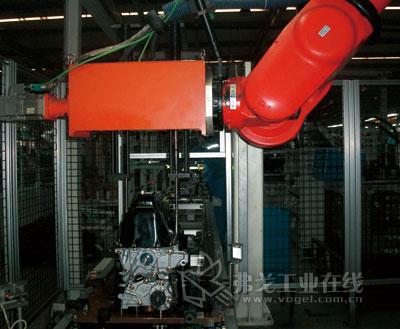
图1 安装在机器人上的两根电动拧紧轴柔性装配发动机油底壳
近年来,随着我国汽车工业的快速发展,汽车品种日益繁多,发动机行业也逐渐加快了新产品的开发力度,不同排量、不同型号的发动机共线装配是未来的发展趋势。
近年来,随着我国汽车工业的快速发展,新产品、新技术的应用,各汽车厂不断开发出新的产品以满足市场需要。汽车品种日益繁多,使得发动机行业也逐渐加快新产品的开发速度,不同排量、不同型号的发动机共线装配是未来的发展趋势。
规划发动机柔性装配线的前提
在规划或改造发动机柔性装配线前,首先需对其进行定位。结合可能共线装配的发动机品种、需求的产量及这些发动机产品可能应用于哪些汽车等情况,确定该柔性发动机装配线的适应产品范围、生产节拍及设备自动化程度等。柔性装配线并不是说可装配的发动机品种越多越好。可靠的柔性装配线应是针对某范围内一些类型品种的发动机实现共线装配。现在很多企业在进行发动机产品开发时,也是在某一平台上进行开发,不同品种发动机的许多机加零部件可以共用,利于产品加工和发动机装配,发动机制造成本也更具有经济性。
装配工序的设计
规划或改造装配线过程中,在进行工艺排序时需要对各工位的装配动作进行分解,评估合理可行的每步作业时间,计算出该工位的生产节拍,对各工位作业内容进行工艺优化重组和合并,既保证一人多工位作业,也能保证整线各工位生产节拍具有相对的平衡性,同时也考虑到员工的劳动强度。整线设备及工装在配置时需符合人机工程,减少人工不必要的动作及行程。在满足可装配发动机尺寸的前提下,手动工位间距不易过大或过小。
装配线的输送、定位一般采用非同步机动滚道或差速链和工件随行夹具相结合的方式。柔性装配线由于产品的多样性,为适应定位基准的变化,一般采用更换工件随行夹具定位块和机床夹紧元件实现共线。也可通过采用工件(缸体)的快速过渡板与工件随行夹具联接方式,不同的工件对应不同的过渡板,通过更换过渡板实现共线。缸盖总成或5C件转运到柔性装配线上,为了提高工作效率,可采用AGV自行小车搬运或机械手抓取搬运,AGV自行小车搬运的产品品种范围更广些,机械手受结构和空间的限制,夹爪不能设计得太复杂。
保证装配柔性的设备选择
1. 电动或气动螺栓拧紧机的配置方式
电动或气动螺栓拧紧机在柔性装配线上,如果使用满轴配置可能会导致装配线柔性差。结合多产品特点,可选用单轴、双轴或少量轴数的合适配置方式,再通过伺服或机械变矩的方式,实现柔性装配产品的快速切换。也可以通过机器人或机械手加电动拧紧轴方式满足柔性装配需要,如油底壳螺栓拧紧,通过在机器人上配置电动拧紧轴,可提高动作效率,并可满足拧紧位置和工艺拧紧顺序的变化要求(见图1)。
2.采用伺服控制数控系统
柔性装配线上,锁片压装、自动翻转机及涂胶机等类型机床采用数控伺服系统控制比较好。伺服控制的优点是定位精度高,行程控制上可实现无级变化。装配生产过程中检测到装配的产品变化时,可以通过自动调用相应程序来满足产品的装配需求。
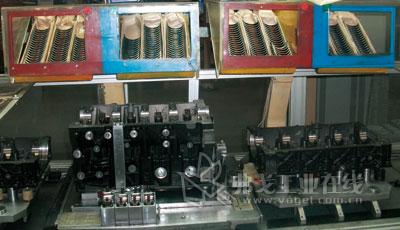
图2 连杆轴瓦防错提示料架
3.试漏检测设备的选择
不同的产品形状,会导致机床夹紧点位置或密封形状结构也不一样,根据产品不同结构可采用多密封工作头或一台机床双工位、多工位来适应不同产品需求,可共用一套控制系统。产品更换时,采用快速更换密封工作头或工作密封工位,既适应产品变化又节省投资费用。装配线上的不同工位对密封检测试漏仪的要求也不一样,根据检测产品控制的泄漏量要求和检测腔的体积等因素,决定选用绝对压力式、压差式还是质量流量式试漏仪。绝对压力式泄露检测仪简单、可靠,不需要平衡参考工件。在精度要求较高的情况下,推荐使用差压式泄露检测仪。在大泄露流量下,推荐使用质量流量式泄露检测仪。
4.采用快换结构
需要通过机械调整和更换机械部件来满足柔性装配的机床,在设计制造时要尽量采用快换结构,机床动作行程上需预留足够的空间,并且在机床控制上要确保换型正确,防止机床误装、误撞。快换结构在设计时,尽量做到外形有明显差异和标识清晰,不易错装。装配线所有工位在混装产品类型切换时,各工位都要有相应的产品信息提示,并且经过人工有效确认后,机床才能执行新批次产品的装配。如在产品切换时,先通过一只工件MASTER随行夹具来进行各工位的告知,MASTER随行夹具所到各工位时,人工检查和确认工位机构是否满足切换产品装配条件,当条件满足后进行按钮确认,机床开始新产品装配工作。在程序控制上自动对每台装配的产品型号进行核查校验,确保装配产品与机床的机械结构对应。
保证装配质量的放错技术
装配防错可分为人工防错和设备自动防错,一般采用人工和设备自动防错相结合的方式较多。人工防错通过建立标准的操作流程和借助一些简易的目视工具进行目视检测,及时发现错、漏装问题。设备自动防错通过程序控制及相应的检测手段,做到不错装或不漏装的目的。
物料防错,是柔性装配线的防错重点,大批量连续生产中,因人员疲劳和疏忽容易出错。防错料架防错是物料防错的重要手段,防错料架有多种方式,一种是在料架的各料盒取料口位置设置一个指示灯,指导操作者取料装机。取料前对应装配产品料盒前的指示灯点亮,当操作者拿完零件之后相应的指示灯变灭;当操作者错拿零件或在没有取安装零件就按下工位放行按钮时,停止器不放行,报警器发出声响,达到警示防错的目的。另一种防错料架是不同产品类型使用不同的料架盛装,在装配的产品切换时,对料架做整体切换(可旋转或移位),通过扫描或料架位置检测方式检查料架是否切换,达到装配产品防错。这种方式适用于产品批次切换频次少或单品种批量生产的柔性装配线,对于完全混线装配的生产线使用不方便。还有一种防错料架采用色标差别来区分,相同类型产品使用统一颜色标识的料架或料盒,取料时直观明显。适用于该工位产品类型少,工件外形差异大的装配工位。根据防错料架的防错级别和形式不同,其投资成本也有较大的差别,主要根据装配产品的特点和结合以后生产管理方式,来选用最适合的防错料架方式。图2中连杆轴瓦取料,通过料盒指示灯自动提示、取料自动检测及不同色标料盒达到取料防错。
设备自动防错技术中,对于涂胶状态检测、发动机总成错、漏装检测,以及装配零件方向检查等工位,可采用图像识别技术,通过图像对比,快速发现问题;具有手动拧紧扳手或拧紧枪工位,操作人员在切换套筒时,按套筒选择器提示选择套筒进行作业,并对拧紧扳手或拧紧枪的每步工作实时计数,在程序上实现按步骤作业防错控制,防止漏拧或错拧;对于自动拧紧机工位,利用拧紧机自身具有的防错功能,通过转矩、角度及屈服点相互的监控关系达到装配防错。位置检测防错,在柔性装配线上应用也是很多,通过光电、限位或接近开关等传感器,检测该工位对应发动机产品类型的机械位置,指导装配或检测错、漏装。
建立数据采集系统
在柔性装配线上建立一套数据采集系统十分必要,配置数据采集和管理服务器,服务器与装配线的每台设备通过以太网实现互联。有些装配线工位采用一维条码或二维码扫描方式读取发动机产品信息,没有其它数据信息载体,工位上装配的数据实时通过以太网的网络系统传到服务器上,但当某网络节点中断时,将出现该节点数据丢失现象。装配线目前使用较多的方式是通过RFID技术的数据载体,在装配线工件随行夹具上安装RFID存贮卡,记录产品型号信息、收集每个工位的作业情况(如该产品在哪些工位进行了作业,是手动完成还是设备自动完成,是否有返修等情况),并存贮关键和重要工位的装配数据(如拧紧机、试漏机及测量机等记录数值)。在该产品装配下线前,数据采集系统将把记录在存贮卡中的所有数据采集到装配线的服务器上,并与工位上实时传给服务器的数据进行校验,确保记录数据正确和完整。RFID技术的优点主要是无接触式读写数据,存贮卡使用寿命长,适应环境范围广,可靠性和稳定性好。装配线的数据采集系统中,集成相应数据管理和SPC统计分析软件,可对柔性装配的每台发动机产品装配数据及状态进行历史数据查询或追溯,并可通过SPC数据统计分析,发现设备或装配件存在的缺陷。
结语
不同的发动机产品实施共线生产,是未来轿车制造工业的发展趋势。发动机柔性装配线需具有以下几方面特点:可共性强,装配产品切换方便,操作简单;设备夹具及支撑等模块化机械结构设计,方便更换变型;具有有效的防错、检测功能;装配数据、状态信息可实现历史追溯。
评论
加载更多