高精度导条专用刀具在加工长孔类零件时具有较好的稳定性并能获得更好的加工表面,在缸盖凸轮轴孔的加工中应用广泛。本文基于机床切屑液循环系统,分析了多种条件下对导条专用刀具的影响,为加工缸盖凸轮轴孔提供了参考。
表面粗糙度及机床过滤系统简介
1. 表面粗糙度的定义
表面粗糙度是指加工表面具有的较小间距和微小峰谷的不平度。其两波峰或两波谷之间的距离(波距)很小(在1 mm以下)。它属于微观几何形状误差,表面粗糙度越小,则表面越光滑。粗糙度在机械配合中对耐磨性、稳定性、疲劳强度、耐腐蚀性和密封性等有着重要影响。
本研究运用英国高精密粗糙度测量仪Taylor i120对凸轮轴孔表面粗糙度Ra进行分析。Ra的计算公式如下

在取样长度I内,Ra是所有纵坐标值的算术平均值。Ra对应于条件AA(算术平均)和CLA(中心线平均)。
从图1所示的Ra测量原理可知,加工表面存在刮痕时会导致Ra超出控制范围,因此研究并控制刮痕的产生是降低Ra的关键方法之一。本文也将重点讨论刮痕的产生原因及控制方法。
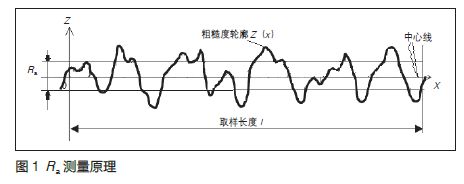
2. 机床循环过滤系统
以MAG机床为例,如图2所示,循环过滤系统的组成如下:
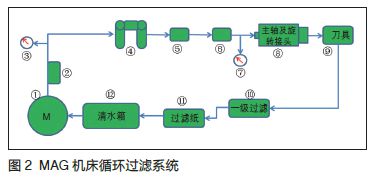
(1)高压泵 提供压力和流量,将清水箱中的切屑液送往高压滤芯;
(2)比例溢流阀 通过开关量大小来控制冷却回路压力;
(3)机械压力表 显示高压泵出口压力值;
(4)高压过滤芯(三级过滤) 过滤切削液中的杂质(过滤精度为60 mm);
(5)流量监控传感器 监控回路所通过的切削液液体流量;
(6)高压截止阀 控制高压切削液的通断,其由气阀控制接通或断开;
(7)压力传感器 监控通往主轴高压冷却的压力;
(8)旋转接头 实现外部管路与主轴旋转芯轴的密封连接;
(9)刀具 切屑液使用及加工;
(10)一级过滤 过滤切削液中的铝屑(过滤精度为0.35 mm);
(11)过滤纸(二级过滤) 过滤切削液中的杂质(过滤精度为40 mm);
(12)清水箱 切削液水箱。
循环工作基本原理:切屑液与铝屑的混合物经过三级过滤进行循环(即一级过滤、过滤纸和高压滤芯),每一级过滤系统都至关重要,如过滤系统存在缺陷,则进入主轴参与冷却润滑的切削液会带入大量杂质。
凸轮轴孔表面粗糙度影响因素研究
1.刀具在主轴上的跳动影响
以MAPAL导条专用刀具为例,在加工中,要求刀具在主轴上的近端跳动≤2 mm,远端跳动要求≤5 mm,而刀具的跳动值可通过刀具上的螺栓进行调整,跳动合格与不合格的刀具分别加工验证试验结果如表1、表2所示。通过表1、表2可知,刀具在主轴上的跳动对凸轮轴孔表面加工质量有着巨大影响,从图3也可以看出表面加工质量存在差异。
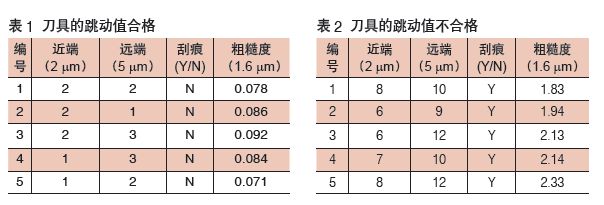
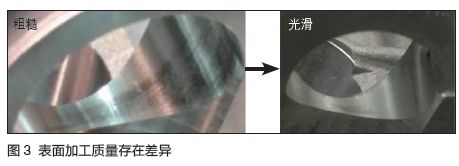
综上所述可以得出结论:刀具在主轴上的近端及远端跳动越小,越能获得较好的表面粗糙度及表面加工质量。
2.过滤系统颗粒度影响
当刀具在加工两个以上的孔时,为了保证同轴度,必须保证刀具为同一方向进入孔内加工,这时第一个孔作为加工第二个孔的导向孔,就要保证刀具导条既不能与孔直接接触摩擦,又不能使导条与孔间隙过大导致同轴度超差,因此需要在导条与孔之间形成一层切屑液油膜。此时,只需要在导条上与孔的相对位置开切屑液槽即可保证为主轴持续提供切屑液。图4所示为导条加工刀具示意图。
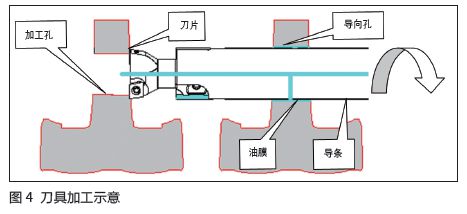
如图4所示,加工孔时导条与导向孔间形成油膜并相对运动。保证刀具跳动在合格范围内时,切屑液颗粒度对孔表面加工质量会产生重要影响。由机床润滑循环系统的构成可知,进入主轴前切屑液经过三层润滑过滤,保证加工中切屑液颗粒度在控制范围内,进入主轴前的第三道过滤(即高压滤芯过滤)。假设滤芯粘附铝泥会影响最终进入主轴切屑液的颗粒度,最终会影响加工表面质量。对比验证结果如表3所示。
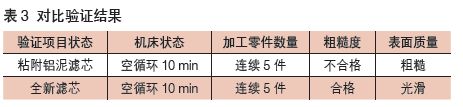
结语
本文运用对比验证方法,研究了导条刀具在加工长孔类零件时的运用以及提高加工表面质量的方法,即降低刀具在主轴上的跳动及降低切屑液颗粒度来提高表面加工质量的方案,从而降低了工件加工时的报废率和生产成本,帮助企业提升了产品竞争力。
评论 0
正在获取数据......