成全部加工任务。为了达到要求的产量,一条生产线可能有几个相同的生产单元组成,使之对批量的适应能力大大加强,比如在产品的试制阶段,可以先上一个单元,随着产量的加大,可以按照节奏随时扩充单元。这种方式还适用于不同的单元生产不同的产品,因而可实现多品种混流生产。产品成熟期过后,产品产量必然会下降,必须要有新的产品替代旧的产品,我们可以逐步从生产线中调出一个单元进行新产品的试制,试制成功后可以从旧的生产线中逐步调出生产单元开始新产品的生产,随着旧生产单元逐步调整成新品种的生产单元,从而实现新旧产品的平稳过度。而刚性线一旦开动就必须全线运行,且一旦产品更新换代则全线淘汰。
这样做还有一个好处是,可根据产品的产量合理安排人员,当产量减少时可以减少生产单元的数量,同时需要的操作人员和占地面积也同步减少,而刚性线哪怕是只生产一个零件也需要生产设备全部开动,所有的操作人员都要上班,造成人员和设备以及厂房资源的浪费。
由于汽车的使用寿命相对较长,因此,即使一个型号的汽车停产,也要保证已出售产品在整个寿命期内的备件供应,如果是单元化的生产,只需要保留一个单元即可满足备件的生产需要。举例来说,小巨人公司在给一家用户提供的一条年产30万套变速箱零件的生产线中,把该生产线分成完全相同的年产10万套的3条线,缩短了生产线的长度,也使产品的生产组织方式变得非常灵活,既可以同时生产同一种产品也可以同时生产不同型号的2种或者3种产品,而且可以把由于设备故障所造成的影响降低到最小。
另外,随着技术进步的加快,新产品的设计或者产品的升级也随之加快,柔性生产线要具备随时对零件的这些改变做出反应的能力,柔性生产线线中的数控机床通过更换刀具和修改加工程序可以实现这种要求。
4. 生产线的可扩展性
柔性化生产要求在产量增加或减少的情况下,要随时可以根据市场的需要进行产量调整。小巨人公司为一家客户设计制造的发动机零件生产线,在设计阶段就充分考虑了产品扩展的需要,整条生产线一次规划,分步实施,预留了发展的空间,在将来需要扩充产量的时候,只需增加相应设备就可以。为了使生产线中的机床得到充分利用,在增加机床的同时适当调整工艺,增加物流线的长度就可以很快扩充到规划的产量,最大程度地节省了用户投资。
柔性线的优势还在于交货周期上。由于在柔性线上使用了标准的数控加工设备,因此只需要进行刀具、夹具、物流和辅机的设计,就可使交货周期大大缩短,有些甚至是和产品的设计验证同步进行。
柔性线是通过先进的物流技术按照工艺顺序将工件依次输送到各个数控机床和辅机上的,物流充当工件运送和中间存储的作用,减少了工件工序间的存储数量,提高了机床利用率。由于汽车零部件的生产批量比较大,一般每个工序的机床数量都在2台以上,物流采用双层料道,上层为毛坯或者上工序加工的成品,下层为本工序加工的成品,在工序间转换的地方设置工件提升装置,将上工序的成品自动提升到上层料道成为下工序的材料。加工前后的工件不会产生混淆。因此,柔性线的优势还表现在当生产线其中的一台设备出现问题停机维修时,也不影响输送料道的畅通,从而保持整条生产线的正常运行,避免了停工。
在柔性制造系统的基础上,结合自动化技术和信息网络技术把零件的生产和管理结合起来是目前柔性化生产技术的最新进展,也是精益生产的精髓所在。MAZAK公司特有的智能化网络化的数控系统为这种需要提供了基础的数据和数据传输通道,加上专门开发的CPC(智能生产中心)软件,通过CPC软件对各个加工设备实时动态数据的收集和分析,为管理者提供了科学准确的决策依据,从而对生产过程中的设备、人员、刀夹具、程序和计划等要素进行实时调度和控制,及时发现和解决生产中的各种问题,而且当生产线中的设备出现问题的时候,管理人员可以通过网络第一时间得到设备故障信息,迅速准确地处理问题。
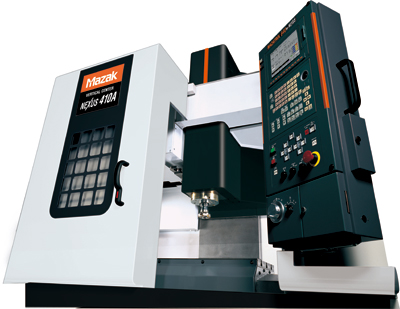
由加工中心组成的柔性生产线已经在汽车零部件生产中大量采用,但是在一些发动机和变速箱壳体零件的生产中,主要还是由卧式加工中心组成的生产线,而卧式加工中心的价格是立式加工中心的几倍。在当前汽车产能过剩和价格下滑的形势下,如何降低生产成本也是各个厂家关心的问题。小巨人公司根据用户这种需求,大胆提出“以立加代替部分卧加,由立加和卧加共同组成柔性化生产线”的解决方案,其经济性并已在多家客户的实际生产中得到验证,为用户节约了大量资金。比如,在发动机缸盖和变速箱壳体的生产线中,在基础的平面铣削和大量的钻孔攻丝等环节中使用立式加工中心,而在凸轮轴孔、气门座圈孔和气门孔的精加工中使用卧式加工中心。在变速箱壳体的结合面以及面上各孔的加工中采用立式加工中心,而合体后加工轴承孔的时候采用卧式加工中心。这种以立式加工中心为主,在生产线中适当配置高速卧式加工中心的方案为客户节约了大量投资。
小巨人公司为客户提供的立式加工中心和高速卧式加工中心组成的生产线已经成功应用在汽车发动机缸盖、下缸体和变速箱壳体及离合器壳体的生产线中,并得到良好的经济效益和社会效益,经受住了大批量生产的考验。此外,在这些生产线中,小巨人公司不但提供了机床、刀具和夹具,而且还提供了包括物流、清洗、打标和检测,甚至还有生产线的信息、管理的软硬件等所有生产线需要的辅助设备和管理软件等整套解决方案。
评论 0
正在获取数据......