机器人视觉引导在焊装车间的应用
在某商用车焊装车间,库卡机器人结合ISV视觉产品形成的机器人引导定位,可以完成从EMS小车上抓取侧围的任务。应用机器人视觉引导可有效控制系统稳定性和系统故障率,同时节约成本。随着视觉引导技术的发展,可以更好地满足装配需求,保证产品的质量。
在汽车生产焊装车间,使用传统机器人抓手时需要将被抓物料放置在高精度定位工装上,一般要求定位精度达到±1mm。当前合资车企和自主车企的自动化线体视觉引导系统已经大规模投入使用,见表1。利用机器人视觉引导系统抓件,很好地解决了待抓取物料的高精度定位问题,大大简化了物料上件器具、物料输送EMS等工装的设计,解决了多车型柔性化上料工具共用的难题,为实现无人AGV智能物料配送奠定了基础。
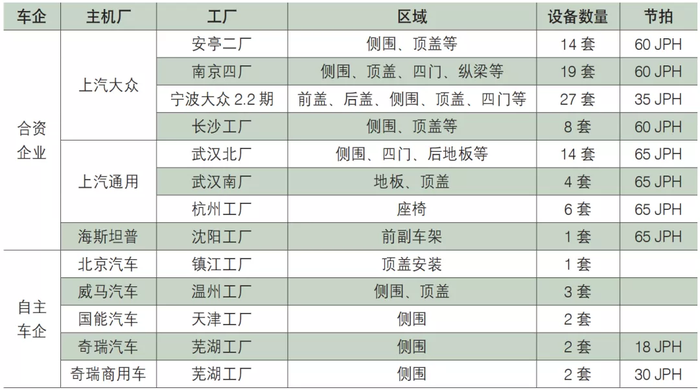
机器人视觉引导系统就是用机器代替人眼来做测量和判断,对目标进行摄像拍照获取图像信号,传送给图像处理系统,转换为数字化信号。图像处理系统根据数字化信号进行运算获取目标特征,根据逻辑判断的结果来控制现场机器设备的动作,进行各种装配或者检测报警缺陷产品。
如图1所示,经过标定的视觉引导系统对目标零件拍照,利用目标图像上至少4个非共线特征点的图像坐标,确定目标与相机间的相对位置。利用目标上特征点间的几何关系表示物体的结构和形状,并通过提取物体特征在模型和图形之间建立起对应关系,计算出物体空间位置的坐标后,机器人按照计算空间坐标位置进行取件。
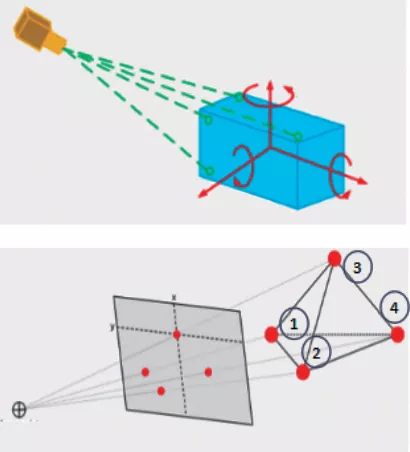
机器人视觉引导系统主要由机器人、视觉系统控制柜和测量传感器三大部分组成。
视觉系统的主要构成分为五个部分:照明、镜头、相机、图像采集卡和视觉处理器。其中拍照摄像设备、图像传感器、视频信号数字化设备及视频信号处理器在应用上不断推陈出新,技术上从2D到3D正在不断进步。
利用相机拍照,结合零件自身的三维信息,实现零件相对于初始状态的6个自由度(3个方向位置和3个方向旋转角度)精确定位;利用3D引导X、Y、Z位置偏移及角度偏转;采用结构紧凑、体积小的传感器;移动式安装在机器人6轴工具上,固定式安装在工位区域固定支架上;为节省节拍,推荐相机配置3个,满足1次拍照获取所有所需特征点数据。
系统功能相机拍照应实现零件6自由度精确定位;系统应用:侧围料箱取件、放件(层叠、非层叠)以及EMS小车上取件等;拍照距离:500~800mm;拍照范围:700mm×70mm~1000mm×1000mm;容差范围:±70mm的位置偏移、±5°的零件偏转;引导精度:±0.5mm;测量时间:≤2s;测头尺寸:φ100mm×200mm;通信接口:总线(Profinet、Profibus、EthernetKRL及EthernetIP);测量特征:孔(圆孔、方孔及腰孔等)、角点及边线。
相机:500万像素单色相机;1inchCMOS;千兆以太网(GigabitEthernet),转换速率:1000Mbit;光源:蓝光,传感器内置一个光源,同时传感器可以驱动一个外置光源;线缆:配套2根机器人专用高柔线缆。
方案1:相机安装在机器人抓手上,机器人与距离传感器通过模块相连,实时读取距离值。视觉引导系统与机器通过现场总线相连。
具体步骤:机器人从等待位置运动至取料箱前方某一固定安全位置,机器人沿料箱放件方向直线运动(目标点设置在料箱最后一个零件后方),同时机器人实时读取距离数值。当机器人读出距离值为0.8m(机器人程序设置)时,机器人运动速度降低至40%;当机器人读出距离值为0.75m(机器人程序设置)时,机器人运动速度降低至10%;当机器人读出距离值为0.7m(机器人程序设置)时,机器人运动停止。视觉系统控制相机对零件拍照,计算零件偏差,机器人根据计算结果修正取件轨迹,按修正后的轨迹进行取件。
方案2:当相机安装在固定支架上时,机器人就不需要再安装距离传感器。机器人运动到安全距离后,启动视觉系统控制相机对零件拍照,视觉系统计算零件偏差,机器人根据计算结果修正取件轨迹,按修正后的轨迹进行取件。
利用3D激光传感器测量零件特征,实时构建零件坐标系,精确定位待装配零件及车身相对于初始状态的6自由度偏差(3方向位置及3方向旋转角度),同时考虑被装配件与车体的偏差。通过3D引导X、Y、Z位置偏移及角度偏转;移动式安装在机器人6轴工具上,固定式安装在工位区域固定支架上。
单车型标配为8个传感器;利用地上两个固定式传感器测量左右侧围A柱上主定位孔,检测侧围X向定位;采用顶部四个纵向传感器测量车顶开档边界,检测车顶开档Y、Z向偏差及三个方向偏转;顶部四个纵向传感器配合两个横向固定式传感器监测顶盖X、Y、Z向偏差及三个方向偏转;顶部四个纵向传感器配合两个横向固定式传感器监测顶盖装载后的左右间隙及位置。
系统功能:激光传感器测量,实现6自由度精确定位;系统应用:四门两盖、车顶最佳匹配装载;拍照距离:350~1200mm;拍照范围:60mm×80mm;容差范围:±25mm的位置偏移;引导精度:±0.5mm;测量时间:≤2s;测头尺寸:76mm×76mm×L(L由工作距离而定);通信接口:总线(Profinet、Profibus、EthernetKRL及EthernetIP);测量特征:孔、角点及边线。
相机:130万像素单色相机;1/1.8inchCMOS;千兆以太网(GigabitEthernet);转换速率:1000Mbit;光源:蓝光,传感器内置光源;线缆:配套1根机器人专用高柔线缆。
车身进入工位后,传感器检测车身位置及车顶开档。抓手抓取顶盖后,传感器检测顶盖位置状态。根据测量结果计算出车顶需要纠正的偏差,实现精确装载。传感器检测顶盖和车身匹配状态,如果位置偏差较大,需重新引导机器人进行二次精确装载。
标定的目的是找到需要标定传感器坐标系与机器人凸缘坐标系之间的关系,标定的时候保证靶标位置不变。配置好guide_para.mdb文件并复制拷入offline文件夹,点击GuideOffline配置波特率改为115200,将传感器编号改为所要标定的传感器编号,亮度调为适中,点击“相机测量”进行拍照。相机标定一共需要拍摄传感器在黑白方格标定板9个位置的9张照片,拍摄时标定板不能移动,第一个位置传感器在标定板中间位置且垂直于标定板,其他8个位置在标定板的四边与四角且标定板垂直方向向外倾斜15°左右,传感器与标定板的距离最好为500~600mm。9张照片以传感器号的命名方式放入以传感器号命名的文件夹中。标定完成后将轨迹中所有点都修改为TOOL0,BASE0根据机器人引导轨迹BASE来决定,需要统一。
机器人引导抓件轨迹应按现场实际情况来决定,抓件位置根据零件在料箱的具体位置而定,通常做零位。我们选取料箱最内侧的位置摆放零件做零位,零件摆放不应使零件受力变形,应使零件处于自然状态,将零件摆正、固定。
步骤顺序为:①调整机器人至抓件位置做抓件点,抓件点应做到销子插进销控,各个夹头刚好触碰到零件;②从抓件点当前位置延料箱出件方向水平移动100mm(具体位移视现场实际情况),做调整点及出件过渡点,注意干涉;③延料箱出件方向水平拉出距离零件500~600mm处,调整传感器位置,做拍照位,记录当前位置(若无干涉可以寻找拍图清晰的拍照位),将测距仪设置为当前位置停止,接着水平拉出80~200mm后记录测距仪减速点;④从拍照位延料箱出件方向水平拉出料箱外一点,做ready点或出件点,沿途有干涉可做过渡点。
选特征点可以选取孔、凸台、角点及弧线等特征明显且易于匹配的特征,最好选择孔为特征点。特征孔要选没有干涉的孔,选择零件层叠时特征稳定的特征点。如果零件特征极少,但特征受外界因素影响较大时,需改善特征环境,以提高特征匹配效果,如将特征点背景涂黑,使特征点不受环境影响。特征点至少选取4点,通常选取5~8个点。特征点选取后在对应的零件数模上找出零件的理论值,然后配置MDB表中的measurepoint表,配置相应的特征点信息。
报错类型一:超时,即在正常引导抓件过程中,机器人走到Ready,等引导语句后,机器人上报出Timeout,或是走不下去,或是系统未准备Systemnotready,则此类型为超时问题。
超时问题出现原因:①未开启Device通信软件,即连接机器人与控制柜之间关系的软件,或是未开启引导软件;②交换机上或是工控机上绿色网线松动;③机器人程序未按照标准轨迹流程走,即在走过ready语句后又重复走一遍ready,或是没有走ready语句直接跳过然后去走拍照语句。
超时解决方法:①检查相应软件是否开启,开启顺序,先开启通信软件Device,再开启引导软件;②检查交换机或是工控机上网线是否松动;③检查机器人程序逻辑是否完整;④以上三点检查OK后,软件按顺序重启,机器人退回原点,或是Ready语句之前,然后再次走程序即可。
报错类型二:超差,即机器人弹出报错对话框,软件上显示超限,此时可以继续执行到home点选择重拍或者检查零件状态。
超差原因:零件本身偏移过大、变形,其他问题干扰导致引导软件匹配失败。
在焊装车间实践视觉引导应用以来,稳定性较好,经统计故障率,平均故障间隔时间MTBF可达1000h。综合考虑人工成本、设备生命周期成本等因素,采用视觉引导带来的实际效益在多车型柔性切换抓件工位就能实现三年节约30多万元,值得更广泛地推广及应用。随着激光3D引导技术发展,能够更柔性地满足各种装配匹配的要求,从而保证产品质量的更加稳定。
AI《汽车制造业》
龚淑娟
李峥
评论 0
正在获取数据......