在汽车底盘前纵梁零件的冲压工艺设计过程中,通过对产品工艺性进行评估,科学地进行冲压工艺补充造型,结合CAE分析技术进行模面的数模再造补偿,可以使制件成形质量满足要求,并有效地避免零件后期调试的回弹、扭曲缺陷,减少模具调试次数,缩短模具制造周期和制造成本。
汽车前纵梁产品在车身结构中承受着整车的有效载荷,是整车承受冲击力、碰撞力的关键部件,决定着整车的载重量,关系着整车的安全性能。为了减少整车质量,大部分主机厂都采用屈服强度较高的钢板,厚度相对于“五门一盖”零件较厚,既能满足车载强度,又能满足车辆轻量化的要求。纵梁零件具有形状复杂、外形不规则、板料厚、屈服强度高以及成形后翘曲、扭曲和回弹严重等特点,因此,需针对前纵梁产品的缺陷进行预测,提前对可能出现的缺陷采取对策。但如何有效利用工艺手段克服上述不足,保证产品质量,已经成为整个模具行业技术研究的重点,并对实现汽车轻量化、节约能源、保护环境和提高安全性能等具有重要意义。
本文以某公司载重货车的左/右前纵梁为例,介绍了其冲压工艺设计及回弹扭曲控制要点。通过CAE模拟仿真技术优化冲压工艺造型设计,使之成形更加充分;提前预测产品和工艺造型缺陷,并对回弹、扭曲进行补偿;实现数模再造技术,确保产品最终质量;避免后期模具调试靠钳工打磨、修抛解决缺陷;减少模具实际调试次数,进而达到缩短模具制造周期、降低生产调试成本并提高企业生产效能的目的。
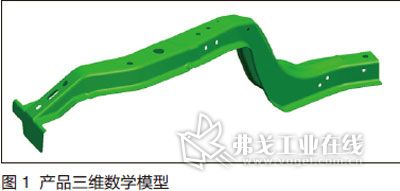
产品工艺性设计
1.产品材料属性
左/右前纵梁(见图1)材料在车身结构中承担碰撞安全、行驶稳定性等作用,其材料属于比较典型的加磷高强度冷连扎钢板,材料属性如表所示。
2. 产品工艺性评估
该产品是比较典型的载重货车前纵梁零件,形状复杂、正面侧面均为S形、落差大。在零件冲压成形过程中,由于应力、应变的不均,该产品极易产生回弹、翘曲等缺陷,是整个汽车模具行业冲压工艺规划设计中的难点。
3. 工艺补充造型
前纵梁零件的冲压工艺造型对于零件的最终品质至关重要,也是汽车模具开发的核心技术之一。就产品凸缘面来说,通常有以下三种造型方案:
(1)直接将产品凸缘作为拉延压料面,后工序修边、整形和冲孔。这种造型方法简单、成形深度较浅,但其存在的不足是,材料流入不均匀,易产生成形不充分、压料面不平等缺陷。
(2)把产品全部作为凸模成形,拉延出全部产品形状,后工序修边、整形和冲孔。这种造型方法的不足是,成形深度大,易开裂且材料利用率较低。
(3)左边局部凸缘面在凸模成形,右边形状较深的部位采用凸缘做压料面,后工序修边、整形和冲孔,如图3所示。这样的优点是零件全部拉延成形,刚性好且变形小,可提高材料利用率,并有效应对零件回弹、扭曲和凸缘翘曲问题。
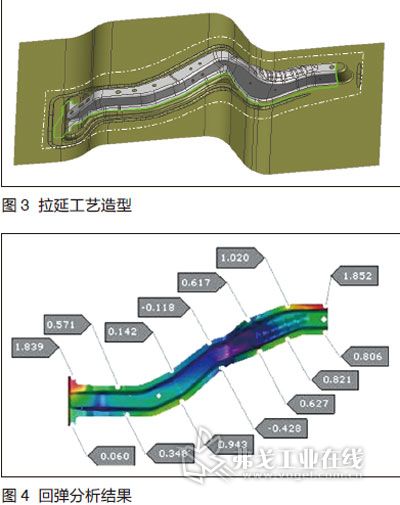
4. CAE分析
(1)回弹分析
前纵梁零件的常见缺陷主要是回弹和扭曲,此时常用的CAE拉延成形性分析已不能满足需求,为更准确地对零件缺陷进行预测,需要对零件进行全工序分析,即按照“拉延—修边—整形”的工艺流程对零件进行回弹分析,如图4所示。此分析应在拉延稳定性分析判定合格后进行,并依照检具状态设定支撑点和夹紧点,否则会影响回弹分析的准确度。
(2)回弹补偿
对零件进行回弹补偿应在零件的工艺造型和工序最优的状态下进行,以获取最佳的零件状态和相对小的补偿量。综合之前所述方案和回弹分析的结果(最大回弹量为1.8mm),可在此基础上进行回弹补偿。
对于回弹补偿,我们可借助CAE软件的自动补偿功能实现,通过设定补偿工序、补偿区域和过渡区域,软件可自动对比基准数模并进行型面补偿和回弹分析。这里要注意的是:分析参数的设置应与原分析状态一致,这样才能保证回弹补偿的准确性。此补偿可循环进行直至零件达到合格状态。对于简单的内板零件可以直接应用补偿后的数模,外板及重要零件不建议直接应用。
此前纵梁经过两轮回弹补偿后达到合格状态(型面公差±0.5mm),我们参照软件的补偿数值,利用NX4软件进行数模再造,分别体现补偿后的各工序数模,如图5所示。
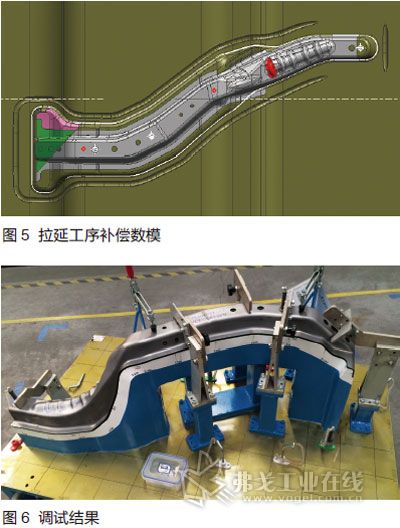
调试与验证
通过科学的工艺补充造型,紧密结合CAE全工序分析、回弹补偿和数模再造等核心冲压工艺技术的应用,该产品的首次调试效果基本符合预期,仅因毛坯偏置出现一端局部开裂,调整坯料定位以及压边力后予以解决;经检测制件回弹、扭曲等缺陷得到有效控制,与CAE分析结果基本吻合。该件通过上述技术的应用,提高了最终产品的综合质量,减少了试模次数,节约了人力、材料和设备成本,为后序模具型面的精细化研配提供了基准,确保了首轮试装件的及时供应。调试结果如图6所示。
首轮样件合格率检测报告显示,产品的基准合格率达100%,型面合格率约80%,孔合格率在80%以上,切边合格率近100%。
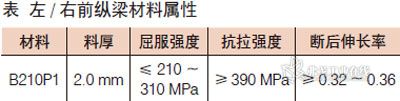
结语
汽车纵梁产品模具的开发相对于“五门一盖”来说是一个全新的专业,因产品本身结构复杂,具有无规则、高强度和板料厚等特点,易造成后期调试零件的扭曲、回弹缺陷。如何寻找合理解决措施是国内外行业面临的一项重大课题。CAE成形分析、回弹补偿是一个反复模拟、逐渐逼近的过程,每一次模拟后的解析和采取的具体工艺措施是CAE模拟技术的核心,逐渐形成企业的核心经验数据库,为汽车纵梁零件模具的开发提供了重要指导意义。
评论 0
正在获取数据......