发动机的制造精度对其压缩比的影响很大,而压缩比又会影响发动机的可靠性、动力性以及经济性。缸体是发动机产品中的核心部件之一,它把发动机的曲轴连杆机构和配气机构以及供油、润滑和冷却等系统联接成一个整体,其制造精度要求高,加工工艺复杂。
缸体加工精度对发动机的性能有着直接的影响,提高缸体加工精度对提高发动机性能有着十分重要的意义。缸盖结合面(简称“顶面”)作为与缸盖配合的表面,其加工好坏直接影响压缩比的变化,可能会导致功率不足、油气泄漏或者燃烧不完全造成排放不达标等。顶面的加工质量要求包括轮廓度、平行度、平面度、局部平面度、表面粗糙度及波纹度等一系列参数。以这些参数展开研究,对于提高发动机的质量具有重大意义。
缸体顶面
某发动机工厂现有生产线使用德国进口的全自动卧式数控加工中心进行顶面的铣削,与磨削工艺相比,铣削在成本和效率上都有着更大的优势。本文从缸体缸盖结合面的加工工艺入手,提出了基于大批量柔性生产线上进行工艺优化的方案;阐述了使用高柔性的加工中心进行顶面铣削将如何提高其加工质量。
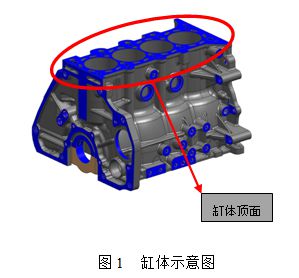
现有加工工艺和加工质量表现
缸体缸盖结合面的现有加工工艺分为两个工序,在粗加工单元OPX1进行粗铣,在精加工单元OPX2进行精铣(当前粗加工后各项特征检测均合格,故本文不对粗加工进行赘述)。OPX2精加工的加工内容如图2所示,图中打剖面为被加工部分。
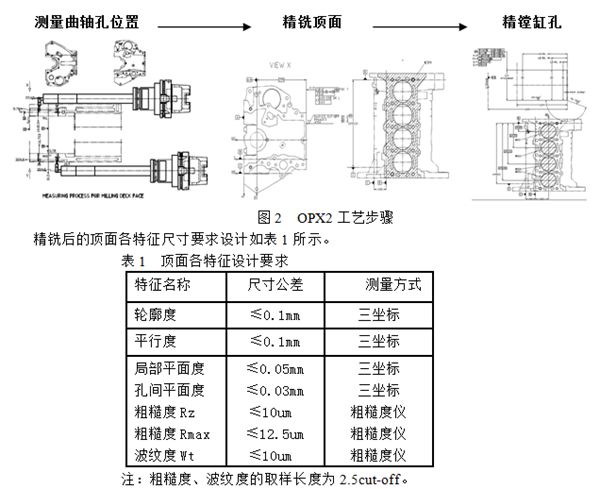
对连续加工的20件进行100%测量,结果如表2所示。
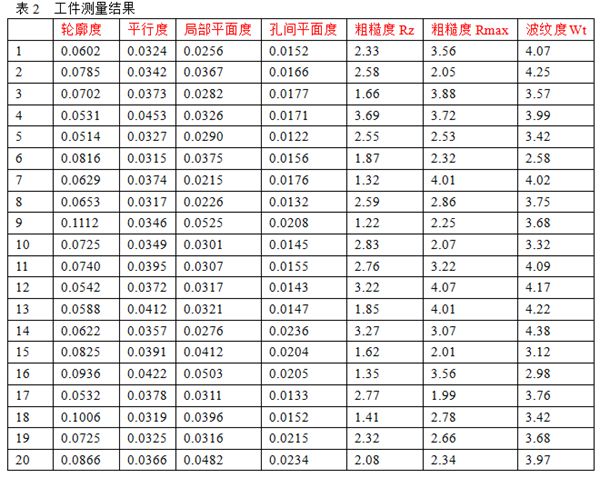
测量结果中,超出公差界限的标识为红色,在公差界限80%以上标识为黄色。上述测量结果显示,表面顶面轮廓度和孔间平面度的加工质量较差,是本文重点进行优化的两个特征。
优化方向分析
缸体零件的加工具有如下特点:主要通过端面铣削来完成平面加工,由于缸体具有壁薄孔多的特点,平面铣削时的变形因素有夹紧力和铣削力;孔系的加工主要是通过以下工艺来完成:镗削、珩磨、钻、铰和攻。
本文从测头精度、夹紧状态、刀具结构以及加工工艺入手,首先分析各因素是否为影响顶面加工精度的主要因素,然后对主要因素进行实验验证。
1.测头精度分析
顶面轮廓度是以曲轴孔中心拟合的理想平面的一个有基准要求的形状精度公差,顶面到曲轴孔中心的距离将极大地影响轮廓度的加工情况。依据此前提及的加工工艺,精铣顶面前会自动对曲轴孔中心进行测量以找正中心,保证距离加工的准确性。对现有机床A/B/C/D的测头测量精度进行确认,结果如表3所示。

精度测量方法为使用测头对机床某固定标准环进行测量,重复50次取最大最小值的差值作为测量精度,D机床进行50次测量的数据如图3所示。D机床的测头精度较差,则其加工距离波动性较大。收集D机床近期的加工距离测量情况(见图4),数据呈现离散分布,波动达到0.0889mm,与论点测头精度影响距离的稳定性相符合。
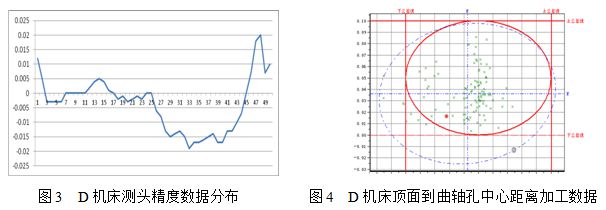
2. 夹紧状态分析
距离加工的稳定性还受加工过程中缸体是否存在移动的影响,如夹紧力不足将会导致切削过程中工件偏移而造成距离的波动。依据机床夹具设计图样(见图5)。油缸的设计使用理论压力为5700N(实际使用存在±10%的波动),则夹紧力P=F×L/8.81,其中L=82mm,P的理论值应为4.77~5.84MPa。测量机床A/B/C/D机床的夹紧力,结果如表4所示。实际测量值均在理论要求范围内,故夹紧力不作为优化考虑的方向。
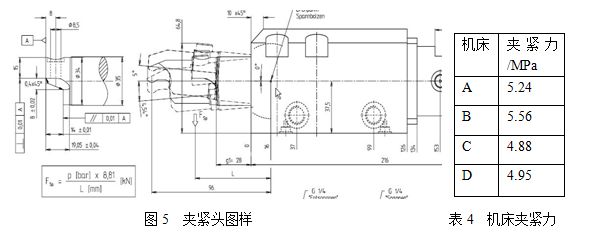
3. 刀具结构及材料
平面度不好首先需要考虑与工件直接接触的刀具,包括刀具的结构及材料、切削参数等,如表5所示。原有生产线使用的刀具为T1,加工时平面度情况较使用T2好。T2刀具因使用国产化的陶瓷刀片,在成本上大大降低,加工参数未发生变化,故本文不计划从刀具方面进行平面度的优化。

4. 测量结果与工艺优化分析
孔间平面度由三坐标进行测量,其扫描路径如图6所示。三坐标的测量路径基本覆盖了顶面的区域,但是测量的点数相对于缸体顶面面积还是十分微小的,大多数边缘、边角的区域都无法探测到。报告中只能获得平面度值最大值的数据,无法知道平面度最大值所在的位置。
2011年,我公司与上海交通大学合作展开2um项目的研究,引进了高精度光学平面测量仪,主要用于平面特征的测量,其功能强大、检测效率高且采样点密度高,可以输出各种平面特征参数,采用激光干涉原理,高度检测分辨率达0.1um,准确度达1um。
将孔间平面度平面度最差的#8号缸体使用高精度光学平面测量仪进行测量,其表面形貌特征如图7所示,可见在缸孔周围平面往内凹陷造成了平面度超差。分析当前加工工艺,在精铣顶面之后进行缸孔的精镗,并且加工倒角,倒角的加工将会造成对顶面的挤压,导致工件的变形令平面度变差。
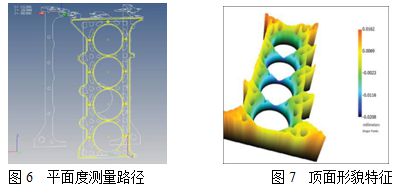
为验证镗孔对顶面平面度的影响,在D机床上进行了如下验证:只精铣顶面连续加工18件缸体,使用高精密光学平面测量仪测量平面度,其平面度FL平均值为0.017mm;完成测量后将工件重新使用D机床进行精镗缸孔并再次测量平面度,FL平均值为0.031mm,平均变差0.014mm。
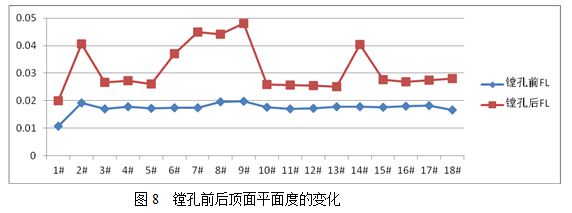
试验结果分析
依据上文的分析,测头的精度及加工工艺将对顶面的加工质量有着重大影响,首先针对D机床加工情况不好,更换了新的测头,重复精度为0.005mm,前后距离稳定性对比如图9所示。
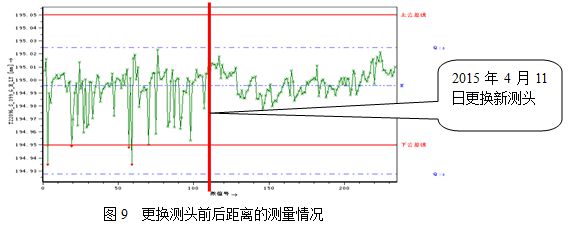
经对比镗孔前后平面度的变化分析,将加工工艺由先铣面后镗孔更改为先镗孔后铣面,前后平面度变化如图10所示。
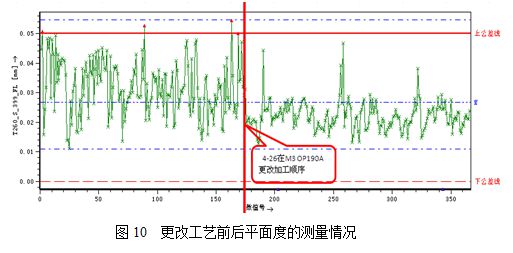
三坐标的测量数据表明,以上两项更改均大大地提高了顶面的加工质量,跟踪更改后3000多个工件的加工测量情况,结果显示未再有超差出现。实践证明,本文提出的两个观点可有效提高顶面的加工质量。
综上所述,我们可得出如下结论:
1. 具有自动补偿功能的设备,在出现加工不稳定时需考虑测量补偿系统的精度是否正常。
2. 加工中工件是否移位依靠夹紧力来保证,需合理地设定夹紧力的大小,以免过小造成夹不紧或过大造成工件的变形。
3. 刀具结构和材质对平面度影响较大,进行新刀具验证时需考虑对质量的影响。
4. 铣面和镗孔在同一工序加工时,需考虑镗孔时对面的挤压变形影响加工质量,合理的进行工艺分配。
评论 0
正在获取数据......