本文介绍了拉延模超硬加工的工艺,通过采用超硬加工的方法,解决了淬火后模具的变形问题,提高了汽车外覆盖件模具的制造质量,缩短了汽车模具的开发周期。
生产现状
传统拉延模的制造流程为“底面+结构面”加工→形面加工→钳工初调→淬火→钳工精调。
拉延模经数控机床精加工后,转交给钳工进行研配和调试。钳工借助研配压力机,对模具的凸、凹模间隙进行调整,在调整到合理的状态后进行淬火。淬火使得模具本身内应力变化,造成模具变形。其中,上模底面最大翘曲可以达到2mm,压边圈可达到2.5mm。这时钳工必须重新研配凸、凹模间隙。这样的工艺存在弊病,即钳工必须在淬火后重新研配凸、凹模间隙,增加了钳工的工作量,延长了制造周期,更重要的是模具的实际形状会与数模不符,造成前期CAE数据反馈的失真。
我厂根据前期淬火后的变形及上述各类问题,尝试调整工艺路线,通过淬火后超硬加工的方式来解决淬火变形的问题。超硬加工的难点在于淬火后,超硬加工是否会对工件的硬度造成影响。本文通过跟踪外板拉延模的超硬加工过程,总结出了超硬加工所必须采用的特殊工艺流程,并与NC编程结合起来,完善地解决了超硬加工中的难点。
淬火超硬加工工艺
通过分析问题,并调整工艺路线,力求解决淬火后的变形问题。具体调整工艺方案为“底面+结构面”初加工→形面半精加工→淬火→“底面+台面”精加工→形面精加工→钳工研调。根据调整后的工艺方案,我们逐步分解问题点,逐个解决各个环节的难题。
1.铸件的底面与结构面的加工
底面加工前,首先要在机床上对铸件的变形情况进行初步确认,确认方法为照相。如果底面变形过大,要在侧面标注该处余量的数值,并向钳工及铸造厂家传递和反馈。底面精加工完成后,要打表确认平面度。底面平面度精度要求(以整体侧围模座为例)是0.05。底面加工所用的刀具有:粗加工采用63mm玉米刀或125mm盘铣刀;半精加工采用200mm盘铣刀;精加工采用200mm盘铣刀,各刀具的进给参数如表1所示。
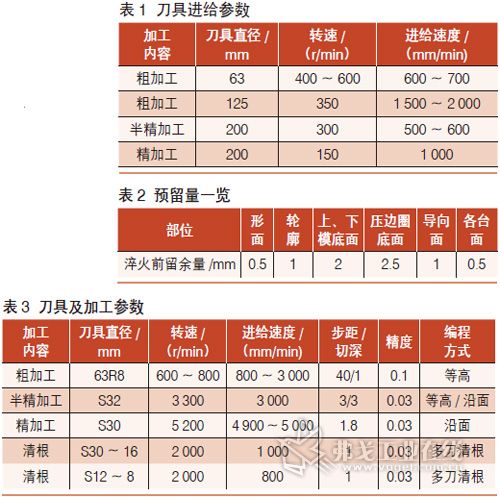
为满足淬火后的加工要求和保证模具最终的闭合高度,形面和底面在淬火前都需要预留加工量,留量的依据是:根据各件的结构和形状不同,淬火后产生的变形大小不一致。具体留量如表2所示。
底面加工完成后要把底面的铁屑和灰尘等吹干净,再次上机床加工前要把底面用抹布擦拭干净。擦拭底面时,要把模座吊在支架上。一次加工前,需要把工作台擦拭干净,通常是把工作台凸起部分用油石磨平,工件直接放在工作台上,工件与工作台面贴死,用塞尺测量底面间隙,底面间隙最大允许值为0.07~0.08。如测量值超出误差,需重新加工底面。
2.淬火前形面的加工
淬火前形面加工的流程为63mmR8刀开粗→S32mm二次开粗→S32mm半精加工→S20~8mm多刀清根。具体的加工刀具与加工参数如表3所示。
3.淬火后的时效处理与检查
工件淬火后,由于变形的关系需要放置一定的周期才能加工,以消除淬火应力。其中压边圈需要放置一天,下模最少一天,上模两天。
在淬火后,精加工前,还要对硬度进行检测。压边圈检测的标准是每隔300mm检测一点;检测的硬度值在50~60HRC范围内为合格。拉延上模和凸模淬火后的检测硬度要求与压边圈相同,但是检测的点在棱线上是每200mm检测一点;在门把手的部位,要增加检测点,间隔50mm检测一点(见图1)。
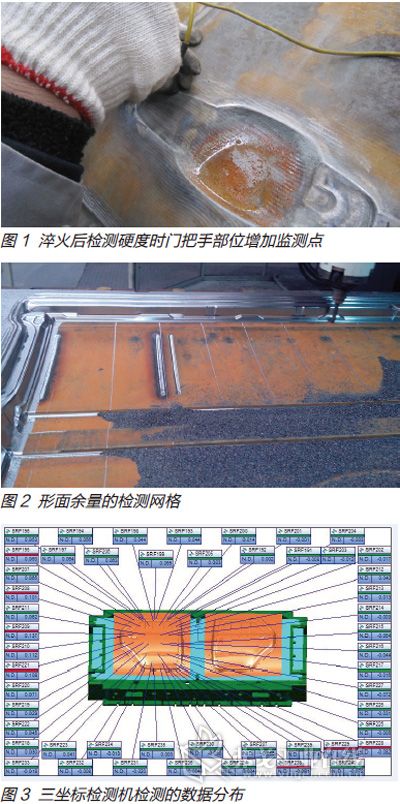
4.淬火后的精加工
淬火失效后,在加工形面前,需要在数控机床上检测底面的翘曲情况。如底面变化未超过预留的数值,则应先加工掉预留量;如翘曲超过预留范围,则根据最大翘曲的数据来加工平底面。
工件底面加工完毕,经过翻转,需要重新在机床上进行形面加工。找正后,用形面检测程序检测形面的变形情况。对形面变形进行检测时,如果检测的变形量不大于0.5~1mm,可直接进行半精加工,如检测超差,需要重新加工底面。检测时,如果形面较陡,必须检测侧面是否余量均匀,如果侧面余量差值过大,要做适当的偏置。检测的方式是:在X方向加工时,每隔300?mm检测,在Y方向上采用同样的方式检测。具体检测的网格的结果如图2所示。
淬火后形面的加工流程为S20mm半精清根→S20mm半精加工→S20mm精加工→S12mm多刀精清根→S8mm单刀半精清根→S8mm多刀清根→S6mm多刀精清根→S4mm多刀精清根,加工参数如表4所示。
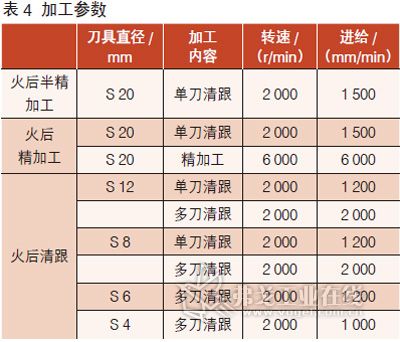
5.超硬加工后的检测
模具形面精加工后,需要由操作者在机床上对形面精度和硬度进行检测;对导向面进行精加工、检测,并将所有检测数据进行标注和记录。然后,用三坐标测量机对形面、导板等进行专检,并出示检测报告。某车门模具的形面超硬加工精度的检测报告如图3所示。
从图中可以看到,形面共检测50个点,其中有8个点超差(红色数值点),合格率为84%,评估加工结果与原来加工模式的检测结果无明显差别。
通过对此套模具的硬度检查来看,硬度基本在50HRC以上,个别区域超过60,各部分软硬不一致,属于淬火不均匀,这些在原先精加工后淬火的模式中也存在。
超硬加工后模具的研调
经过超硬加工后,模具的调试周期相应缩短,由钳工研调两次,变更为淬火加工后一次研调,即可试模。
结语
我们通过三坐标精度检测数据得出,淬火后超硬加工方式的状态与之前加工方式的状态基本一致,加工质量未受到硬度增加的影响。从硬度检测来看,淬火后加工的硬度与加工后淬火的硬度接近。从制造成本来看,数控环节增加工时对应钳工工时会缩减。对于模具的制造质量而言:模具精度和品质有所提升;模具实物贴近CAE模拟结果,为CAE分析提供了数据支撑,提高了CAE的准确性;减少了手工劳动。
评论 0
没有更多评论了