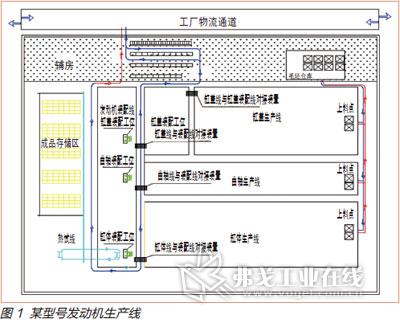
本文以奇瑞公司某型号发动机生产线为例,对缸体、缸盖等自制件和装配线的物流方式进行了研究,提出了整体化、连续化的发动机生产物流理念。
制造业中,物料搬运占有相当大的成本比重,约为30%~40%,据相关资料显示:机械加工领域,每生产1t产品,物料搬运量约50t。因此,为了实现降本增效、提高企业竞争力的目的,就要求从生产过程中想方设法降低成本,精益生产等思想正是在这样的背景下应运而生的。同时从生产管理的角度看,物流搬运也是工伤的高发领域,因此非常迫切需要对物流自动化进行研究。
本文以某发动机工厂5大自制件(缸体、缸盖、连杆、曲轴和凸轮轴,以下简称为“5C件”)和装配线物流方案为例,分别对工厂的整体物流方案和各零件具体物流方式的选择进行研究,提出了整体化、连续化的整体工厂概念。
工厂物流方案选择
发动机制造业是资金、技术密集型行业,提高生产中的物流自动化,不仅可以降低成本、提高效率,还可以减少工人数量,减轻劳动强度。提高物料搬运效率的方法有三类,分别为机械化、高速化和连续化,因此因地制宜,采用合适的物流方案就显得尤为重要。生产物流一般是均衡连续和有规律可循的,产品生产活动在一定时期内是相对稳定的。如发动机在生产计划排定后,在同一班次持续时间内,各件物流需求是动态平衡的,因此可使用连续式物流输送系统。
对于整个发动机工厂,需要根据自制件数量合理规划生产线以及各生产线的内部物流、配送物流和不同生产线间的对接物流等,这其中牵涉因素众多,需要统筹考虑、系统分析。图1所示为某型号发动机生产线规划,产能30万/年,自制件包括缸体、缸盖、曲轴、凸轮轴(位于其他厂房)、装配线以及热试台架。该发动机生产线是一个整体式物流平台,缸体、缸盖和曲轴等与装配线是一个相互连接的整体,充分使用JIT模式,最大化实现零库存,及时响应物流需求,从而尽量减少在制件库存与滞留时间。
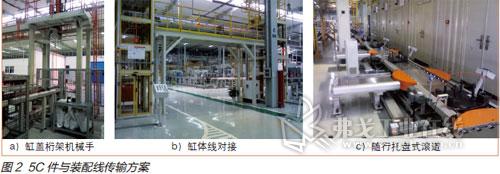
JIT模式要求快速响应客户需要。对于机械加工生产线,装配线是其客户;对于装配线,整车装配线是其客户,当客户提出要求批量供货时,应该快速响应,并及时按质按量供货。目前汽车业广泛采用订单拉动式生产模式,只有订单下达后,相应的生产活动才开始进行,但为了排除设备故障造成的断货隐患,一般厂商都会留有一定量的安全库存,因此发动机下线一般先进入仓储间,5C件生产线也留有成品暂时存放区域。发动机成品占用体积大,且不允许倒置,因此需要采用立体仓库,以暂时存放成品。
物流方式选择
发动机工厂内的零件转运有多种方式,常见的有滚道输送式、桁架机械手式、悬链式和物流小车式等,具体如表所示。前期规划时需要根据不同情况因地制宜,采用最佳的物流方案,不同方案配合使用,发挥最大效率。
1.物流方式合理选择
(1)根据工件材质 工件材质不同需要采用合适的物流方式,保证高效、无损伤的物流快速响应。随着发动机轻量化需要逐步增加,缸体、缸盖框架等越来越多地采用铝件,由于铝件质地软,易造成磕碰与划伤,因此滚道的材质需要重点考虑。为了尽量减少滚道传输造成的损伤风险,缸盖机械加工生产线下线后,在与缸盖装配线对接时,优先采用桁架机械手,如图2a所示,既降低了风险,又提高了效率;缸体机加工生产线与装配线对接,由于缸体为铸铁材质,硬度较高,不易磕碰划伤,可以采用滚道式传输,如有通道或其他设备需要避让时,可采用升降台与滚道配合使用,如图2b所示;缸盖装配线或铝件机械加工生产线采用随行托盘式,可以完全避免传输造成的划伤,同时减少了频繁的定位时间,如图2c所示。
(2)根据工件形状 工件形状不同需要采用合适的载体进行输送。轴类零件由于重量轻,机床类型不同,生产节拍快,因此更适宜采用桁架机械手,从而降低工人劳动强度,减少工人数量,大幅提高生产率,如图3所示。而箱体类零件形状较规则,且重量较大,适宜采用滚道输送。
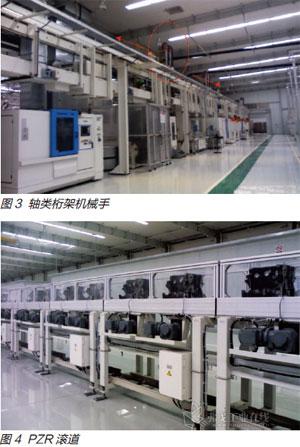
(3)根据质量和精度要求 机加工生产线的粗、精加工单元,可以选用不同的上下料方式,最大程度地节省成本。如缸体缸盖生产线,粗加工单元由于采用柔性化程度较高的加工中心,集中化布置,故机床上下料时,允许采用人工手动上下料;精加工往往由多工位组合专机或珩磨机组成,为了排除人为操作误差、保证加工精度,机床采用抬起步伐式,全自动过件,因此机床必须采用全自动上下料方式。
另外,不同设备间也需要根据实际情况选用合适的物流方式。如加工中心之间采用非机动滚道,机构简单、成本低;加工单元与辅机之间采用机动滚道;精加工结束后,为了防止磕碰划伤,可以采用PZR(Power Zone Roller)滚道(见图4)。
(4)根据需求量、频次 5C件与装配线对零件的需求量、频次不同需要采用合适的物流方式。如5C件生产线一般为三班制,装配线为两班制,那么就要求5C件的输送为连续式的输送;而发动机除5C件外的其他外协件,采用物流小车间断式、定点式配送,从而防止在制件的停滞和积压,实现整个生产线的节拍平衡。
(5)根据单个工件重量 工件重量不同要求的机械化水平也不同。如缸体毛坯较重(约20kg),工件上线、下线需要借助吊具操作,以降低员工操作强度,改善员工工作环境,如图5所示;而缸盖、轴类重量较轻,可以采用人工搬运的方式。
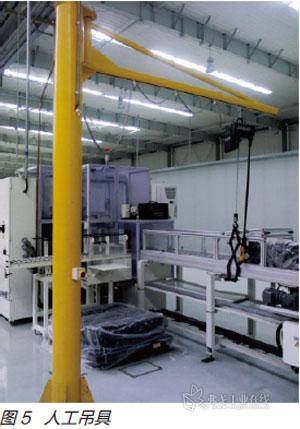
2.综合考虑统筹安排
发动机工厂内物流量大,各零件差异性大,要求从投资成本、运营维护等方面考虑,保证合理高效。如毛坯库房需要尽量靠近机加工生产线上料区域;切屑的收集转运需要路程尽量短,防止抛散;三坐标测量间需要尽量远离外部物流通道,防止振动对精密仪器的影响。
内部生产物流涉及各生产线内部的物料传递与输送,需要合理选用传输载体,优质高效地组织生产。如滚道输送方式与桁架机械手或AGV小车相比,成本更低,故障率大幅下降;物流配送路线合理规划,保证送货路线与返回路线尽量不交叉,降低空载率。
发动机下线后的储存、转运同样需要考虑。发动机成品形状不规则,不允许倒置或倾斜,因此空间利用率低,如合理选用自动化立体仓库,不仅可以提高空间利用率,还可以提高物流的自动化程度,减少误存。
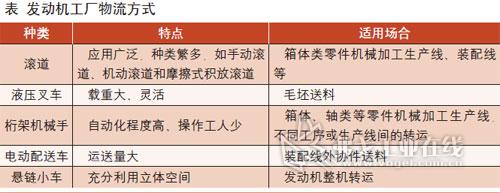
初期规划时需要考虑外部物流配送、内部生产物流组织和发动机成品下线后的存储转运等因素,做到各因素间的兼容和高效,由于发动机生产线的特殊性,生产量大、节拍快,要求物流通畅,因此让原先单独的生产线彼此之间连通,实现无缝对接。通过采用上述整体化、连续化的发动机工厂规划理念,最终实现更高的产能密度。
结语
创新是制造业精益化的必经之路。本文在对发动机工厂整体物流解决方案和具体物流方式等进行了研究之后,提出了整体化、连续化的发动机工厂物流规划理念,相较于传统物流方式,优势明显,推广意义重大,该模式开创了国内发动机整体化工厂的先河。
评论 0
正在获取数据......