与化石能源相比,有机材料制成的车辆涂层无疑更加有利于环保,利用创新的涂装工艺,将使车辆的涂层更具耐腐蚀性,同时也能够在涂料生产过程中有效的降低排放。目前,宝马正在努力建立可持续化的供应链,并在其车辆制造过程中限制化石资源的使用。而采用新的涂装工艺,可以将涂装过程中的二氧化碳排放量减少40%。
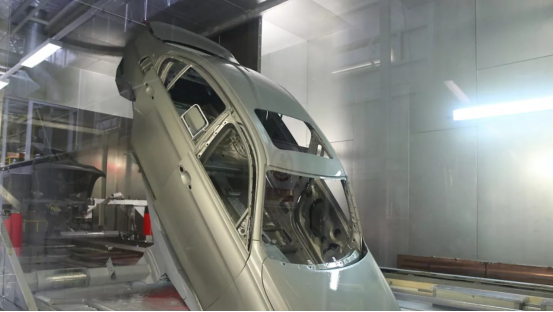
由于在生产过程中会排放大量导致全球变暖的挥发性有机化合物,涂装工艺仍然是汽车制造中综合成本最高昂的工艺之一。作为一家规模庞大的化工企业,巴斯夫不仅一直为全球多家汽车制造商提供涂料,而且还积极参与新型涂料的开发与应用,帮助汽车制造商在成本和环保因素之间取得平衡。
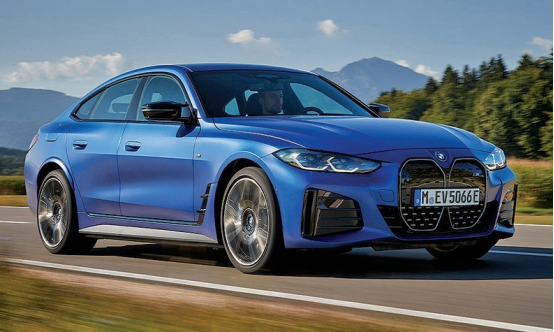
尽管车辆的表层涂装很薄,但目前的汽车外表涂料需要由四层工艺组成,制作流程相对繁琐,其中包括了电泳层、中涂层、色漆层、清漆层。为了减少排放并节省工厂车间的宝贵空间,巴斯夫对取消底漆步骤的可行性做出了研究。然而,在清漆层和色漆层破损开裂时,底漆可以阻隔外界因素对电泳层的侵蚀,其具有必要的功能型。因此,此项方案在可行性上存在着较大的难度。

为了提供最优的平衡性方案,巴斯夫开发了IP工艺,那就是将漆层进行融合。而使用创新的e-coat CathoGuard 800工艺,节省了底漆的干燥步骤,减少了工艺流程。因此,整个涂装生产线的长度可以获得缩减,同时也减少了原材料的消耗,并降低了二氧化碳排放。
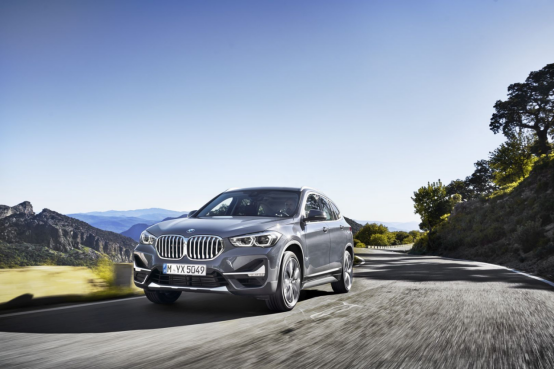
目前,宝马与巴斯夫正在联手开发污水处理厂生物废物涂料,并提出更为环保的涂料制造方案。在中国,华晨宝马的铁西工厂是第二家采用IP工艺的宝马工厂,巴斯夫工程师协助安装、实施和测试整套涂装系统。通过这套先进的涂装系统,将有利于企业降低能耗与成本,并更能够有效的保护当地的生态环境。
评论 0
正在获取数据......