0 引言
涂装车间的传统设计是基于二维CAD制图软件,在满足生产线节拍以及工艺设备参数下,各专业相互贴图来绘制二维施工图。此方式下数据不能及时共享,设计过程繁琐且各专业之间设备可能相互干涉,施工图质量无法达到最优。涂装车间传统设计是基于CAD二维制图软件,在满足生产线节拍以及工艺设备参数下,各专业相互贴图来绘制二维施工图。此方式数据不能及时共享,设计过程繁琐且各专业之间设备可能相互干涉,施工图质量无法达到最优,同时也无法响应工程勘察设计行业全面推广BIM技术应用的要求。为解决这些问题,数字化协同设计提供了有效的解决方案。
1 数字化协同设计所包含的内容
本文阐述的数字化协同设计由三部分构成,包括数据交换设计云平台、可研方案展示模块以及正向设计模块。
通过建立涂装车间工艺设备建设运行中各阶段的专属文件夹,搭建数据交换设计云平台如图1所示。
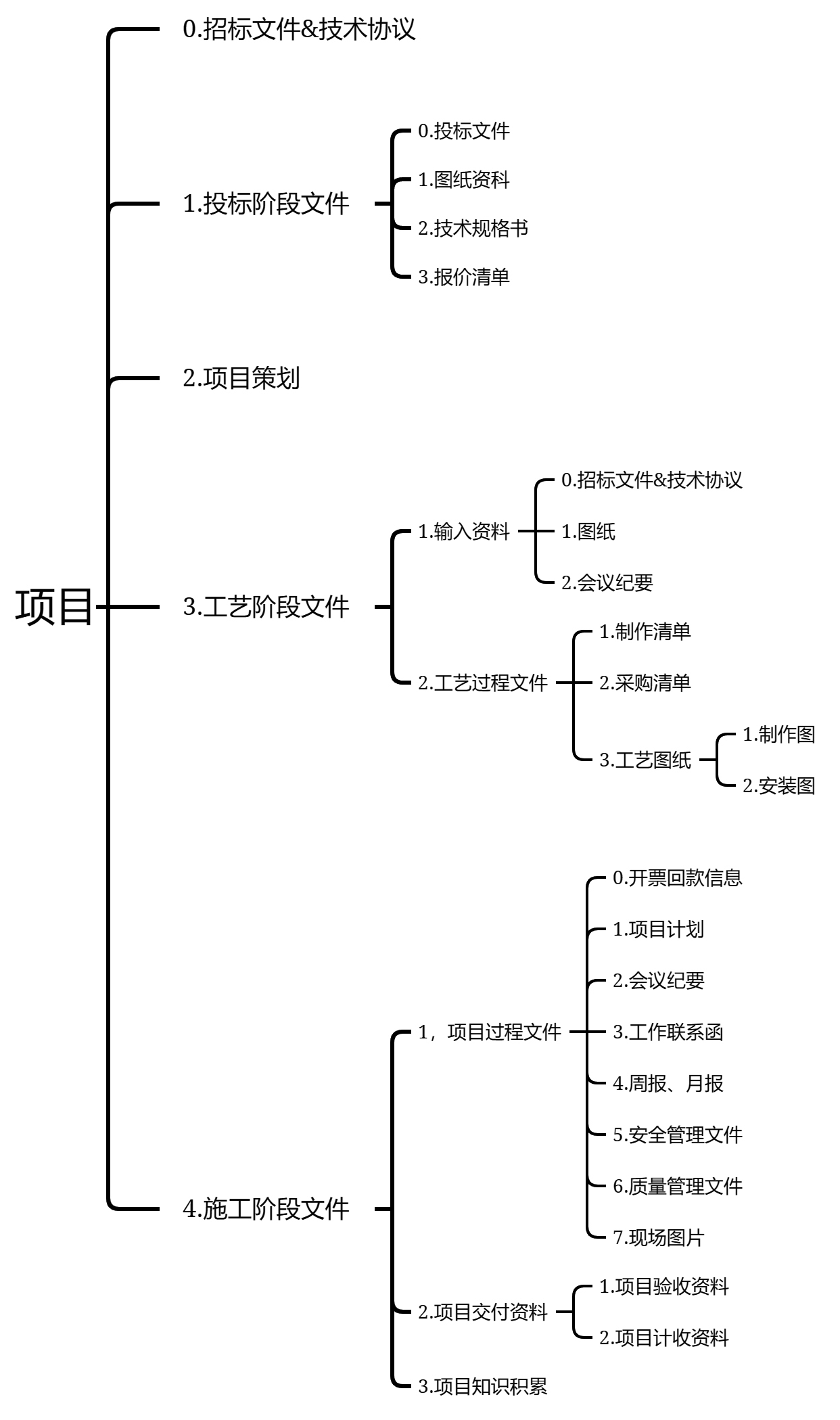
图 1 数据交换设计云平台结构示意图
可研方案展示模块通过建立系列简易参数化模型库,并利用数据交换设计云平台中的工艺设备建设运行数据,进行可研方案展示。
正向设计模块的作用是在可研方案模块展示确认通过后,根据各工艺设备的结构形状特点以及专业术语建立设备代号,确定以设备自身为原点的设备坐标系,并设定对应的工艺设备建模逻辑,根据工艺设备建模逻辑和工艺设备的结构特点,对参数化模型库中的各类工艺设备模型进行编程二次开发。
各类工艺设备参数化仿形模型实现参数化驱动后,正向设计模块还可用于形成涂装车间BIM模型。利用设备代号、设备坐标系、工艺设备建模逻辑和参数化驱动的各类工艺设备仿形模型等,在车间工艺设备汇总软件中进行基于同一个轴网信息文件的涂装车间各专业模型的工艺汇总,形成涂装车间BIM模型。
正向设计模块还用于对涂装车间BIM模型进行干涉测试,当干涉测试结果显示BIM模型存在干涉时,对涂装车间BIM模型进行修改,直到BIM模型不存在干涉,才完成涂装车间工艺设备数字化设计。流程如图2所示。
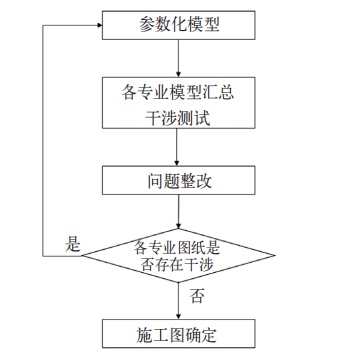
图 2 干涉测试处理流程图
综上,数据交换设计云平台记录了可研方案展示模块以及正向设计模块的数据;可研方案展示模块与正向设计模块为递进关系。
2 数字化协同设计各模块具体功能及应用
2.1 数据交换设计云平台
数据交换设计云平台是通过建立涂装车间工艺设备建设运行中各阶段的专属文件夹树来实现的,文件夹树的命名规则为“年份-立项号-工程总称-项目名称”;云平台管理员根据项目策划表分配各参与人员查看、检入、检出文件的权限;同时设计云平台为实时共享数据提供协同作业环境,数据交换设计云平台通过企业服务器存储工艺设备建设运行数据,云平台针对小的更改和大的修订提供版本控制以防止数据丢失,数据交换设计云平台通过安全登录和权限管理来保护数据,免遭盗窃、破坏和滥用,确保信息安全,数据交换设计云平台的索引数据库实现工艺设备建设运行数据的检索。
2.2 可研方案展示模块
该模块可将方案布局形式由平面转化为立体,并以动画的形式,让需求方更直观的了解到整个方案。该模块将数据交换设计云平台中的工艺设备建设运行数据输入到简易参数化模型库中,形成参数化驱动的工艺设备,在简易参数化模型库,利用车间工艺设备汇总软件,将参数化驱动形成的工艺设备放置于车间轴网的对应位置上,完成全车间三维工艺布局;通过可视化仿真软件提供漫游视频,包括工厂外围环绕预览、设备生产动画、车间设备分层预览、重点设备细节分解展示及机运路线展示等,将整个工艺方案进行立体展示。图3所示为某涂装车间仿真漫游画面。
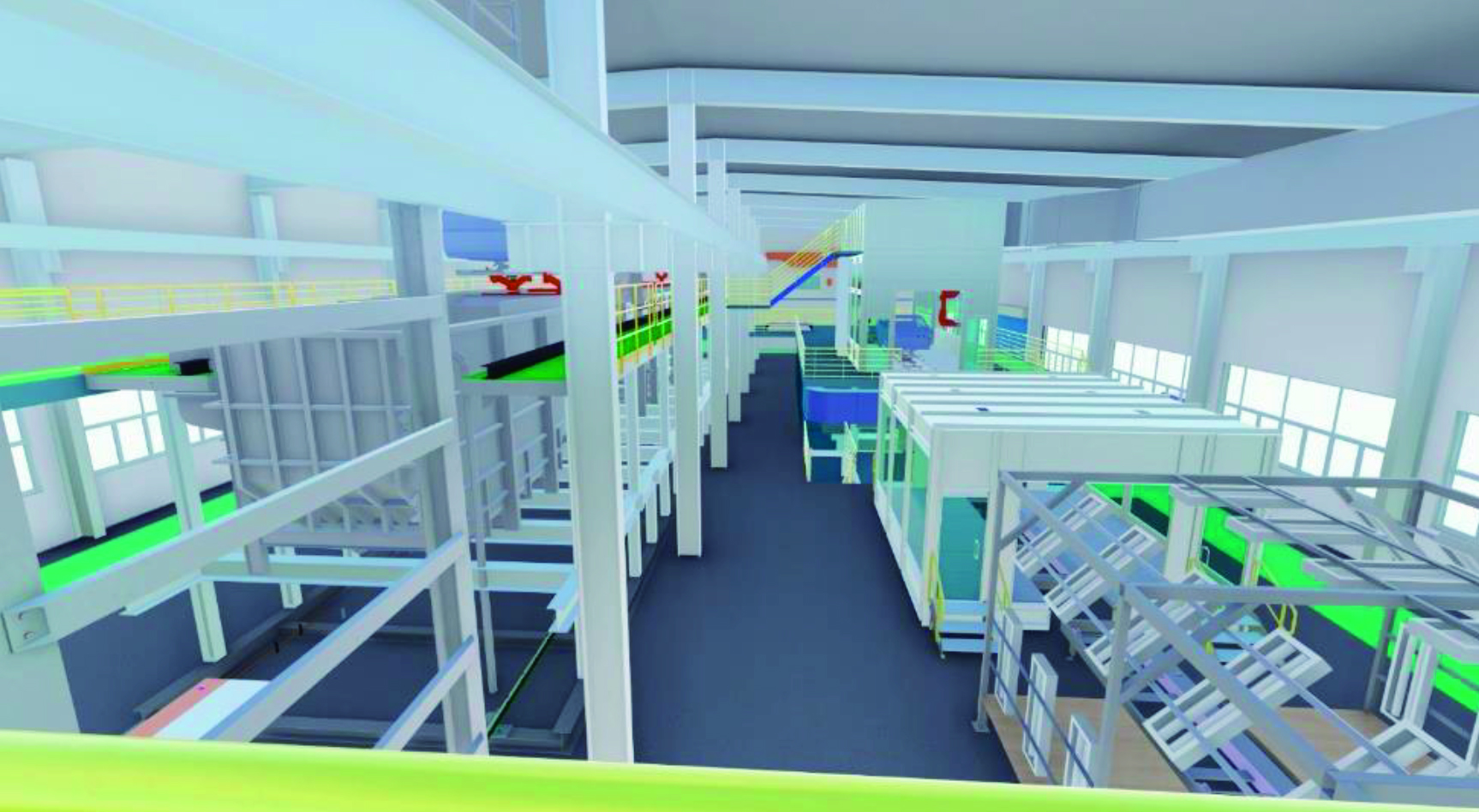
图 3 某涂装车间仿真漫游画面
2.3 正向设计模块的功能
正向设计模块包括定义设备数模代号、参数化驱动工艺设备模型以及干涉测试三大功能。
(1)设备数模代号的定义规则
根据各工艺设备的结构形状特点(如多孔、线管、圆形和方形等)以及专业术语在excel表格中建立设备代号,如图4所示。代号要便于设计时准确、方便、快捷地从数据库调取模型,代号是串联零件、部件、设备信息以及工程图的纽带,设备代号具有唯一性。
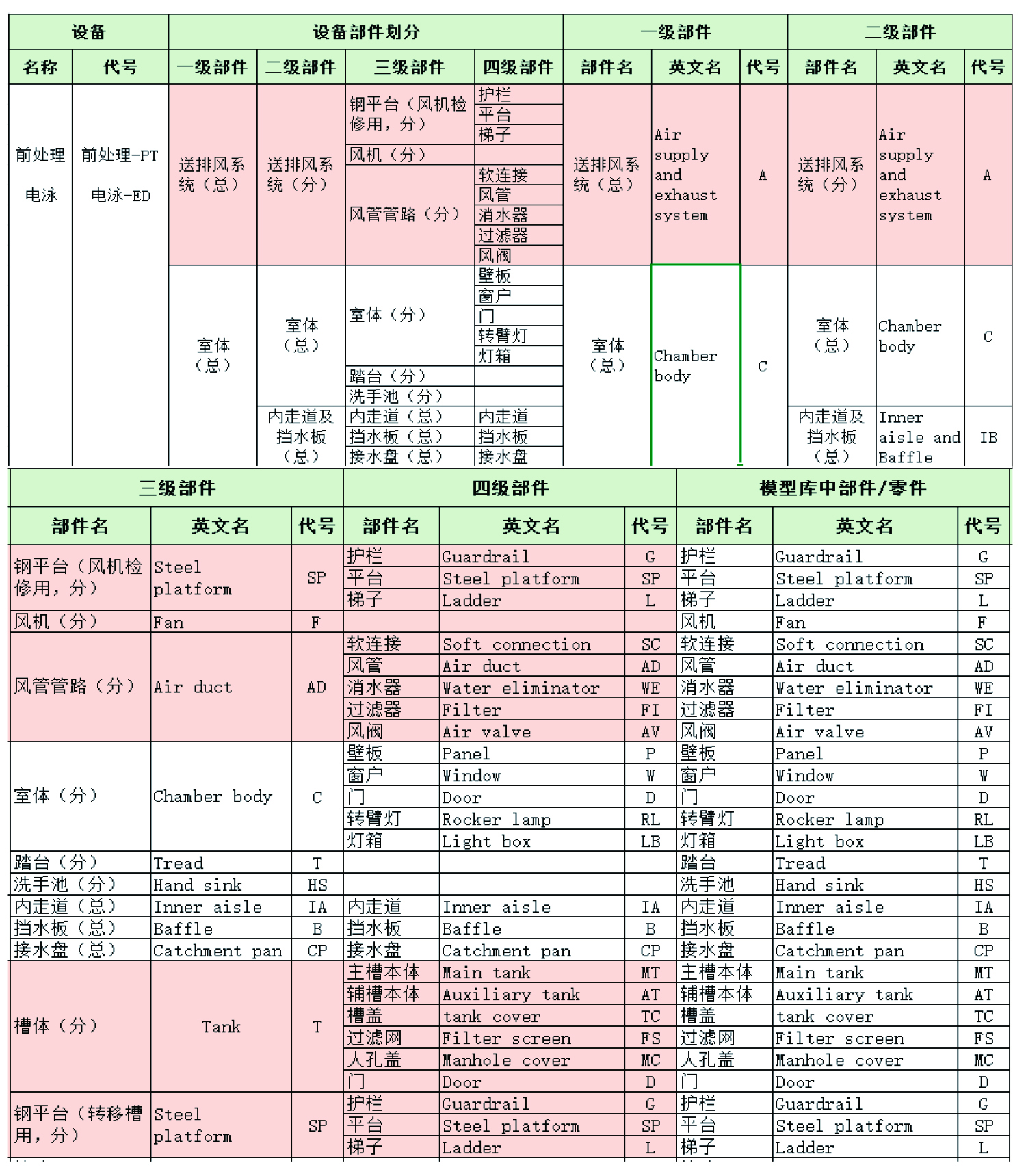
图 4 某汽车涂装非标设备部分数模代号
(2)参数化驱动工艺设备模型
参数化驱动工艺设备模型具有“一套模型,多次使用”的特点,是根据工艺设备的结构形状特点确定以设备自身为原点的设备坐标系,并设定对应的工艺设备建模逻辑(自下而上,自内向外,先加后减等),统一设计规范,便于使用及修改模型,根据供应商提供的图纸来建立外购件模型,根据所述建立设备代号、工艺设备建模逻辑和工艺设备的结构形状特点在inventor软件的iLogic编程模块中(图5)对参数化模型库中的各类工艺设备参数化模型进行编程二次开发,使各类工艺设备模型实现参数化驱动,通过代码生成模型控制表单,使模型能够通过参数驱动来生成图纸,达到“一套模型,多次使用”的目的。例如:喷漆室的长宽高以及下部的漆雾处理结构形式均可通过参数来驱动。
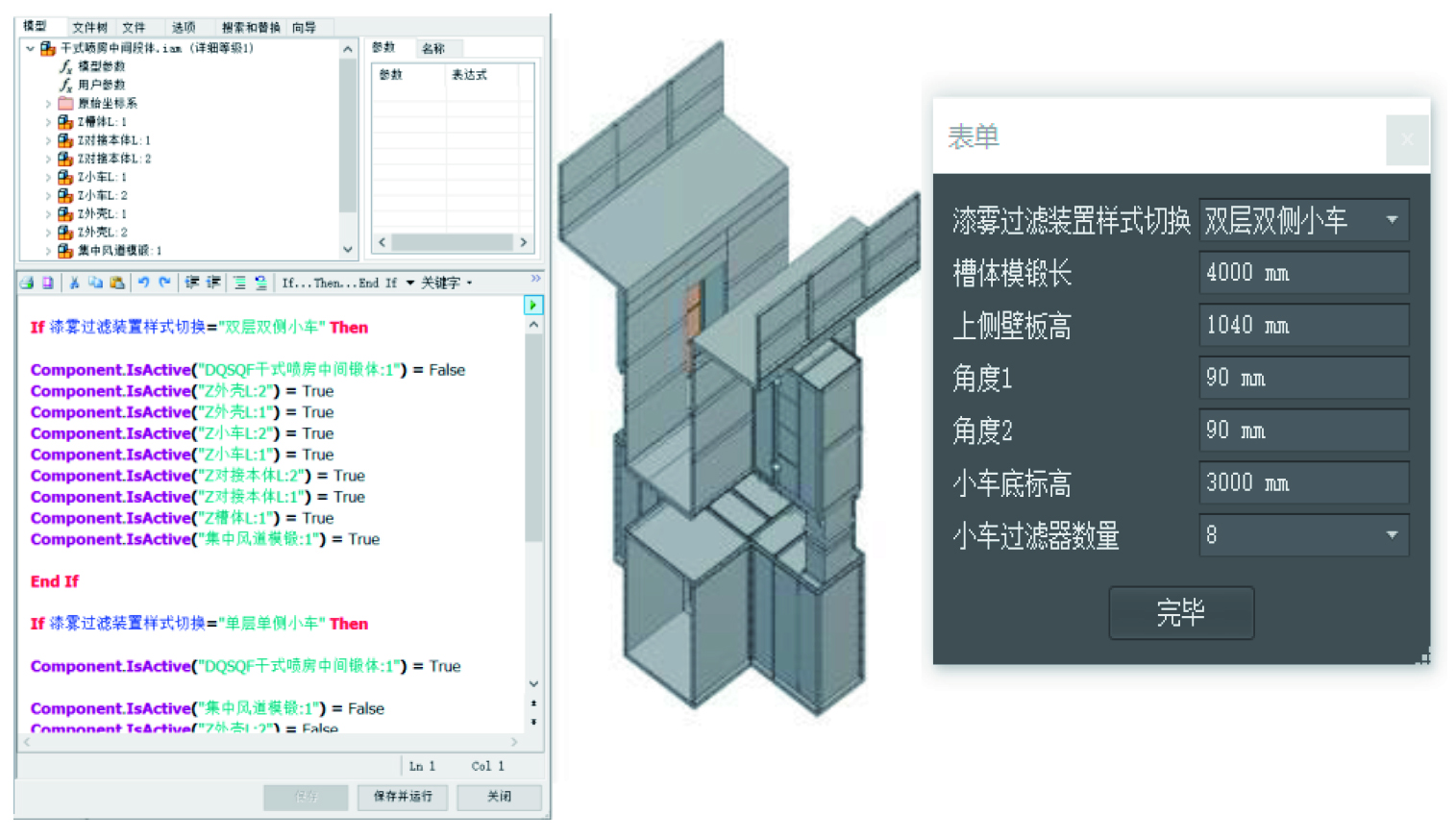
图 5 某汽车涂装非标设备部分模型参数化代码
(3)干涉测试
各专业设计人将所有基于参数化建模后的零部件放置于轴网上,由BIM总图人员进行最后的工艺汇总,从而形成一个完整的涂装车间BIM模型,将该模型转至干涉测试结果界面后,各设备交叉干涉部分的状态、级别、轴网交点等信息可以清楚地看到。图6所示为某干涉测试报告。待BIM总图人员判定状态、增加干涉视点后(图7、图8)再将其分配给相关的设计人员修正整改,优化设备管路布局。整改原则为“小管避大管”“次要避主要”等。多次循环该流程直至解决所有干涉点为止,如图9所示。
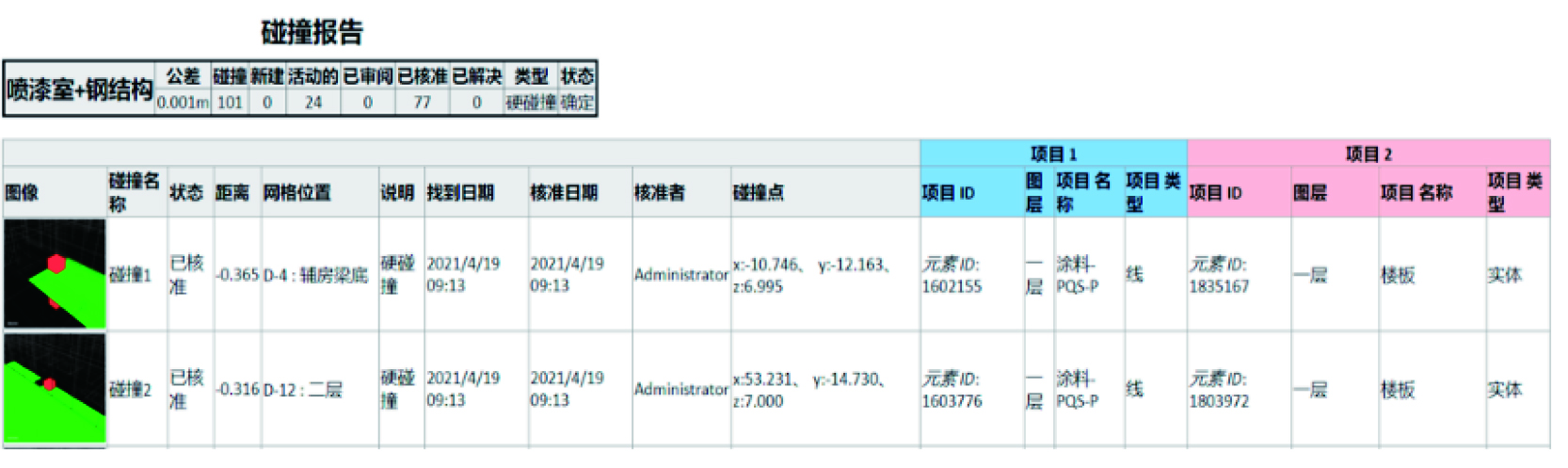
图6 干涉测试报告
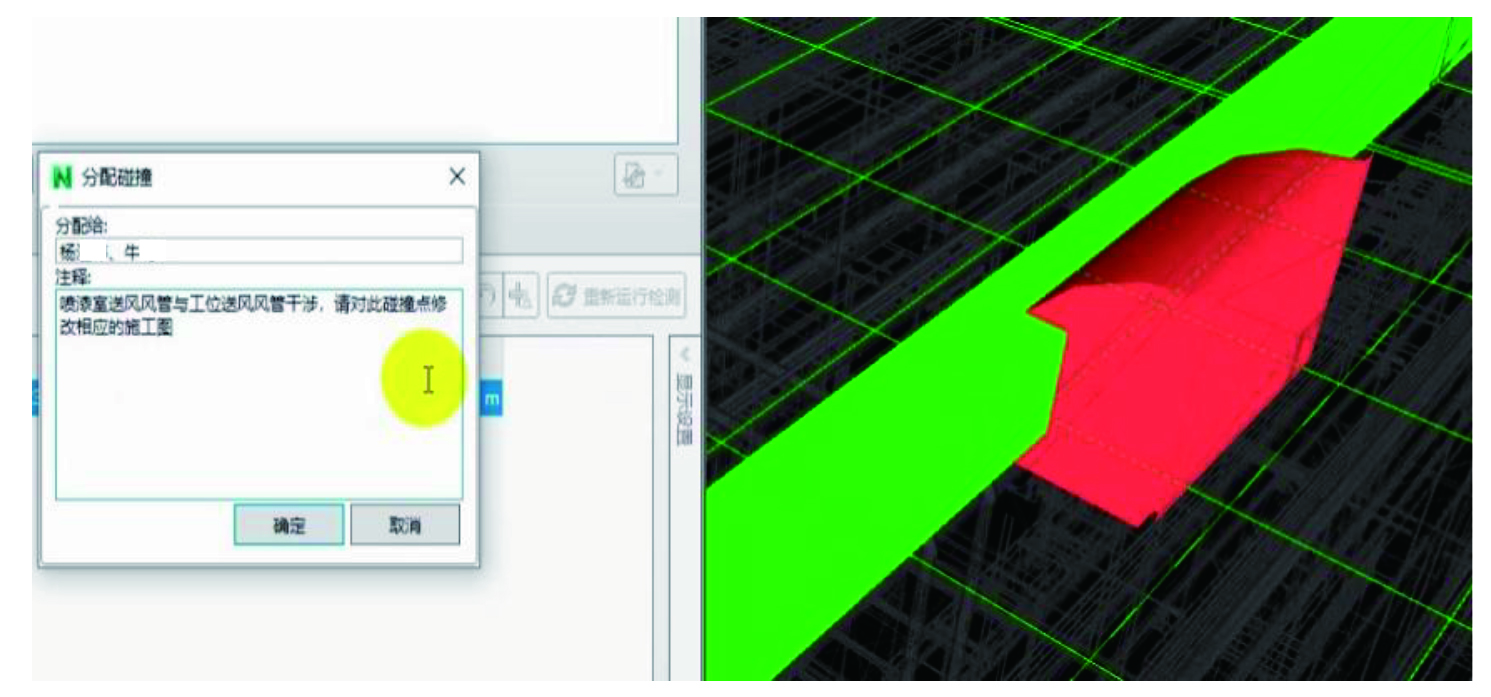
图 7 干涉点分配
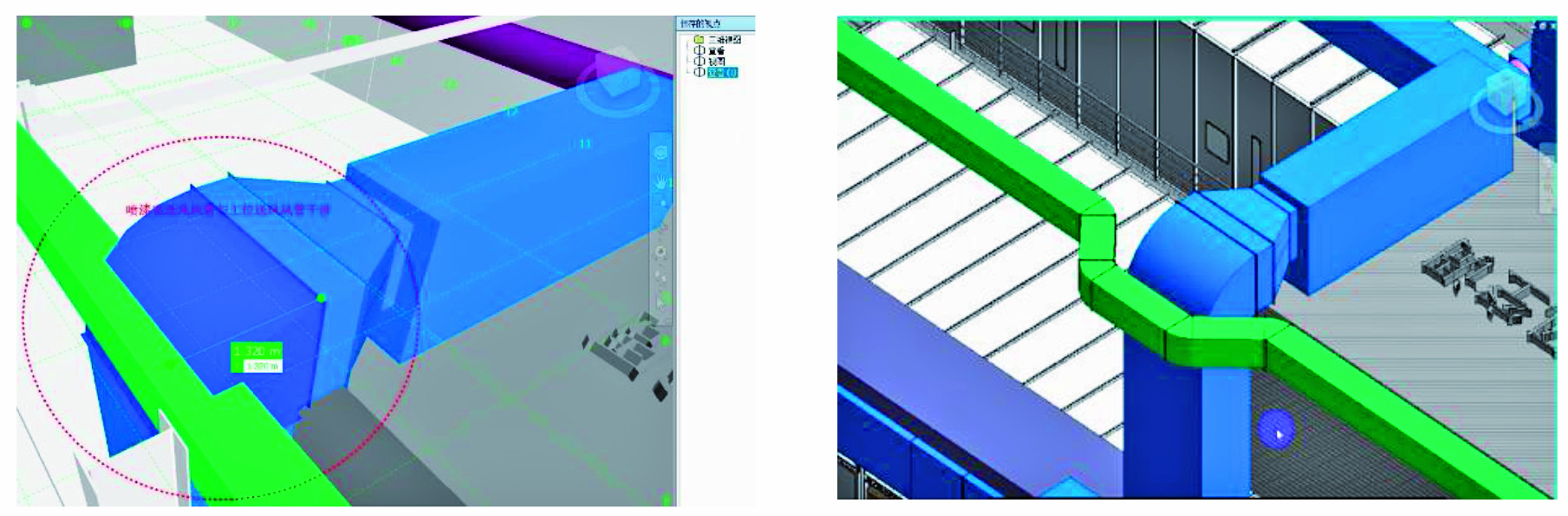
图 8 干涉点保存 图 9 干涉点整改完成
3 结论
本文简单阐述了一种快速的、简单的涂装车间工艺设备数字化协同设计方案,解决了设计数据不能及时共享、设计过程繁琐且无法高效协同作业等问题。将整个作业数据检入至设计云平台使设计数据具有可追溯性,统一的设计标准可快速生成施工图。依托该方案所生成的全车间信息模型,可快速协调各专业设计人员提前规避设计风险,让设计方案达到最优的效果。涂装非标设备参数化设计过程与BIM技术的结合是工程勘察设计行业值得探索的一个领域。
本文为“AI汽车制造业”首发,未经授权不得转载。版权所有,转载请联系小编授权(VOGEL100)。本文作者:罗明全 肖志伟 游和平,单位:武汉东研智慧设计研究院有限公司。责任编辑龚淑娟,责任较对何发。本文转载请注明来源:AI汽车制造业
评论 0
正在获取数据......