对于汽车而言,发动机就如同“心脏”,也是汽车制造业的核心技术和尖端工艺。
东风商用车有限公司(简称“东风商用车”)旗下的东风龙擎动力有限公司是国内唯一一家同时生产“龙擎”品牌的汽油、柴油、天然气发动机和中重型变速箱的制造厂,建厂以来已累计生产发动机280多万台。
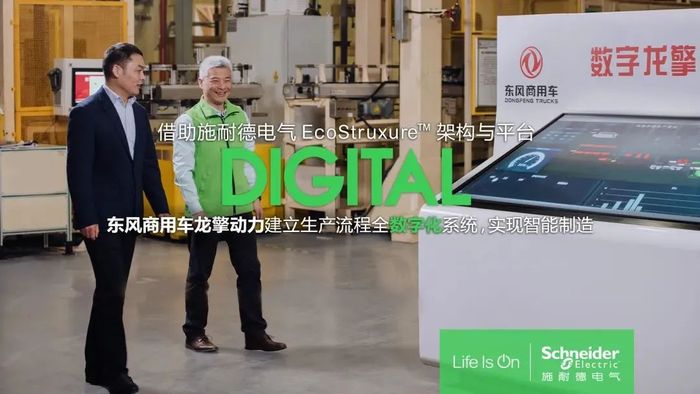
为了满足生产线自动化、智能化控制及精益化管理需求,东风商用车期望建立发动机工厂的生产流程全数字化信息系统。基于面向汽车行业的EcoStruxure™工厂解决方案,施耐德电气为东风商用车提供了由AVEVA系统平台搭建的智能制造平台及5G解决方案,助力其打造汽车行业先进的数字化智能工厂。
求解“不可能的制造方程”
在东风商用车的发动机工厂,每年有近10万台满载着尖端技术的发动机走下产线,而后随着一辆辆货运卡车走遍中国的大江南北。
同为发动机,制造难度其实也有高下之分——与乘用车相比,商用车因自带“生产工具”的属性,所以发动机的制造技术和难度更胜一筹:
为应对大型货物的运输和牵引重量,商用车发动机的设计需要具有更大的排量和更高的燃烧效率;
商用车需要在更恶劣的道路和环境条件下行驶,比如氧气稀薄的高海拔地区、雨雪/高温/低温等恶劣天气、粉尘严重的极端环境等,因此商用车发动机必须具有更高的可靠性;
商用车往往要进行长时间的运营,发动机一般需要能支撑80万到100万公里的可靠性;
商用车发动机需要符合更严格的排放标准,同时还要追求更高的燃油经济性。
兼顾功率、可靠性、耐久性、环保性和经济性的过程,就如同在求解一道“不可能的方程”,这无疑是对东风商用车制造水平的一场“大考”。
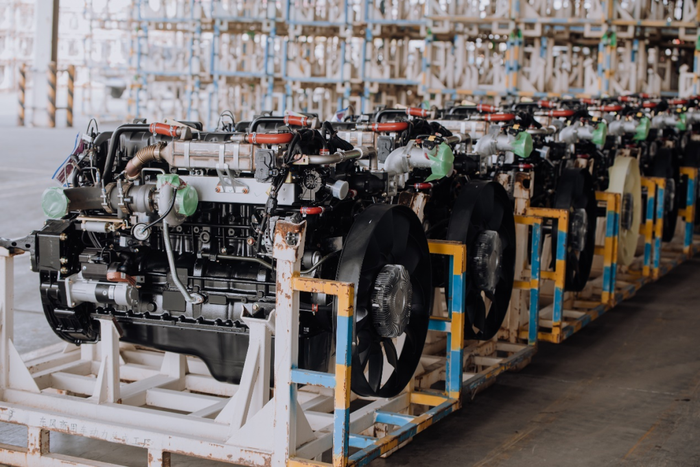
以东风龙擎DDi11发动机的生产制造为例,在DDi11发动机的缸盖线上,存在着生产系统和设备之间信息孤岛林立、生产过程数据无法精确追溯到单件、设备发生异常不能及时响应、现有系统难以支撑工艺柔性化调整等问题。
以点及面,这些挑战也是东风商用车发动机工厂整体需要“补课”的关键。在施耐德电气的助力下,东风商用车在面向数字化和智能化的制造大考中交出了一份令人惊艳的“答卷”。
制造全流程的可视、可控、可追溯
如今,在东风商用车的工厂车间里,自动化设备、机器人和工人们各司其职、相互协作,确保每台发动机的质量和性能都符合标准。
伴随着零部件在产线上的流转,数据也在各个数字化系统和设备之间顺畅的流动,并最终汇总于统一的平台,以实现制造全流程的可视、可控和可追溯。
· 设备运维
一旦设备发生任何异常或故障,系统都能第一时间将相关信息推送给相应的维修人员,减少故障停机引起的停工停产;
· 生产优化
基于大数据平台,施耐德电气助力东风商用车试点了设备预防性维护和刀具智能管理,对于刀具使用寿命的提高提供依据,使得设备寿命延长约25%;
· 质量管控
质量管控模块的引入如同为每一个工件配备了一张“身份证”,将管理颗粒度从“批次”细化到“工件”,追溯工件包括原材料、生产工艺、设备工况在内的所有生产信息。
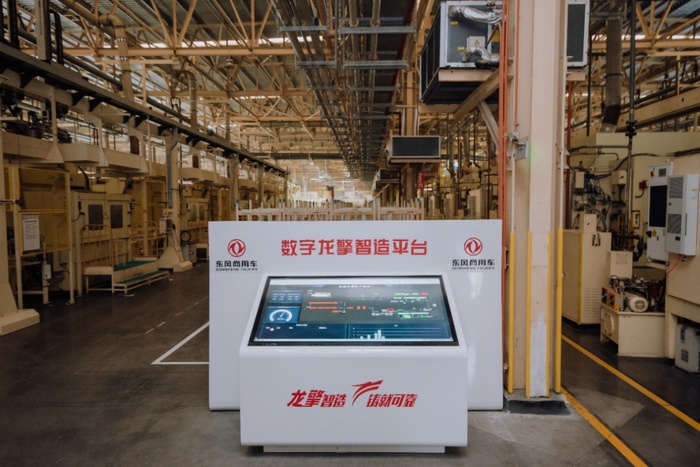
基于施耐德电气EcoStruxure架构与平台的智能工厂数字化解决方案,我们能够从设备层采集相关数据并通过5G网络传输到平台层进行深度分析,实现设备预测性维护、点巡检修管理、质量数据采集管理、工艺指导及节拍寻优、故障监控管理及安灯呼叫、信息提示和推送管理等功能,通过OEE及开动率等KPI指标提高生产效率、运维效率和柔性化制造水平,通过大屏显示、中控展现、移动设备为相关部门人员提供数据支撑及管理手段,提升工厂生产的自动化智能化水平。
——李昌运
东风龙擎动力有限公司首席师
5G剪掉工业制造的线缆
随着商用车市场竞争格局日益激烈,东风商用车需要针对长途运输、农副散杂、快递快运、城建渣土等细分场景提供更加定制化的产品,这对工厂的柔性化生产能力也提出了更高的要求。
传统的工厂互联大多依赖“有线+WiFi”的组合,其局限性显而易见——
工厂环境复杂,有线网络难规划、部署成本高,易造成线缆过多、混乱的情况;
WiFi网络抗干扰性与移动性差,同时基于WiFi的网络环境也不具备边缘能力。
而5G具有易部署、低时延、高可靠、大带宽、广连接特性,宛如一把锋利的剪刀,成功为工业制造减去了多余的线缆,让其柔性化部署不受限制。
在施耐德电气的助力下,东风商用车在商用车领域率先打造了5G全连接工厂,这在全国乃至世界范围内都属于比较领先的技术。
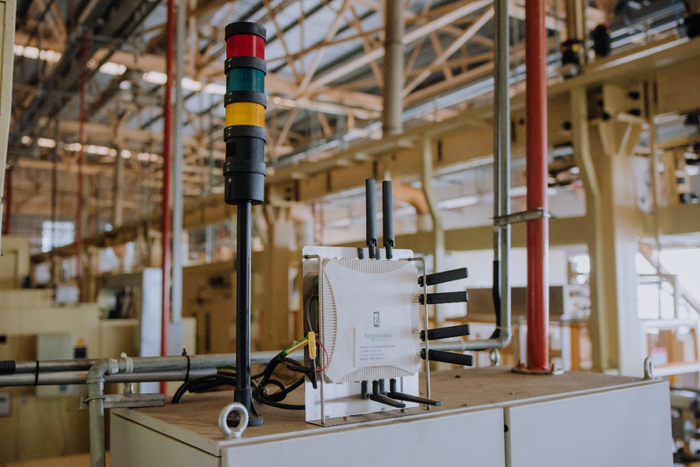
当然,5G工厂的建设也并非易事,在建设过程中,工厂现场曾遇到过不能查明的电气信号干扰问题。为了解决这一问题,施耐德电气和东风商用车的工程师们通力合作,反复尝试各种品牌的数据读取装置进行现场测试和分析,最终花费两三个月的时间让干扰迎刃而解,保证了项目的顺利交付。
好风凭借力——未来,东风商用车也将继续与施耐德电气一起,在绿色智能制造及数字化转型之路上携手前行,共赢可持续未来。
评论
加载更多