我公司的发动机缸体3线,铣削铸铁缸体采用数控专机和加工中心,自2009年投产以来,在OP20、OP30、OP40和OP180等铣削余量大的工序,普遍存在着刀具寿命低、加工质量不稳定现象,频繁换刀严重影响正常生产。在OP20序,加工300件就需要停机检查更换5~6片左右的崩刃刀片(见图1);在OP30序和OP40序,新刀加工80~100件后就会出现刀具急剧磨损、掉渣、尺寸不合格和振纹等质量问题;在OP180序,铣刀加工60~100件时就会出现零件掉渣严重,只能更换刀具。
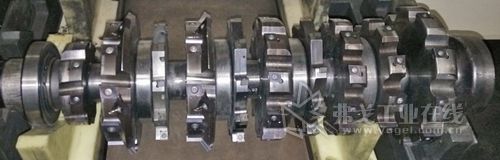
缸体3线铣削刀具的消耗是加工相同零件的缸体1线(自动线)的两倍,问题十分突出,严重影响正常生产和制造成本,必须重点解决。
初步分析问题原因
1.缸体3线和缸体1线的比较
缸体3线和缸体1线加工的产品相同且工艺接近,但设备、刀具等选型存在着较大差异。缸体1线为刚性自动线模式,采用步伐式输送、多工位加工、集中供应切削液和地沟排铁屑。缸体3线采用的是数控专机和加工中心组合起来的具有一定柔性的生产线,专机带B轴,可加工多个面;集中供应切削液,采用提升泵将单机的铁屑和切削液一起泵回到回液主管道,返回切削液中心进行处理。经对比分析,铣削工艺系统刚性方面缸体1线较缸体3线要强,由于刀具结构和供应商不同,所以我们初步分析认为,工艺系统刚性和刀具是问题产生的主要原因。于是,确定在刚性、刀具和加工参数方面进行改进。
2.改进工艺系统的刚性
工艺系统刚性对刀具寿命影响十分大,刚性不好造成刀具寿命低的事例比比皆是。缸体3线加工中心和数控铣的主机采用标准设备,在选型和设计时,重点考虑了刚性问题,采用数控铣专机粗铣就是为了提高刚性满足生产效率的要求,数控铣的主轴轴承直径达到240 mm,B轴为齿盘式630 mm×630 mm数控转台;加工中心铣削选用刚性足够的HSK100机械主轴和630 mm×630 mm数控转台,并对刀具、夹具等系统进行了加强,因此要再进行大的改进提高刚性比较困难。通过分析,我们判定OP30、OP40工序的夹具刚性较差一些,还有改进空间。于是,我们首先在切削力最大的OP40工序进行夹具改进试验。
缸体3线OP40工序的加工内容是粗铣缸体的缸盖结合面和正时面,设备为630 mm×630 mm齿盘式数控转台的数控铣削专机,夹具安装在回转台上。改进前的现状是,加工80~100件后刀具出现微崩刃、急剧磨损,切削力大,造成加工的零件在B轴方向偏转,尺寸严重超差,更换新刀片加工后工件尺寸合格。为提高系统刚性,减少B轴方向的偏转,我们对夹具进行了重新设计,把夹紧机构支座固定在机床底座上,在夹紧支座上增加零件辅助支承,使设备床身承担部分切削力,改变所有切削力都由回转台承受的现状。改进完成后进行试验,刀具寿命略有改进(提高20件左右),刀具微崩的情况还是存在,刀具出现急剧磨损后,加工面的尺寸还是存在超差(切削力过大)。
OP40工序夹具刚性改进的试验证明,缸体3线OP40工序铣刀寿命低的主要原因不是工艺系统的刚性问题,所以我们就没有再继续改进OP30工序的夹具。
3.改进刀具的刀片形状及材料
(1)改进刀片刃型 由带前角的刀片改为0前角的刀片,提高刃口强度。试验证明,刀具寿命略有提高,但微崩、急剧磨损的情况还是存在。
(2)改进刀具材质 我们试验了多家供应商的多种材料的刀片,刀具寿命有一定的差别但寿命都不是很高。虽通过优化材质,刀具寿命有所提高,但都没有达到预期的要求:OP30/40工序加工不到200件还是存在急剧磨损、尺寸不合格和加工掉渣等问题;OP180加工中心刀具寿命由60件提高到80件,刀具磨损、加工零件掉渣严重。
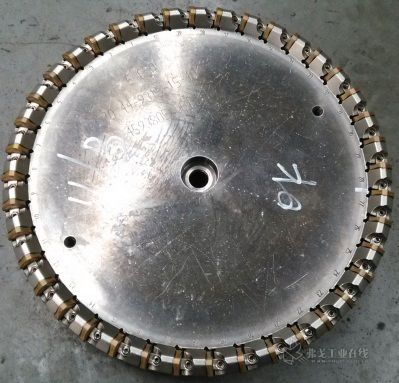
4.优化加工参数
为查清问题的根源,我们采取不考虑节拍问题,在OP40工序进行降低进给速度和转速的试验。
(1)工艺设计 如图2所示,刀具直径315 mm,40个刀片,转速140 r/min,进给速度1 600 mm/min。
(2)工艺试验 转速降低到100 r/min,进给速度减低到800 mm/min。
试验结果显示刀具寿命无显著改善。试验证明,目前的加工参数不是刀具寿命低的主要因素。
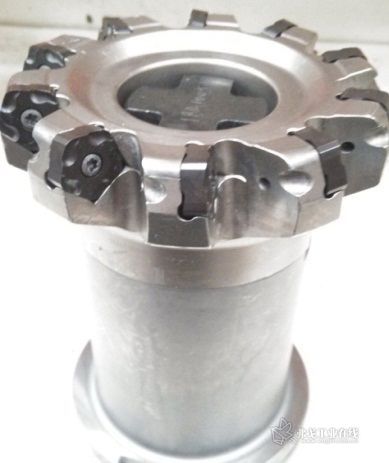
深入分析,解决问题
1.进一步分析
通过前面的探索、试验,刀具寿命普遍偏低的主要原因并没有找到。我们继续重点跟踪分析OP40工序刀具的整个磨损过程:刀具加工到90件时状况很好没有磨损,但之后出现微崩刃和快速磨损,仅能加工20件左右就不能使用。刀具出现微崩刃,切削状态恶化,刀具寿命迅速降低,过早的出现微崩是导致刀具寿命低的重要原因,因此,
解决微崩刃问题是我们提高刀具寿命的关键。
刀具微崩刃影响因素很多,刀具的结构、材质,加工的零件材质、缺陷,工艺系统刚性,切削液(刀片的温度发生剧烈变化),切削力(冲击、大小)等。前期的试验已经验证刀具、工艺系统刚性等都不是导致刀具寿命低的主要因素,于是切削液对刀具的影响成了我们研究的重点。
比较两条生产线,缸体1线采用地沟排屑,刀具冷却切削液流量大,冲屑流量小;缸体3线采用的是通过提升泵和管道排屑,设备内冲屑消耗的流量较大,虽然目视所有刀具冷却切削液水流量不小,但相对1线流量要小很多。铣削刀具刀齿多,粗加工余量大,铸造表面硬度高,加工时切削温度较高,如果冷却稍不充分就会出现温度剧变的情况,对于硬质合金刀具来说,温度的剧变承受能力差,容易出现崩刃现象。特别是刀具磨损或微崩后切削力更大,加工区温度更高,切削液不充分造成的温度剧变更严重,形成恶性循环,就会使刀具急剧崩刃和磨损,同缸体3线铣刀目前出现的刀具急剧磨损的现象比较接近。不同厂家刀具材质及涂层不同,温度的剧变承受能力也有差异,但目前还没有能承受温度剧变的硬质合金和超硬材料,所以,必须要保证刀具充分、均匀的冷却,排除温度变化对刀具寿命的影响。
2.工艺试验
对于缸体3线的设备,大幅增加切削液流量十分困难,必须改造管道系统和提升泵,但改造周期较长。为确定切削液问题是否是刀具寿命低的主因,我们首先在便于实现干切的OP180工序的加工中心上进行干切工艺试验,采用先完成干铣加工工步后进行其他湿切加工工步的干湿结合方法,避免了切削液冷却不充分造成的铣刀温度的骤变,同时又保证了夹具、设备冲屑干净,不会造成设备排屑不畅的问题。试验结果显示,刀具寿命由以前的
60~100件提高到了300件,证实了切削液冷却问题是缸体3线的铣削刀具寿命低的主要原因。OP180工序的刀具如图3所示。
3.干切改造
为解决问题,我们对缸体3线铣削余量大、刀具寿命低的铣削工位(工步)进行改造。
(1)对采用加工中心的OP10和OP180工序,修改切削液控制程序,实现先干铣加工,后进行其他湿切加工,干、湿加工结合,输送时冲洗夹具和零件,保证零件、夹具及设备的清洁。
(2)对于OP20、OP30和OP40工序的铣削专机,改进切削液管道和控制系统,采用干铣加工,铣削加工时,加工区切削液关闭,设备内其他区域继续冲屑;输送零件时,加工区切削液打开,冲洗零件、夹具上的铁屑,保证零件、夹具和设备的清洁。
4.改进效果
通过改进,缸体3线的铣削刀具寿命得到大幅提升,崩刃情况改善十分明显。
OP20工序组合铣刀,安装有108片刀片,改进前加工300件就要停机检查、更换崩刃刀片,勉强加工到1 500件,须换下崩刃的刀片多达25片。改进后,刀具加工到2 000件,很少出现刀片崩刃情况,降低了刀具消耗,减少了换刀时间。换刀情况的改善如表所示。
改进后,铣削刀具寿命达到或超过缸体一线的刀具寿命,刀具消耗降低8.5元/件,按年20万产量计算,节省刀具费用170万元,并且减少了停机换刀时间,产生了良好的经济效益。
结语
刀具寿命低是个复杂问题,只有对影响因素进行逐一排除,才能找到真正的主要原因。本文中的案例让我们清楚地认识到,切削液有助于排屑,保证加工质量,提高刀具寿命。但当其不能充分冷却刀具时反而会降低刀具寿命,影响加工质量。
为此,在铸铁件的铣削中,特别是余量大的粗铣,采用切削液加工时必须要有十分充足的切削液流量,才能保证刀具的充分冷却。针对本案例中的问题,采用干铣加工,切削液仅用于冲洗和排屑,既避免了温度剧变对刀具的影响,又简单地解决了零件、夹具和设备的清洁和排屑问题,是一个很好的选择。
评论 0
正在获取数据......