0 前言
进气系统是整车开发的重要系统之一,其设计的优劣直接影响发动机燃烧效率,当进气系统整体阻力过大时,发动机的功率损失增加,产生动力不足、振动和噪声增大的问题。本文针对某中型载货车发动机进气量不足的问题,通过流体分析和结构优化改型,降低了进气系统阻力,并通过台架试验验证,经后续市场验证,解决了发动机进气量不足的问题,为车辆进气系统的设计优化、提升车辆进气性能提供了思路。
1 进气系统模型建立与流场分析
1.1 进气系统概述及优化目标
整车的发动机进气系统包括进气道系统(包含高位进气道、波纹管和进气挺管)、空气滤清器和进气连接管路,如图1所示。根据发动机的进气量需求匹配一定流量的空气滤清器(以下简称“空滤”),中型载货车的空滤进气量一般为500~900m3/h,进气阻力1.75~2.5kPa。
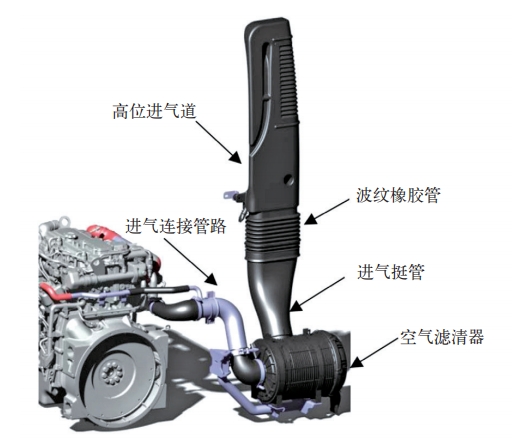
图1 发动机进气系统
空气经过空滤过滤之后进入发动机中,空滤的进气阻力跟进气量有关,目前发展得很成熟,不作为重点关注对象。进气连接管路阻力由管路设计形状决定,该部分阻力相对空滤及进气道系统较小且由于车辆边界的限制,进气阻力优化空间小。所需要改进的车辆由于车身以及货箱等边界限制,整体宽度要低于普通车辆的进气道,该车辆的进气系统提升性能主要难点是对进气道的进气阻力的控制,即减小高位进气道、波纹管和进气挺管的进气阻力。
1.2 模型网格划分及边界条件确定
根据进气道的三维模型,基于STAR-CCM+软件分析计算原进气道的压力损失。该软件在流体域具有更高的精度、收敛速度和网格数更少的多面体网格,各部分网格划分值大小如表1所示,边界层为3层,边界层网格厚度为2mm,考虑波纹管和进气格栅段处的气流状态更加复杂,对该处流体部分的网格进行了加密处理。进气道的计算模型如图2所示。
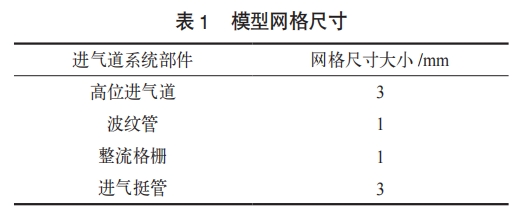
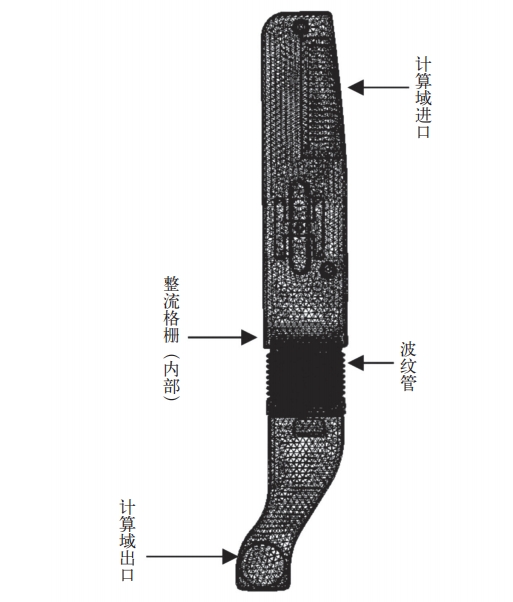
图2 进气道内流场计算模型
高位进气道进口(计算域进口)边界条件设置为质量流量入口,发动机台架试验数据所需进气流量约为900m3/h,考虑进气效率90%,分析空气流量设为1000m3/h(质量流为0.329kg/s)。进气挺管出口(计算域出口)边界条件设置为压力出口,压力设置为0Pa。其余部分设置为无滑移壁面边界条件,采用稳态计算模式,基于N-S方程求解,内部气体为不可压缩的粘性流体属性,湍流模型选择κ-ε湍流模型。监测面选择进气道出口处(整流格栅)、波纹管出口和进气挺管出口3处,监测截面流体的静压值,速度等相关计算信息。
1.3 计算结果与分析
监测面的计算结果随迭代步变化的曲线小于10-4,监测面静压值在最后迭代步数在400以内,波动值小于1~2Pa,计算结果收敛。通过对监测面的数据汇总,计算得到进气道各段压力损失结果如表2所示。
计算结果表明:①高位进气道存在较大的压力损失,为进气道主要压力损失区域,波纹管入口处速度分布不均匀,如图3所示,这是由于气道入口在整个气道右侧,进风量相对左侧较大,且高位进气道上有“H”凹型加强筋结构对进入的气体造成挤压,加剧了进入气道部分的进气阻力。②波纹管段的压力损失为315Pa左右,这与波纹管的外形和入口端的进气速度有关。③进气挺管进气阻力约为424Pa,挺管变径段S处(图2中)是压力损失的主要原因。
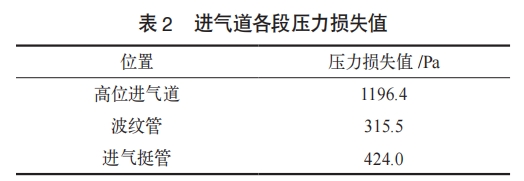
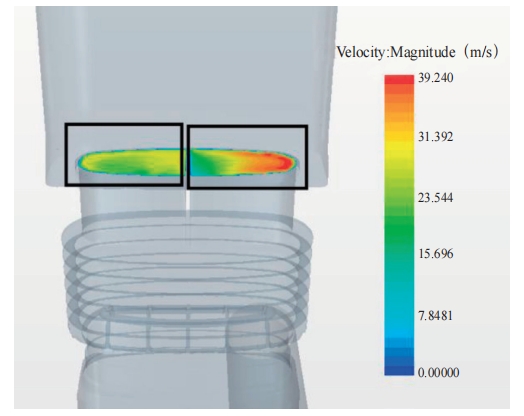
图3 波纹管入口速度分布
2 进气道系统优化改进与流场分析
2.1 优化目标
通过流体分析可知,进气道总进气阻力为1.936kPa。发动机标定流量为900m3/h,且要求在此流量下,空滤压力损失≤2.5kPa,整个进气系统压力损失≤3.5kPa,车辆所用空滤的阻力为1.7~2.0kPa,从空滤至发动机的管路进气阻力整体不到0.2kPa,由前面可知,空滤到发动机的管路和空滤本身可优化空间较小,进气道总体阻力应≤1.3kPa,是要达到的优化目标。
2.2 进气道结构优化改进
由上述分析可知,高位进气道是主要压力损失区域,而其宽度是导致进气道阻力大的主要原因,所需优化的进气道是中型载货车货箱及驾驶室之间的距离较小,高位进气道整体厚度受限于驾驶室、货箱以及挡泥板等边界,所以对于进气道厚度方向的优化无法实现,如图4所示。因此主要通过以下两个方向对进气道优化改进:①增加高位进气道进气格栅的长度A、进气道整体宽度B,并取消进气道的“H”凹型加强筋。②波纹管段的进气阻力跟高位进气道出口的宽度C有关,入口由宽变窄会导致气流截面的突然减小,造成压力损失,所以需要优化高位进气道出口以及波纹管的截面尺寸,同时增加进气挺管的宽度D。由于要避让车身起升装置,变径段S(图4中)的尺寸优化空间有限,但为了使进气挺管入口和下面的出口处实现更加流畅的过渡,需要调整S段的设计尺寸。
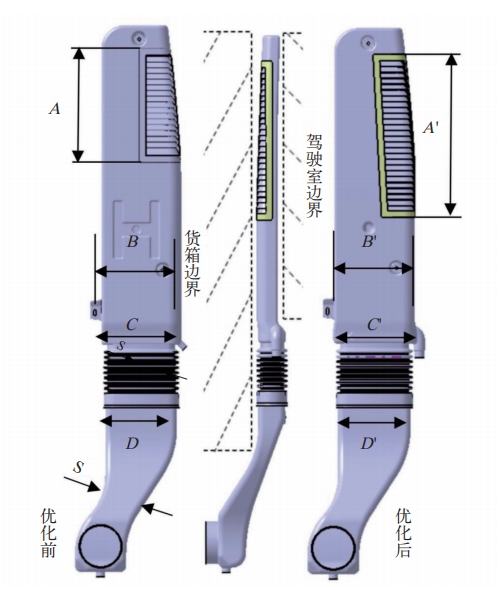
图4 进气道结构
2.3 优化前后对比分析
优化后的进气道结构如图4所示,通过软件分析得到优化后的进气道各部分阻值,优化前后进气道系统各部分阻力对比如图5所示,高位进气道、波纹管和进气挺管压力损失分别为677.3Pa、236.4Pa和424Pa,分别降低44.2%、25.2%和32.8%,进气道整体优化效果明显,优化后进气道进气阻力降低至1.188kPa,满足优化目标1.3kPa。
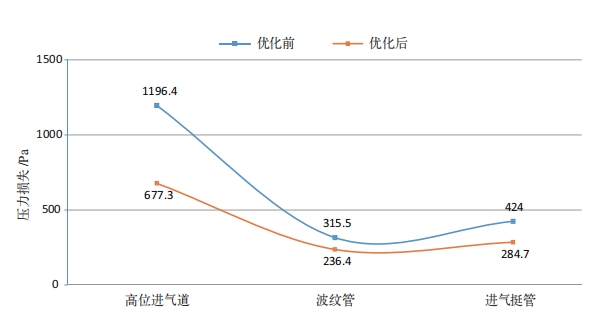
图5 进气道优化前后各部分压力损失值对比
3 进气道台架试验及结果分析
3.1 试验布置及条件
为验证优化后进气道的实际性能,优化后的进气道通过3D打印做出样件,配900m3/h空滤进行台架试验。
测试环境大气压力103.01kPa,测试温度22.5℃,相对湿度48%,在高位进气道出口、进气挺管出口两处分别布置传感器,分别测试进气道在进气流量为400~1000m³/h下两处的阻力值,测试结果如表3所示。
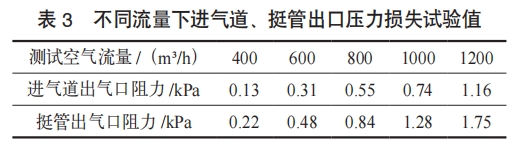
3.2 试验结果与分析
由实测的结果可知:
(1)随着进气流量的增加,进气道的整体阻力递增,当发动机进气需求量较小时进气的整体阻力也较小。
(2)高位进气道压力损失实测值为0.74kPa,与仿真结果0.67kPa偏差在10.4%左右,进气挺管出口端的压力损失实测值为1.28kPa,与仿真结果1.1884kPa偏差在7.1%左右。考虑高位进气道内部气流流速较大,流动状态较复杂,另外测试的环境的大气压和湿度等影响,与分析结果的偏差在合理范围内。
(3)该进气道在进气流量1000m3/h进气整体阻力下实测值为1.28kPa,则发动机标定流量900m3/h下进气道进气阻力必然小于1.3kPa,达到了本次进气道优化改型的目标。
4 结语
针对某中型货车发动机进气不足的问题,首先分别对车辆的进气系统各部分进行了分析,指出由于进气系统中空滤和发动机进气管路的进气阻力优化提升空间较小,主要对进气道(高位进气道、波纹管及进气挺管的集成)进行优化改型设计。优化后的高位进气道、波纹管和进气挺管经过STAR-CCM+软件分析,进气阻力分别降低44.2%,25.2%,32.8%,进气道整体阻力综合降低38.6%。通过对快速样件的台架试验进气阻力测试验证进气道改型结果,试验结果显示,实际进气道总进气阻力由改进前的1.936kPa降低至1.28kPa,进气系统整体压力损失降低33.9%,大大提升了车辆进气系统的性能,为车辆进气系统的设计优化、提升车辆进气性能提供了思路。
参考文献
[1] 李继龙,李宏.进排气系统对整车性能的影响[J].轻型汽车技术,2014.29-32.
[2]申晋宪,王铁.载货车总体设计分析[M].北京:中国标准出版社,2013.
[3]张桃沙,苏小平,等.某发动机排气歧管热应力仿真与分析[J].机械设计与制造,2016(11).171-174.
[4]刘林,杨华松.某重型卡车进气系统匹配分析[J].汽车实用技术,2018(11).44-46.
[5]朗道.理论物理学教程:流体动力学[M].北京:高等教育出版社,2013.
[6]闵海涛,王建华.汽车设计[M].北京:机械工业出版社,2021.
[7]孟萌.柴油机进气系统CFD流场分析[D].大连:大连交通大学,2018.
[8]刘京一.某商用车发动机进气系统流场分析与优化改进[J].轻型汽车技术,2017(1).20-25.
本文为“AI汽车制造业”首发,未经授权不得转载。版权所有,转载请联系小编授权(VOGEL100)。本文作者:丁庆楠,单位:徐工集团工程机械股份有限公司科技分公司 。责任编辑龚淑娟,责任校对何发。本文转载请注明来源:AI汽车制造业
评论 0
正在获取数据......