新能源市场太火爆了,尤其是电动汽车领域热搜话题不断,成为全民关注的热点。电动汽车最受关注的是续航里程和充电速度,这都与动力电池有关。
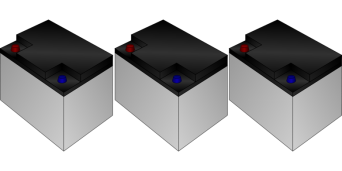
图片来源:pixabay
作为电动汽车核心部件之一的动力电池是怎么制造的呢?工序如何?目前动力电池主要以锂离子电池为主,锂离子电池的制造工艺复杂,生产工艺流程较长,细分的话,涉及几十道工序,而且每一道工序都需要严格控制,才能保证产品的可靠性和安全性。按照外观形态不同,锂离子电池可以分为圆柱电池、方形电池以及软包电池等。
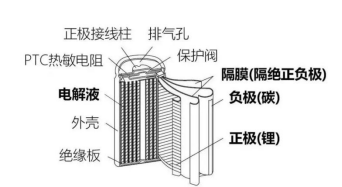
锂离子电池结构
以圆柱形锂离子电池为例,从整体来看,电池生产工序可以概括为3大工段,21道工序。3大工段分别是前段工序(极片制备)、中段工序(电芯装配)、后段工序(化成封装)。21道工序分别是负极匀浆、正极匀浆、涂布、辊压、分切、制片、卷绕、入壳、底焊、滚槽、烘烤、注液、焊接、封口、清洗、套膜、活化、化成、陈化、分选、分容。
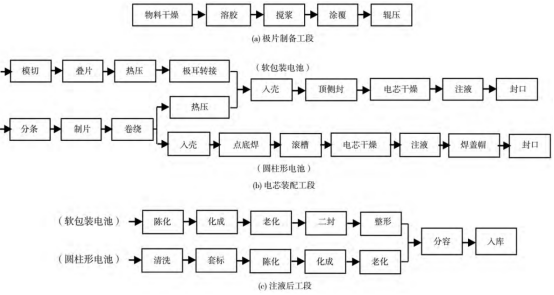
锂离子电池生产工序流程
前段工序主要是极片制备阶段,包括正(负)极匀浆、涂布、辊压、分切、制片。
正(负)极匀浆
将正(负)极活性物质、导电剂、粘结剂等正(负)极物质混合在一起的混料过程,混料是把电池活性物质材料和辅料,在溶剂中进行高度分散形成牛顿型高粘度流体,达到将活性物质、导电剂、粘结剂及其它添加剂充分混合,均匀分散的目的。
涂布
将浆料通过涂布机在集流体表面涂覆一层厚度均匀的涂层,再经过烘道加热将溶剂除去,得到极片。
辊压
涂布完成后,极片需通过辊压机调整轧辊间隙、收放卷位置、张力等,并用试片试压,确保试压后的试片厚度符合工艺参数要求。
分切
将较宽的极片用分切机分切成单颗电芯所需要的宽度。
制片
在制片机上焊接极耳并在极耳位置贴上绝缘胶包覆裸露的集流体和极耳。
中段工序主要是完成电芯的制备,包括卷绕、入壳、底焊、辊槽、烘烤、注液、焊接、封口、清洗、套膜。
卷绕
是由条状正负极极片和隔膜通过卷绕机卷成圆柱形卷芯,这一工序管控要点在于负极极片必须完全包覆正极极片,而隔膜必须完全包覆负极极片,对工艺精度的要求非常高。
入壳、底焊、辊槽
卷芯完成后需放入钢壳并通过底焊使得负极耳与钢壳连接,这时整个钢壳就是电池的负极,再通过辊槽固定钢壳内的卷芯。
烘烤
将已入壳的卷芯置于烘烤箱中烘烤,直至卷芯的水分含量达到标准后才能转入下一工序。
注液
通过注液机将电解液注入烘烤后水分要求合格的卷芯。注液完成后,锂电池的四大主材均被应用到电芯之中。
焊接
将盖板与正极耳焊接在一起,这时整个盖板就是电池的正极,焊接的管控点在于防止虚焊、偏焊及盖帽外观不良。
封口
将钢壳与盖板密封,使壳体内的电芯体处于完全密封的状态,与外界环境隔离,避免物质交换。
清洗
清洗工序的目的是清除电池钢壳表面残留的电解液,防止电解液腐蚀钢壳。
套膜
套膜工序是保证电芯正负极端分开,防止外部电路发生短路,同时使电池有一定的美观度。
完成中段工序意味着一颗外形完整的电芯制造已经结束。之后就是后段工序,此工序主要目的是将电芯激活,经过检测、分选、组装,形成锂离子电池成品。主要包括活化、化成、陈化、分选、分容。
活化
电芯套膜之后在恒温环境搁置一段时间,使电解液充分浸润极片和隔膜,防止因电解液浸润不均匀而导致析锂。
化成
通过第一次充电,使得电芯激活,此过程中负极表面会形成一层稳定的固体电解质相界面(SEI)膜。电池在化成后,才能体现真实的电性能;没有经过化成的电池,无法进行正常充放电。
陈化
将化成后某一荷电状态的电芯在一定温度环境下搁置一段时间,并测试搁置前后电池的电压,根据电压下降情况筛选、分类,排除外界因素的影响,剔除压降大或压降异常的电芯。
分选
根据电芯交流内阻大小分选出不同内阻档位电芯,剔除内阻异常电芯。
分容
分容即分析容量。电池在制造过程中,因工艺原因使电池的实际容量不可能完全一致,通过一定的充放电检测,将电池按容量分类的过程称为分容。
经过上述3大工段,21道工序,新的锂离子电池产品被制备出来。在整个过程中,锂离子电池的生产既要严格把控好各工序的质量控制点、优化制作流程,还要严格控制生产环境的温度、湿度和洁净度等等。锂离子电池的生产是一个相当复杂且精细的工艺流程,细节决定成败,只有精雕细琢、百炼千锤才能做出优良的电池产品。
参考来源:
1、宋玉洁等.纯电动汽车用锂离子电池的制造工艺与管控点
2、刘芬等.锂离子电池主要生产工序及控制点
3、锂电池生产过程视频+图解.数字化企业
4、锂电池生产工序完全手册.旺财锂电
评论 0
正在获取数据......