随着汽车消费市场需求逐渐升级,竞争也日趋激烈,汽车及零部件制造企业面临着质量提升和降低成本双向压力,如何有效保证汽车零部件的加工质量和精度,并在此基础上不断提高加工效率,缩短单件产品的生产成本,成为当前汽车及零部件制造企业最为关注的重点。尤其是发动机制造,因其大批量、高精度、高质量、高稳定性的加工特性,要求发动机加工车间必须不断提高效率,以应对节拍要求。
江淮汽车是国产品牌中的佼佼者,其核心发动机 1.5TGDI 发动机是国内首款自主研发、技术成熟并广泛量产的机型,集国际先进的缸内直喷、废气涡轮增压、双可变气门正时、集成中冷器式塑料进气歧管和油气分离一体式缸盖护罩、静音链驱动、涨断连杆等多项先进技术于一身,具备高功率、高品质、低油耗、低排放、轻量化等特点,与普通发动机相比,它的待速油耗最高可降低30%以上,可使整车节油20%,实现了强劲动力与超低油耗的完美融合。
满足节拍与效率要求
“这些主要是为江淮瑞风S5配套的,它的优势是低转速高扭矩,高转速高功率,这样就使得车辆起步更迅捷,动力也更充沛。平常我们都是开足两班,高效生产。”面对罗列在加工车间内正待进入下一道工序的1.5TGDI涡轮增压直喷发动机的缸体件,任建菊,合肥江淮铸造有限责任公司(以下简称江淮铸造,为江淮汽车股份有限公司控股子公司)车间主任表示,“集团一方面不断进行工艺优化,从工序调整上降低节拍;另一方面,要求从单件成本降低上狠下功夫,从切削加工方面要效益。这对我们来说,是挑战也是机遇。”
江淮铸造的主要业务是为江淮汽车集团提供铸件产品,在同为集团下属的发动机厂的工序调整后,江淮铸造的机加车间承接了缸体的加工任务,主要集中进行缸体的半精加工和钻孔的精加工工序,以实现更严苛的加工节拍要求。据介绍,按照集团高效生产的要求,整体缸体加工的节拍要求是2.5~3 分钟,可是之前由于要兼顾缸体孔加工工序,整体节拍难以达到上述目标,会被延长至5~6分钟。而现在通过工艺改进,由铸造公司完成孔加工工序,整体缸体加工的节拍可以缩短至2分05秒,这在同行里算是非常快的了。
“这道工序以前在集团公司发动机公司加工时,不仅满足不了整体生产线加工节拍,而且成本很高,转入铸造公司加工后,车间建立了专业的加工生产线,在选择刀具时也进行了更严谨的比对。”任主任介绍说。由于是大批量生产,出现一个突发事件可能就会造成产品报废甚至影响整个生产线的节拍,因此只能选择稳定性更好的刀具。目前江淮铸造加工车间全部采用进口先进刀具,为了保证产能,在选用刀具时严格遵循优选耐用度高、切削效率高及使用成本低的原则,并最终确定使用了瓦尔特刀具最具代表性的三个产品系列:瓦尔特-蒂泰克斯(Walter Titex)深孔钻,Walter BLAXX™(黑锋侠)和Tiger•tec®老虎刀片。
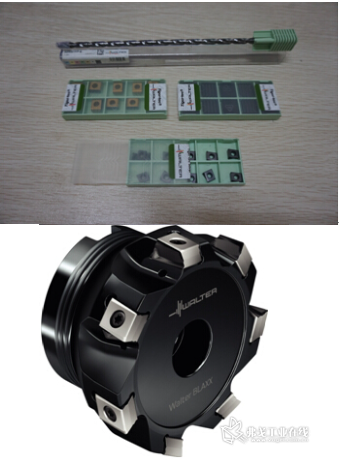
任主任解释说:“我们很早就知道瓦尔特是国际上领先的刀具品牌,在汽车发动机行业有很多成功的应用,而且兄弟公司那里大量的刀具都是用的瓦尔特的产品,口碑很好。在批量用过瓦尔特刀具后,效果的确令我们非常满意。”
在对节拍影响最大的孔加工方面,江淮铸造采用的是瓦尔特-蒂泰克斯Alpha 4 XD系列高效整体硬质合金内冷深孔钻头(简称XD 深孔钻),钻头的直径范围为3~20mm,钻孔深度达到70 x Dc时也能确保最高工艺可靠性并无需退刀。抛光的排屑槽有效保证了深孔加工过程中的可靠排屑,从而确保了加工质量。由于该钻头有4个刃带,在加工斜向出口和贯穿孔时的性能优越,被广泛应用于汽车行业和通用机械行业中。此外,为了满足现代机械加工的效率要求,瓦尔特-蒂泰克斯XD钻头拥有卓越的性能和先进的涂层,与单刃枪钻相比生产效率提高达10倍。
缸体孔加工为精加工,其加工步骤为: 铣凸台毛坯面、钻¢6引导孔、钻¢6深孔(深175mm)、扩M10*1底孔及倒角、攻M10*1螺纹, 一步加工到位。钻孔的时间约一分钟左右, 每小时约加工20台缸体。“目前使用的4支钻头已经钻了7000多个孔,几乎一个钻头可以加工1600 ~1800个孔,对比之前用的另一个知名品牌的钻头最高钻1200~1400个孔,可以说寿命更高。”在一番实际对比过后,瓦尔特产品的优势凸显。据介绍,江淮汽车这款发动机缸体的材料为灰铁250,因为含硅比较多,对刀具耐磨性要求格外高。因此瓦尔特的这款钻头达到这么高的寿命远远超出了行业平均水平。另外,刀具寿命的提升除了降低成本外,也大大节约了换刀时间,可谓是一举两得。
更长寿命 更低成本
在铣削刀具选择上,江淮铸造采用了Walter BLAXX™(黑锋侠)铣削缸体端面,用瓦尔特Tiger•tec®老虎刀片铣轴承孔上的两个端面。
瓦尔特老虎刀片取得的成功有目共睹,业内人士几乎无人不晓老虎刀的威力。多年来,Tiger•tec®切削刀具材料在多个应用领域树立了切削新标准,帮助数以万计的用户实现加工效率的提升。江淮铸造在2012年就已经开始应用老虎刀产品,目前用它来加工缸体的五个面:可以做到一次性加工完成,所有面的加工要求是粗糙度Ra 1.6,公差控制在五丝以内,这样到了江淮汽车发动机工厂那边,只要把端面精铣一下,就可以进入下一道工序了,整体加工节拍得到很好保证。
Walter BLAXX™(黑锋侠)是瓦尔特近年来推出的全新一代铣刀产品,代表了极其坚固同时极其精确的结构方式以及不同寻常的性能和工艺可靠性。瓦尔特技术专家介绍说:“刀片的设计优势是降低了刀刃的成本。由于使用了最新的压缩模技术,并被设计成4个螺旋式的正型切削刃,如此可配备不同尺寸的刀片、不同数量的切削刃。刀体芯部较大的体积保证了加工时的稳定性,并且带来了加工时相对较安静的特点,使加工工艺更加可靠。极少的震动使刀具寿命有了提高。另外,刀片布置在外围也预留了以后可以设计更多切削刃的延伸空间。可以说,黑锋侠完美的结合了刀体和刀片的优势,使得刀具强度增加,耐热、耐磨能力大大提高。另外,新型Tiger•tec® Silver 银虎刀片切削材质的特性也不容小觑。”
“工作人员反映黑锋侠与之前采用的其他品牌进口刀具相比,在同样的加工效率下寿命更长。比如之前1个刃可加工30个缸体,现在是1个刃可加工50~60个缸体,而且刀具本体抗震性有很好的改进。”任主任介绍道。
效率的提高最直接的体现就是生产成本的降低。“现在企业对降低制造成本的要求越来越高,要求我们评算定额成本。不仅仅是单价核算,而是核算到每一个加工步骤上,挑战是很大的。”任主任表示。
任主任对比过,之前平均到发动机单件加工上,这些工序的成本大约在60元~100元区间,而现在核算下来只需20元,每件减少了最低达40元左右的成本损耗。如果按年产10万件计算,那就有400万的费用节省。而实际上,快速发展的江淮汽车已经拥有年产70万辆整车、50万台发动机及相关核心零部件的生产能力。一个小小的工艺调整就能降低约三分之二的成本,这对集团公司而言,无疑是一种成功的创新尝试。
任主任最后介绍道:“瓦尔特通过高性能的产品和服务帮助我们实现了工序上的顺利变化,给我们带来了一定的经济效益和可持续发展的空间,而且,他们会经常主动询问产品的应用情况,并结合自身的丰富经验给予改进意见,这样的合作让人感到非常安心。如果有新的加工任务,新的加工要求,我们非常愿意试用瓦尔特的新产品,也愿意跟他们讨论新的解决方案。”的确,在加工工艺和解决方案的提供上,瓦尔特始终与客户保持着及时、深入的沟通,详细地了解客户的真正需求。凭借“优势技术能力”,瓦尔特正不断助力客户同步实现提升加工效率、降低加工成本的升级目标。
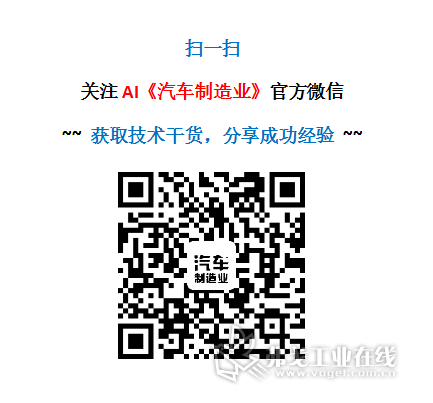
评论 0
正在获取数据......