本文详细论述了伺服系统在某公司发动机缸体移载机上的应用,介绍了系统的硬件配置、硬件组态以及软件编程。通过该系统实现了缸体的升降、行走高速运动和精确定位的功能,满足了生产的节拍要求。
目前发动机生产线正朝着高自动化、高智能化的方向发展,许多拧紧、检测单机设备,如自动拧紧机、曲轴回转力检测机、止推间隙检测机和气门间隙检测机等都采用了全自动方式,实现了无人操作,大大提升了产品的质量。但缸体、曲轴等工件的上线,多数厂家还是采用人工作业。这种方式存在许多缺点:该工位的操作工除了需要人工进行条码扫描,还要将转挂缸体与生产线发动机托盘进行对接,这一过程往往需要反复操作才能实现对接准确,操作时间长、操作难度大;采用行车吊挂缸体进行转挂对接,缸体经常掉落,给操作工人身带来了安全隐患;人工进行缸体与发动机托盘对接,对接往往不准确,影响后续工位单机自动工作的稳定性。
解决方案
针对上述缺点和不足,我们设计了一种全自动缸体移载装置,主要由主线举升回转定位装置、刻印线举升定位装置、升降伺服定位装置、行走伺服定位装置、夹紧装置和翻转装置组成(见图1)。电气核心部分采用三菱Q系列可编程控制器Q02UCPU,定位控制采用三菱QD75D2系列定位模块和MR-J3-A系列伺服放大器,实现了发动机缸体从刻印线自动移载到主装配线。该装置主要实现了以下几个主要功能:采用举升定位装置,实现缸体的定位;行走机构采用伺服定位装置,实现水平行走的精确定位;升降机构采用伺服定位装置,实现升降的精确定位;设置举升回转和翻转装置,实现缸体从刻印线到装配线的姿态改变。
缸体移载装置动作流程如图2所示,动作详细流程如下:托盘运送到工位A后,被举升气缸举升到位并旋转90°,此时PLC系统检知托盘方向,如果托盘方向正确、缸体处于水平状态,移载机构迅速移动到缸体上方,下降并夹紧两侧基准夹具定位孔,把缸体提升到翻转位置;移载机构移动向主线B工位,水平回转90°,移动到位后移载机构下降,把发动机放在托盘上,夹紧装置松开,移载机构回到原位,缸体举升机构、托盘举升机构等均回原位,载有发动机的托盘被放行。

伺服系统硬件配置及信号连接
伺服系统配置如表所示。在该系统中,我们采用绝对位置系统,并且伺服电动机都带有机械电磁制动装置,防止停电时位置信号丢失以及升降装置掉落,在初次构建伺服系统时,只需进行一次原点回归,避免从停电到恢复供电时需要重新进行原点回归的动作过程。伺服放大器与定位模块之间的连接信号如下:“CR”脉冲清零信号,主要用于当原点回归完成后,需要进行脉冲清零;“RD”伺服放大器准备好信号,当伺服放大器没有故障,可以正常工作时,输出该信号给定位模块;“PP”和“PG”正反脉冲信号,该信号由定位模块给出,主要执行定位和控制方向的作用;“LZ”编码器Z相脉冲信号;“DOG”近点狗信号,该信号来自机械原点开关;“LSP”正转行程末端,该信号来自正极限开关;“LSN”反转行程末端,该信号来自反极限开关。
伺服放大器与外部装置(如PLC、继电器等)之间的连接信号如下:“ENG”外部紧停信号,当该信号接通时,伺服放大器停止工作;“SON”伺服接通控制信号,当放大器准备好后,接通该信号,伺服放大器处于工作状态;“RES”伺服复位控制信号,当伺服放大器出现故障后,通过该信号复位伺服放大器;“PC”ABS传送模式开启信号,当该信号接通时,伺服放大器处于执行绝对位置读取工作模式;“TL”ABS请求控制信号,当该信号接通时,伺服放大器执行绝对位置读取请求;“ABSB0”ABS发送数据位0;“ABSB1”ABS发送数据位1;“ABSBT”ABS发送数据准备完;“ALM”伺服放大器故障信号,当伺服放大器出现故障时,输出该信号;“INP”伺服放大器定位完成信号,当伺服放大器定位完成后,输出该信号。
伺服放大器及定位模块参数设置
伺服系统要正常的工作,必须对伺服放大器及定位模块相关参数进行正确的设置和调整,伺服放大器需要设置的主要参数如下:“PA01”简称STY,控制模式选择,伺服放大器有位置控制模式、速度控制模式以及转矩控制模式3种模式供选择,本系统选择位置控制模式;“PA06”简称CMX,电子齿轮分子;“PA07”简称CDV,电子齿轮分母。“PA06”和“PA07”两项参数设置很重要,如果设置不当,可能会导致伺服放大器错误运行。需要通过专用的软件对定位模块进行参数设置,设置的主要参数包括单位、每转脉冲数、每转行程和加减速时间等。
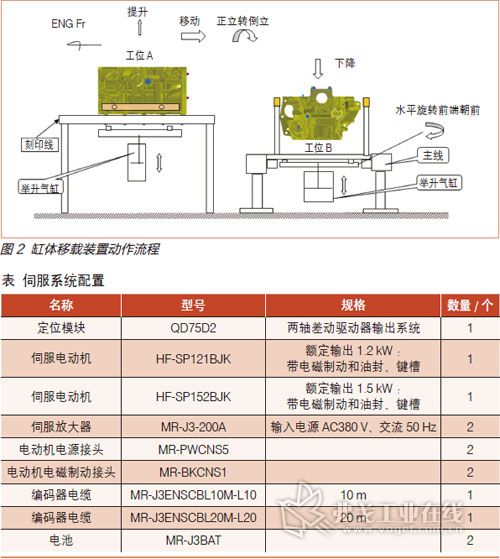
伺服系统软件编程
在该系统中,PLC伺服控制程序主要由初始化程序、绝对位置值获取程序、定位数据设置程序、点动运行程序、定位启动运行程序、原点回归程序、伺服电动机停止运行程序和伺服定位模块故障复位程序这8个程序段组成。
在绝对位置系统中,如果发生伺服开启信号OFF,紧急停止或发生报警,主电路从OFF到ON的过程都必须进行一次绝对位置获取程序,否则系统可能发生误动作。绝对位置传送程序必须严格遵守的时序如图3所示。
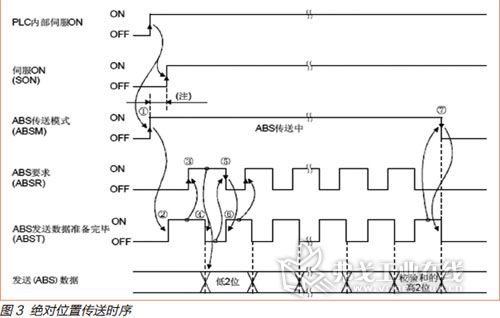
图3中,PLC在内部伺服开启的上升沿,将ABS传送模式(ABSM)和伺服开启(SON)置ON;伺服放大器收到ABS传送模式信号,检测并计算绝对位置后,将ABS发送数据准备完毕信号(ABST)置ON,并告诉PLC发送数据已经准备完毕;PLC收到ABS发送数据准备完毕(ABST)信号后,将ABS请求(ABSR)置ON;伺服放大器收到ABS请求信号(ABSR)后,输出ABS低2位数据并将ABS发送数据准备完毕(ABST)置OFF;PLC确认ABS发送数据准备完毕信号(ABST)为OFF(已经输出ABS 2位数据)后,读取ABS低2位,随后将ABS请求信号(ABSR)置OFF;伺服放大器将ABS发送数据准备完毕信号(ABST)置ON后,准备下一次传送,随后重复3~6的操作,直到完成32位数据及6位和校验数据的发送为止;PLC和校验后,将ABS传送模式信号(ABSM)置OFF,如果在数据发送过程中ABS传送模式信号(ABSM)已经为OFF,ABS传送模式中断。
故障及解决方法
1.伺服电动机不能按指定的位置进行定位
解决方法:伺服放大器电子齿轮参数、定位模块单位、每转脉冲数和每转行程数值设置不正确,更正后,故障排除。
2.伺服放大器出现过载
解决方法:调整丝杠安装;检查电动机抱闸线,发现该线松动,重新接线后故障排除。
3.伺服放大器出现绝对位置读取超时报警
解决方法:检查伺服放大器的绝对位置数据线,发现“ABS0”ABS发送数据位0数据线松动,重新焊接;检查PLC程序,发现绝对位置读取程序时序有误,更正后,故障排除。
4.系统开机运行时,有时会发生升降电动机滑落现象
解决方法:检查程序,发现在伺服开启的条件中未串入电磁内锁互锁信号,修改程序后,故障排除。
5.伺服电动机噪声大
解决方法:在自动调谐无效的前提下,修正“PA09”自动调谐响应参数值。
项目难点和创新点
1.节拍需要达到30s
该套装置动作复杂,互锁条件较多,满足节拍要求是一大难点,也是该项目的成败关键。经过现场的观察,将很多动作进行重叠控制,比如在托盘流出下一工位的过程中,上一工位托盘放行;当托盘搬入时,移载装置行走抓取缸体;当移载装置抓取缸体后,边行走边翻转。
2.缸体、托盘水平检测的实现
该项目中,移载装置要能准确和安全地工作,必须保证托盘和缸体的水平,否则会发生抓取缸体不到位、放置缸体不准确等情况,导致设备的损坏。在该装置中,我们采用两对对射式光电开关来实现缸体水平检测。其原理是用这两对开关水平交叉检测缸体的上表面,当缸体发生倾斜时,其中任意一个开关会发号,系统会报警并停止运行;托盘水平检测同理,同样设置两对对射式光电开关,在托盘的前后两个位置进行检测,当托盘发生倾斜时,其中任意一个开关会发出信号,系统会报警并停止运行。
结语
该缸体移载机在某公司发动机装配线上已调试完毕,使用至今未出现重大停产故障。升降和行走伺服系统正常,升降、行走机构与其他设备动作互锁完整,设备安全得到了有力的保护,整个设备节拍控制为30s。
东风设计研究院有限公司 东风汽车集团股份有限公司
龚淑娟
李峥
评论
加载更多